Application of the Month: NASA Uses 3D Printing to Manufacture More Accessible Antennas
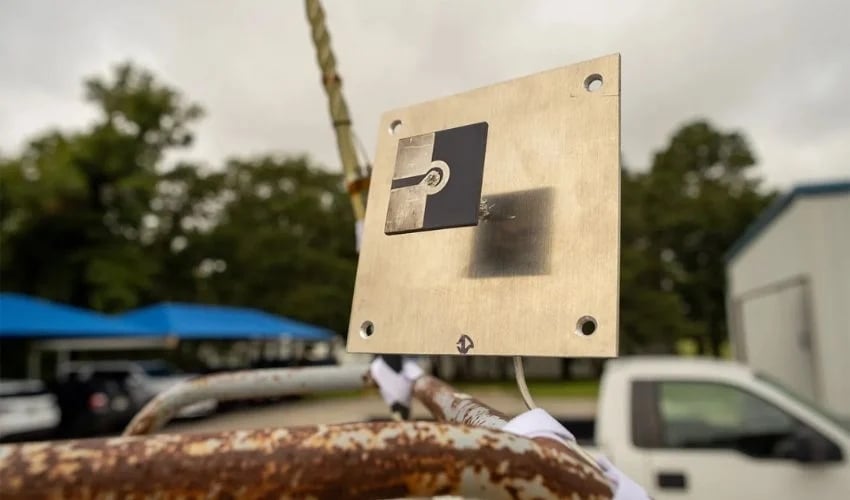
Aerospace is one of the sectors where additive manufacturing has truly left its mark. This includes in telecommunications. Here, 3D printing makes it possible to develop antennas with improved designs and advanced materials. These antennas are essential for data transmission in space missions as they facilitate communication between satellites, probes and the Earth.
Recently, engineers from NASA’s Near Space Network and the Electronics 3D Printing group at Goddard Space Flight Center developed and tested a 3D printed antenna using Fortify’s technology. The project sought to demonstrate low-cost design and manufacturing capabilities for efficient antennas that meet industry requirements. The antenna was evaluated with relay satellites and launched on a weather balloon from NASA’s Columbia Scientific Facility in Palestine, Texas. This development took only three months and represents a milestone in the manufacture of low-cost communication equipment for future space missions.
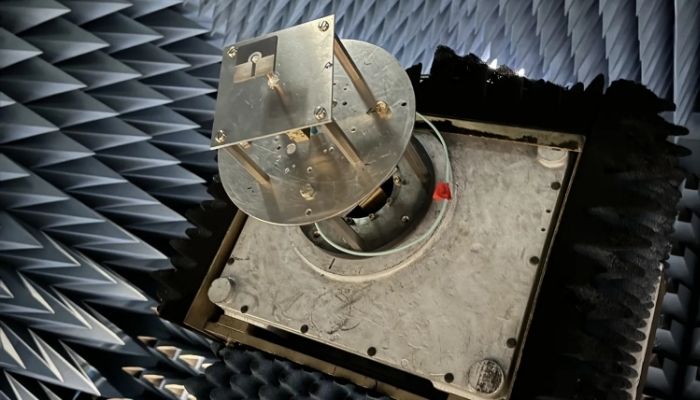
The antenna in the electromagnetic anechoic chamber at the Goddard Center (photo credits: NASA/Peter Moschetti).
The development of 3D printed antennas has many challenges. Manufacturing antennas using 3D printing is particularly complex due to the need to integrate materials with specific electromagnetic properties and ensure adequate conductivity for signal transmission. Engineers designed an optimized structure for data transmission and used innovative materials. NASA stated that “low electrical resistance, tunable, ceramic-filled polymer material,” which allowed it to improve signal tuning. After design and printing, the antenna was tested with NASA’s relay satellites before being tested at high altitudes aboard a weather balloon.
Testing the Efficiency of the 3D Printed Antenna
The antenna was 3D printed using technology from Fortify, a startup specializing in equipment for the manufacture of radio frequency devices. Although it has not specified the exact model of the printer used, it is known that Fortify delivered a Flux One printer to NASA’s Glenn Research Center in August last year. The agency stated that Fortify’s platform allowed its engineers to have full control over the electromagnetic and mechanical properties of the antenna, achieving fabrication in a few hours. The resulting antenna was of the magneto-electric dipole type, and what characterizes it is its doughnut-shaped radiation pattern. A shape widely used in telecommunications.
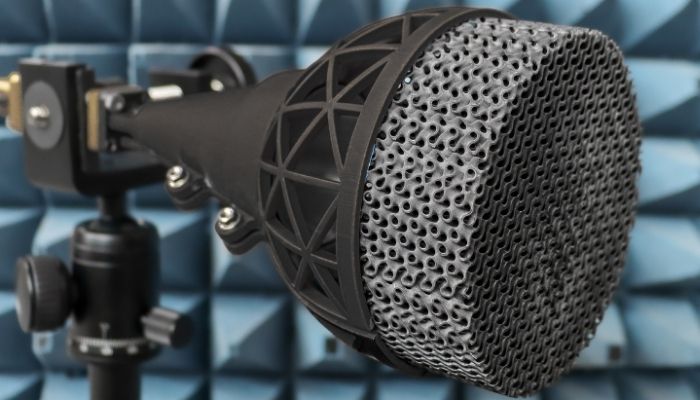
Fortify also develops dielectric materials to manufacture components and devices used in broadband, high-frequency communication and detection systems (photo credits: Fortify)
As part of the initial testing, the antenna was moved to the electromagnetic anechoic chamber at the Goddard Center in Greenbelt, Maryland. This chamber is designed to eliminate electromagnetic interference, which allowed the antenna’s performance to be accurately evaluated. Subsequently, field tests were conducted at the Columbia Scientific Balloon Facility in Texas. In these tests, the 3D printed antenna was compared to a standard satellite antenna, evaluating its performance at different angles and elevations.
The antenna was also subjected to extreme conditions. It was installed on a weather balloon that was raised to 100,000 feet, just over 30 kilometers, in order to verify its ability to send and receive data. Surprisingly, the antenna successfully passed these tests, confirming its viability for future space applications.
This NASA application example opens up new possibilities for antenna manufacturing. Thanks to rapid prototyping and the design and material flexibility offered by additive manufacturing, NASA will be able to develop more efficient communication systems tailored to different missions.
What do you think of NASA’s 3D printed antenna? Let us know in a comment below or on our LinkedIn, Facebook, and Twitter pages! Don’t forget to sign up for our free weekly Newsletter here, the latest 3D printing news straight to your inbox! You can also find all our videos on our YouTube channel.
*Cover Photo Credits: NASA/Peter Moschetti