Automated Depowdering Systems for 3D Printed Parts
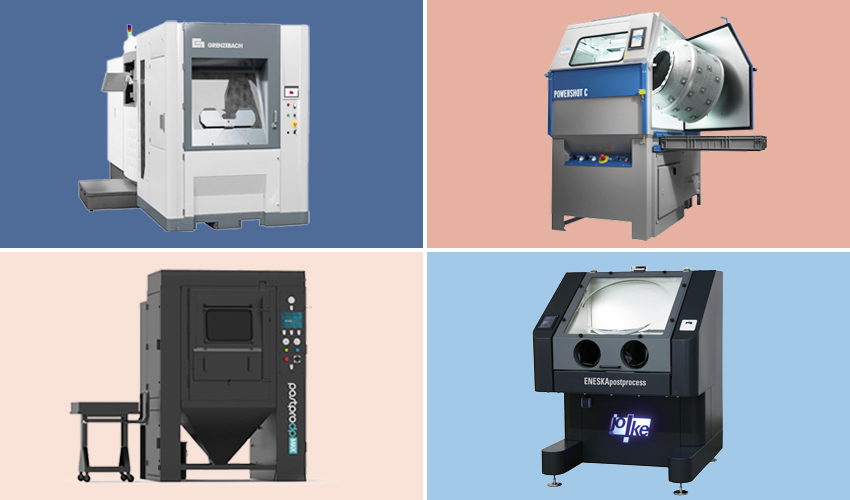
Post-processing after 3D printing is crucial for ensuring the quality and durability of the produced parts. This phase, occurring after printing, involves various processes such as cleaning, surface treatment, and removal of support structures. It is essential for all types of printing, whether large or small. For powder-based processes such as SLS, MJF, and Binder Jetting, depowdering is the first step. This process cleans the parts of residual powder and prepares them for further post-processing steps. Manual handling often produces insufficient results and is particularly useful for small parts and limited runs. This is why many users opt for automated depowdering systems, which save time and improve process efficiency. In this guide, we’ll present a few automated solutions for depowdering polymer parts, followed by depowdering systems for metal parts.
Solukon SFP770
The Solukon SFP770, designed by Solukon Maschinenbau of Augsburg, is an efficient system for automatic powder removal from molten SLS plastic parts. Serving as both an unpacking and cleaning station for polymer parts, it is compatible with the EOS P 770 and can be adapted for use with the FORMIGA P 110 and EOS P 500 through specific adapters. The cleaning process occurs in two stages: first, fully automatic deconditioning, which speeds up processing time, followed by the actual cleaning. The system is equipped with explosion protection, constructed from stainless steel with no ignition sources, and features ATEX-compliant components. Safety is further enhanced by suction and spray monitoring. Additionally, the SFP770 offers several practical functions, such as direct connection to the cleaning system and an ionized blasting device. A manual blasting device is also available for additional cleaning.
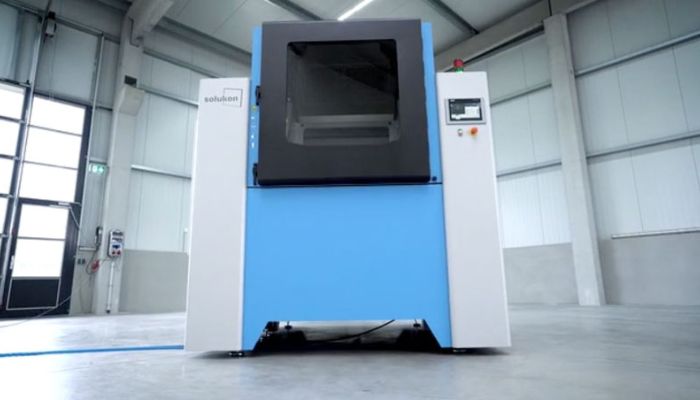
(Photo Credits: Solukon)
Pulvermeister Typ 5
Presented at Formnext 2022 in Frankfurt, the PULVERMEISTER Typ 5 is the latest finishing system from German company PULVERMEISTER, and an improved version of the Typ 4. This innovative system retains all the features of its predecessor, while adding advanced surface treatment to make parts ready for sale in a single operation. Typ 5 uses a patented process in which the abrasive is manufactured from the same material and with the same printer as the parts to be treated. Thanks to a contamination-free recycling process, using a special separation filter, shot particles are filtered from the stream and reintroduced into the blasting circuit. This method ensures a high-quality finish that’s both environmentally friendly and cost-effective.
