Meeting with Arevo and hearing about their 3D printed bike
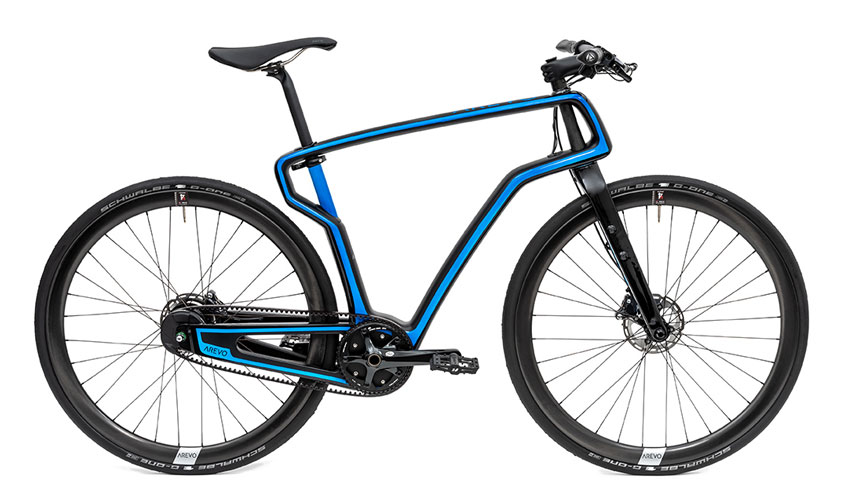
AREVO is a young Californian startup that has developed an additive manufacturing platform consisting of a 6-axis robot capable of extruding different types of plastics and polymers, including carbon fibre. It wants to revolutionise the manufacturing sector by relying on 3D printing; it can then obtain more complex geometric shapes and considerably reduced production times. Their first application is a 3D printed bike frame but the co-founder and president, Hemant Bheda, says they can reach more sectors. We meet up with him to learn more about Arevo’s technology and future projects.
3DN: Can you introduce yourself and tell us more about Arevo?
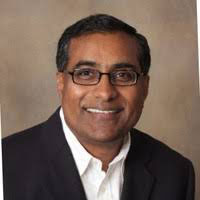
Hemant Bheda
I started my career as a design engineer at Intel and AT & T Bell Lab. It was an excellent training ground to combine innovation and expertise. Then, I moved to California in Silicon Valley where I created several startups in different technological fields – Mediametics, Parama and Metta. The point common to all these companies was to take on the challenge of doing what, at the time, was considered impossible.
In each of these companies, we thought of solutions only from a software point of view and hired the best manufacturers. After Metta, I found myself in the world of polymer manufacturing. This is a real production experience that allowed me to understand this manufacturing business, which is far removed from the bubble of Silicon Valley. It was then that the idea of developing a technology for making light structures for production applications sprang up. In addition, the idea of inventing a technology that would bring production back to the United States pleased me a lot. This is where we created Arevo.
3DN: Can you tell us more about your 6-axis 3D printing platform?
Traditional 3D printers use a 3-axis rotary gantry. The material is deposited layer by layer on an XY horizontal plane (similar to paper printing). It’s more of 2.5D printing, not 3D. At the beginning of AREVO’s life, we asked ourselves a question: why not print a 3D surface rather than a plane? The main advantage we saw was to improve the resistance in the direction of the Z axis. It was a challenge because we had to reinvent the software and find multi-axis machines for 3D surface printing. We turned to a robotic, multi-axis, ready-to-use arm to achieve what we now call free-motion repository.
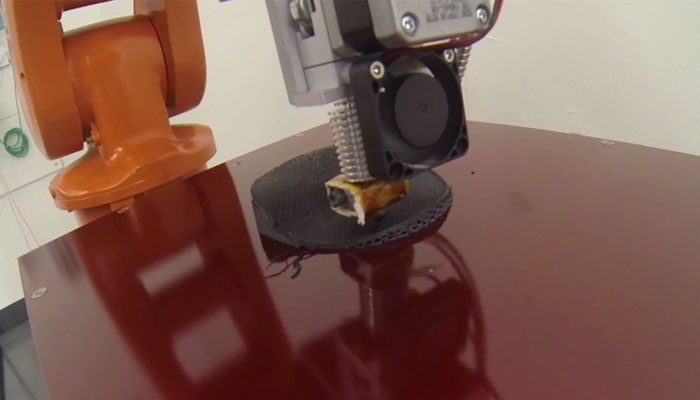
The 3D printing platform developed by Arevo
3DN: What did additive manufacturing allow you to do compared to traditional methods?
For us, the additive manufacturing of composite materials associated with our software has resulted in lighter and stronger parts, with complex geometries that are not possible to obtain with traditional manufacturing methods. With the automation and elimination of tools, we have reduced production costs by 4 times.
3DN: You recently unveiled a 3D printed bike frame: Why use 3D printed carbon fiber?
3D carbon fibre printing allows the creation of lightweight and ultra-rugged structures with geometry that was impossible to obtain until now. The frame of the bicycle is an excellent example of what can be achieved with the AREVO Additive Composite technology. The entire bike – from the idea to the final production – was realised in only 18 days against 18 months with traditional methods. In addition, we are now able to offer a fully customisable bike in its size, colour and style.
3DN: What are your future projects?
We are preparing different applications in the construction, transportation, aerospace and defense sectors. For now, we can not say more but stay tuned to our news!
3DN: How do you see the future of additive manufacturing in the industry?
We believe that additive manufacturing will be used as one of the viable options in production, especially for demanding applications that require energy efficiency, complex geometries, mass customization and high weight resistance. We see great potential for additive manufacturing in areas such as aerospace, transportation, construction, etc.
3DN: A last word for our readers?
What’s more exciting about this technology is that it allows parts to be made when needed and anywhere. It has the potential to balance manufacturing around the world. Find more information on our official website !
What do you think of AREVO, their platform and 3D printed bike? Let us know in a comment below or on our Facebook and Twitter pages! And remember to sign up for our free weekly Newsletter, to get all the latest news in 3D printing send straight to your inbox!