All You Need to Know About Multi-Material 3D Printing
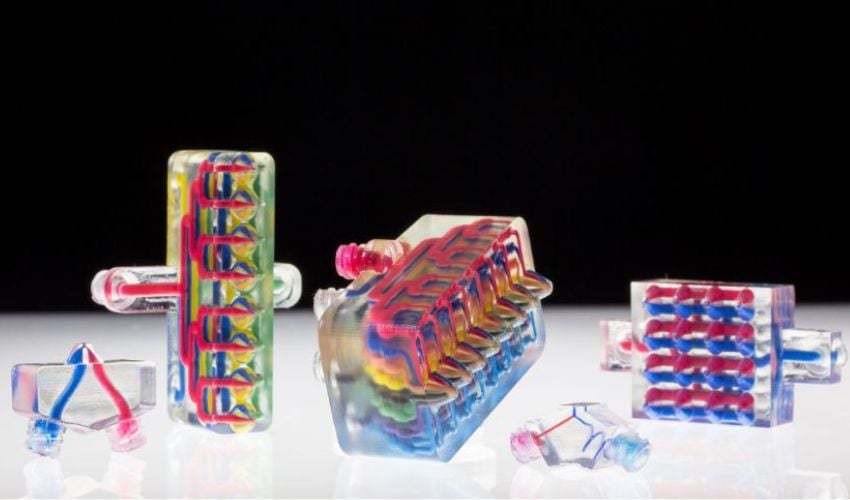
Multi-material 3D printing is, as the name implies, 3D printing several materials in one continuous printing process. It is not the same as multi-color printing, where one material is printed in several color variations. Although the visual result of multi-material printing can be that it contains several colors, the basic aim of printing with multiple materials is to achieve a combination of their properties. Different materials have different characteristics, for example they could be conductive, hard, soft, transparent, chemically resistant, etc. and are therefore particularly suitable for specific applications. In some cases, however, it is necessary to combine the characteristics of different materials in one object in order to fully exploit its application, hence the existence of solutions for multi-material 3D printing.
Indeed, multi-material 3D printing is particularly useful when you want to combine two complementary material properties in one workpiece so that it is, for example, partially rigid and flexible. Multi-material 3D printing also makes it possible to print support structures in a different material that can be easily removed during post-processing. Examples of this include PVA and HIPS. Furthermore, in terms of post-processing, multi-material 3D printing can greatly reduce this, as end parts made of several materials can be produced in one go, making the assembly of individual, separately printed parts unnecessary (thus saving time).
Efficient multi-material 3D printing depends on the technology and hardware used. Although there is a lot of experimentation and constant progress in the field of multi-material 3D printing, not every process is suitable for printing multiple materials at the same time. Currently, multi-material 3D printing is possible with SLA, for example by using several vats with different materials, but also with material jetting (which by design is particularly suited for printing with multiple materials at once). In the latter, printheads are equipped with several nozzles that jet different materials using inkjet technology.
However, FDM is currently one of the most productive and advanced solutions for multi-material 3D printing especially for those who are new to additive manufacturing. Compared to other printing processes, FDM is cost-effective, simple and allows the processing of various thermoplastic polymers and composite materials. Depending on its configuration, an FDM printer can already print various materials. However, depending on the hardware version, there are a few things to consider, which we will discuss below. This guide therefore focuses on multi-material 3D printing for extrusion processes.
