#3Dstartup: Azul 3D and its ultra-fast large format resin 3D printer
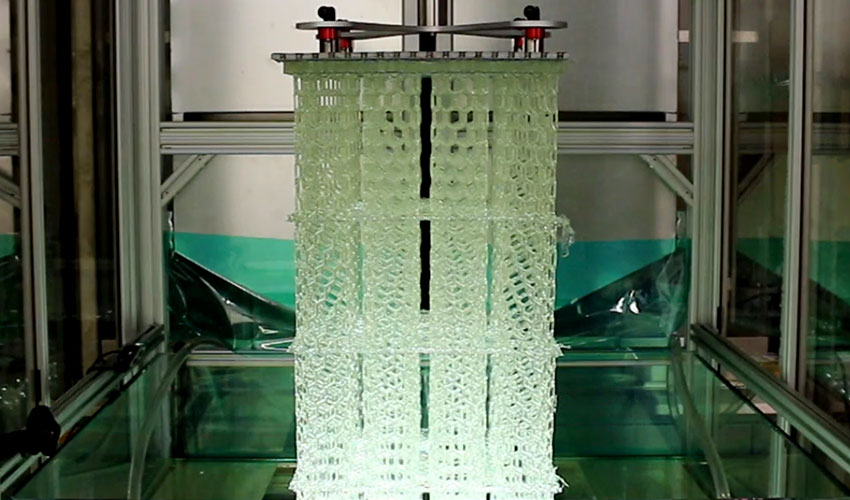
Resin 3D printing processes are now among the most widely used in the additive manufacturing market, offering high precision and resolution. One of the challenges this process still faces, however, is the limited size of the build plate and printing speed. The build process is rather slow and the machines do not allow for the design of large parts or volume production. However, some companies are innovating and developing promising methods, such as the American startup Azul 3D, which developed the HARP process. It has developed a machine based on photopolymerization capable of creating adult-sized parts in just 2 hours! We wanted to meet the team to learn more about this unique 3D printer that could well impact the resin 3D printing market!
3DN: Can you present yourself and tell us about your relationship with 3D printing technologies?
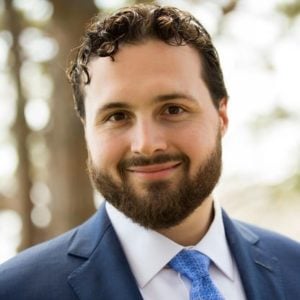
Dr. James Hedrick
I am Dr. James Hedrick, CEO and co-founder of Azul 3D which is commercializing the first 3D printing technology capable of competing with the speed, strength, and economy of scale of injection molding. I started my first company at the age of 16. The profits paid for my college tuition at MIT, where I was also a student-athlete. I went on to receive my Ph.D. at Northwestern University with Professor Mirkin, during which I was part of the team that developed seminal technology, HARP, at the core of Azul 3D. This HARP technology was my first approach to 3D printing that was first applied to nano 3D printing. We quickly pivoted to macro 3D printing in the months following.
3DN: How did you come up with the idea of creating Azul 3D?
I was doing my Ph.D. under the supervision of Professor Chad Mirkin. While working alongside a post-doc in the lab, Dr. David Walker, we started to develop a new nano 3D printer. Early on, we had a breakthrough with the technology but in the process realized we could print large structures with some modification to the technique in addition to printing tiny structures. We recognized immediately that with HARP, we had the ability to transform manufacturing. We transitioned our focus from nano to macro, and the three of us founded Azul 3D to transition the technology from the lab to the factory.
3DN: Can you explain how the HARP technology works?
HARP technology builds off of the field of stereolithography and liquid resin printing in general. The key innovation is the modification which is HARP. HARP utilizing a flowing liquid interface that does two key things at once. First, the movement of the interface enables a continuous pull with a fast vertical print rate. Secondly, it thermally regulates the temperature of the print which is key for printing large parts at these fast speeds.
3DN: What sector are you targeting?
Right now, we are not naming our customers but stay tuned. What I can say is we are working with companies that are ready to use 3D printing for manufacturing of end-use goods. We target sectors that do not have a long regulatory process in order to enable manufacturing sooner.
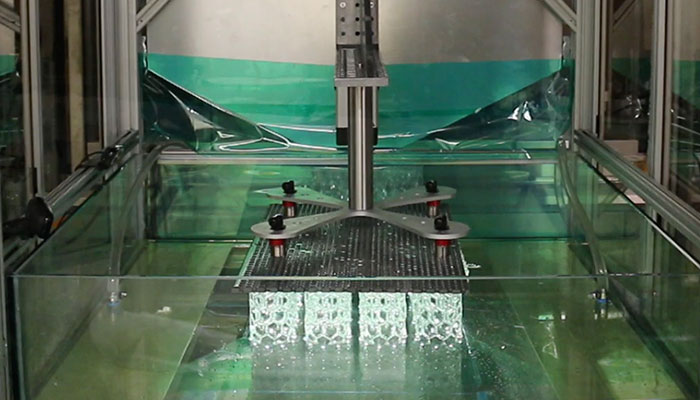
Azul 3D’s 3D printer
3DN: What are the importance and opportunities of large scale 3D printing?
Large scale 3D printing does not limit one to giant parts. It also enables medium-sized parts to be printed en masse. For example, we have been manufacturing face shields that are donated to healthcare workers and first responders across the country. With our smallest printer, we produced 10,000 face shields in 250 hours of print time. Not only that, but we have found our production costs to be cost-competitive against the traditionally manufactured face shields. The throughput and economics together show the possibilities the future has in store for HARP.
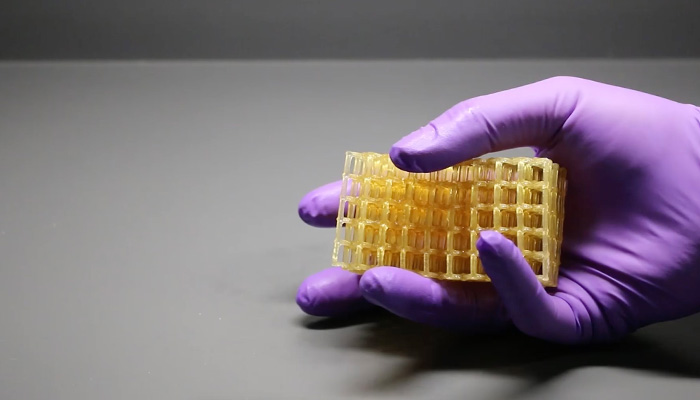
A part made with the HARP 3D printing process
3DN: Where do you see Azul3D in 5 years?
Over the next 5 years, I envision Azul 3D moving further into manufacturing. As a company, we have chosen to start small and focused. We work heavily with each customer to make sure they are able to manufacturer with our printer from the beginning. This enables us to maximize the impact each printer can have. It does stop us from going into every field we want to on day one. As we grow, this will no longer be a limitation. Also, I am also excited to see how customization software evolves. We have done production runs of custom parts and find the limitation is in the design, not the printing. In 5 years, I believe we will have customized manufacturing as a reality rather than a dream.
3DN: Do you have any last words for our readers?
If you have an application that you want to explore for 3D manufacturing, please reach out to co*****@****3d.com. The best fit for our printers today have come from customers as they know their process and product the best. You can find more information HERE.
What do you think of the HARP process? Let us know in a comment below or on our Facebook and Twitter pages! Don’t forget to sign up for our free weekly Newsletter, with all the latest news in 3D printing delivered straight to your inbox! You can find the #3Dstartup interview HERE.