3D Printed Medical Implants: Discover Some of the Most Innovative Projects
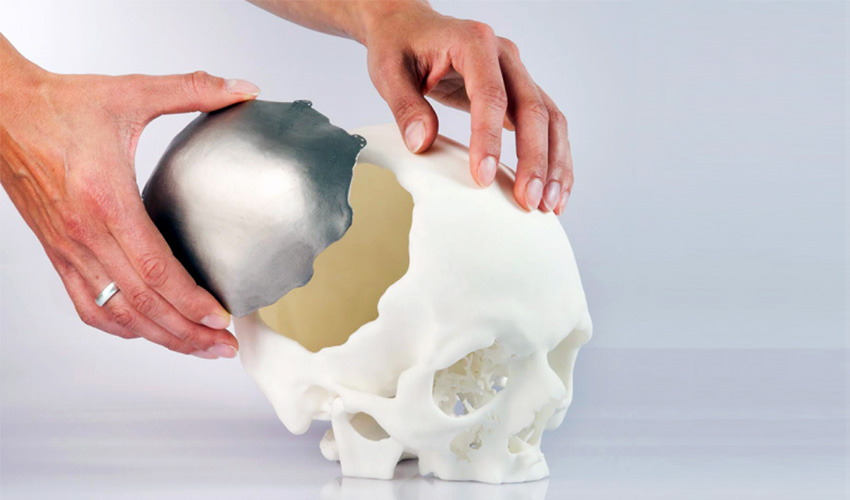
The medical sector is benefiting greatly from advances in additive manufacturing. Thanks to the ability to create unique models for each patient, personalized medicine is finally becoming a reality. Medical implants represent a particularly sensitive field, as they involve the introduction of an external element into the body to replace a failing function or treat a disease. To ensure optimum compatibility, these implants need to be custom-designed, which explains why additive manufacturing has become indispensable in this field. To better understand the current state of implant development, the 3Dnatives team has compiled a selection of implants manufactured using 3D printing. This ranking includes implants already approved as well as others still in the research phase, illustrating the potential and continuing progress of this technology in the medical sector.
3D Printed Implants for Ear
The hammer, anvil, and stirrup are three bones located in our ear, the smallest in our human body because they do not grow after birth. Their shape, size, and position are therefore very important for the proper functioning of the ear. However, sometimes these bones break and need to be replaced. This is what happened in South Africa where a patient had 3D printed titanium bones implanted following a car accident. After a 3D scan of his middle ear, the team of surgeons behind the operation was able to model a bespoke implant, which was then printed on a powder bed laser fusion machine. Titanium was favored in this case for its biocompatibility and strength.
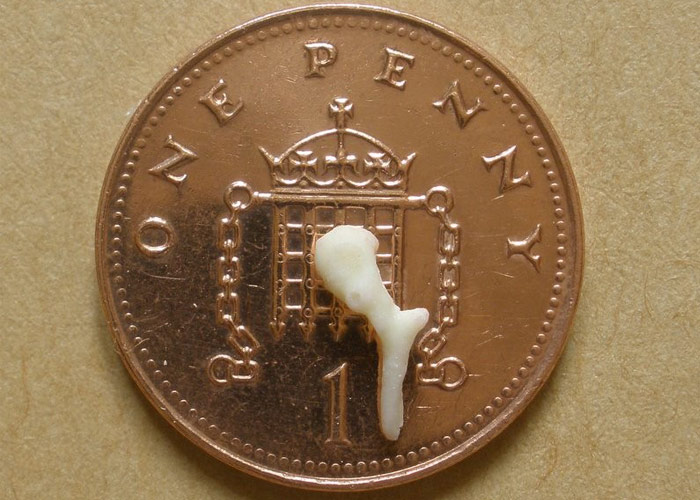
Ossicles are among the smallest bones in the human body. The picture shows a real ossicle and not the implant
3D Printed Jaw Implant After Tumor Removal
Anelia Myburgh, is an Australian woman from Melbourne who improved her quality of life thanks to additive manufacturing technologies. Due to a malignant tumor located in her jaw and teeth, the doctors were forced to remove it, which caused a disfigurement in the woman’s face by losing more than 80% of the jaw. The case of de Myburgh led maxillofacial surgeon George Dimitroulis to explore the possibilities of additive manufacturing for the creation of custom models. Thus, he created a jaw implant with a titanium frame capable of incorporating bone grafts. After more than 5 hours of surgery and several months of recovery, we can affirm that the operation was a complete success and the advances in this technology gave Anelia the security and confidence in her life.
