Axtra3D Shows Its Expertise in Silicone 3D Printing and Molds at Formnext
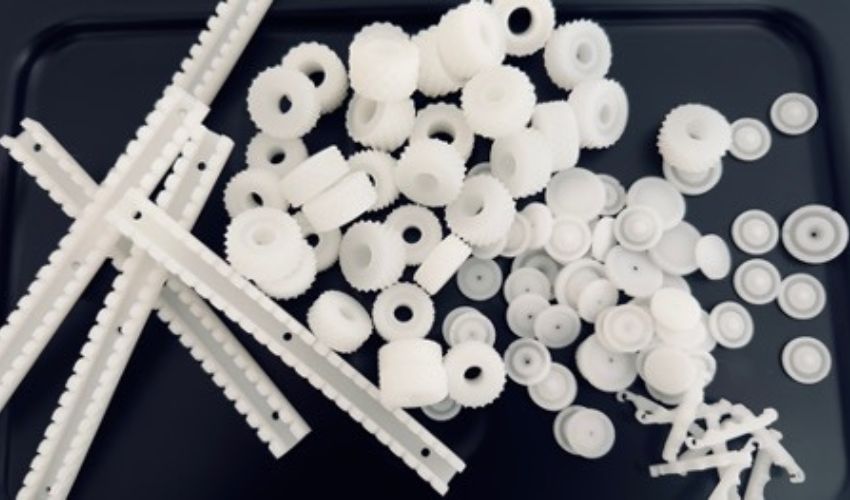
Axtra3D is one of the up-and-coming companies on the AM landscape, having made a name for itself internationally with its Hi-Speed SLA systems. The proprietary Hybrid PhotoSynthesis polymerization (HPS) process and the flagship Lumia X1 solution are indicative of Axtra3D’s determination to not compromise on print throughput, accuracy, resolution or surface quality. Building on the international success of the Lumia X1 SLA system, Axtra3D has continued to develop and will be showcasing numerous innovations at Formnext 2024.
To further extend the applications possible with the Lumia X1, Axtra3D has developed TrueSil-X50, a 100% pure silicone without any additives. This is specially tailored for use with the Lumia X1 system and is expected to set new standards in silicone 3D printing. The new material is characterized by its performance and durability, as it can withstand harsh environmental conditions. Its low viscosity makes it easy to process using 3D printing and allows the creation of complicated geometries with fine details, going down to the micrometer range, to be implemented. Furthermore, in addition to high resolution and precision, the surface quality of parts is also not compromised. Users can make reliable, waterproof, electrically insulating and isotropic parts, and even designs with very thin walls and complicated designs can be implemented.
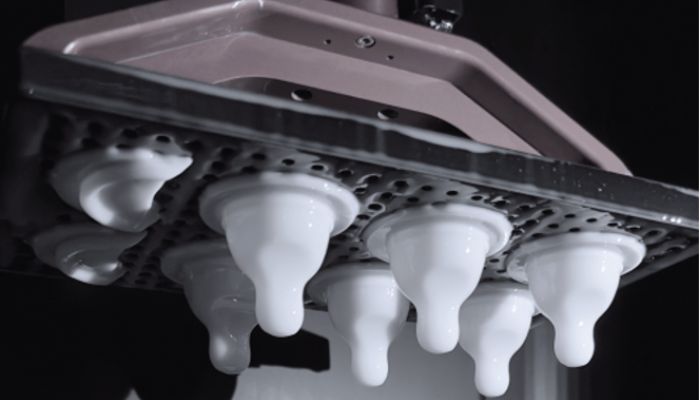
TrueSil-X50 is a 100% pure silicone for various applications.
These properties open a wide range of applications for TrueSil-X50, particularly in industry and healthcare. Specific applications include gaskets and seals, sanitary solutions, household appliances and food processing. In the medical sector, the flexible and biocompatible TrueSil-X50 can be used for implants, hearing aids and mouthguards, as well as anatomical models and applications in dentistry.
Rajeev Kulkarni, CSO of Axtra3D, sums up the advantages of the material: “The combination of silicone’s unmatched durability and Axtra3D’s Hybrid PhotoSynthesis technology makes TrueSil-X50 invaluable in both healthcare and industrial sectors. It’s not just the properties of the material itself; it’s the optimized synergy between silicone’s impressive mechanical strength, high tear resistance, and our HPS technology’s precision and detail that brings the performance to a new level. This enables the creation of safe, long-lasting medical devices and high-performance industrial components that were previously unattainable. TrueSil-X50 truly sets a new standard in durability, resolution, and application flexibility.”
With the introduction of TrueSil-X50, Axtra3D is responding to the market and the increasing demand for high-quality silicone solutions. The new material will be presented at the Formnext, taking place at the moment until November 22nd, and visitors will also be able to get an idea of various application examples. But that is not all Axtra3D has in store for us at Formnext 2024. The new solutions for molds will also be presented at the company’s stand in Hall 11.1, Stand C39.
Axtra3D to Present Comprehensive Mold Portfolio at Formnext 2024
Building on its previous success in ceramic injection molding solutions, Axtra3D will present three more solutions for concept and small series molds in Frankfurt, bringing the total to four. The solutions are produced using the company’s patented Hi-Speed SLA technology and the Lumia X1 and are aimed at different purposes. The individual mold solutions are each designed for a specific production process and include investment casting molds, low-pressure molds, high-temperature micro-injection molding and silicone molds. But what exactly can we expect?
