Why Choose Binder Jetting? Experts Give Their Advice!
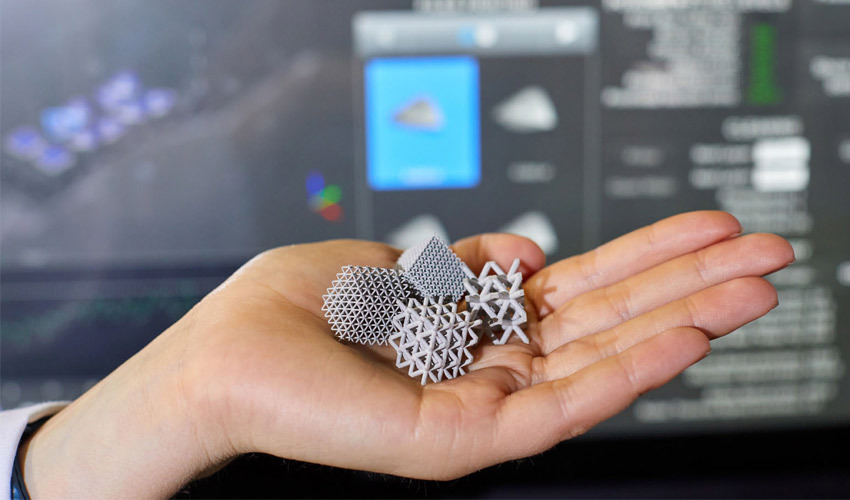
Binder Jetting is one of the various additive manufacturing processes currently available on the market. It works in a similar way to other 3D printing methods, but it is based on the use of a liquid binder in the form of micro droplets and powder, whether metal, sand, ceramic or even composites. Layer by layer, the desired part is manufactured and, depending on the binder and the powder used, post-processing steps, such as sintering, could be necessary. It is a 3D printing process renowned for its flexibility in terms of materials and design, and for its ability to produce large parts. This makes it a key technology for many manufacturers. But what should be considered when a company wants to integrate binder jetting? What are the strengths and challenges of the technology? Our experts have answered a few questions to shed some light on the topic!
Our first expert is Andreas Müller, Product Manager at ExOne. His main focus is on developing and improving the capabilities of sand 3D printing machines. ExOne is one of the leading manufacturers of binder jetting 3D printers, especially systems using sand. Our second expert is Lefteris Havouzis, Managing Director of Lino3D. The Greek company currently supports companies and manufacturers in their additive manufacturing projects thanks to its expertise in several processes, including metal binder jetting. Finally, our last expert is Vincent Poirier, founder and president of Novadditive, the first custom production center for ceramics in multi-process 3D printing.
- Andreas Müller
- Lefteris Havouzis
- Vincent Poirier
How Does Binder Jetting Work?
Like any additive manufacturing process, binder jetting is used to produce a part by superimposing layers of material. In this case, a bed of powder with ideally grains that are ideally spherical and with a diameter of a micrometer. In order for the powder particles to stick to each other, a binder is sprayed onto the plate at the desired locations using a print head. The process is repeated layer by layer until the final object is obtained. Andreas Müller of ExOne adds, “Similar to printing on sheets of paper, the process is repeated layer by layer, using a map from a digital design file, until the object is complete. After printing, an entire job box filled with parts can print in about a half a day, the parts can be removed from the print area. Depending on the material and binder used, additional curing and post-processing steps may be necessary.”
As you can see, two materials are needed for the process to work properly: the 3D printing material and the binder. And what is particularly interesting about binder jetting is the diversity of materials on the market.
