Application of the Month: LEAP 71 Successfully Tests Liquid-Propellant Engine Made With 3D Printing and AI
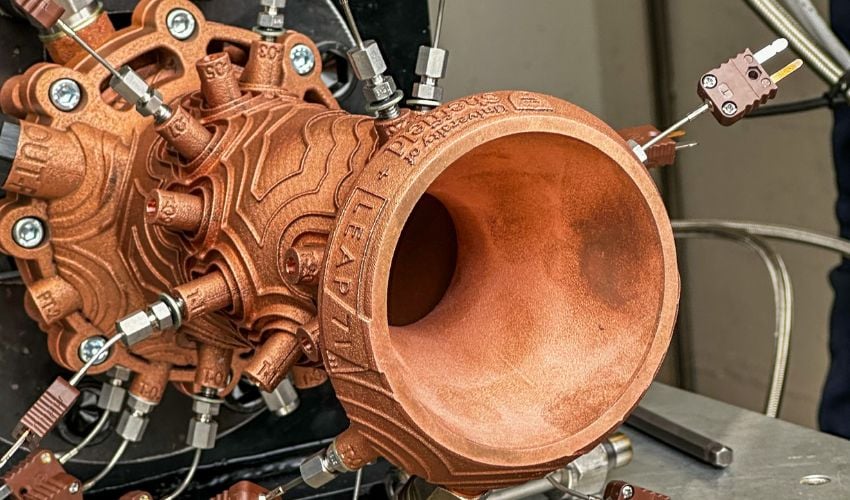
The fact that 3D printing can contribute to groundbreaking innovations and progress in the aerospace industry is underpinned by numerous examples from recent years. NASA and ESA are constantly experimenting with exploiting the potential of 3D printing in space and numerous 3D printing companies have specialized in high-performance applications. Now a new player, artificial intelligence, is entering the stage and is already being touted as the revolutionary of the future. The example of LEAP 71 shows how the combination of AI and 3D printing can lead to advanced approaches and results. The company has succeeded in developing and testing a 3D-printed liquid propellant rocket engine with its AI-based software tool Noyron.
We have previously told you about LEAP 71. The Dubai-based company aims to drive technological progress with the help of computational engineering. To manufacture its products, LEAP 71 relies on highly developed software and additive manufacturing, which was also used in the production of the rocket engine.
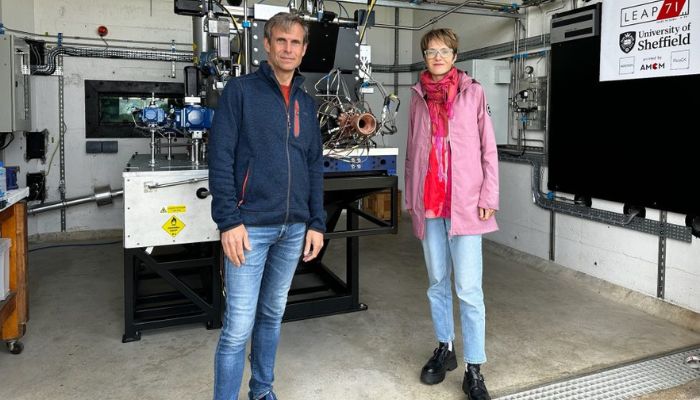
LEAP71 was founded by aerospace engineer Josefine Lissner and entrepreneur Lin Kayser
The aim of the project was to demonstrate the capabilities of the company’s proprietary Noyron software and to test the resulting large computational engineering model of the drive. Noyron uses AI algorithms to automatically implement logical and physical processes in the manufacturing process. Using this software, it was possible to develop the model for the TKL-5 rocket engine – completely digitally and computer-controlled without human intervention.
This also had a remarkable impact on production time. By eliminating the need for CAD design, the engine took just two weeks to manufacture. It was then successfully tested on June 14, 2024 in Wescott, UK, and worked on the first test.
Although LEAP 71 and its Noyron software played a major role in the success of the rocket engine, the company also enlisted the help of other experts. The engine itself was printed on an EOS M290 by AMCM, a German pioneer in 3D metal printing. Copper was used as the material, as this enables very powerful engines with active cooling.
The British “Race to Space” team from the University of Sheffield was also involved, providing feedback and post-processing before the engine was tested for the first time at Airborne Engineering’s test site. All temperature values and critical parameters were within limits at the test launch and those involved were able to confirm that the engine was intact and functioning as planned.

The engine was made from copper using a 3D printing process
Due to its compact size, the engine would be suitable as the final stage of an orbital rocket. It has a thrust of 5 kN or a lift mass of 500 kg, i.e. 20,000 hp. Like many other advanced systems, the engine uses kyrogenic liquid oxygen and kerosene for propulsion. This combination of fuels was a deliberate decision by LEAP 71, despite the difficulty of handling, as the kerosene not only provides propulsion but also cools the engine when it is forced through thin ducts, thus preventing the engine from melting. Although the combustion temperature of the fuels is 3000°C, the surface can be kept stable at below 250°C.
In addition to the sophisticated cooling system, the engineers have also ensured that the rocket drive can be monitored and the data actively used. Thanks to numerous connections for measuring temperature and pressure, it is possible to feed the data directly back into the Noyron calculation model. This data can then be used to revise the model and further develop the software. Noyron could create new design variants of the engine model in less than 15 minutes, which could also be tested directly after production. Josefine Lissner, aerospace engineer and Managing Director of LEAP 71, emphasizes the importance of Noyron for accelerating developments:
This is an important milestone for us and the entire industry. We can automatically create functional rocket thrusters and directly move to practical validation. From final specification to manufacturing, the design of this engine took less than 2 weeks. In traditional engineering, this task would take many months or even years. Each new engine iteration takes only minutes. Innovation in space propulsion is hard and costly. With our approach, we hope to make space more accessible for everyone
You can find out more about LEAP 71 HERE. Let us know in a comment below or on our LinkedIn, Facebook, and Twitter pages! Don’t forget to sign up for our free weekly newsletter here for the latest 3D printing news straight to your inbox! You can also find all our videos on our YouTube channel.
*All Photo Credits: LEAP 71