#3DStartup: Andiamo on their 3D Printing & AI Platform for Orthoses
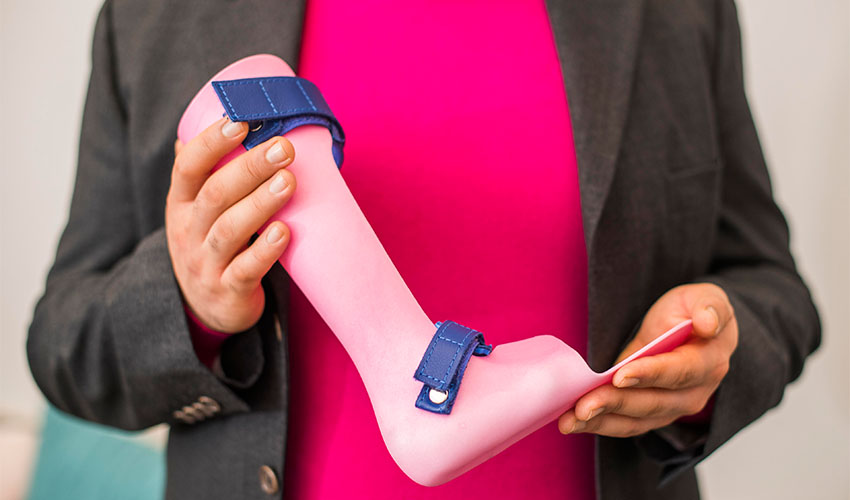
Orthoses are medical devices that are made to stabilise, relieve, immobilise, guide or correct a part of the body. Since each patient is different, an efficient orthotic device should be perfectly adapted to the wearer’s body and needs, which in practice is rarely the case. The startup Andiamo, based in London, empowers clinics and clinicians to offer tailor-made orthoses to their patients thanks to their 3D printing & AI platform. The biggest benefits additive manufacturing brings to this field are accuracy, time and cost. For example, delivering a perfectly tailored 3D printed brace can be achieved within 48 hours instead of the typical three months when relying on traditional manufacturing techniques. In order to learn more about Andiamo’s platform and the changes it seeks to bring to the orthotics industry, we spoke to Chief Commercial Officer, Hugh Sheridan!
3DN: Could you present yourself and your link with 3D printing?
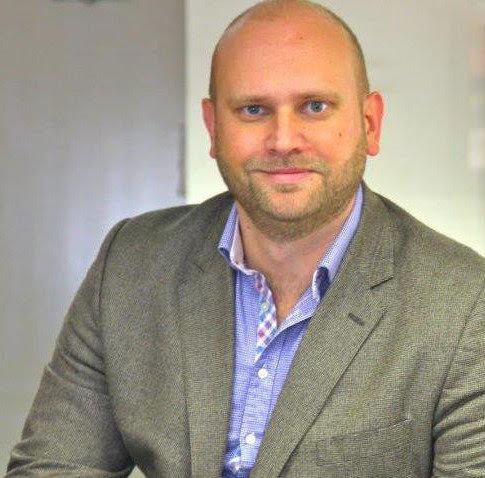
Hugh Sheridan
I am Chief Commercial Officer of Andiamo and have been involved in the Orthotics Industry for over 20 years having been the CEO of the UK’s largest Orthotic Material Manufacturer and Podiatry Supplier. My first project in 3D printing was when we started printing test foot orthotics on an FDM 3D printer using TPU filament as a lattice. The material was brilliant and allowed a whole new range of prescription variables to be met although the 3D printer at that time was slow and unreliable.
3DN: How did the idea of creating Andiamo come about?
The founders of Andiamo are Naveed and Sam, their journey started when their son, Diamo, was born in 2003. Diamo was diagnosed to have severe developmental delay, he was quadriplegic and had very little head control which meant he needed extensive treatment to help him with basic functions. He needed to have a multitude of orthotics braces and gators to help me perform simple actions. Getting his orthotics right was very challenging. The process as a whole was very long and frustrating. Very often, the braces would come a few months after the measurements were taken, by that time Diamo had outgrown them.
