Application of the Month: 3D Printed Scaffolds Help Rebuild Australian Man’s Jawbone
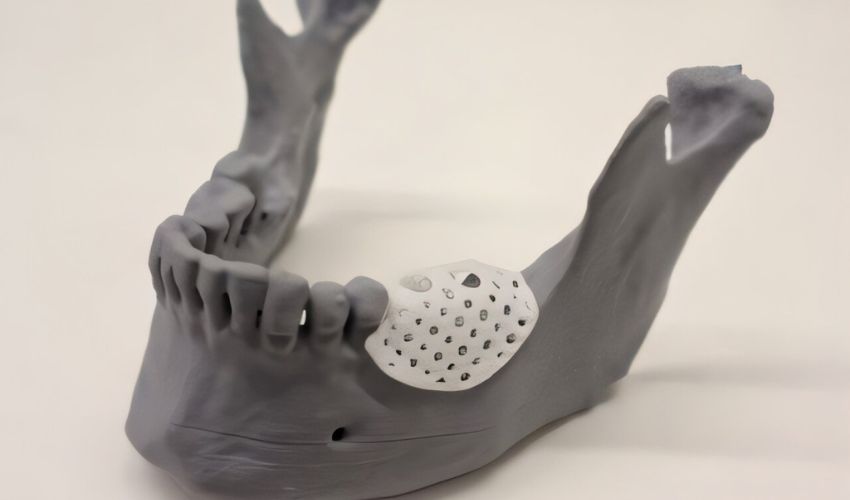
Researchers at the University of Queensland have accomplished an incredible feat. Clinicians at the school of dentistry have successfully used custom-made 3D printed bone scaffolds in staged alveolar bone augmentation to help rebuild part of a man’s jawbone. The hope is that the process will be able to be optimized and used for even more patients suffering from bone defects in the jaw.
Staged alveolar bone augmentation, a surgical procedure to improve the shape and size of the alveolar ridge for dental implants or prostheses, is a demanding procedure that, while often successful, can be difficult. Indeed, there is not currently an accepted ‘ideal approach’ for it according to the researchers, although guided bone generation (GBR) is the most common.
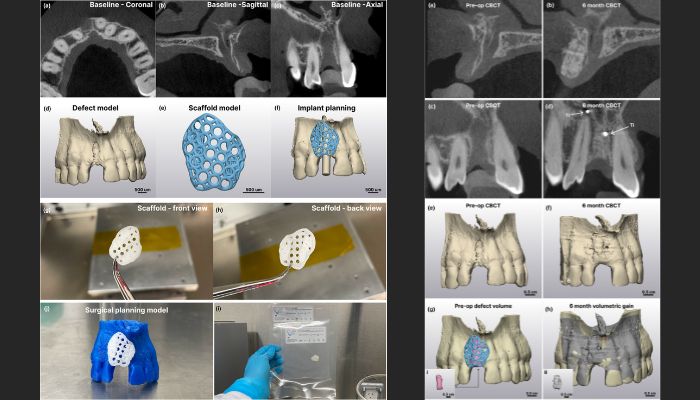
Results showing the jawbone as well as the lattice and the final results
Common issues using GBR include the need for chair side membrane shaping, as well as second-stage removal for non-resorbable membranes. And while 3D printing has been successfully used for patient-specific meshes to regenerate alveolar ride defects, these have been made of titanium and thus need to be surgically removed. The researchers sought to overcome this.
The rather exceptional case was described by Professor Saso Ivanovski from UQ’s School of Dentistry, who led the clinical trial, as a clear example of the safe and effective use of bioprinting for this purpose and using biocompatible material. He further expands, “In this case, the scaffold supported and encouraged new bone to grow in the jaw of a 46-year-old man, allowing a dental implant with a new tooth to be securely inserted. The bone scaffolds are custom designed for the patient, effectively regenerate jaw bone [sic] and are completely resorbable, so there is no need for additional surgery to remove them.”
Rebuilding a Jawbone With 3D Printed Scaffolds
But for those who are not dentists, what exactly is a ridge defect? In essence, the alveolar process refers to the ridge of bone that houses the sockets for the teeth on the jawbones, holding them in place. Therefore, if there is a defect, there can be difficulties in holding both healthy teeth and implants in this case. Bone augmentation, where scaffolds are put in place to encourage bone growth in the correct areas, is the preferred treatment for large volume defects.
Here, the 46-year-old man involved was informed that due to large horizontal defects, it would be difficult to put in an implant after the removal of his tooth. The patient then consented to the use of patient-specific, 3D printed PCL scaffolds to help encourage bone growth in the area. Although this was the first successful case, it is actually part of a trial that has been ongoing since January 2022.
As can be expected, the process to create the 3D printed scaffold was a long one. In order to make it patient-specific, the first step was to take an intraoral scan and CBCT scans before using dental implant planning software to create a digital plan for the implant. This was exported as an STL file and refined using Materialise 3-Matirc Research 15 software.
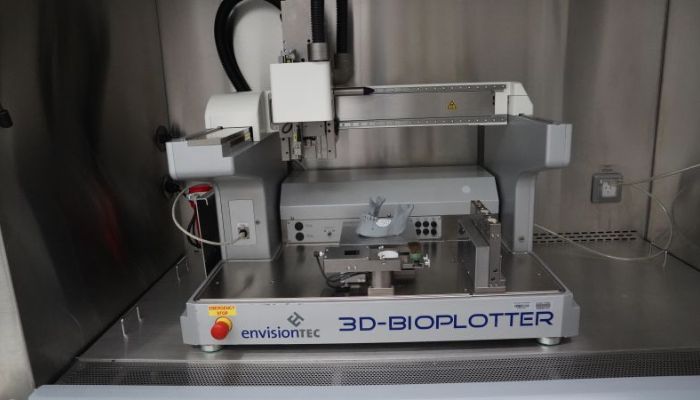
The University of Queensland’s 3D-Bioplotter
The 3D printing itself was done in a purpose-built biosafe cabinet and made using the Desktop Health 3D-Bioplotter® Developer Series printer and medical-grade PC08PCL. Originally made by EnvisionTEC, acquired by DM and turned into Desktop Health and ETEC in 2022, this bioprinter uses extrusion and a 200 μm Tecdia Arqué needle for PCL at a temperature of 110°C, with a movement speed of 1 mm/s and a pressure of 400 kPa. The PCL scaffold was put in place and covered with a resorbable porcine collagen membrane.
It then took about six months before the patient was found to have sufficient bone growth for an implant. In fact, the approach resulted in a volumetric bone gain of about 364.69 ± 2.53 mm3, or a volumetric gain of 108.4% as compared to the original defect. Recovery for the patient was smooth, with no excess pain nor swelling. Since then, the team has gone on to use this method for a further nine patients.
The lead biomedical engineer for the project, Dr. Reuben Staples, concludes, “Our team is the first in Australia to locally manufacture university-developed 3D printed bone scaffold implants for dental reconstruction in human trials using our certified Quality Management System. It is compliant with the Australian regulatory requirements. Because the medical grade synthetic polymer used is more cost effective than currently available non-resorbable metallic commercial alternatives, this is a significant step forward in how 3D printing can be used to create affordable, safe and effective bone implant solutions to reconstruct jawbones and teeth for people in need. There is still more to be done in this field, but it’s exciting to see this success.”
What do you think of using 3D printed scaffolds to rebuild a man’s jawbone? Let us know in a comment below or on our LinkedIn, Facebook, and Twitter pages! Don’t forget to sign up for our free weekly Newsletter here, the latest 3D printing news straight to your inbox! You can also find all our videos on our YouTube channel.