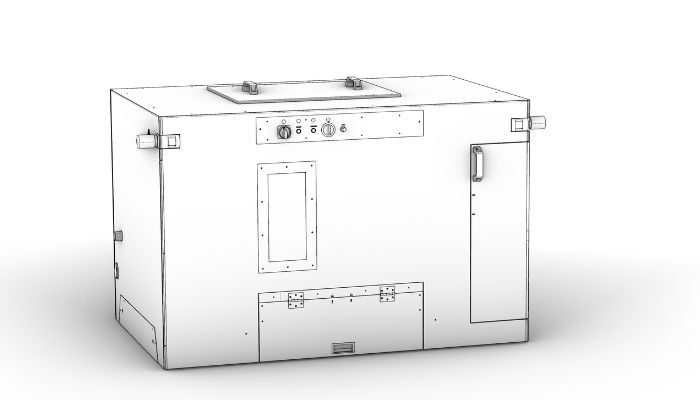
(Photo Credits: PULVERMEISTER)
AM Technologies PostPro DP MAX
The PostPro DP MAX is an industrial de-powdering system developed by Additive Manufacturing Technologies (AMT), a company offering post-processing solutions for 3D printed parts. Part of a diverse range of de-powdering systems, including the DP Studio, DPX, and DP Pro, PostPro DP MAX stands out for its highest post-processing volume, with a capacity of 63 liters. This system makes the process fully automated to maximize throughput. Compatible with plastic powder technologies such as SLS, MJF and SAF, the PostPro DP MAX is CE and ATEX certified. It is designed for use in environments where consumable media and generated dust may be combustible, guaranteeing safety and efficiency.
Avia Tools DP1000
The DP1000 is an advanced depowdering system from Avia Tools, designed to handle parts up to 1 metric ton and 1.5 meters tall with its volume of 62” x 63” x 99”. It features an optional, atmospherically controlled cabin, and motorized CNC capabilities for ease of use. The DP1000 leverages percussive manipulation and 360-degree axis rotation to ensure thorough cleaning, especially for complex parts like rocket end nozzles. It also contains inert gas processing for reactive metal powders and programmable repeatable cleaning cycles, and allows easy loading of large parts through roof access (an additional optional feature) and a built-in side door. With a substantial working envelope of 480 x 480 x 1000mm, the DP1000 offers a versatile solution for those looking to enhance the automated depowdering process.
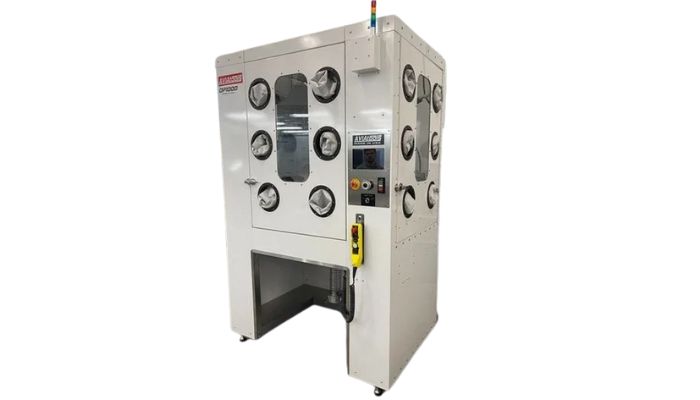
(Photo Credits: Avia Tools)
DyeMansion Powershot C
Germany-based DyeMansion is renowned for its post-processing solutions for additive polymer manufacturing, offering a comprehensive range of machines for surface finishing, part cleaning, and coloring. Today, we take a look at the Powershot C, an efficient solution for cleaning plastic powders. This machine features an automatic system with manual loading. The depowdering process is simple: parts are loaded into the machine basket, the program is selected, and after 3 to 10 minutes, the parts come out clean. With dimensions of 1700 mm x 1310 mm x 2030 mm, it can process up to 26 liters in just a few minutes. The Powershot C is used across various sectors, including medical, consumer goods, manufacturing, mobility, and transport, offering a versatile solution for many applications.
