Anisoprint and its 3D printing solution for continuous fiber composites
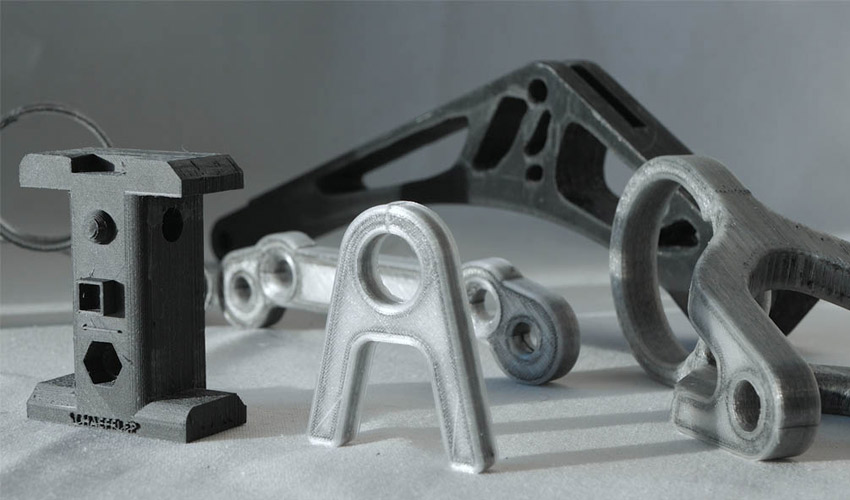
Anisoprint is a Russian 3D printer manufacturer that has developed a 3D printing solution for continuous fiber composites. Based on the principle of melt deposition, its Composer machine makes it possible to reinforce any 3D printing plastic with composite fibres during the process itself. A patented coextrusion principle that could interest more than one industry: composite materials are generally stronger, lighter and more resistant and therefore make them ideal solutions for aerospace, automotive and medical industries. We met with Anisoprint’s CEO, Fedor Antonov, to learn more about this technology, its benefits and limitations.
3DN: Can you present yourself and your link with 3D printing?
Anisoprint is a technology company that was founded by engineers and scientists with a joint vision on how composites can work if they are designed and applied in the right way and how dramatically they can change manufacturing. We’ve learnt to manage unique properties of composites to invent a technology that can replace metal, giving stronger and lighter parts that are also cheaper. The perfect approach to implement this vision appeared to be through 3D printing, a common name for a wide range of technologies that revolutionise the way we manufacture things in many industries through digitalisation and automation. Now our technology of 3D printing of composites with continuous fibers allows reducing manufacturing costs in the majority of areas from aerospace to healthcare.
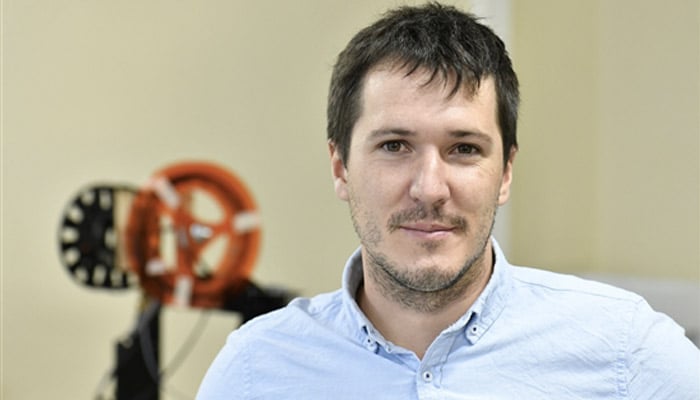
Fedor Antonov
3DN: Can you tell us more about the 3D printer you developed?
Our printers are based on our proprietary composite fiber coextrusion technology (CFC). Composite fiber coextrusion is a core innovation in our products, and it significantly differs from the other approaches to 3D-printing of composites with continuous fibers (prepreg, dry fiber coextrusion, lamination — they all have their limitations). In CFC technology, we reinforce plastic with continuous composite fibers directly during the printing process, not at pre-stage like in other technologies. This approach allows using any plastic you want (PETG, ABS, PC, PLA, Nylon, etc) and changing composite infill density.
By varying materials to reinforce, the direction of fibers and density of the structure, we can make more optimal parts with intricate shapes, complex lattice structures, or bionic designs. Eventually, it leads to reducing manufacturing costs because with this approach we use the exact amount of material that needed to get the required properties of a part.