Renishaw’s Rib Cage
Due to breast cancer, 71-year-old Welshman Peter Maggs underwent an 8-hour operation to remove the tumor. In the surgical process, three ribs and part of his sternum were removed, so doctors looked for a way to replace the missing parts. To do this, they turned to metal additive manufacturing, specifically Renishaw solutions, in order to create a high-quality, biocompatible model of the rib cage. Cardiothoracic surgeon Ira Goldsmith explained that one of the main benefits of using a 3D printed prosthesis is that it can be completely customized and tailored to the patient. And he proved it, offering Maggs a fast and efficient solution.
3D Printed Silicone Heart Valves
Of course, implants do not just include bones, though those are easier to create and thus more prolific on the market. Recently, we have also seen examples of implants for parts originally made from organic tissue. For example, this case of a bioinspired heart valve prosthesis, which was made using silicone AM. Created in a collaboration between a team of researchers from ETH Zurich and the South African company Strait Access Technologies, these artificial 3D printed heart valves were created as a way to replace valves in an aging population. The researchers decided to create the valve out of silicone as it is compatible with the human body. Additionally, by using 3D printing they would be able to make a valve that is a more perfect match to the patient. It should be noted that though the initial results were promising, they estimate that it will take another 10 years before these 3D printed heart valves could actually be on the market.
A 3D Printed Carbon Artificial Retina
An additional application for 3D printed beyond bones is for retinas. In this case, an Australian engineer developed a 3D-printed artificial retina made out of carbon to help people see again. Dr. Matthew Griffith from the University of Sydney made a breakthrough when he realized that essentially, like a computer, a body is just a carbon-based semiconductor. With this knowledge, he determined that he could replicate an eye by creating a carbon (and thus fully bio-compatible) device that absorbed light and then created an electronic charge, exactly like an eye. Furthermore, thanks to low-cost manufacturing with 3D printing, it was entirely possible for him to design this artificial retina himself. Though the device is not actually completed yet and will not even go to clinical studies until the next three to five years, Griffith is hopeful that it will be useful for patients who have lost their sight, even potentially restoring color vision which is not currently possible.
Restorative Oral-maxillofacial Implants
AB Dental uses Selective Laser Sintering (SLS) to create customized Implant Systems and has innovated the technology and application in the oral-maxillofacial field. The company’s system allows doctors to plan dental and facial restoration treatments with more precision compared to traditional methods. The company offers several restorative 3D printed implants for patients, including sinus roof augmentation, orbital bone repair, and a subperiosteal implant for resorbed jaws.
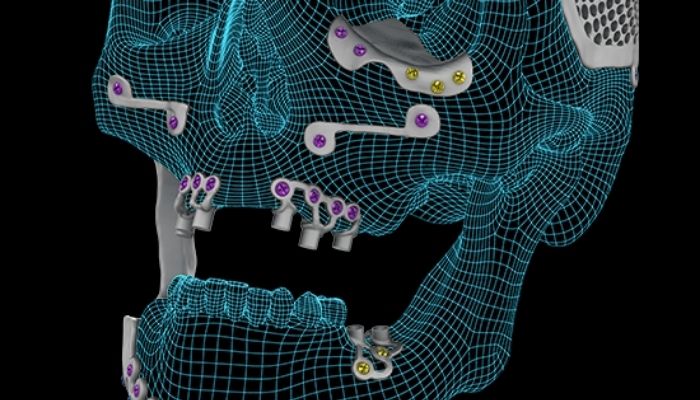
Photo Credit: AB Dental
Customized Microporous Bones
With the trademarked motto “We Print Bone”, Particle3D was launched in 2014 by two medical engineering students and their professor with the goal of developing a new solution for replacing destroyed or surgically removed bone. Today, Particle3D is further developing patient-specific bone implants based on a patient’s own CT/MRI scan which results in 3D printed implants that provide uniquely bone-like internal architecture containing micro- and macro porosities—just like real bone.
