BMW M Visionary Materials Seat Wins Sustainability Prize Thanks to 3D Printing
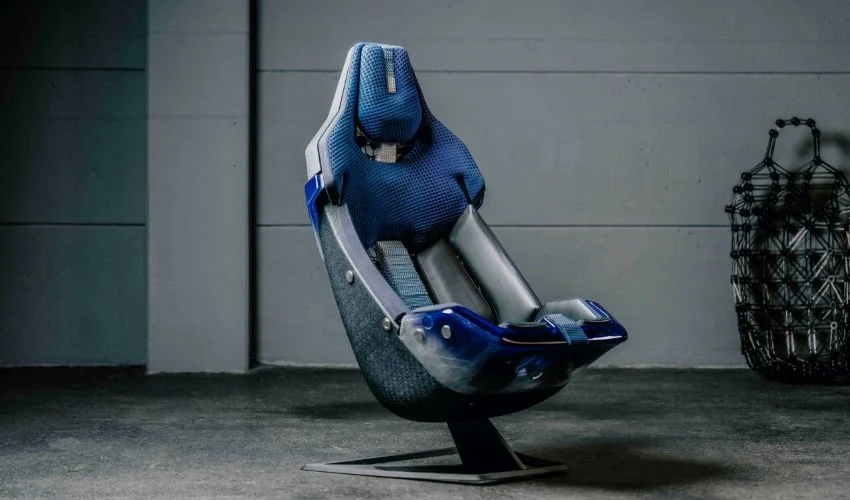
The automotive industry is steadily moving towards greater sustainability and 3D printing is playing a crucial role in this transition. This is because additive manufacturing enables companies to produce more environmentally friendly, lighter and more efficient components. This in turn reduces the ecological footprint and paves the way for a greener future.
An impressive example of this is the BMW Group’s BMW M Visionary Materials Seat, which has now been awarded the Altair Enlighten Award in the “Sustainable Processes” category at the Center for Automotive Research Seminar in Michigan. This annual award recognizes innovative lightweight and sustainable solutions in the automotive industry that minimize carbon, water and energy consumption and promote the recycling of materials. Without the use of additive manufacturing, the environmentally friendly production of the seat would not have been possible, as BMW was able to dispense with support structures and chemical post-processing.
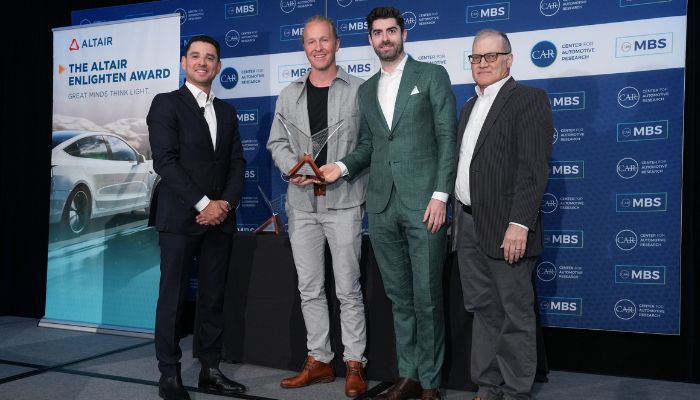
The Altair Enlighten Award honored the BMW Group’s progress in innovation (photo credits: BMW Group)
The Visionary Materials seat was produced in collaboration with the BMW design team for color and material concepts as well as various partners such as Management Consulting GmbH, Bcomp Ltd, Gradel Light Weight Sàrl and Lasso Ingenieurgesellschaft. Falco Hollmann, Innovation Manager for Lightweight Design and Sustainability at BMW M GmbH, accepted the award and explained: “We are showing today what will be possible tomorrow with existing technologies and materials in order to take our efforts to reduce emissions and conserve resources to the next level. This is about more than just substituting materials; it is above all about designing for circularity.”
The team placed particular emphasis on using plant-based materials, improving recyclability and creating an appealing design that combines high quality, lightweight construction and functionality. The seat is intended to be a starting point for future process developments, particularly in sustainable seat design and with a focus on the entire production life cycle.
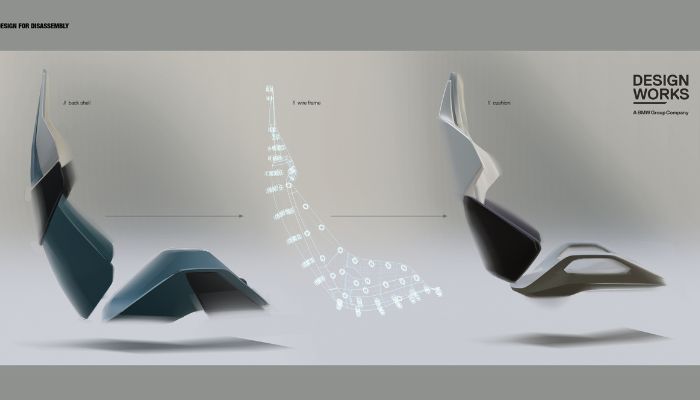
The design of the seat supports easy removal (photo credits: BMW Group)
In addition, the CO2 footprint has been reduced by as much as 90% thanks to additive manufacturing and the use of robot-wound support structures made from fiber composites and materials of natural origin. The low module complexity and the use of unmixed materials also facilitate recycling.
The continuous optimization of the process chain was crucial to the success of the project. In this context, Roberto Rossetti, Head of Development for the Complete Vehicle Life Cycle at the BMW Group, explains: “One of our biggest lessons was the balancing, in other words, how to model our process chain to generate missing primary data. The data obtained provides new insights, both in terms of today’s negative contributing factors and the design of tomorrow’s processes. This experience provides a solid foundation for continuously improving sustainability and developing innovative solutions for forward-thinking mobility.” Find out more about the BMW Group’s M Visionary Materials Seat HERE.
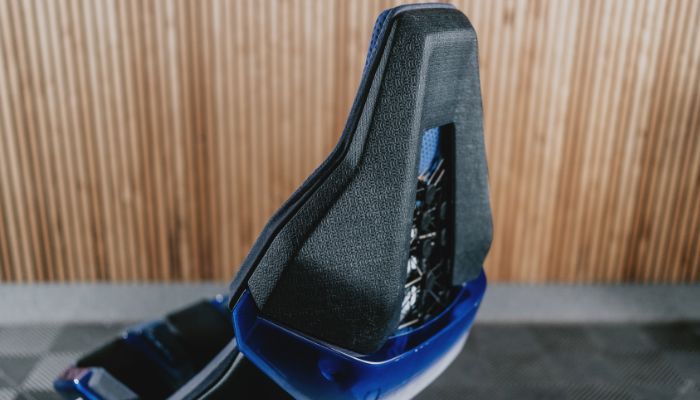
Photo Credits: BMW Group
What do you think of the sustainable seat and the use of 3D printing in its production? Let us know in a comment below or on our LinkedIn, Facebook, and Twitter pages! Don’t forget to sign up for our free weekly newsletter here for the latest 3D printing news straight to your inbox! You can also find all our videos on our YouTube channel.
*Cover Photo Credits: BMW Group