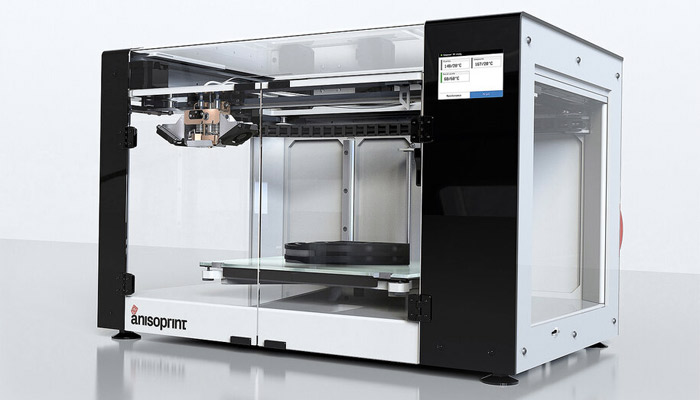
The Composer 3D printer | Credits: Anisoprint
The main reason why we still do not have composite structures everywhere, just like in nature around us, is that existing manufacturing technologies apply too many limitations to what you can actually do with composite materials. Structures have to be flat, fibers straight and materials choice was limited. Most technologies are expensive and require hand labour. We wanted to make a technology that has as few such limitations as possible while maintaining the unique properties of composites: strength and lightweight.
Our first product, Anisoprint Composer, already implements most of these ideas. It is a desktop, user-friendly and inexpensive machine, which allows you to reinforce any type of thermoplastic polymers with high strength reinforcing fibers, just like rebar in concrete, making the material a dozen times stronger.
For ease of managing the material properties, we’ve developed our own software — Anisoprint Aura. It’s possible to download it for free from our website. There you can control over the fiber directions and volume fraction to make complex shape structures with desired properties, that are lighter, stronger and cheaper than any other material.
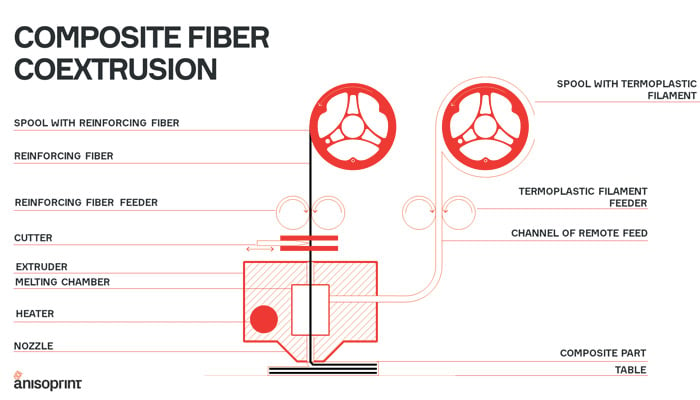
The process behind the coextrusion technology | Credits: Anisoprint
3DN: What are the challenges associated to composite 3D printing? Its benefits ?
The main challenge when printing with composites is associated with the nature of these materials. To create a composite, you have to merge the reinforcement, the component that brings the properties to the material, with the matrix, which makes dissimilar reinforcing elements work together. This is not a simple process. In most of the cases, the reinforcement is a fibrous material, which consists of very long and thin microfibers, and the matrix is a viscous polymer. Merging these two while ensuring good impregnation of fibers with the polymer and good bonding between components is tough.
We do it in two stages: first, we impregnate fibers with a special polymer, which has a low viscosity in an uncured state, easily goes inside the fiber tow and bonds to it tightly. Then we heat it up, and the polymers cures, morphing to a stiff and a solid substance. This is done prior to printing. When we print, we use these composite fibers as a reinforcement, pulling them through the nozzle together with plastic, and plastic bonds these fibers together when they are shaped into a part’s structure. That’s why the process is called coextrusion. Such an approach allows choosing plastic with certain chemical resistance, frictional properties, flame retardancy and other properties you want to print with to make it many times stronger, even stronger than metal.