Partially 3D Printed Cartilage Implant to Fight Osteoarthritis
In humans and dogs, a tiny layer of cartilage preserves joint surfaces and allows bones to glide together properly. Unfortunately, over time, this cartilage breaks down, resulting in osteoarthritis and therefore joint pain. To overcome this, researchers at North Carolina State University developed a textile-based implant containing cartilage derived from the patient’s stem cells. Partly 3D printed, this type of implant has been successfully tested on a group of dogs with hip problems. This group was split into two, and one part received the implant and the other did not. As you can imagine, the dogs that received the implant recovered to their full potential 4 months after the operation.
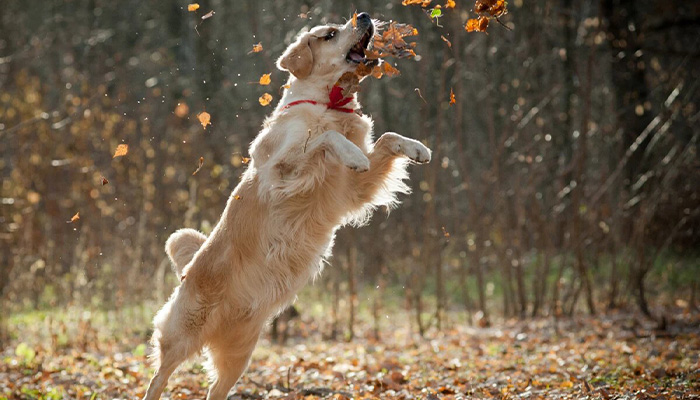
Photo Credit: Deposiphoto
The World’s Largest 3D Printed Cranial Implant
Startup Arcomedlab has achieved the feat of creating the world’s largest cranial implant using 3D printing. Since its inception, Arcomedlab has handled over 600 real-life clinical cases, specializing mainly in cranial reconstruction with customized implants, as well as custom facial reconstructions. In addition, they have carried out a variety of complex surgical planning procedures. Currently, this company is able to completely reconstruct the skulls of patients of all ages, as well as any facial bone structure, using FDM and SLA 3D printing technologies for medical purposes. Thanks to these technological advances, they are pushing back the boundaries of reconstructive medicine, offering innovative solutions tailored to each patient’s specific needs.
The ELAINE Research Project
As part of the ELAINE (Electrically Active Implants) research project, researchers at the University of Rostock are developing bioactive structures for bone replacement. Currently, titanium implants are commonly used, but they have limitations: their adaptation to the body’s anatomical conditions is imperfect, and they can loosen over time, causing long-term problems. To overcome these challenges and improve the treatment of bone defects, scientists are exploring the possibilities offered by additive manufacturing. They are working on electrically active implants that mimic the behavior of natural bone structures, drawing inspiration from bone physiology. The material chosen is barium titanate, capable of releasing ions on contact with body fluids. The technology used to create these implants is LCM, a light-curing technique. This process involves the use of polymers loaded with piezoceramic particles, which are then placed in a printer to create a fine structure by photohardening, giving the material its biocompatibility. 3D printing has the added advantage of enabling the manufacture of tailor-made implants, adapted to each individual patient. Although this project is still in the research phase, it is envisaged that these implants could be in clinical use within the next ten years.