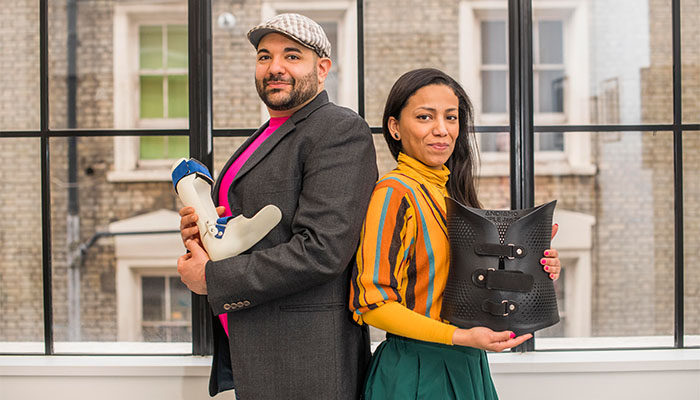
Samiya and Naveed Parvez, the parents of Diamo and founders of Andiamo
After Diamo passed away in March 2012, Naveed and Sam were driven to make sure this experience would never be felt by other parents. Therefore, they started to investigate the existing orthotic service, production, procurement model and realised that 3D printing could allow for many more prescription opportunities, lower cost devices and much higher quality with a first time fitting, which would massively improve the family experience. The Andiamo platform has been developed to work with SLS, MJF and DLS. These technologies allow the Andiamo AI platform to manufacture medical devices at the lowest cost, fastest speed with the most stringent quality controls.
3DN: What are the benefits of 3D printing for the orthotics industry?
Cost, Profit & Time with patients. The whole O&P (Orthotics & Prosthetics) industry is based around making devices using different methods to mould material around including plaster casts, foam boxes, wooden lasts, foam blocks. Once the form of the body and prescription has been created then more sheet material is used to make the device, with the most widely used materials being EVA, PU, polypropylene, polyethylene, polyester, rubber, fibreglass, cotton, carbon and leather. The components such as prosthetic feet and knee joints are then attached to the moulded material. A huge amount of products, components, raw materials and accessories as well as manufacturing equipment are used in this process.
The Andiamo AI platform uses 3D printing, which wipes these costs and supply chain away. There is a massive benefit to clinicians and clinic owners and their relationships with patients. By centralising manufacturing the Andiamo platform is able to provide huge cost savings. At the same time the clinician gets back a huge amount of time from the Andiamo first time fit devices allowing them to spend more time with patients creating better experiences and greater outcomes.
3DN: What is the role of AI in all of this?
There are 3 parts, firstly CAD/CAM systems with CNC machining are used extensively in the O&P industry but they are not as widespread as they could be, apart from insoles where they use templates and shapes, every orthotic and prosthetic wearer is different, so a CAD technician is needed to make sure the correction is built into the machined body form. In order to get a first time fit, 90% of the time we would need to use a CAD technician for the device. Using AI allows us to scale the number of designs to whatever level, whilst still achieving first time fit devices and standing by our promise of not using templates or shapes.
Secondly, FEA (Finite Element Analysis) engineering is built into the design process and AI controls this, allowing a huge range of prescription possibilities. Finally, we also use AI in our quality process as clinicians can visually inspect their device from any browser and sign off prior to print.
3DN: What about Andiamo’s future projects?
We’re not a 3D printing company – we’re in the business of creating happy families. That means having the widest range of orthotic and prosthetic devices available at the lowest cost and highest quality available in all areas of the world. That wearer base will allow us to integrate sensors in all devices measuring, compliance, gait, pressure and activity. We believe that by allowing the clinician to have more data about their wearers, this will lead to better outcomes not just for the patient but their whole family. It’s the future of healthcare.
3DN: Any last words for our readers?
The cloud-based platform that has been built by 30 people in offices in Gdansk and London was in many ways built by accident curing a parents problem. What this group of people have built is a platform and central printing service that offers the O&P industry massive cost savings, first time fit devices and a whole new range of prescription possibilities due to FEA technology in the design process.
What do you think of Andiamo? Let us know in a comment below or on our Facebook and Twitter pages! Sign up for our free weekly Newsletter to receive all of the latest news about 3D printing straight to your inbox!