Audi Sport Enhances Production and Tooling with 3D Printing
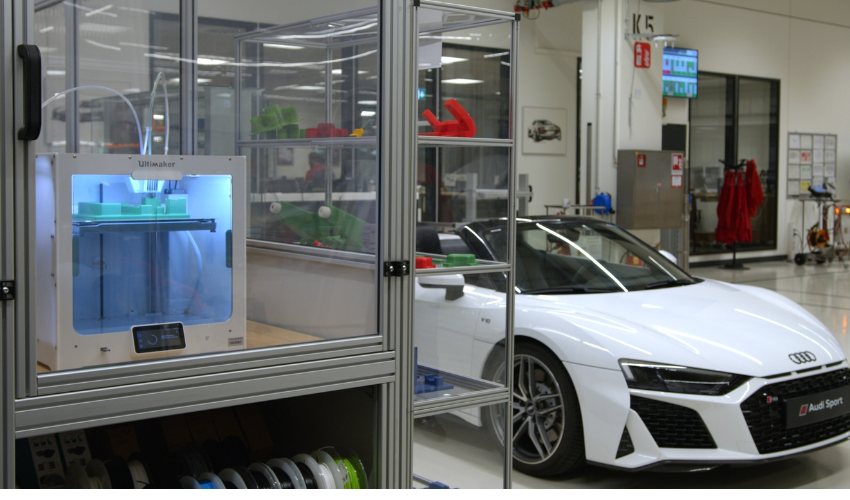
Following the emerging trend of increased use of 3D printing in the automotive sector, Audi Sport‘s Böllinger Höfe facility in Germany, renowned for developing high-performance vehicles like the Audi R8 and the fully electric E-Tron GT, recently adopted the technology to overcome a significant production challenge.
The introduction of the E-Tron GT required nearly 200 specialized tools, jigs, and fixtures, a process that traditionally demanded extensive time and resources. However, thanks to the integration of 3D printing and Trinckle’s Fixturemate software, Audi Sport has transformed its workflow, achieving unprecedented efficiency and cost savings.
Central to the E-Tron GT’s production model is an intense degree of customization, with each vehicle tailored to specific customer orders. This calls for an efficient and adaptable production process, which the adoption of 3D printing has significantly enhanced. Trinckle’s Fixturemate software has streamlined the design of custom fixtures, reducing the time needed from hours to between 10 and 20 minutes per design. This user-friendly tool enables the creation of precise and functional components without the extensive expertise typically required for traditional CAD software.
Speaking on the benefits of the Fixturemate software, Cem Guelaylar, a 3D Printing Expert at Audi Sport, explained, “We put our parts in Fixturemate and bring the fixture out of this software in minutes. Normally, in classic construction, we need [two to four] hours, depending on the size of the part. Fixturemate is very easy to use. We can bring trainees and show them how to use the fixturemate software, and they can directly work with it and bring the fixtures in a short time.”
The efficiency gained from this software is particularly crucial for Audi Sport, where assembly precision directly affects the quality and consistency of each vehicle. For instance, custom jigs ensure that components like the head-up display are perfectly aligned, ensuring safety and functionality while enhancing user experience.
Also contributing to Audi’s improved workflow is the integration of UltiMaker S series 3D printers, which has enabled the in-house production of essential tools and fixtures, dramatically reducing lead times. Audi reports that what once took weeks or months to outsource can now be achieved within a single day, translating to cost savings exceeding roughly 80%. “3D printing helped us to get these tools in a very short time. The workers come to us and say, I need a fixture to assemble the cars. It takes one day to get this tool in his hand.”
Furthermore, 3D printing’s flexibility has allowed the company to experiment with a range of materials tailored to specific applications, from TPU95a to ESD-safe PLA. This has resulted in easier production of electronic components, ensuring safety and compliance with industry standards.
What do you think of this increased adoption of 3D printing by Audi? Let us know in a comment below or on our LinkedIn, Facebook, and Twitter pages! Don’t forget to sign up for our free weekly newsletter here for the latest 3D printing news straight to your inbox! You can also find all our videos on our YouTube channel.
*All Photo Credits: UltiMaker