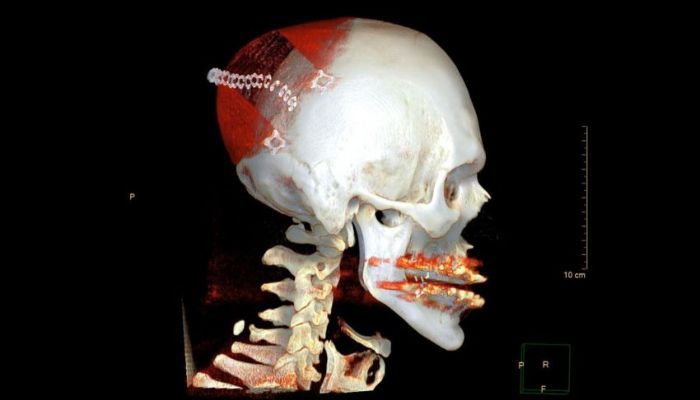
(Photo Credits: University of Salzburg)
The ‘MyBone’ Bioprinted Nose Graft
A collaboration between Toulouse University Hospital, the Claudius Regaud Institute, and the Belgian company CERHUM led to the successful reconstruction of a cancer patient’s nose using 3D printing in 2022. The procedure involved the creation of a custom bioceramic implant, coined ‘MyBone,’ which mimics human bone and promotes osseointegration and osteoconductivity. After a detailed scan of the patient’s face, the implant was 3D printed using stereolithography. Initially placed in the patient’s forearm to promote vascularization and cellular colonization, a process where the cells grow into the structure of the implant, the nose was later transplanted to the patient’s face, where it was connected to her blood vessels through microsurgery. This method provided a high level of biocompatibility and durability while reducing the risk of infection and the need for future replacements. The procedure resulted in the successful transplantation of a fully functional and aesthetically pleasing nose, highlighting the potential of 3D printing in major reconstructive surgery.
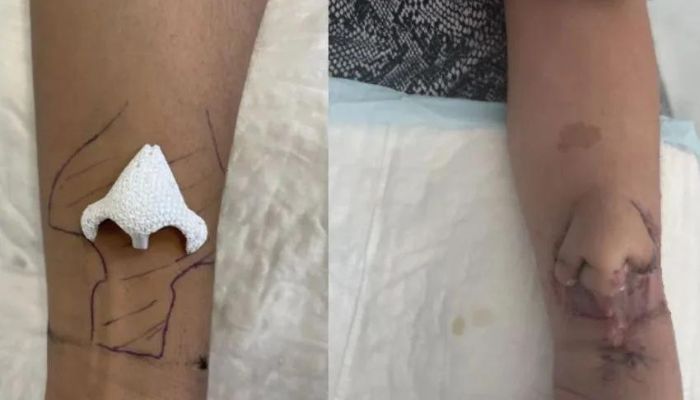
(Photo Credits: Toulouse University Hospital)
BellaSeno: 3D Printed Breast Implants
BellaSeno manufactures breast implants made from polycaprolactone, a suture material commonly used in the healthcare sector, using 3D printing. These 3D printed implants are intended for people with breast cancer or other breast diseases, and are designed for use in reconstructive and plastic surgery. BellaSeno has developed a 3D printing solution that supports clinically compatible materials. These implants are designed to completely resorb within five years, during which time they are replaced by natural fat cells in the body. The first ten patient tests have shown promising results, with positive patient evaluations and a good safety profile for the 3D implants. Surgeons have also given positive feedback on the use of these 3D printed implants.
