ARCHIBIOFOAM: The 3.5 Million Euro Project for 4D Printing Buildings That Adapt to the Environment
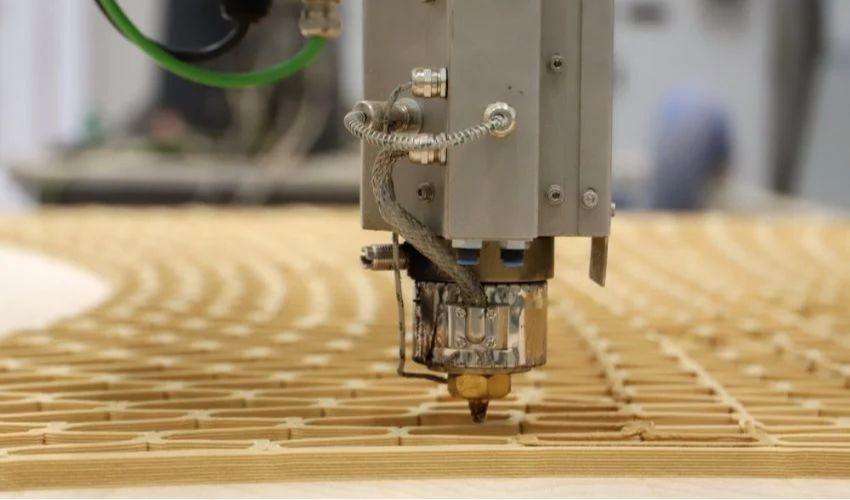
The construction industry is one of the most innovative sectors, where new technologies and materials are continually being tested and fine-tuned to move toward more sustainable construction and solve long-standing problems. Additive manufacturing is one of the technologies being studied in the field because it allows for building design to be reimagined with materials that are not accessible with traditional technologies. We have seen a number of ongoing projects in Italy in this field such as the European ConstructAdd project, which has the involvement of the Milan Polytechnic, and the innovations brought about through WASP and D-shape technology around the world.
In this vein, the European project ARCHIBIOFOAM, which also has the participation of the University of Milan, has been awarded a 3.5 million euro grant from the European Innovation Council (EIC) to develop an expanded, 3D-printed biomaterial capable of changing shape and reacting according to its surroundings. Let’s see what it’s all about.
The ARCHIBIOFOAM Project: The Challenge of More Sustainable Construction
The ARCHIBIOFOAM project was born out of a specific need: to reduce the environmental impact of the construction sector, now responsible for 40 percent of annual global emissions. How? Through 4D printing and the use of a special biofoam (or bio-foam), which is organic and biodegradable. The project partners are the Center for Complexity and Biosystems at the University of Milan, Finland’s Aalto University, its spin-off company Woamy, and the University of Stuttgart. Each brings its expertise and specialization to integrate bio-based materials science, computational design of metamaterials and robotic additive manufacturing.
For the long-term, designers envision the construction of passively ventilated buildings using bio-derived foams from extruded wood cellulose. Over the next three years, the goal of the project is to print the biomaterial to make exterior building facades with porthole-like openings capable of opening and closing in response to the environment.
According to the partners involved, these load-bearing expanded biomaterials could replace typical polluting and nonrenewable building materials such as concrete, steel and glass. In fact, ARCHIBIOFOAM biofoam would have comparable strength to these materials, even though it is composed of 90 percent air, is biodegradable and adheres to circular economy principles.
4D Printing of Adaptive Architecture
The University of Milan, represented by Stefano Zapperi, a professor of matter physics and an expert in the automatic generation of 3D digital models, will be responsible for the development of proprietary software. This software will enable the specification of design parameters to be algorithmically optimized, including sensitivity to heat and moisture in the material.
“We are currently witnessing a revolution in structural design thanks to algorithms that can find the most effective geometry for a desired function, such as programming shape changes under external stimuli,” commented Professor Zapperi. “During the ARCHIBIOFOAM project, we intend to expand the capabilities of our software and adapt it to the physical characteristics of biofoam and the needs of the building industry. I envision a pipeline in which the architect specifies only his requirements in terms of shape, mechanical properties and response functions, and the computer provides a 3D digital model ready to be fabricated on a large scale.”
The University of Stuttgart, led by Dr. Tiffany Cheng, will be in charge of the large-scale 4D printer used to make buildings. 4D printing offers the ability to program printed objects to transform autonomously in response to environmental stimuli. Digital design and robotic production of biofoam would thus offer the possibility of creating adaptive architecture, dramatically reducing the carbon footprint throughout the building’s life cycle.
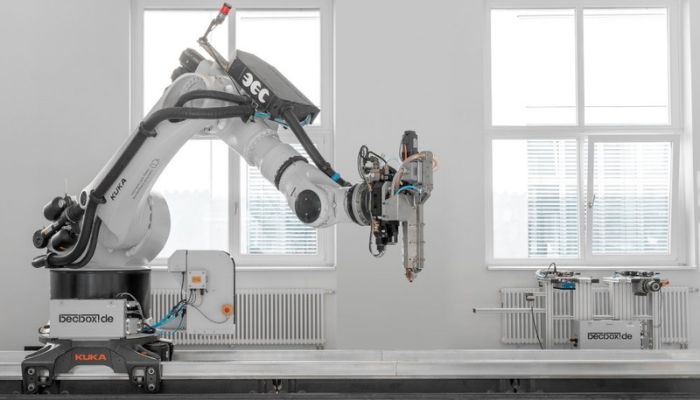
The LFAM platform, developed by the University of Stuttgart, consists of a 6-axle KUKA Fortec KR420 R3080 on a 12-meter linear track.
“Robotic additive manufacturing is particularly suitable for structuring materials at high resolution, thus unlocking the performance potential of bio-foam on a large scale,” Cheng said. “By adapting the single-material system through our manufacturing process, we aim to meet the multiple functional requirements of building components, such as loading capacity and shape change for adaptive ventilation.”
As for the other partners, Woamy will work on expanded biomaterial technology with the goal of bringing biofoam to market, while Aalto University will coordinate the entire project. Read more here.
What do you think of the ARCHIBIOFOAM project? Let us know in a comment below or on our Facebook and Twitter pages! Don’t forget to sign up for our free weekly Newsletter, with all the latest news in 3D printing delivered straight to your inbox!
*All Photo Credits: ICD/IntCDC, University of Stuttgart