How to Reduce Costs by Automating Post-Processing in 3D Printing
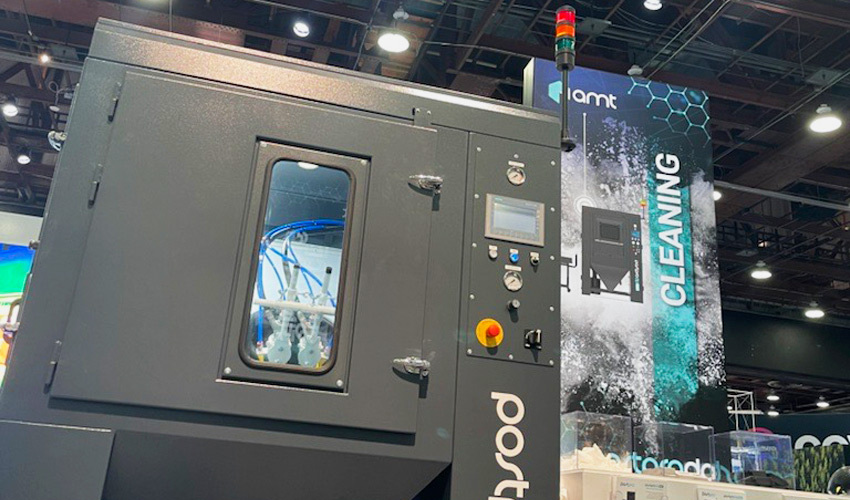
Process and workflow automation is a fundamental aspect of Industry 4.0. These types of automation systems serve to control and monitor a process, machine or device in a computerized way, with the goal of operating it automatically to improve production. As stated by Fortune Business Insights, the industrial automation market is expected to reach a value of almost $300 billion in 2026, which is double its value from back in 2018. All these collected data show us the vital importance of these systems today as they allow companies to optimize and improve the performance of all their industrial operations. This is also particularly relevant if we take it to the additive manufacturing sector where, though still requiring human labor, more and more automation solutions are being adopted for production and post-processing especially as AM continues to industrialize.
Against this backdrop, the international company AMT offers automated post-processing solutions for 3D printed parts. Thanks to the advantages provided by its solutions and innovative technologies, many of its customers have already managed to reduce manufacturing costs and optimize production. One of them is Blue-White Industries, a company dedicated to the development of devices, accessories and machinery for water treatment. Due to high capital investments, they began to evaluate the possibility of integrating 3D printing as an alternative to manufacturing molds for their products. They needed to adopt a solution that would increase production throughput and offer a durable and aesthetic surface finish. That’s when they turned to AMT.
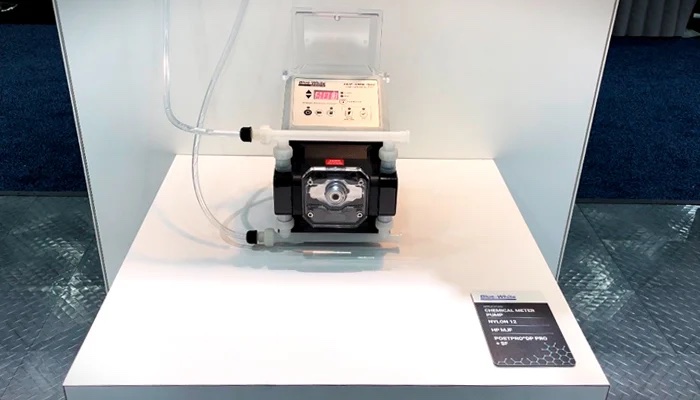
The CD1 pump developed by Blue-White Industries using AMT’s technology (photo credits: AMT)
Benefits of Automation in Post-Processing
When a company looks to automate certain processes in the supply chain, it is primarily looking to reduce costs, minimize errors and increase production traceability. Focusing on post-processing, automation allows companies to gain a number of benefits over other surface finishing systems. In the case of Blue-White Industries, teams needed to 3D print and post-process some of the components for its CD1 pump, which is responsible for delivering chemicals smoothly and continuously. Patrick Murphy, Director of Engineering at Blue-White Industries, commented, “We decided to adopt AMT’s PostPro Depowdering and Chemical Vapor Smoothing technology which enabled us to reduce bead blasting time, increase throughput, and overcome early part failure for running under maximum load conditions. All through a process that was repeatable and reliable.”
To optimize post-treatment, they integrated AMT’s PostPro DP PRO machine, a solution developed for cleaning and finishing 3D printed parts. This automated system allows parts to be treated easily and quickly, as it eliminates the most time-consuming and costly interventions in the supply chain. With it, the company has succeeded in unlocking new potentials and expanding its field of applications to different models. In addition to cost reduction and increased productivity, the adoption of PostPro DP PRO also offers many other advantages. Among them, we can find a considerable reduction in cleaning time and part finishing through depowdering and vapor smoothing. Linked to this, an increase in production throughput could also be seen thanks to the ample space on the machine and faster cycle times.
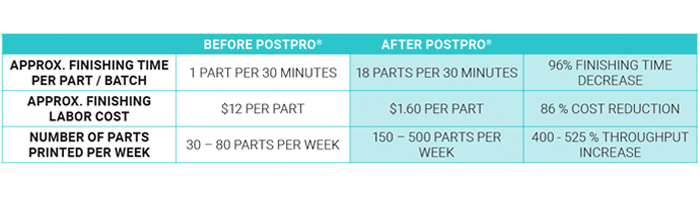
Blue White Industries saw both reduced cost and increased production thanks to AMT PostPro® automated systems (photo credits: AMT)
A Solution to Optimize Production
The Blue-White Industries team also claims that automated post-processing has helped to increase the strength, performance and aesthetics of its parts. This was done through AMT’s Chemical Vapor Smoothing technology. A combination of AMT’s automated depowdering and chemical vapor smoothing systems allows for a reliable and repeatable process from batch to batch. As for how the depowdering process works, the machine can clean large batches of parts gently and quickly, in as little as 10 minutes. Characteristic of this solution is also the generosity of the basket where post-processing takes place. With a capacity of up to 20 liters, the basket is easily removable, facilitating the loading and unloading of parts. In addition, its angle is automatically adjustable, offering optimal product rotation to adapt to different geometries and large batch volumes. All these properties make the PostPro® DP PRO an ideal solution for optimizing processes and achieving higher throughput in the production line. AMT PostPro depowdering machines can also be used for surfacing. Notably for this, they can be adjusted to suit specific requirements for parts as well as different technologies. This shows that AMT has a wide range of post-treatment solutions, with technology ranging from depowdering to surfacing and chemical vapor smoothing. The latter automatically smooths and seals the surfaces of 3D printed parts, achieving a surface finish with a look and feel similar to injection molding.
Industrial automation systems are very diverse and respond to the different needs of each sector. With this, we see the importance of incorporating new methods into the supply chain in order to generate value and take advantage of the many benefits they offer. You can learn more about post-processing automation on AMT’s website HERE .
What are your thoughts on post-processing automation in 3D printing?Let us know in a comment below or on our Linkedin, Facebook, and Twitter pages! Don’t forget to sign up for our free weekly Newsletter here, the latest 3D printing news straight to your inbox! You can also find all our videos on our YouTube channel.
*Cover Photo Credits: AMT