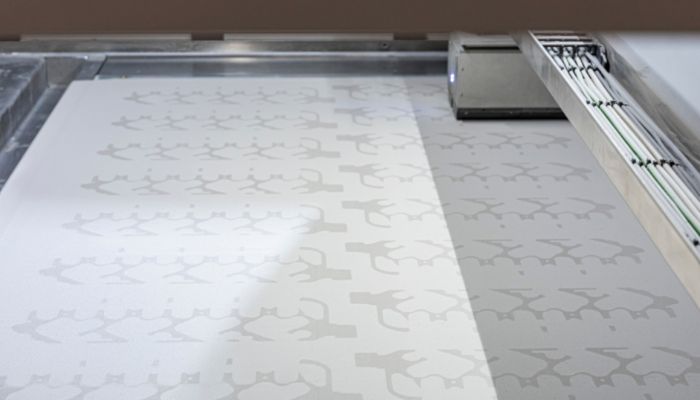
During jetting, binder is selectively placed on the material, sand in this example (photo credits: ExOne)
Material Flexibility in Binder Jetting
Sand Binder Jetting is compatible with metal, ceramic, sand and composite powders. It is therefore a technology that will address many types of applications – for example, sand Binder Jetting is popular for the design of foundry cores or molds, avoiding the need for tooling and offering greater design freedom. Andreas Müller explains, “ExOne sand 3D printing uses foundry grade sand and binder to create metalcasting molds and cores. Sand is also printed into other complex designs and infiltrated with resin to form durable end-use parts. The combination of print media and binder is customized for each application. Our 3D printers handle a variety of sandcasting materials including silica and ceramic sands. Different binders, such as furan, phenolic, and inorganic binders are available to cast a variety of alloys from aluminum and magnesium to iron and steel.”
If we now turn to metals, the same diversity of materials exists. Lefteris Havouzis says: “In general, all alloys can be effectively sintered (mainly iron-based alloys such as stainless steel, tool steels, nickel-based super alloys, chromium-cobalt alloys, as well as difficult-to-weld alloys such as refractory alloys). The most important point is that binder jetting can work with hard-to-weld alloys, where processes using a laser fail.”
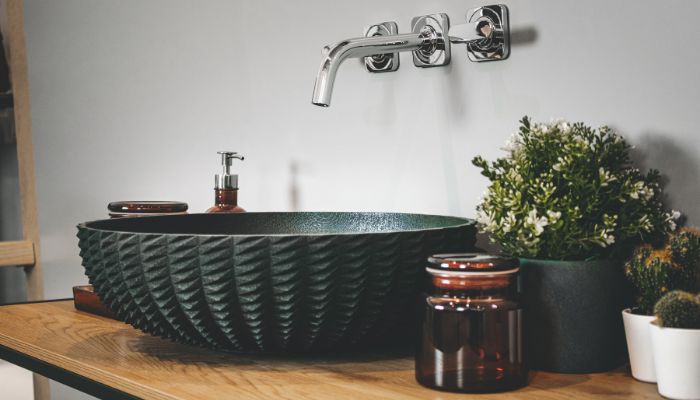
Though often used for indirect processes, sand binder jetting can also create durable end-use parts (photo credits: ExOne)
Remember that in terms of process, a sintering step after printing will be necessary. Immediately after leaving the 3D printer, the part, called a green part, is very fragile and porous and will have to be heat treated to obtain its final mechanical properties. Unlike other metal processes using powder, metal binder jetting does not require print supports since the surrounding powder supports the part.
Finally, on the ceramics side, binder jetting is also one of the technologies used by manufacturers. Vincent Poirier explains: “Theoretically, all ceramics are compatible with binder jetting, provided that a suitable binder has been developed and that powders with spherical grains or that can be spread correctly can be produced. In practice, the ceramics developed for this process must have an advantage over competing additive manufacturing technologies.” So application is key when opting for ceramic powder bonding: you have to have a very specific project in mind, otherwise, the choice of this process is not justified. Alumina, zirconia, boron carbide or infiltrated silicon carbide are all ceramics used in binder jetting.
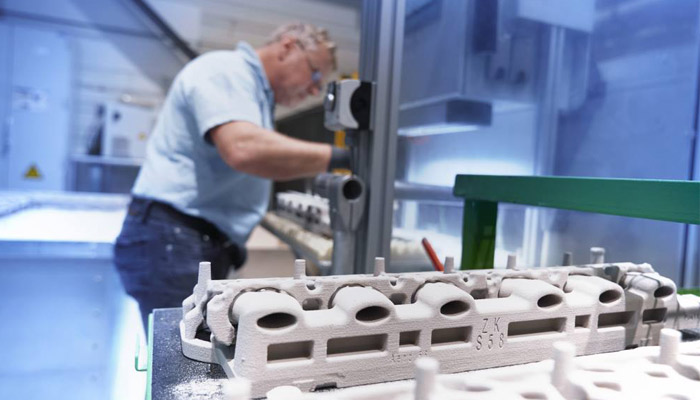
Sand binder jetting is widely used to create molds and cores (photo credits: BMW Group)
Advantages and Limitations of Binder Jetting
As you can see, one of the main advantages of powder bonding is its material compatibility. Note that everything is relative: the range of metals for example is more limited than those used with laser processes. But it is interesting to be able to play on the powder/binder combination according to the desired application.