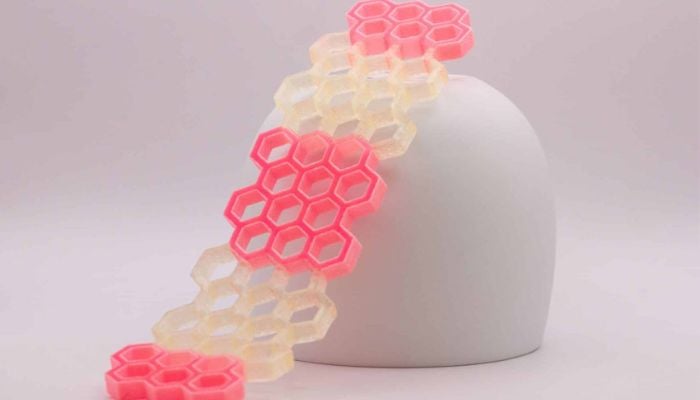
Although multi-material printing is possible with various technologies, it is most advanced with FDM processes (photo credits: Printing with Novojet technology from Quantica / Quantica)
The Multi-Material 3D Printing Process
Like any printing process, multi-material 3D printing starts with the design. Nowadays, most common CAD programs support the labeling of parts with different materials or the assignment of geometries to different materials. For successful multi-material 3D printing, it is then important to set the correct slicer parameters, as the printer needs to know when each material is to be printed. In some cases, corresponding instructions must be integrated into the G-code. However, the exact settings depend on which printer configuration is used for printing; whether it is a printer with one nozzle, whether there are several nozzles or an add-on. Let’s take a closer look at the different possibilities!
Single Printhead
It is perfectly possible to implement multi-material 3D printing with a standard FDM printer. However, if the printer has an extruder with only one hotend and one nozzle, manual material changes must be made. This requires the printer to interrupt printing as soon as a new material comes into play. Corresponding pauses can already be embedded in the G-code. Depending on the slicer, this step can be very simple or quite complicated.
In general, printing with several materials on a standard printer is very time-consuming and labor-intensive, even when small parts are involved. The process becomes more difficult if several materials are used per layer and the materials do not alternate layer by layer.
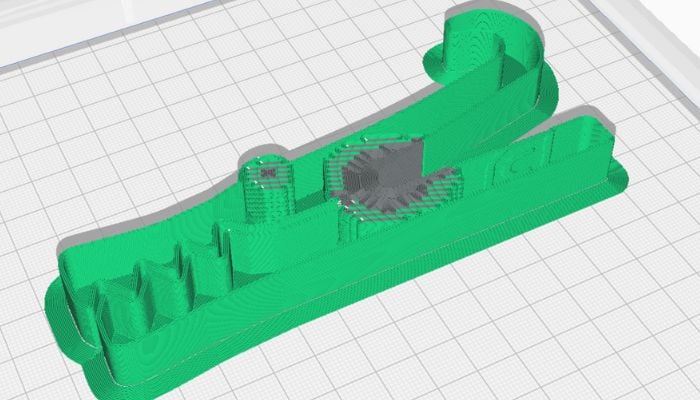
The different materials have to be taken into account as early as the design process and during slicing (photo credits: UltiMaker)
In addition to manual filament changing, there are already printers that provide for printing with multiple filaments. One example, which is mainly used in multi-color printing, is a mixing hotend. However, if this system is to be used for printing with several materials, the respective printing temperatures must be very close to each other – in the optimum case identical – to avoid printing errors.
If you use a printer with a Bowden extruder, you can use a classic Y-splitter to combine two different materials. With the Bowden system, the materials are used and extruded alternately, but are always “ready” so that the eponymous Y shape is formed. This approach is also used for two-color printing and can be extended to a dual Y-splitter for multiple extruders.
In addition to these hardware features, you also have the option of upgrading your printer with add-ons to print with multiple materials. With its MMU1, MMU2 and the latest MM3 multi-material upgrade kits, Prusa has created add-ons that allow printing with up to five different filaments. The MMU is simply attached to a single-material printer and a splitter-based Bowden extrusion system is used to print with multiple materials.
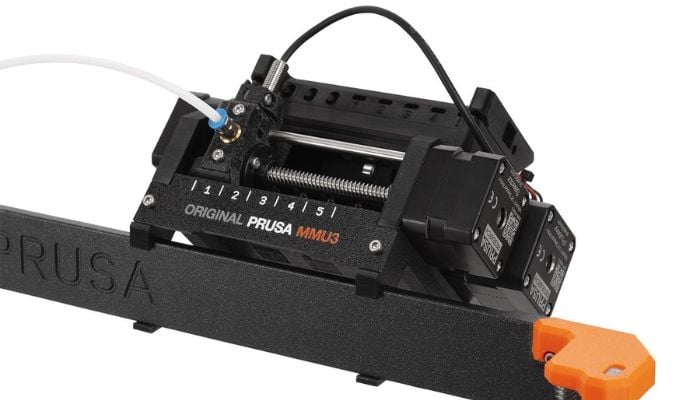
Prusa3D offers the possibility to print multiple materials with its Multi Material Upgrades (MMU) (photo credits: PrusaDd)
Another add-on is the Mosaic Palette. This additional device for FDM printers of all kinds cuts the filaments to size and reassembles them into a single, precise print strand. The filament can then be printed in a single pass without changing or pausing. There are now also suppliers who equip their printers with additional systems for multi-color or multi-material 3D printing. With its AMS (Automated Material System), Bambu Lab has created a system that no longer limits the user to printing with a single filament and allows for versatile, aesthetic and functional prints.
