Antibacterial, 3D Printed Metal Under Development for Surgical Implants
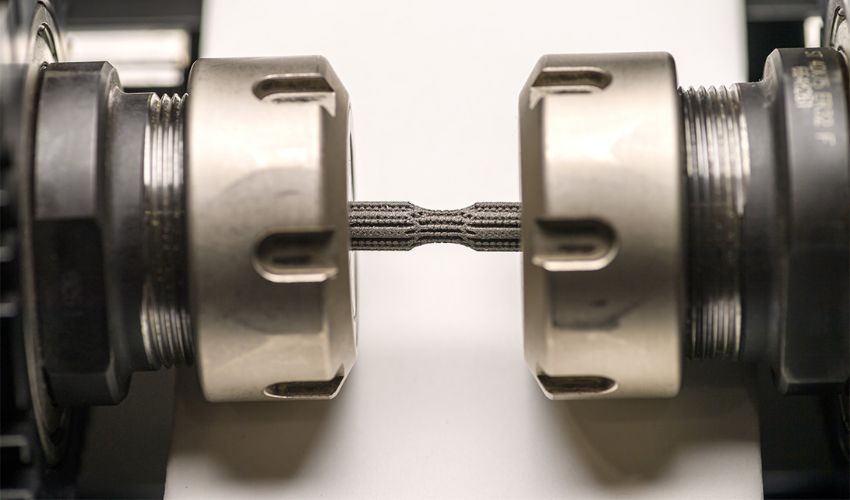
Within the realm of medical 3D printing, we often discuss the value of plastic filaments, photopolymer resins, and silicone technologies that can assist with the comfort and rehabilitation of patients receiving treatment. However, one material that must not be overlooked within this field is the use of metal 3D printing. The use of metal in the medical field is a crucial part of many implants, surgeries, and some prosthetic pieces which can often accompany patients for years or indeed, for a lifetime. One issue with medical parts, in general, is the acceptance or rejection of foreign material when interacting with the human body, leading to adverse side effects or infection. To combat these issues more easily, researchers at Washington State University (WSU) have announced their successful test of a 3D printed metal designed to be naturally antibacterial, opening the possibility for the material to one day be used for surgical implants.
During testing, the 3D printed metal was able to kill 87% of infection-causing bacteria and was able to do so without compromising its function as an implanted piece of medical equipment; the tissue around it did not reject the new implant. The WSU research team is hopeful that this development will be a means to control the spread of bacteria during common implant surgeries such as for the hip or knee. The growth of bacteria and subsequent infection during and after these surgeries is the leading cause of implant rejection. With materials that are naturally resistant and able to kill harmful bacterial cells, the outcomes for many may improve dramatically.
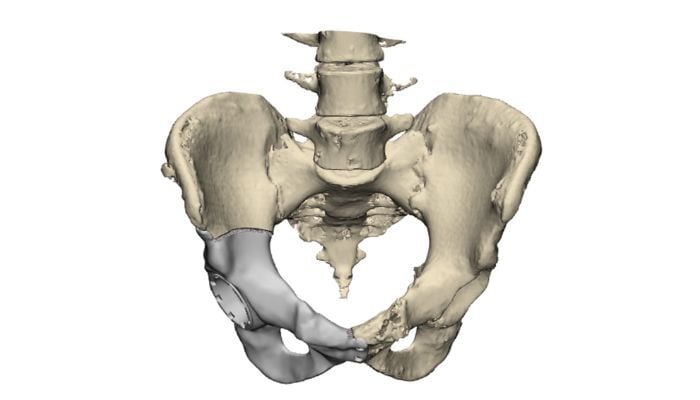
Titanium has been used in traditionally manufactured and 3D printed medical fields. (Photo credits: TrabTech)
The standard metal most often used for common surgeries is titanium, which has no major antibacterial properties and has been regularly utilized in the medical industry for nearly half a century without major technological changes. This has often led to post-surgery infections due to bacterial buildup on the implant. The danger is not only limited to one’s time on the operating table but can also develop in the following weeks or months. Indeed, in the worst of cases, patients may be forced to return to surgery to get the implant removed and replaced. The metal produced by the WSU team, however, would remove the need for such drastic measures while also eliminating the need for the patient to ingest supplemental antibiotic drugs.
Over the course of three years, researchers studied the medical and functional properties of the 3D printed metal. The material developed by the WSU team is a metallic conglomerate of titanium, tantalum, and copper. The last of which causes bacteria to die when encountering the metal’s surface. Meanwhile, the use of tantalum, which is resistant to corrosion, is also capable of boosting the connection and growth of cells and tissue in the implanted area.
“We need to find something where the device material itself offers some inherent resistance – more than just providing drug-based infection control. Here’s what we’re saying, why not change the material itself and have inherent antibacterial response from the material itself?” Explains Professor Amit Bandyopadhyay, one of the researchers and authors of the research paper. Fellow co-author Professor Susmita Bose continues, “The biggest advantage for this type of multifunctional device is that one can use it for infection control as well as for good bone tissue integration. Because infection is such a big issue in today’s surgical world, if any multifunctional device can do both things, there’s nothing like it.”
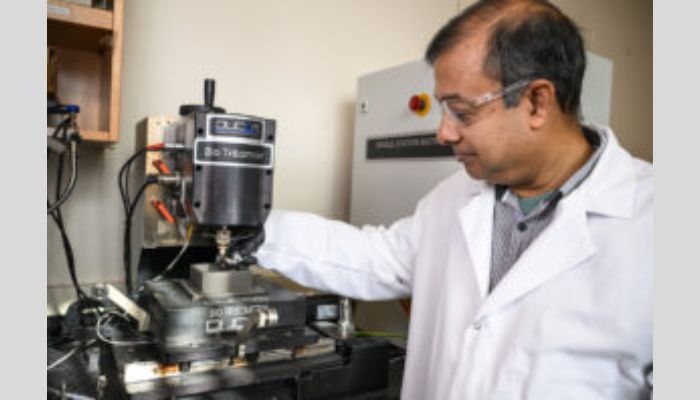
Professor Bandyopadhyay is part of the research team who is looking into refining the development and properties of the 3D printed metal. (Photo credits: WSU Photo Services)
The research into the 3D printed, bacteria-resistant metal is still ongoing, as the team hopes to increase the antibacterial properties of the metal from 87% to 99%. They also wish to test the viability and durability of real-world, long-term use of their 3D printed metal for those who may potentially be fitted with the material. You can learn more about the research being done by the team at WSU by clicking HERE.
What do you think about developing antibacterial metal used for surgical implants? Let us know in a comment below or on our Linkedin, Facebook, and Twitter pages! Don’t forget to sign up for our free weekly Newsletter here, the latest 3D printing news straight to your inbox! You can also find all our videos on our YouTube channel.
*Cover photo credits: WSU Photo Services