ASICS Works With Dassault Systems on 3D Printed Shoes
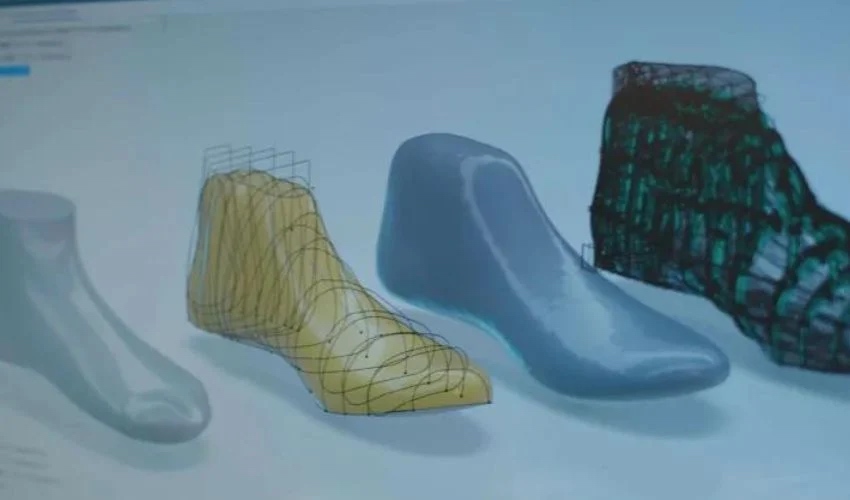
Amidst the excitement of the Olympic Games, ASICS has announced a new partnership with French software manufacturer Dassault Systèmes. As athletes from around the world strive for gold, ASICS and Dassault Systèmes are setting new standards in footwear technology and customization through 3D printing. The collaboration promises not only customized sockliners, but also more sustainable production.
The joint work takes place in the ASICS Personalization Studio in Paris. Here, ASICS leverages its expertise and Dassault Systèmes’ modeling and simulation technology, including the 3DEXPERIENCE platform and Virtual Twin technology. Pascal Daloz, CEO of Dassault Systèmes, emphasizes: “We share ASICS’ commitment to innovations that improve health and well-being. Our partnership reflects this by demonstrating a holistic approach to manufacturing that prioritizes the consumer experience. It also shows how the virtual world is catalyzing the 21st century economy. Through their foundation in science, our virtual twins enable industry to not only improve the performance and the experience of products but to advance more sustainable business models.”
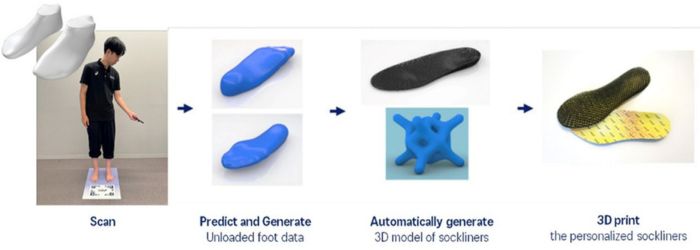
The 3D foot scan process (photo credits: ASICS and Dassault Systèmes)
To create the individual sockliner, a foot scan is first carried out. Based on the foot shape data, the sockliner is 3D printed layer by layer in a grid structure of flexible material. The resulting sockliner is breathable and soft, and the degree of softness can be individually adapted to the customer’s needs. “The exact level of softness can be varied for any part of the foot, which aids physical recovery by reducing strain, while also improving performance,” the two companies explain.
The tailor-made sockliners not only offer individual customization, but are also environmentally friendly. Thanks to 3D printing, the ecological footprint of the shoe can be reduced. “The typical production of a sports shoe emits 3kg of CO2.3D printing reduces CO2 emissions to 900 grams,” emphasizes Pascal Daloz. In addition, material losses that occur during traditional production by cutting are avoided and the sockliners can be produced locally, which reduces transportation and emissions.
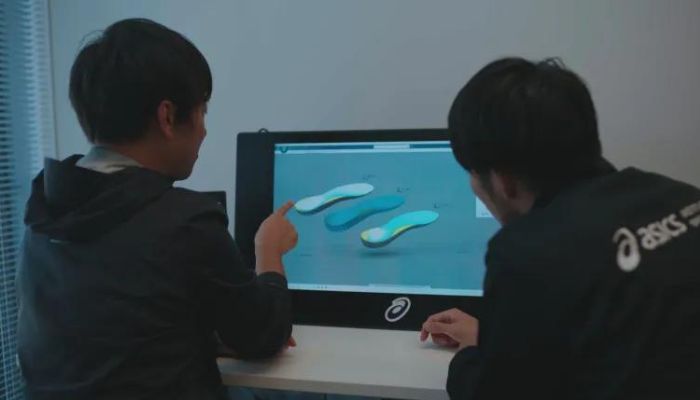
Photo Credits: ASICS
From 2025, production will be relocated to Japan with the aim of also manufacturing insoles for other shoe models. Before then, however, ASICS plans to carry out operational tests as part of a trial run. Find out more about the customized insoles HERE.
What do you think of this partnership between ASICS and Dassault Systèmes for 3D printed shoe components? Let us know in a comment below or on our LinkedIn, Facebook, and Twitter pages! Don’t forget to sign up for our free weekly newsletter here for the latest 3D printing news straight to your inbox! You can also find all our videos on our YouTube channel.
*Cover Photo Credits: ASICS and Dassault Systèmes