All You Need to Know About Vapor Smoothing in 3D Printing
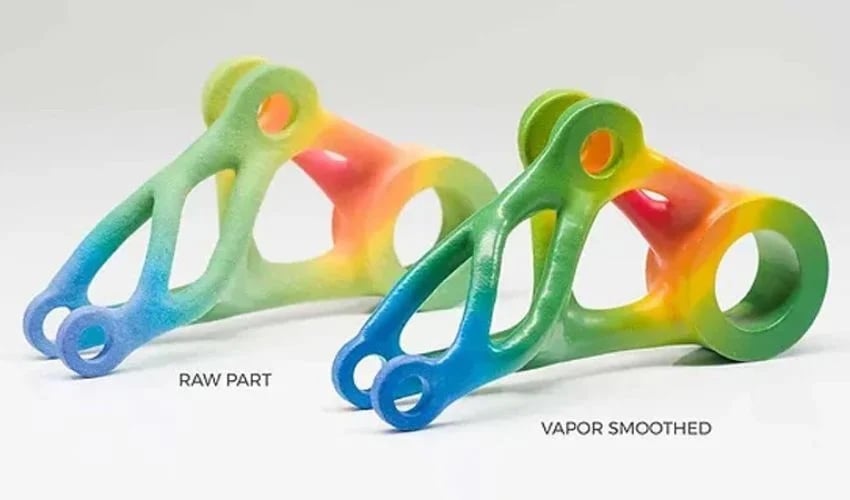
Many parts are not immediately usable after 3D printing and, depending on the printing process chosen, require cleaning and finishing. Through this, it is possible to improve an object’s mechanical properties or refine its surface finish. There are a multitude of techniques available for this purpose, but they always depend on the printing technology, the material and the application. One method of surface treatment for plastic parts is vapor smoothing.
This physical-chemical process densifies and smoothes the surface of thermoplastics. The chemical is applied to the part via steam injection. The longer and more intensive the chemical treatment, the glossier and smoother the 3D printed part. But how does it work, and what do you need to watch out for?
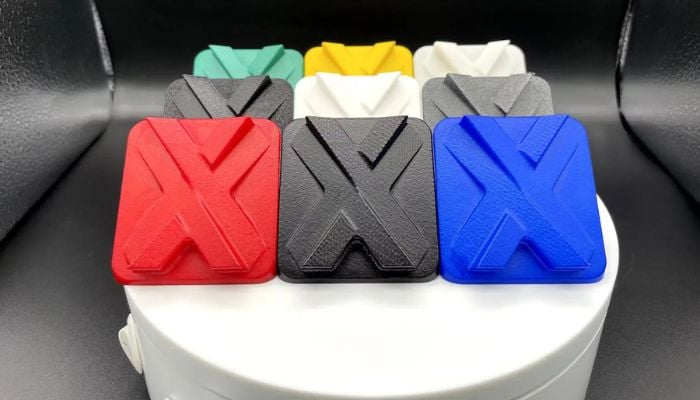
Vapor smoothing is a post-processing technique used to obtain smooth surfaces on 3D printed parts (photo credits: Xometry).
How Does Vapor Smoothing Work?
The principle of vapor smoothing is to liquefy the top print layer under the effect of steam and chemicals, and to reorganize the surface molecules, thus improving its structure. The process takes place in a hermetically sealed, heated chamber, into which the 3D-printed parts are placed.
The chosen chemical solvent is then heated and steam is introduced into the chamber via a feed system. Here, the steam condenses on the surface of the parts, triggering a reaction that partially melts the top layer of the parts. This has the effect of smoothing out rough areas or pores, leaving a smooth, balanced surface.
In dedicated solutions, this smoothing chamber is already integrated. The finishing process takes place automatically in several stages. After heating, solvent addition and chemical melting, the solvent is automatically extracted, leaving no residue on the parts. Parts are also dried directly in the machine.
For best results, the different parts should not touch and rather should be placed or suspended on a grid. This ensures that the chemical treatment takes place on all sides and that the result is homogeneous.
However, parts manufactured by additive manufacturing often feature complex geometries that complicate suspension and placement. In such cases, depending on the geometry of the part, temporary eyelets have to be placed, or even suspensions considered, as part of the design process. These can be removed after vapor smoothing.