Spengler Vibroblast
Spengler, an emerging company in the IntegrAM group, offers cutting-edge solutions for 3D printing post-processing. In particular, it offers the VibroBLAST Air machine, an automatic 2-in-1 tool for part dewinding and pre-finishing. The VibroBLAST Air is designed to process plastic parts resulting from 3D printing using selective laser sintering or HP Multi Jet Fusion. What sets this solution apart, according to the manufacturer, is its ability to treat parts with great delicacy, without altering their surface or quality. This machine is also at the heart of the DCK 01 automated all-in-one solution, offering a complete process including de-soldering, surface finishing, as well as powder screening, recovery and mixing.
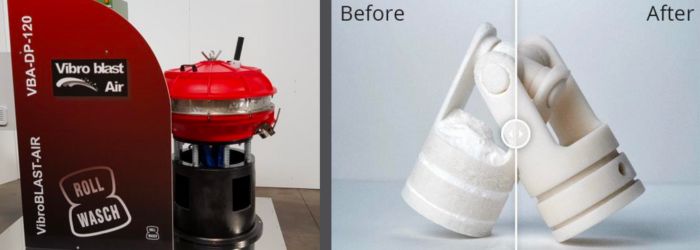
(Photo Credits: Spengler)
Solukon SFM-AT350/-E
SFM-AT350 systems from Solukon, a German machine manufacturer, are widely adopted for the de-soldering of metal parts resulting from additive manufacturing. Equipped with a turntable, these machines offer great flexibility of movement, and also allow manual de-soldering if required. A material lock collects the removed metal powder. Since October 2023, the de-soldering system has been available in two variants with different excitation modes: pneumatic for the SFM-AT350 and piezoelectric for the SFM-AT350-E, promising gentle, self-regulating de-soldering. The new versions are compatible with Solukon’s SPR-Pathfinder software, which calculates an individual movement pattern for each component, ensuring thorough cleaning. Solukon has recently enhanced its machines to enable cleaning of medium-sized parts up to 100 kg and sizes up to 400 x 400 x 400 or 500 x 280 x 400 mm. These systems are now compatible with the EOS M400 and Nikon SLM 500 printers. The machine itself weighs 650 kg and requires a space of 2,300 x 2,300 x 2,300 mm.
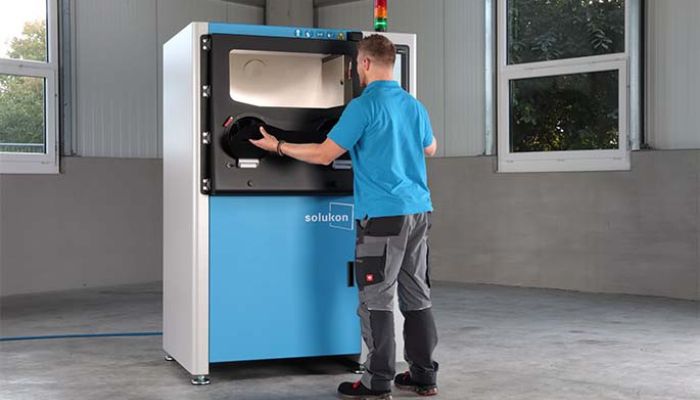
(Photo Credits: Solukon)
Addiblast MARS03
Addiblast, a Slovenian company, presents the MARSO3 machine, a specialized solution designed for depowdering complex metal parts or those with internal channels. With a capacity of 200 kg and a working area measuring 850 mm x 900 mm x 1000 mm, it features an automatic cleaning system, complemented by resistant gloves for manual work. The desoldering process occurs within a sealed chamber, where parts are cleaned through vibration on a rotating table. The MARSO3 integrates three crucial post-processing steps: desoldering, recycling of remaining powder, and surface treatment of printed parts. Weighing 1800 kg, it is an ideal choice for post-processing components in aerospace, medical, automotive, and industrial foundry applications.