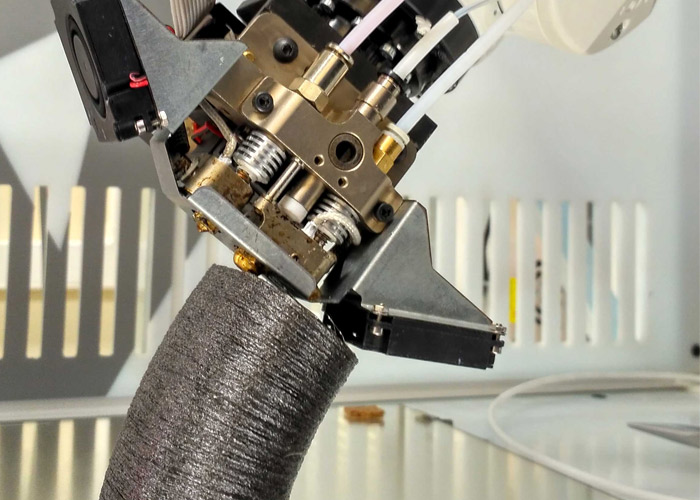
Photo Credits: Anisoprint
3DN: What sectors are you targeting with your solution?
Composites are of the highest demand in the industries, that require low weight. First of all, it’s aerospace (airplanes, helicopters, drones, spaceships), high-performance mobility (sport and racing cars, bikes, bicycles) and healthcare (prosthetic, orthopaedic braces, corsets, insoles). All these sectors are already implementing composite materials in certain products, but composite 3D-printing can increase the number of such parts in these products dramatically. As a result, we will have lighter planes, consuming less fuel and making flight cheaper; electric cars will require less power to move to longer distances; bicycles will be as light as your shopping bag; people with special needs will have custom, slim and light prosthetics that perfectly fit their body.
It is a long path though. We have to be sure that the materials and structures we make are reliable, safe and have a predictable lifespan. That’s why every industry, especially when the product performance can affect people’s lives, require strict and complicated certification procedures. Everything has to be certified: the material, the hardware, the production process. Certification is one of the main barriers today for 3D-printed parts to enter our everyday life. We also work on certification for our materials and technology, but we are, as well as most of the players on the 3D market, at the beginning of the journey. That means today we have to find other applications. There are such segments, for example, manufacturing tools.
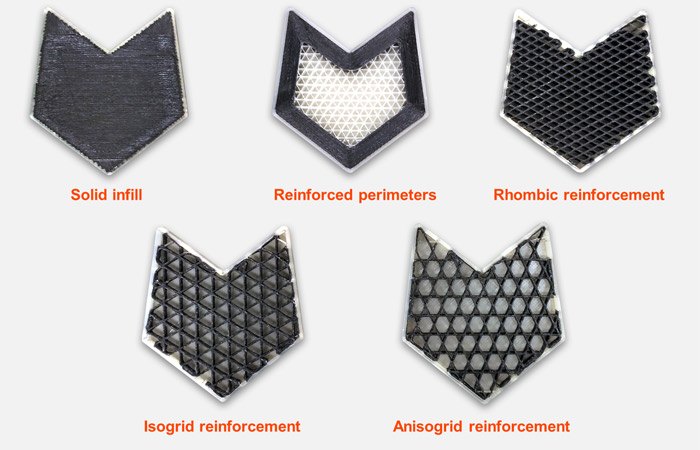
Photo credits: Anisoprint
Most of the technologies our customers use require custom tools, such as molds, dies, clamps, fixtures, jigs and so on. These tools have to be made quickly and on-demand. Often they bear significant loads in operation, require to be stiff and sturdy. In many cases they are handled by workers, so they have to be lightweight. Using anisoprinting it’s possible to get all these properties. Our customers using Composer 3D printer at their production can replace any broken part in some hours, not months like in a case with parts that should be ordered from external tool companies. They focus all this repairment inside their production so reduce equipment downtime. They also significantly reduce costs because printing parts are cheaper, have a longer lifespan and aren’t required such expenses like external companies’ service and logistics.
3DN: What are your future projects?
Now we have two formats of desktop Composer printer, it’s yet a niche product, used for manufacturing tools, jigs and fixtures, non-primary spare parts for bicycles, scooters and wheelchairs. It is also used for research by several Universities in Europe and Russia.
3DN: Any last words for our readers?
The era of 3D printing will come. We just have no other way. The benefits that it has over traditional manufacturing is obvious, so we just need to go for it. There will be applications for various different technologies: plastic, metal and composite, but the way we design, manufacture and deliver things will change forever. And it will be a more sustainable and natural way.
What do you think of Anisoprint and their technology? Let us know in a comment below or on our Facebook and Twitter pages! And remember to sign up for our free weekly Newsletter, to get all the latest news in 3D printing send straight to your inbox!