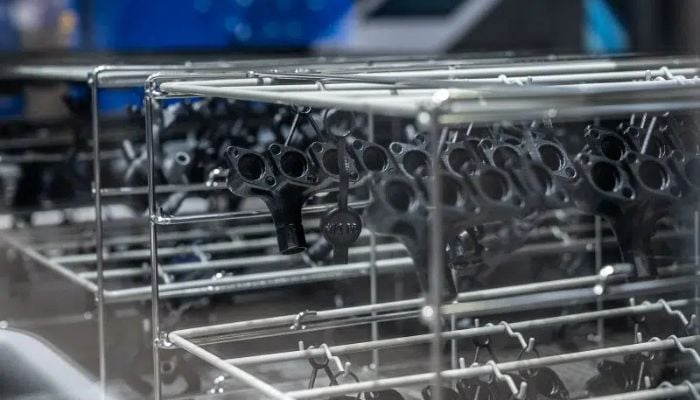
The 3D-printed parts hang in the chamber (photo credits: DyeMansion).
Compatibility With Printing Technologies and Materials
Vapor smoothing is a post-processing method for thermoplastic materials. This means that the technique is compatible with a wide variety of materials – including PA, ABS, PC, PLA, PP, TPU, PETG – which can be processed in different 3D printing technologies.
The process is particularly popular for SLS or MJF parts, which have a rough surface after printing. But parts manufactured using FDM can also be reworked using vapor smoothing.
Depending on the material, different chemicals are used to achieve the best possible result. Acetones are recommended for ABS and ASA, while trahydrofuran (THF) is recommended for PLA. Methyl ethyl ketones (MEK) can also be used for ABS, PETG and PC.
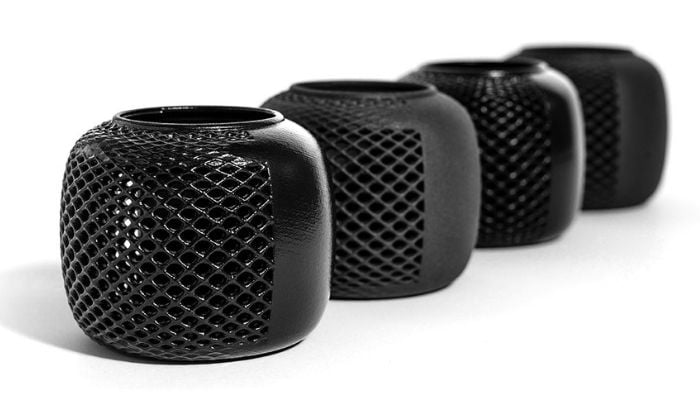
Vapor smoothing is possible for parts made from many different materials (photo credits: Protolabs)
Advantages and Applications
The main advantage of vapor smoothing is that it enables 3D-printed components to be treated so that their surface quality and aesthetics are equivalent to those of injection-molded parts. Appearance and feel are two decisive arguments in favor of vapor smoothing, as it corrects surface heights and depths and produces uniform, smooth surfaces. This, in turn, facilitates the cleaning of components and thus hygiene. Chemically smoothed components are more resistant to dirt and bacteria, enabling a wide range of applications for treated components.
Vapor smoothing also improves part properties. After treatment, they feature enhanced mechanical stability, higher flexural and tensile strength, and improved sliding properties. This advantage can be exploited in particular for thin-walled components, as the reduction in porosity during smoothing has a positive effect on mechanical load-bearing capacity.
By melting and resealing the top layer, vapor smoothing also makes parts water-repellent and resistant to chemicals, which is particularly important for parts that conduct liquids and ensure watertightness. Smooth surfaces also facilitate subsequent coloring or painting, and guarantee uniform coloring.
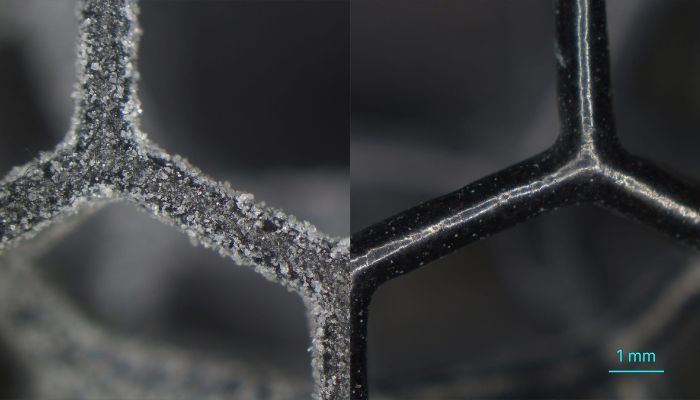
The surface finish of 3D printed parts can be considerably improved by vapor smoothing (photo credits: ASM).