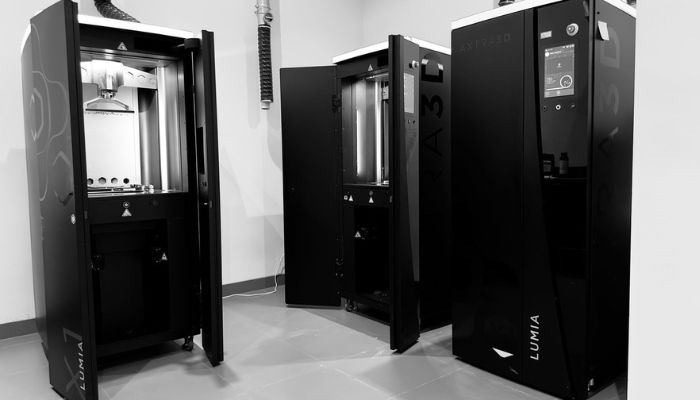
The Lumia X1 from Axtra3D
The investment casting molds made of Ultracur3D® RG 3280 ceramic are suitable for concept injection molding as well as small series production. These are solutions that are extremely rigid and can withstand high temperatures. High-temperature micro injection molding can also be used to create molds for high temperatures, which are primarily intended for use in the automotive or aerospace industries. In both cases, a high degree of durability and precision is required, which is ensured by the Figure 4 HI TEMP 300-AMB material.
However, if users are looking for molds made of high-viscosity materials, low-pressure molds made of Ultracur3D RG 1100 resin are best suited. These molds are very rigid, chemically resistant and robust, allowing them to also meet the requirements of high-performance sectors.
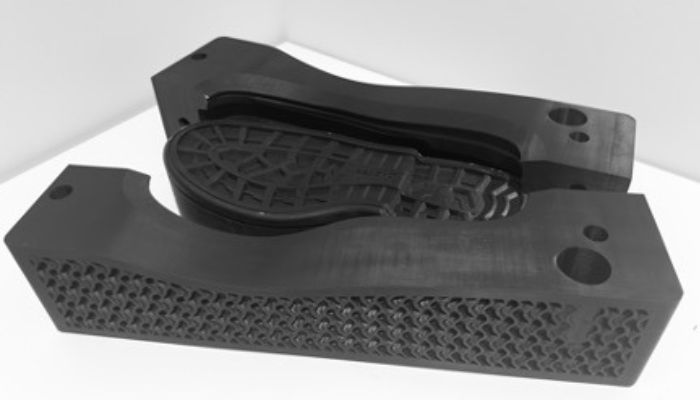
Rubber-like materials are difficult to process by injection molding, the Ultracure3D RG 1100 can be printed and rigid shapes can be 3D printed.
Meanwhile in healthcare, the solution for silicone molded parts is particularly impressive. These are created with the Lumia X1 from Ultracur3D ST 45 Black. The molds made from this material are characterized by high durability, tensile strength and thermal stability, so that they remain intact over several casting cycles. This solution was designed especially for silicone casting, where tight dimensional tolerances and a smooth surface finish are important.
Axtra3D’s proprietary HPS technology plays a key role in these new solutions, as Rajeev Kulkarni emphasizes: “Axtra3D’s mold solutions provide a faster, more flexible, and cost-effective alternative to traditional metal tooling, reducing lead times and enabling affordable small-batch production. This is achieved via HPS which combines laser precision with DLP for rapid, high-resolution mold production, and TruLayer technologies that boost print layer separation speed, surface finish, and quality. It overcomes all the limitations of conventional metal molds and furthermore, each mold solution is tailored to specific production needs.”
There is no doubt that the expanded mold portfolio strengthens Axtra3D’s position in the market and highlights its expertise in concept casting and molds for small series. This offers users a wide range of possibilities, as a wide variety of industries can benefit from it. This goes hand in hand with Axtra3D’s intention to constantly offer new ways of additive manufacturing and overcome prevailing hurdles.
At Axtra3D, our goal has always been to push the boundaries of what additive manufacturing can achieve, without compromising quality, speed, or material flexibility. We continue to work together with customers to develop solutions tailored to industry-specific requirements. This approach has ensured a strong alignment between Axtra3D’s technology offerings and the needs of industries where precision and performance matter most. – Rajeev Kulkarni
You can of course see all these solutions at Formnext 2024 and get in touch with Axtra3D. If you have the opportunity, be sure to stop by booth C39 in hall 11.1, otherwise you can find more information about Axtra3D by visiting their website or by downloading their recent Mold Solutions White Paper.
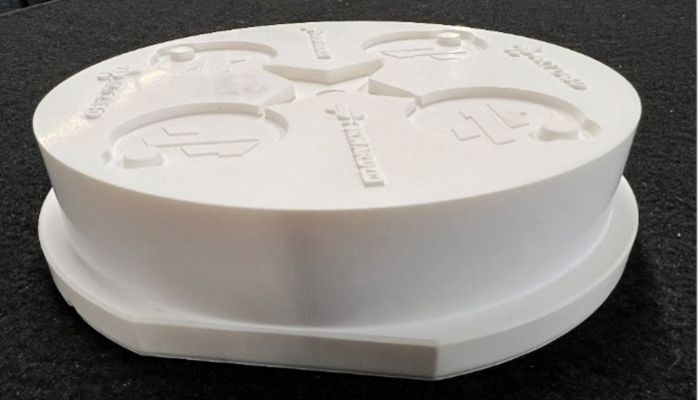
Ceramic Mold printed with Ultracur3D® RG 3280, a ceramic-loaded polymer
Will you be visiting Axtra3D’s booth? What are you most excited for? Let us know in a comment below or on our LinkedIn, Facebook, and Twitter pages! Don’t forget to sign up for our free weekly Newsletter here, the latest 3D printing news straight to your inbox! You can also find all our videos on our YouTube channel.
*All Photo Credits: Axtra3D