All You Need to Know About Sand 3D Printing
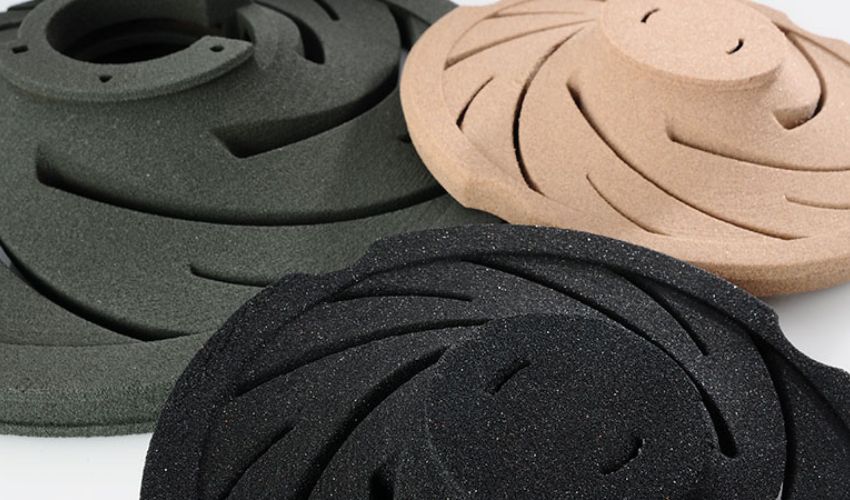
You have almost certainly already heard about plastic and metal 3D printing. But did you know that sand is also a potential 3D printing material? Indeed, it can be a cost-effective solution for a wide range of sectors, and is particularly complementary to traditional sand casting. But how does 3D sand printing work, and how can traditional sand casting benefit from this additive process? We take a closer look at these questions in this article.
To understand the importance of sand 3D printing for casting, it is first necessary to understand the traditional sand casting process. Sand casting is a casting process used to produce final parts in metal and other materials. The mold into which the liquid material is poured is made of sand, which withstands high temperatures. The original casting process has been tried and tested for millennia, dating back to around 3,200 BC. Of course, the manufacturing process has undergone various stages of development, but the basic concept has remained unchanged.
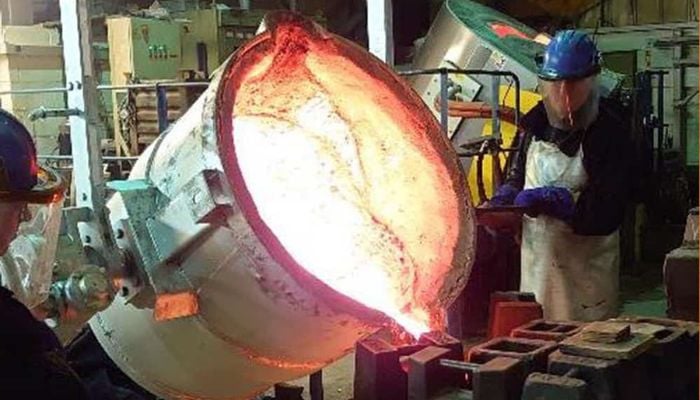
In the sand casting process, a liquid material (usually metal) is poured into sand tanks (photo credits: BigRep)
The process begins with a 2D drawing of the object to be manufactured. Based on this concept, a model is produced, but if it is to be used for final metal parts, its dimensions are increased to allow for shrinkage. In addition, the model must include casting channels. The manufactured negative mold is pressed into a construction box filled with sand. An image of the model – the mold – is then formed in the sand. The liquid material (aluminum, steel, magnesium, iron) is poured into this mold and removed as soon as it has cooled. As part of the finishing stages, the runners and feeders must also be removed.
Although sand casting has a proven track record with detailed results, the process steps mentioned above show that it’s a complex process with many stages. This is where 3D printing comes in. The combination of conventional molding and additive manufacturing makes the process more efficient, as molds or cores for parts with cavities are designed digitally by CAD and manufactured by 3D sand printing. In this way, the steps of model design, model creation and impression in molding frames are eliminated. In short, 3D printing offers a shortcut to the desired objective, saving time, costs and resources.
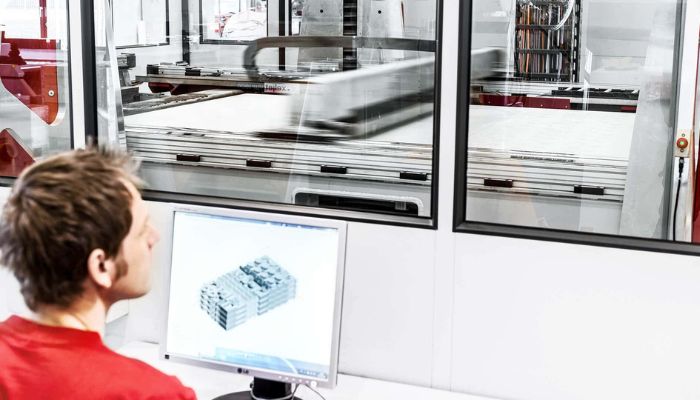
Before printing, the shape design is created by CAD (photo credits: voxeljet)
Before discussing the many benefit in more detail, let’s focus on sand 3D printing itself. Instead of the traditional sand from the sandbox or beach, we use quartz sand, which itself consists mainly of quartz grains. Different types of sand can be used, depending on the casting alloy of the final part. SH-F01 quartz sand is matte and black, while SH-P14 is beige and typically sand-colored. Both offer high heat resistance and strength. Synthetic sand SH C052 can also be used. This is ceramic-based and offers properties similar to those of the above-mentioned types. In 3D sand printing, the sand is then transformed into molds for sand casting by binder jetting instead of traditional powder (metal or plastic).
