Ansys Additive Simulation and Aconity3D Cooperate to 3D Print Flawless Bicycle Frame
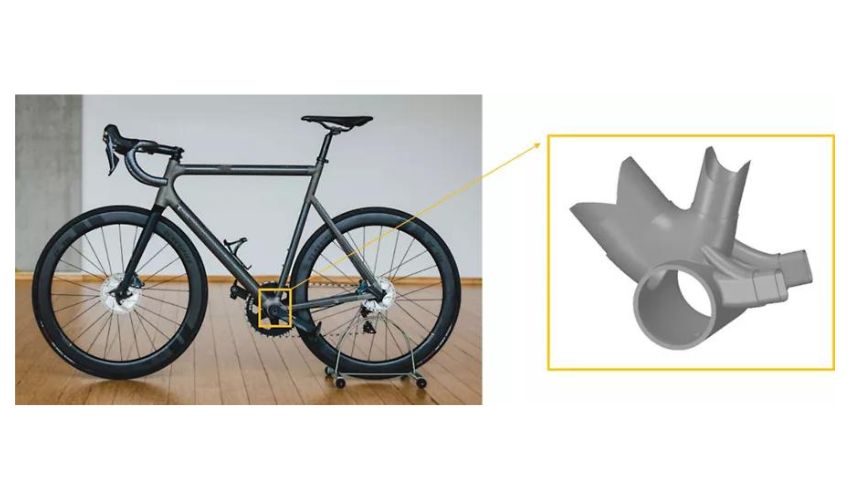
Brightlands Chemelot is one of four innovation campuses located in Limburg, the Netherlands. Here, designers, researchers, and engineers have collaborated to create a fully 3D printed bicycle, one of the first of its kind, using high-performance materials and additive manufacturing techniques to achieve a lightweight, durable and customizable frame. However, this discussion will focus on the production of the bottom lug, a critical component connecting various segments of the structure. To manufacture this part, Brightlands partnered with Aconity3D, a leading manufacturer and provider of laser-based metal 3D printing solutions.
In order to create a durable and lightweight bottom lug for the custom-made bicycle, designers opted for Ti-6Al-4V material. This titanium alloy is renowned for its strength and is typically used in aerospace and medical applications. The AconityMIDI+ laser powder bed fusion (LPBF) system at Aconity3D GmbH was used to 3D print the lug. However, during the printing process, an unexpected problem arose due to the use of support structures. The high stresses during the build process caused delaminations at the interfaces between the lower lug part and the supporting structures, which became too weak to maintain a solid bond with the built part geometry.
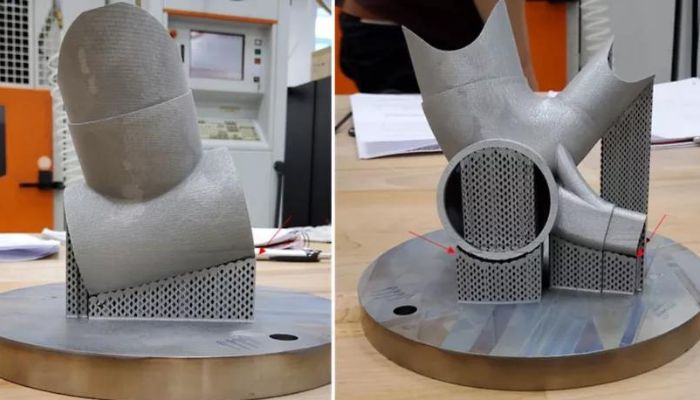
Delamination defects in the parts (Photo credits: Aconity GmbH)
Joining Forces With Ansys Additive Simulation and Aconity3D
Ansys and Aconity3D have partnered to address the challenge of delamination in support structures by integrating 3D printing process simulations into manufacturing. By utilizing the Ansys Additive LPBF simulations, the team could efficiently identify crucial areas and evaluate construction guidance and support strategies. The LPBF simulation provided a high-stress results tool highlighting critical stress regions, enabling engineers to recognize areas susceptible to crack formation during or after construction. Subsequently, based on the simulation outcomes, an optimized strategy was implemented for physical validation printing on the advanced Aconity MIDI+ system.
A static structural model, which includes inherent stress, was utilized to simulate the manufacturing configuration of the defective creation, including the exact manufacturing orientations and support structures. A high-stress function was added to the simulation results section to identify areas with critical stress buildup during printing. Upon reviewing the simulation results, it was found that the identified high-stress areas corresponded with the locations where delaminations occurred during the actual construction. These areas are likely to act as initiation sites for delamination, which would quickly spread across the adjacent interface between the underside of the tab and the supporting structures.

Aconity MIDI+ simulation can predict possible errors
What do you think about these two large companies joining forces to anticipate possible errors in 3D printing? Let us know in a comment below or onour Facebook, Twitter and LinkedIn pages! Sign up for our free weekly Newsletter here, the latest 3D printing news straight to your inbox!
*Cover Photo Credits: Aconity GMBH