Avoiding Defects in Laser Powder Bed Fusion
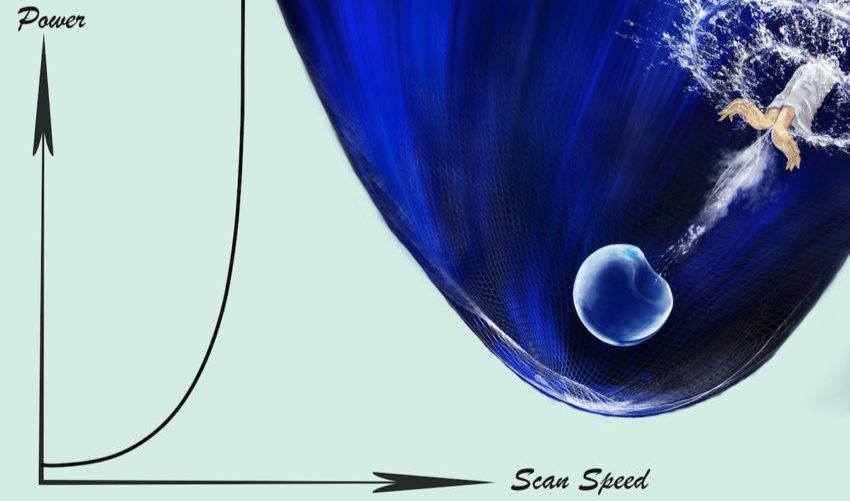
Researchers at Carnegie Mellon have discovered a way to avoid defects and increase the durability and resistance to corrosion of metal parts produced by Laser Powder Bed Fusion (LPBF). The research was primarily focussed on understanding how and why structural weaknesses develop during the printing process and drawing a solution from that information. The result of their findings was that it is possible to reduce the likelihood of defects and thus increase the structural integrity of the final product by increasing the speed and restricting the heat of the laser.
Laser Powder Bed Fusion (LPBF) is part of the Powder Bed Fusion (PBF) family, all of which use a build platform containing powder material to additively manufacture a part. The powder can either be a polymer or a metal. It wasn’t until the 1990s that several companies began to explore using Powder Bed Fusion for metal: metal powder particles were melted using a heat source such as a laser or electron beam to form a more or less complex part, layer by layer. Laser Powder Bed Fusion uses a laser to additively manufacture a metal part. The technology is currently the most extensively used metal additive manufacturing process. While Laser Powder Bed Fusion is good for creating parts with complex geometries, the products have limited durability and corrosion resistance.
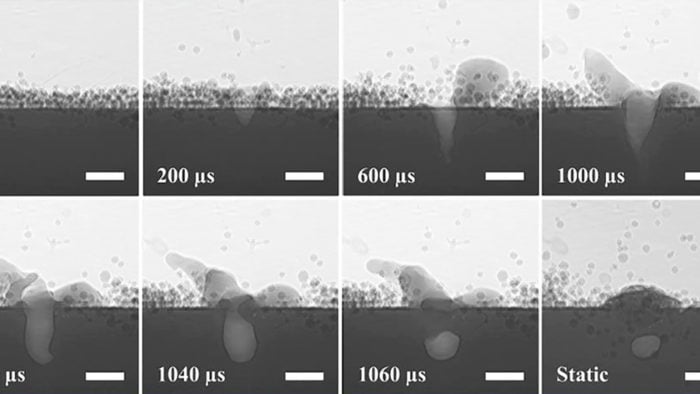
High-speed x-ray images of ‘keyhole’ defect forming taken by Researchers at Argonne in 2017. (Image via Argonne National Laboratory.)
When a slow-speed, high-power laser is melting metal powder, it can create keyhole-shaped cavities in the melt pool during the 3D printing process. This occurs under certain conditions where the depth of the molten pool is controlled by the evaporation of the metal as opposed to the conduction of heat in the underlying solid material. The evaporation of the metal can create deep and narrow vapour depressions, known as “keyholes”. Small bubbles or pores form at the bottom of the keyhole, becoming detrimental structural defects if trapped in the solidifying metal. Keyholes lead to porosity, which degrades alloy performance, especially fracture properties.
The research team examined unstable keyholes with bright high-energy x-ray imaging, building on research that quantified the keyhole phenomenon. They found that the instabilities are caused by fluctuations in the keyhole’s depth and increase strongly with decreasing scan speed and laser power on the unstable side of the boundary. These fluctuations generate acoustic waves in the liquid metal that force the pores away from the keyhole and later trapping them in the resolidifying metal.
According to Anthony D. Rollett, a professor of materials science and engineering at the Carnegie Mellon College of Engineering, “the real practical value of this research is that we can be precise about controlling the machines to avoid this problem.” The solution, then, is to define a minimum speed and maximum heat. “You can think of the boundary as a speed limit, except it is the opposite of driving a car. In this case, it gets more dangerous as you go slower. If you’re below the speed limit, then you are almost certainly generating a defect,” adds Rollett, “As long as you stay out of the danger zone [i.e., too hot, too slow], the risk of leaving defects behind is quite small.” You can read the report of their findings HERE.
What do you think of this new research? Let us know in a comment below or on our Facebook and Twitter pages! Sign up for our free weekly Newsletter, all the latest news in 3D printing straight to your inbox!