BMW Turns to WAAM to Make Vehicle Components
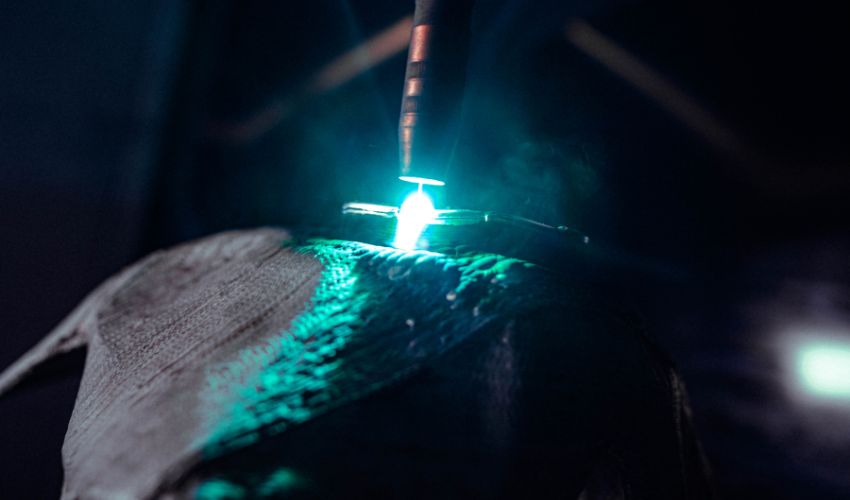
When we discuss key industries using additive manufacturing, car manufacturing is undoubtedly on that list. The automotive sector has been an early and adamant adopter of 3D printing technologies with many famous companies (including Ford, Ferrari, Volvo and Aston Martin, among many others) integrating AM into their assembly lines. Now in latest news, famed German luxury car manufacturer BMW has announced the expansion of its AM capabilities with the adoption of Wire Arc Additive Manufacturing (WAAM).
You probably know that this is not the first time that BMW has turned to additive manufacturing. We have previously covered BMW’s use of laser powder bed fusion to help in Olympic sports like Bobsledding as well as to create bikes. Additionally, it has long used the technology as a part of its production. But this latest news shows how they plan to use WAAM to make even larger components.
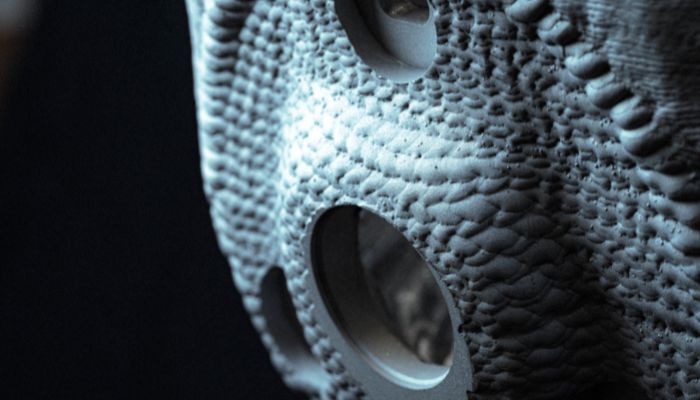
A close up of a part made by BMW using WAAM
Why Is BMW Adopting WAAM?
It actually is not entirely accurate to say that BMW is new to WAAM adoption. Actually, the press release shows that the BMW Group has been trialing and testing this process for a number of years now, since 2015, and have had a WAAM cell, from MX3D, for the production of test components on their Additive Manufacturing Campus in Oberschleißheim since 2021.
However, it seems the company is accelerating the use of WAAM specifically for the creation of large-scale components, something for which the technology is known, while also taking advantage of other benefits. “In this early stage it is already clear that the WAAM process can result in lower emissions in the production process. The lower weight of the components, their advantageous material usage ratio, and the option to use renewable energy means that the components can be produced more efficiently,” explains Jens Ertel, Head of BMW Additive Manufacturing.
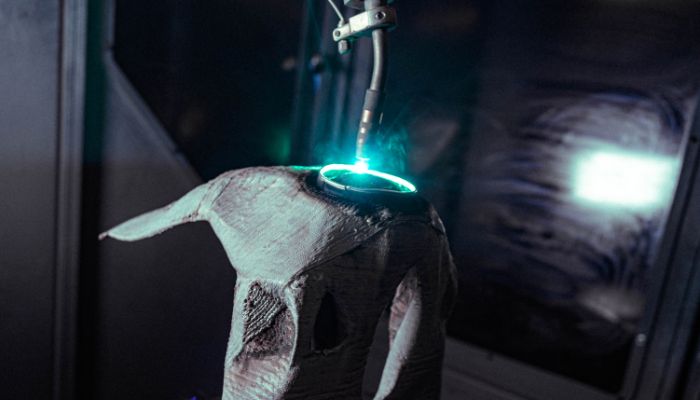
A component being made using WAAM
At the moment, the company expects to start testing end-use parts, especially those made for the body, drive, and chassis areas, with vehicle trials starting in 2025. Coupled with a move to increase the use of generative design along with WAAM, BMW has high hopes for the parts created using this technology. All while continuing to develop its use of additive manufacturing including LPBF, such as with its latest car, the BMW Vision Neue, which used AM for lighting and interior components.
“It’s impressive to see how WAAM technology has developed from research to become a flexible tool for not only test components but also series production components. The use of generative design methods enables us to make full use of design freedom and thus the potential of the technology. That was unthinkable just a few years ago,” concludes Karol Virsik, Head of BMW Group Vehicle Research. You can find out more in the press release from BMW HERE.
What do you think of the adoption of WAAM 3D printing by BMW? Do you think other car manufacturers will soon follow suit? Let us know in a comment below or on our LinkedIn, Facebook, and Twitter pages! Don’t forget to sign up for our free weekly newsletter here, the latest 3D printing news straight to your inbox! You can also find all our videos on our YouTube channel.
*All Image Credits: BMW