It is also a technology that allows the production of large parts – depending on the capacity of the machines of course. Indeed, binder jetting carries out its printing stage at room temperature, which eliminates the risk of thermal distortion – there is no warping, for example. The user will therefore be able to imagine larger and more complex parts. Lefteris Havouzis of Lino3D adds: “If we compare with other technologies in the metal industry, we should mention in general a greater freedom of design, a reduction in manufacturing and marketing time due to the absence of tools and a greater complexity of the production mix that we can achieve. In the same print, we can print dozens of different batches without any changes.”
In addition to the volume of the parts, the relative speed and simplicity of the process can also be mentioned. Andreas Müller commented: “Binder jetting is renowned among additive manufacturing methods specifically for its high volumetric output. Among additive manufacturing technologies, it’s also the most similar to traditional printing with its simple approach and speed. The binder functions like the ink as it moves across the layers of powder, which like printing on paper, forms the final product. By contrast, many other forms of 3D printing build parts with a single point — often a laser or nozzle — that extrudes, melts or welds material together. Such processes require significantly more material and time to draw out each part with a single point, layer by layer.” Binder jetting machines in contrast can deposit many droplets of binder in one pass, reducing manufacturing time and increasing productivity. Take note, however, that post-processing steps can lengthen the process.
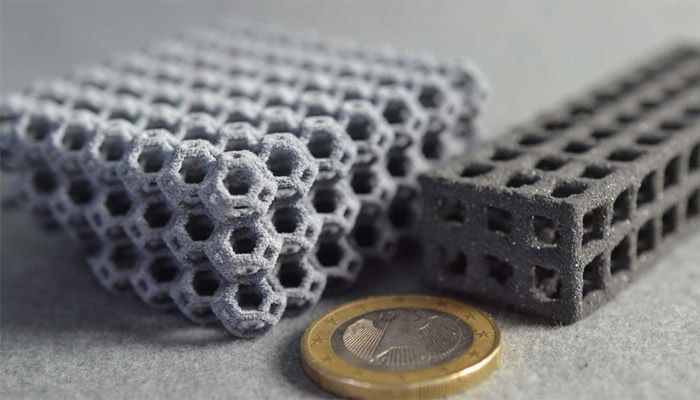
The use of ceramics requires post-processing (photo credits: WZR)
Post-processing is one of the ultimate limitations of binder jetting, especially when using metal and ceramic powders. You have to go through debinding and sintering steps that will add time but also affect the final part. Lefteris from Lino3D says: “When looking at the technology, it is important to mention that the critical phase of Binder Jetting is the sintering phase where several phenomena have to be taken into account. Working with a partner that can manage the entire value stream can then be very interesting.”
The result will be a more porous part with weaker mechanical properties. Vincent Poirier concludes: “The more the powder has the ability to settle well, the less porous the preform and then the ceramic part will be. It is therefore essential to choose the right powder and opt for spherical powders.
A Few Last Words of Advice
The most important keyword is INTEGRATION: Binder Jetting, like any other manufacturing technology, is not a stand-alone solution, but to realize its potential, it must be integrated into the company’s ecosystem, from design to post-processing. – Lefteris Havouzis
Sand 3D printing is a flexible production technology. It’s suitable as a fast manufacturing method for producing sandcasting tooling and can also be used to produce unique end-use products. The important thing to consider is the right combination of technology and material to suit those needs. At ExOne we offer an all-round sand 3D printing support, with a service center for our European customers right here in Germany where we walk customers through the different options and evaluate the best solution to solve their production challenges. – Andreas Müller
For ceramics, you need to have a very specific application that unequivocally requires this technology. As with other ceramic additive manufacturing technologies, we cannot cover all cases. In addition, it is important to understand that the know-how is not only in printing. Ceramic know-how is also important to master, for example, firing cycles and the consequences of sintering shrinkage on the finished products. – Vincent Poirier
Do you use binder jetting? Let us know in a comment below or on our Linkedin, Facebook, and Twitter pages! Don’t forget to sign up for our free weekly Newsletter here, the latest 3D printing news straight to your inbox! You can also find all our videos on our YouTube channel.
*Cover Photo Credits: Tecnalia