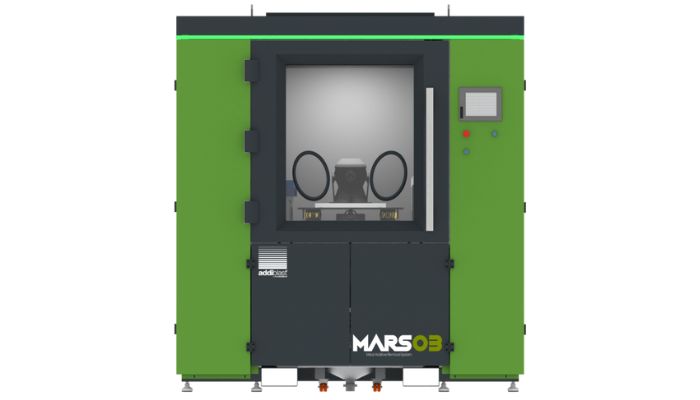
(Photo Credits: Addiblast)
Volkmann DPS Metal
German company Volkmann specializes in powder handling and material transport, striving to develop solutions to automate and facilitate this task. One of its branches is dedicated to additive manufacturing, and it has designed several post-processing systems, including de-powdering solutions. The one we’re particularly interested in today is the DPS Metal 1 model which, as its name suggests, has been designed for metal powders. The operator can place his printing plate directly into the machine, which then turns it over and uses compressed air or inert gas to remove the excess powder. The DPS Metal 1 machine then proceeds to a complete de-powdering and cleaning of the part. The DPS Metal 1 then cleans the part in a closed chamber and ensures complete de-powdering.
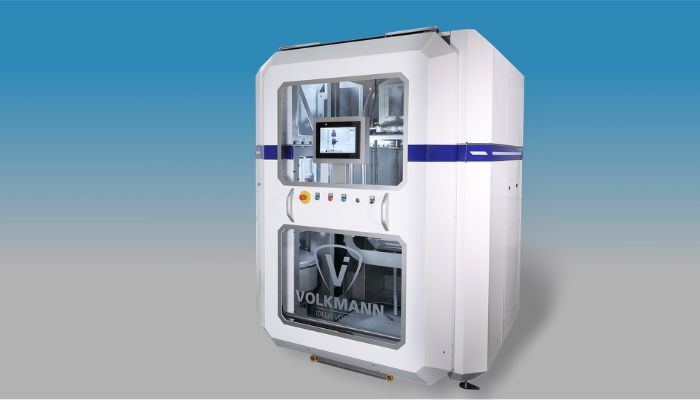
(Photo Credits: Volkmann)
Grenzebach Dual Setup Station
The Grenzebach Dual Setup Station offers an automated solution for de-soldering 3D metal prints, guaranteeing a safe process for printed products. By automating powder removal, this solution reduces downtime for industrial 3D printers due to cooling, unpacking and setup. This optimizes the use of additive manufacturing with metal powder, increasing productivity and reducing the need for manual labor. Thanks to the Grenzebach Dual Setup Station, unit costs per part are significantly reduced. Risks to employees are also minimized: exposure to dust and hot objects is limited, reducing the need for costly personal protective equipment and technical protection measures.
Joke ENESKApostprocess
The Joke ENESKApostprocess is a specialized solution tailored for finishing 3D prints. It effectively cleans powder residues, removes substrate plates and supports, smoothens surfaces, and executes various processing tasks. With a generous working area measuring 940 x 790 x 250-600 mm, this machine employs a compressed air gun to eliminate dust, even from challenging corners, eliminating the need for protective clothing. The ENESKApostprocess is fully enclosed to mitigate health risks associated with dust exposure. It features efficient suction and filtration systems, ensuring no dust escapes during operation. Prior to opening the unit, an additional 10-second suction phase is activated for safety, after which the glass dome is unlocked to facilitate the removal of the finished part.
What do you think of these automated depowdering systems? Let us know in a comment below or on our LinkedIn, Facebook, and Twitter pages! Don’t forget to sign up for our free weekly newsletter here for the latest 3D printing news straight to your inbox! You can also find all our videos on our YouTube channel.