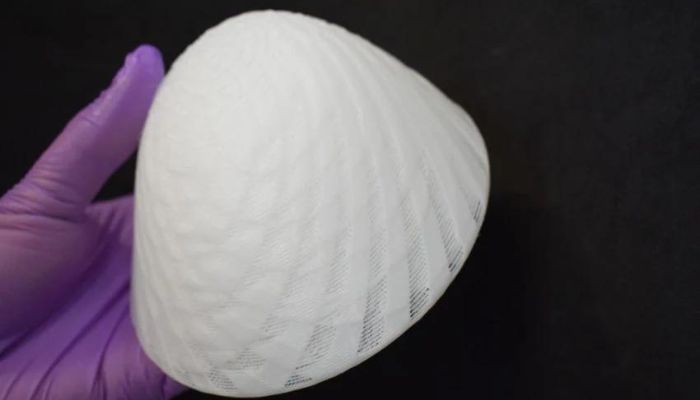
(Photo Credits: BellaSeno)
An Implant to Repair Knee Cartilage
Nanochon’s mission is to facilitate cartilage replacement and repair for patients suffering from knee injuries. To achieve this goal, the company is using 3D printing technology, in particular the extrusion technique, to create an implant designed to replace damaged or lost cartilage. The device, called Chondrograft™, is made from an innovative biocompatible composite material that promotes tissue regeneration. The Chondrograft™ is additively produced by the molten filament manufacturing process, using Nanochon’s proprietary composite material. What sets this implant apart is its unique structure: in addition to its visible microstructure, it has submicron porosity. After post-treatment, this characteristic makes the implant more flexible and malleable, while maintaining its structural integrity.
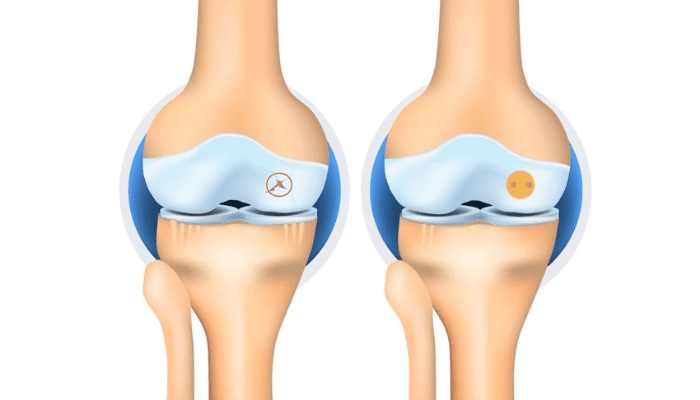
(Photo Credits: Nanochon)
Matricelf Bone Marrow Implant
In 2022, Matricelf, an Israeli regenerative medicine company, achieved a breakthrough by successfully testing 3D printed spinal cord implants on mice with chronic paralysis. The implants demonstrated an impressive 80% success rate in restoring the ability to walk. Matricelf’s technology begins with a biopsy of the patient’s omental tissue, which undergoes a proprietary decellularization process to create a durable hydrogel. Simultaneously, induced pluripotent stem cells (iPSCs) are derived from the patient’s mature cells and integrated into the hydrogel. This process results in the development of patient-specific neural implants capable of repairing damaged spinal cord tissue. While the implants are currently in the experimental stage with animal testing, researchers are optimistic about their potential to revolutionize treatment for spinal cord injuries caused by accidents and sports injuries. Matricelf has filed patent applications in the USA and Europe as they continue to advance their research toward human applications.
