BMW Leverages 3D Printing for Improved Robotic Gripper Design
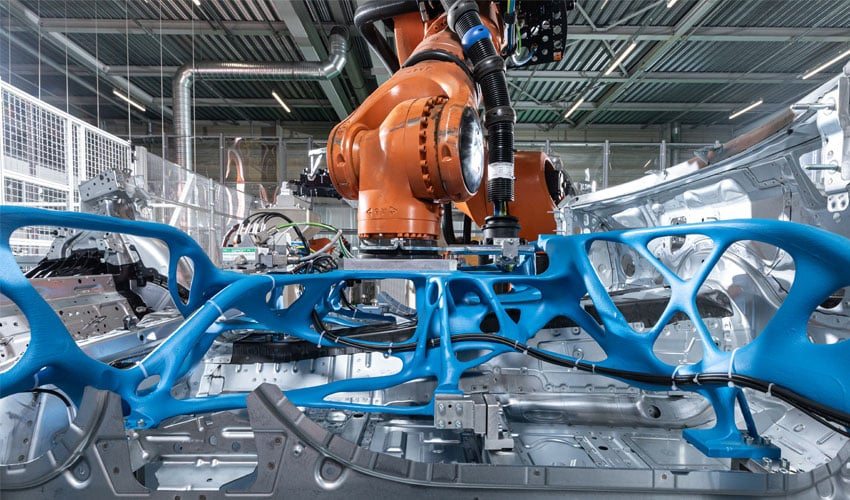
Additive manufacturing has become a fully-fledged production process for the BMW Group. For over 30 years now, the automaker has relied on 3D printing for the manufacture of automotive parts, tools, work aids, and training. The “Additive Manufacturing Campus” in Oberschleißheim plays a central role in this development. Last year, a total of over 300,000 parts were printed here, using a variety of processes. More recently, at the same center, the automaker unveiled 3D-printed XXL grippers. They have been installed on a press for the production of all the German brand’s carbon-fiber-reinforced polymer (CFRP) roofs.
This robotic gripper, weighing approximately 120 kilograms and requiring 22 hours for printing, showcases the efficiency of additive manufacturing. By leveraging this process, the final product achieves a 20% reduction in weight, significantly enhancing operational efficiency. The manufacturing process combines two techniques: SLS for crafting vacuum and needle grippers crucial for lifting CFRP, and Large Scale Printing (LSP) for producing the expansive roof shell and load-bearing structure. Notably, LSP utilizes recycled plastic injection pellets, rendering it exceptionally conducive to economically and sustainably manufacturing large components. As a result, the process yields a notable 60% decrease in CO2 emissions during the production of the grippers.
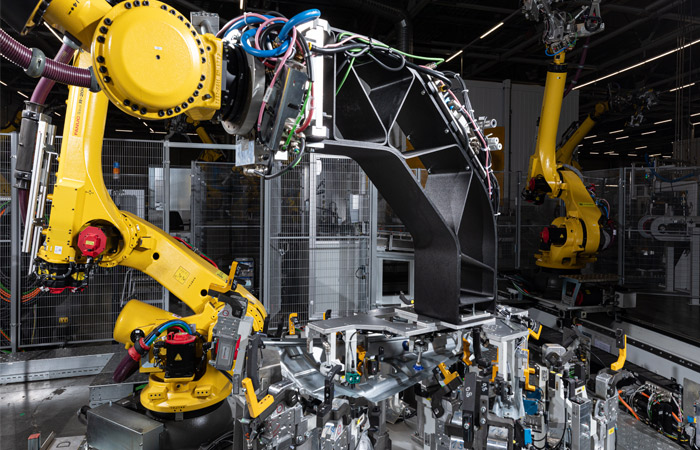
Example of a 3D-printed gripper at the Regensburg plant
Jens Ertel, Head of BMW Additive Manufacturing, explained, “The increasing use of additive manufacturing in the BMW Group production system has many benefits. For example, we are able to quickly, economically, and flexibly produce our own production aids and handling robots, which we can individually adapt to specific requirements at any time, as well as being able to optimise their weight. Less weight allows higher speeds on the production line, shorter cycle times and reduced costs. Plus, smaller robots can be used in the medium term, which also cuts CO2 emissions and costs.”
The German group continues to innovate, as demonstrated by their latest development unveiled last summer: a bionic robotic gripper designed for enhanced efficiency. This advanced gripper features a topologically optimized design, incorporating a roof shell produced by the LSP printer, suction cups manufactured via SLS, and a load-bearing structure optimized with bionic principles. Additive manufacturing plays a pivotal role, particularly in producing the sand casting mold, subsequently filled with liquid aluminum, resulting in a further 25% reduction in weight. Notably, these grippers are primarily employed in manufacturing CFRP roofs for BMW M models. The enhanced lightweight design has led to a significant reduction in the number of robots required for production, from three to just one, thanks to its reduced weight. Moreover, the Landshut plant now employs double clamps, each individually manufactured through 3D printing, further optimizing efficiency and productivity.
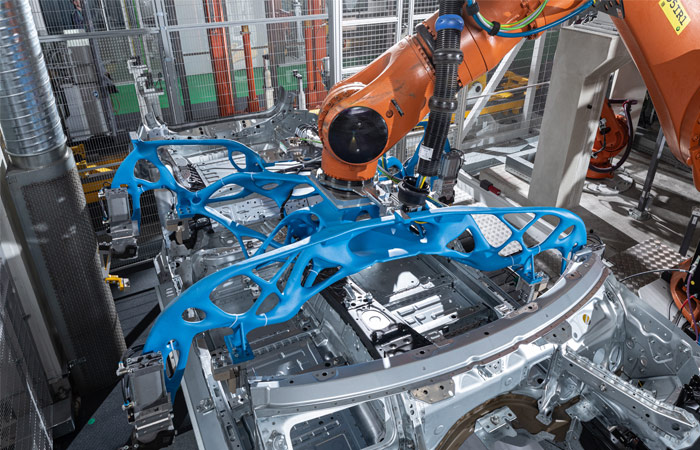
The new generation of bionic grippers, installed in Munich
BMW has taken innovation to new heights, with the Munich plant now employing bionic grippers capable of handling and maneuvering the entire floor of a BMW i4. This revamped gripper model, weighing in at a modest 110 kilograms, signifies a notable 30% reduction in weight compared to its predecessor. This achievement was made possible through the BMW Group’s investment in the Synera software tool, a widely utilized platform within BMW known for facilitating rapid and efficient component optimization.
Markus Lehmann, Head of Plant Engineering and Robotics at the BMW Group’s Munich plant, comments, “At the Munich plant, we are continuously expanding the use of production aids created through additive manufacturing. When it comes to the field of gripper and handling systems, we use 3D printing to equip our established grippers with individual, printed attachments and are already replacing complete gripper systems with highly-integrated and weight-optimised bearing structures. When handling the full BMW i4 floor assembly, this allowed us to reduce the weight of the complete gripper by 30 percent – 50 kg – and thus to extend the service life of our facilities.” To learn more about this project, click here.
What do you think of BMW Group’s use of additive manufacturing and its grippers? Let us know in a comment below or on our LinkedIn, Facebook, and Twitter pages! Don’t forget to sign up for our free weekly newsletter here for the latest 3D printing news straight to your inbox! You can also find all our videos on our YouTube channel.
*All Photo Credits: BMW Group