Benefits and Applications
Binder jetting is considered particularly efficient compared to other 3D printing technologies. This applies not only to the processing of polymer or metal powders, but also to sand. This means that binder jetting not only allows users to skip the many stages of conventional sand molding, but also enables molds to be produced particularly efficiently. The time saved in production also translates into financial gains. For example, mold printing can cut costs by up to 75% over the entire production run.
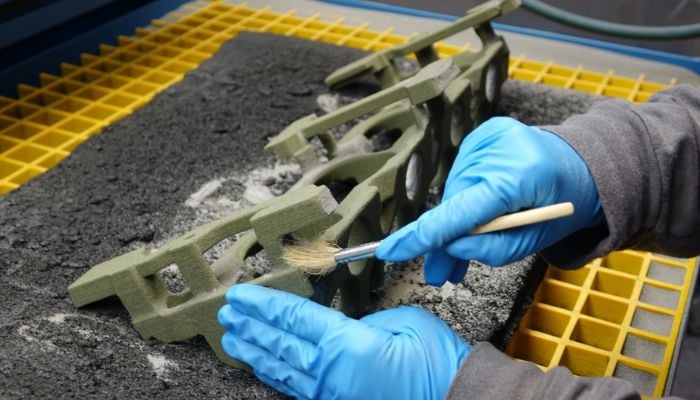
A machine operator cleans sand from a 3D-printed core (photo credits: Hoosier)
The 3D model is designed on the computer, making it easy to make individual modifications and adaptations. Complex geometries can also be realized, and production at any scale. Another advantage is that binder jetted sand molds are dimensionally accurate and can be produced in any quantity. This also offers competitive advantages, as customer requirements can be better met.
In addition to saving time and money, sand printing also saves resources. It is no longer necessary to process materials to create a physical model. Since additive processes largely use only the materials actually required, they also generate less waste. Quartz sand is considered an environmentally-friendly material, it is available in virtually unlimited quantities, and unused printing powder can also be partly reused. In this sense, 3D sand printing contributes to more sustainable production.
Sand 3D printing can be considered for molds for a variety of applications, especially those requiring efficient production of complex parts. This is the case in the automotive or aerospace industries, concrete applications being wheels or propellers, for example. The British Boro Foundry has used sand 3D printing to produce spare parts, for example. The technology can also be used for the manufacture of designer furniture, in art and restoration. It can be used to produce prototypes and small series.
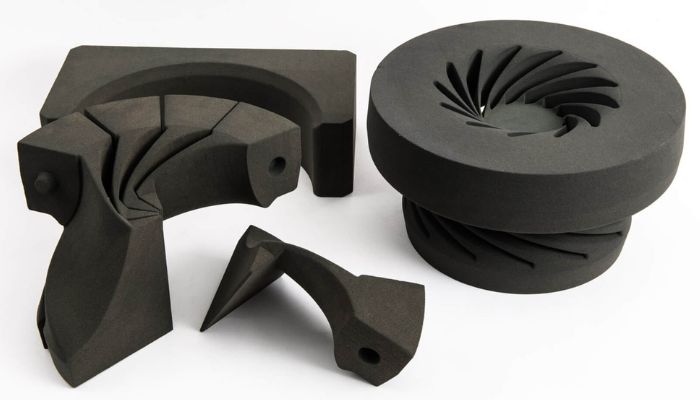
A sand 3D printing mold for a wheel (photo credits: voxeljet)
Sand 3D Printer Manufacturers
Within the 3D landscape, there are a few manufacturers who specialize in sand processing. German company voxeljet, in particular, has made a name for itself in this area. It offers a number of sand 3D printing systems, including the VX 200, 500, 1000, 2000 and 4000 machines, which feature a print tray of various sizes. In addition to voxeljet, we should also mention ExOne (acquired by Desktop Metal in 2021 but still running the sand side of the business), which has also focused on binder jetting systems and is one of the leaders in the sector.
Although sand 3D printing covers a narrower range of applications than 3D printing of resins, polymers and metals, it does meet specific needs. That is why more and more service providers are adding it to their offering, to better meet customer needs and help small foundries that want to reform sand casting by 3D printing, but don’t have the resources to invest in a sand 3D printer themselves.
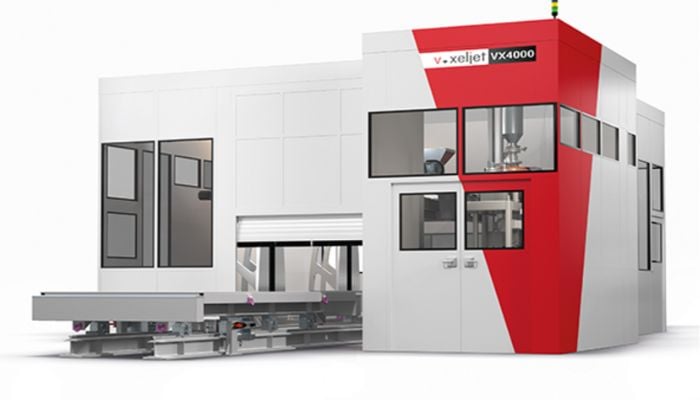
The voxeljet VX4000 is the largest sand 3D printer to date (photo credits: voxeljet)
What do you think of sand 3D printing? Let us know in a comment below or on our LinkedIn, Facebook, and Twitter pages! Don’t forget to sign up for our free weekly newsletter here for the latest 3D printing news straight to your inbox! You can also find all our videos on our YouTube channel.
*Cover Photo Credits: ExOne
Hello,
I am interested in getting a quote for a series of sculptures to be printed out of the 3D printed sand casting method. I have a stp file that I can share with you.
Best,
David