Bespoke Car Manufacturer Arash Uses MakerBot & Carbon Fiber For Electric Hypercar
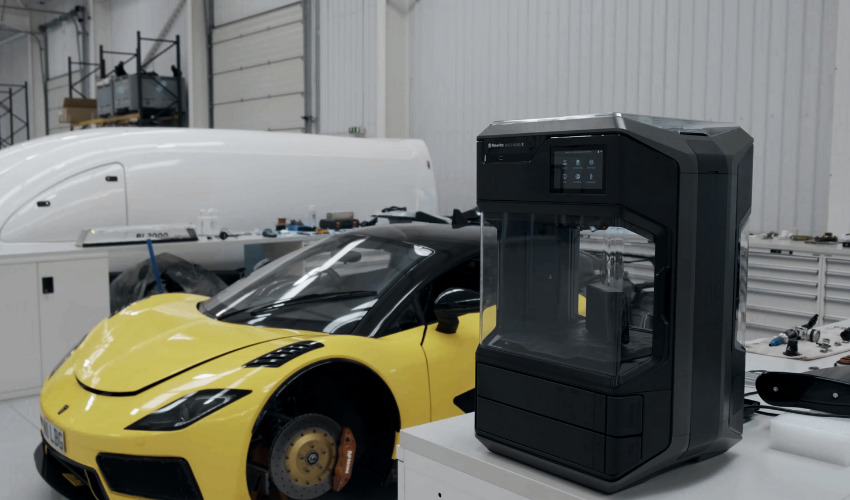
UK-based hypercar manufacturer Arash Motor Company is leveraging the efficiencies of 3D printing in its car factories in order to accelerate car production. While Arash has been using MakerBot 3D printers for numerous years, the company has just recently introduced nylon carbon fiber for its newest fleet of vehicles. Using various materials on the MakerBot METHOD X, including MakerBot Nylon Carbon Fiber and ABS, the Arash team 3D-printed production parts to be used directly on the vehicle.
The Arash production facility features the MakerBot Replicator 2, Replicator Z18, and METHOD X. Additive Manufacturing allows the Arash team to test performance improvement in the use of composite structures, engines, electric motors, and aerodynamics. 3D Printing even helped achieve a sleek aerodynamic aesthetic for the company’s latest electric hypercar project. Prior to working with MakerBot, the team would go through the time-consuming and cumbersome process of prototyping with aluminium – from fabricating, bending, welding, shaping, etc. “The MakerBot 3D printer series reduces the time from a file on the computer screen to prototyping and checking for touch and feel. That’s a big thing. Sometimes you miss a hole or a fixture, but you can catch that on a CAD model. Then after it’s printed, you can physically check it,” said Arash Farboud, founder and lead designer.
The Next Electric Hypercar from Arash
Recently 3D printing has been used in the design of several high-performance vehicles, including examples from Bugatti and McLaren, among others. AM brings unique advantages in the creation of these super fast vehicles, notably helping to reduce weight and increase aerodynamic properties thanks to 3D printing’s ability to optimize strength and weight. For this new hypercar, the Replicator Z18 from Makerbot helped Arash to design the complex chassis structure and the aerodynamic structure. Thanks to the flexibility afforded by 3D printing, they were able to integrate new techniques like suspension and wing design, wishbone suspension checks, hub and center lock fitments and scale models to show structural parts.
Of course, design is not the only area where AM affords advantages to automobile makers. The increased choice of material and how to use it also plays a significant role. In this case, Arash used nylon, also known as Polyamide (PA), which is a widely used polymer in AM, with various applications. The primary characteristics of Nylon filaments include their great flexibility and resistance to impact or abrasion. Additionally, nylon that is reinforced with carbon (PA12) becomes incredibly durable, allowing it to replace aluminum and other metals due to its high strength-to-weight ratio, stiffness, and heat resistance. As you can imagine, this makes it especially popular in the automotive industry. “Most people think that 3D printing filaments being used are not strong enough, or that 3D printing is only used for models or prototypes. But we’re actually using these parts on cars. They are accurate for our applications”, Farboud shared in a statement to the press. You can learn more about Arash on its website HERE.
What do you think of Arash’s use of the MakerBot Method X? Let us know in a comment below or on our Facebook and Twitter pages. Don’t forget to sign up for our free weekly newsletter, with all the latest news in 3D printing delivered straight to your inbox!
Cover Photo Credit: MakerBot