Using additive manufacturing to break the codes of architecture
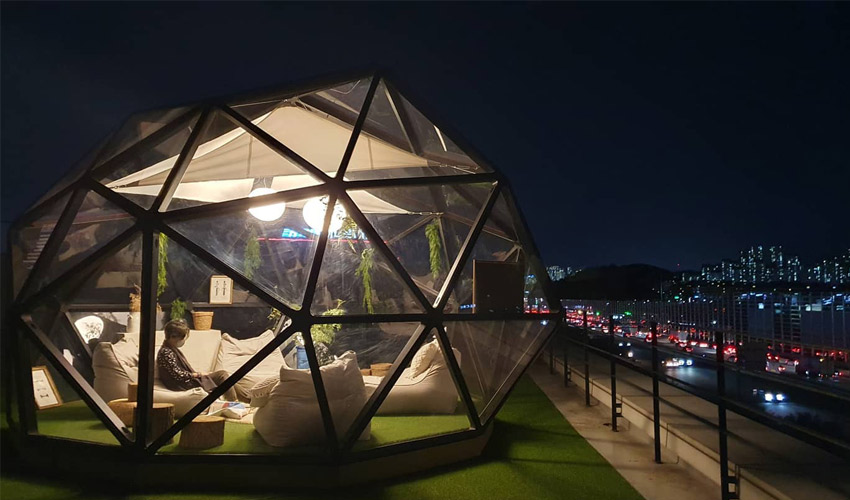
The HS HITECH 3D printing service uses additive manufacturing to build modular structures including customised structural elements called Blobee. Thanks to HP’s Multi Jet Fusion technology, they were able to design the various joints of a glass substructure, surpassing current shape and geometry limitations in the industry. More generally, it is a process that allows the Korean company to mass produce, quickly and more efficiently. Additionally, lead times and costs are greatly reduced. This marks another great innovation for 3D printing in the construction sector!
It’s now been a few years since the American manufacturer HP launched itself in the additive manufacturing market, offering a technology combining powder and a binder, it allows designers and industry professionals to accelerate their production cycle. Indeed, the technology is renowned for its speed, its ability to design parts with a fairly generous volume, and high quality. HP Multi Jet Fusion technology is now used in many sectors, including medical and automotive, but also construction. Even if we are more used to seeing players in this sector using concrete 3D printing, polymer additive manufacturing can be interesting for imagining more complex shapes and supporting original architectural projects.
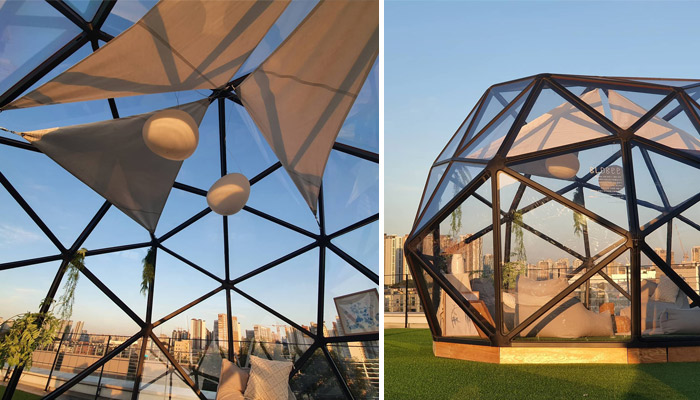
Thanks to HP Multi Jet Fusion technology, the Korean company can imagine more complex joints and thus atypical structures.
This is the case of HS HITECH, which has created Blobee: modular structures made of glass and joints that allow the different panes of glass to be connected to each other. The structure can be used as a work space, a simple coffee shop or even a room to rest. In addition, the company has developed a 3D printing laboratory for the construction sector that allows it to characterise manufacturing processes to go further in the creation process. In most cases, current manufacturing methods are not suitable for imagining atypical architectures, façades and interiors, mainly in terms of geometries. Seung Gyu Yu, Head of HS HITECH’s printing laboratory, explains: “For example, if we imagine that there are triangles with different angles at the same vertex, the structures supporting them are not in the same plane or phase. Several efforts are then required to bring these parts together and we have based our entire joining system on these geometry issues“.
Thanks to HP Multi Jet Fusion technology, this challenge could be met much faster, reducing prototyping and final manufacturing time. Indeed, additive manufacturing allows more complex shapes to be imagined thanks to more suitable design methods. HS HITECH was able to imagine Blobee, a system of custom-made joints that can be assembled together regardless of their shape. The end result is a multifunctional, fully glazed space. The company points out that the HP machines offer both greater speed of execution and the ability to produce large customised parts. The company remains rather discreet about the arrival of these atypical structures in the world, but we will not fail to keep you informed of the progress of the project!
What do you think of this project? Let us know in a comment down below or on our Facebook and Twitter pages! Don’t forget to sign up for our free weekly Newsletter, with all the latest news in 3D printing delivered straight to your inbox!