Cost is also a factor, as vapor smoothing delivers fast, inexpensive results compared with other finishing methods. It is efficient and flexible, and opens up a vast field of applications thanks to its compatibility with a wide range of thermoplastics. As a result, smoothed parts can replace injection-molded parts and be used both as prototypes and production parts.
The above-mentioned sealed surface is important for components carrying liquids, such as channels, pipes and parts for fluid mechanics tests. Combined with the improved mechanical properties of the parts, the process is therefore of interest for components used in mechanical engineering, in the automotive industry, but also in aeronautics and aerospace.
Improved hygiene, on the other hand, plays a central role in the medical environment, and chemically smoothed parts can meet the standards of medicine, dentistry, but also the food industry. Design applications also benefit from this finishing method, as smooth, homogeneous surfaces with a glossy finish make for impressive visible parts.
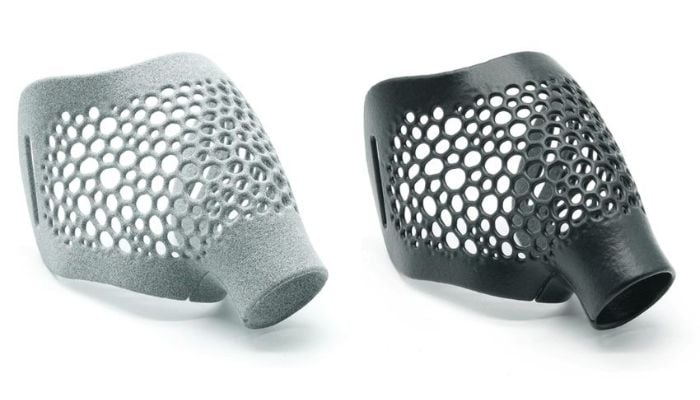
Smoothed parts are used in a variety of industries (photo credits: ASM)
Limitations
Although vapor straightening has many advantages that open the way to a wide range of applications, there are also a few limitations. Indeed, as with any process, there are a number of points to bear in mind which influence the result. For optimum results, the components must be correctly positioned in the smoothing chamber. As mentioned at the outset, natural notches and hooks in the part geometry are an advantage, otherwise eyelets or hangers must be added. The latter may, however, leave marks on the part and reduce its quality.
In addition, parts must not be too thin, as vapor smoothing is not suitable for parts with wall thicknesses of less than 1-2 mm. Even if warping is less than 0.4%, chemical steam treatment can cause distortion and warping effects on large, flat objects.
Finally, it should be noted that handling chemicals always involves a degree of risk. Correct handling and conscientious procedure are essential for user safety.
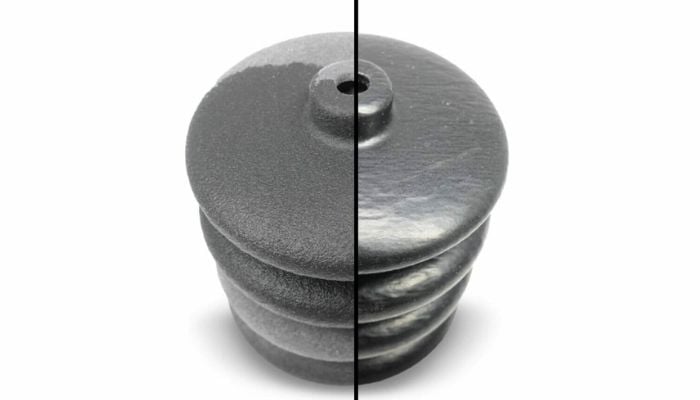
Before vapor smoothing (left) and after (right) (photo credits: ATM)
Manufacturers of Vapor Smoothing Solutions
Although vapor smoothing is becoming increasingly popular for the post-processing of 3D printed parts, the list of machine suppliers for this process is limited. Pioneering British manufacturer AMT offers a high-performance desktop solution with its PostPro SFX system. The PostPro SF Pure and PostPro SF PP machines, on the other hand, are aimed at industrial users. With its Powerfuse S series, DyeMansion is also targeting automated vapor smoothing for industrial applications.
German start-up ASM also specializes in vapor smoothing solutions. With the VX1, the company offers a rapid post-processing solution with cycles of 1.5 to 2 hours.
Do you use vapor smoothing as a post-processing technique? Let us know in a comment below or on our LinkedIn, Facebook, and Twitter pages! Don’t forget to sign up for our free weekly Newsletter here, the latest 3D printing news straight to your inbox! You can also find all our videos on our YouTube channel.
*Cover Photo Credits: Kingroon