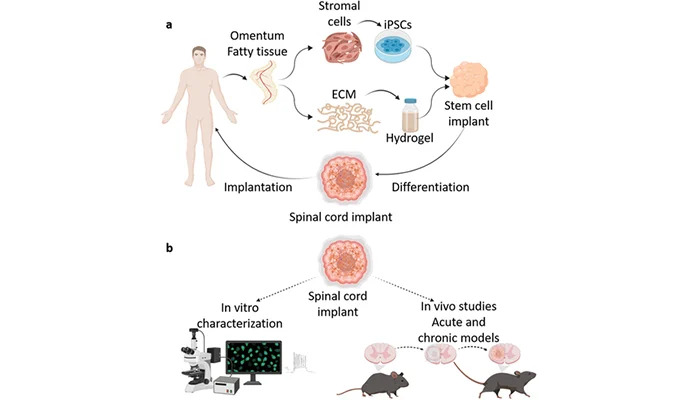
(Photo Credits: Matricelf)
3D Printed Ankle Replacement Implants
Macquarie University’s Limb Reconstruction Centre has dramatically enhanced ankle replacement surgery through their use of 3D printed implants, offering significant relief and restored mobility to patients suffering from severe ankle arthritis or trauma-induced joint deterioration. These implants, made from synthetic materials like hydroxyapatite, mimic natural bone structure and facilitate osseointegration, ensuring long-term durability while reducing the risk of complications post-operation. Unlike traditional ankle fusions and prosthetics, which limit mobility and may lead to further joint issues, these 3D printed replacement implants preserve joint movement and alleviate pain. The procedure, which has been led by orthopedic surgeons Dr. Tim O’Carrigan and Dr. Mustafa Alttahir since 2022, relies significantly less on the insertion of ankle screws and the removal of joint cartilage, resulting in faster recovery with enhanced mobility.
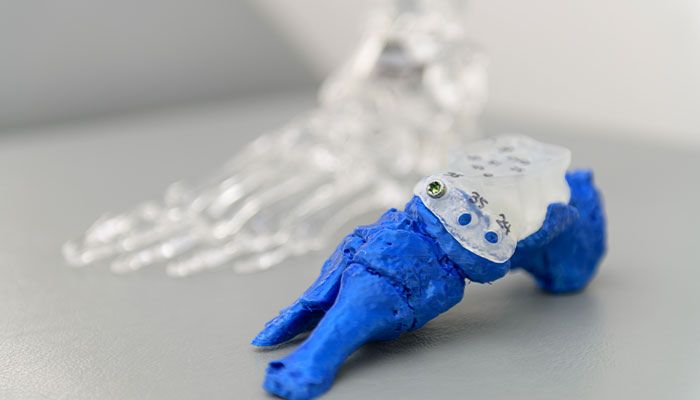
(Photo Credits: Macquarie University)
First 3D Printed Skull Cap for a Child
At the end of 2023, 10-year-old Felix was involved in an accident in which a piece of metal struck his head, penetrating his skull. This incident resulted in loss of vision and, despite emergency surgery, a large part of his skull cap remained destroyed. Doctors at the Salzburg Regional Hospital then re-imaged the skullcap in 3D. The main challenge was to recreate the skullcap without its previous state, based solely on CT images. In just five days, they were able to fabricate a PEEK implant for the skull cap and implant it during surgery. This is the first time a 3D-printed implant has been used on a child. The PEEK should pose no problems for Felix and should remain in his body for many years, requiring replacement by a larger model only when his growth requires it.
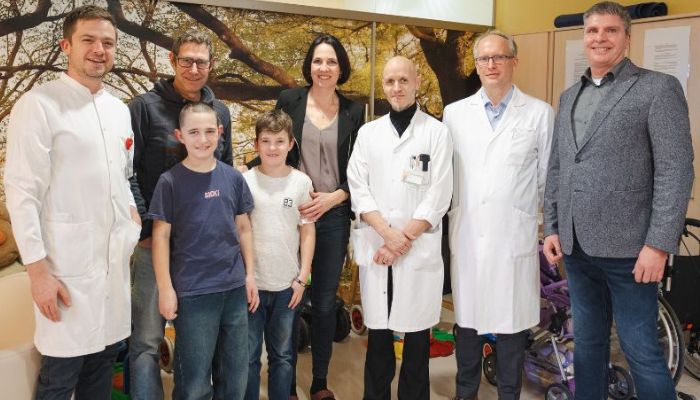
(Photo Credits: Salk / Leon Bernhofer)
What did you think of these 3D-printed medical implants? If you want to share some more we might have missed, you can leave a comment in the section below or on our Facebook and Twitter pages! Sign up for our free weekly Newsletter, all the latest news in 3D printing straight to your inbox!
Sir , I want to know the cost of different 3D printer for biomedical application ie. hip joint