That being said, multi-material prints are much easier to achieve if there are several hotends in one print head. In this case, there is a corresponding nozzle for each material so that no material residue from the previous material clogs the nozzle. There are already single print heads with two to four hotends. However, these make the print head heavier, affecting the printing speed.
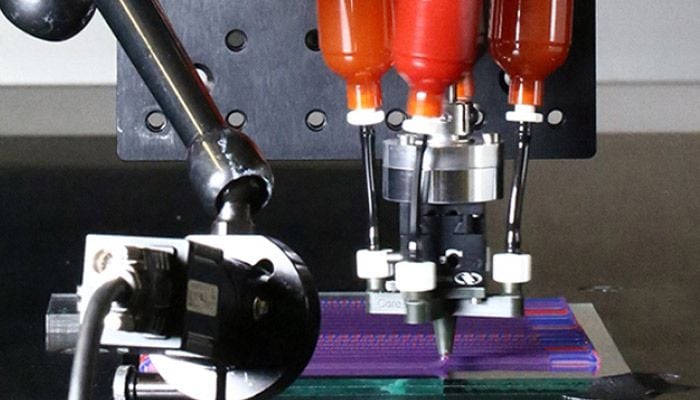
This print head has four filament feeders (photo credits: Harvard John A. Paulson School of Engineering and Applied Sciences)
Multiple Printheads
If the multiple nozzle approach for material extrusion is extended to several printheads, the variety of materials can be further increased. This approach also delivers better results, as the different materials do not come together in one heating block in the hotend. A well-known example of this is IDEX printers (Independent Dual Extruder).
With these printers, there are dual heads, each with a hotend, which are able to move independently to each other. The separate paths of the respective filaments prevent clogging or blockages in the nozzle and some of the most common errors in multi-material 3D printing can be ruled out in advance. However, an IDEX printer can only print two materials at the same time. These are often the base material and the support material.
One tool that pushes the limits of the dual extruder is the tool changer. This tool changer can change heads during operation. These are not only print heads, but also those that can cut, mill and drill (for hybrid manufacturing). In the case of printheads, however, this makes it possible to print different materials with several print heads, similar to IDEX printers.
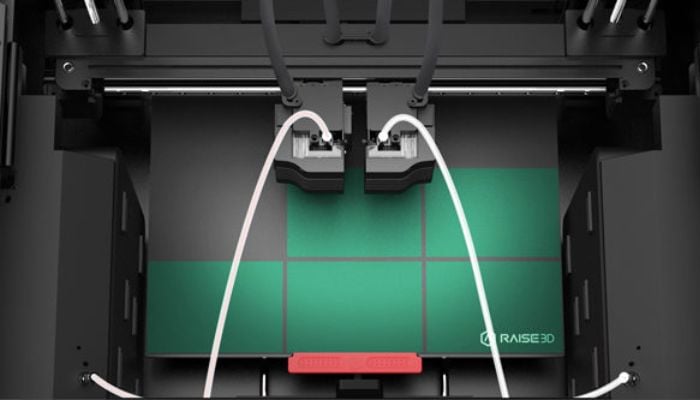
IDEX printers are equipped with two independent extruders and can therefore process two filament types in one print (photo credits: Raise3D)
Applications, Benefits and Limitations
The core objective of multi-material 3D printing is to give an end part different properties. These can relate to the appearance, the material properties or the texture. For example, an end piece can have both glossy and matt parts or be equipped with filling materials.
In terms of its material properties, a multi-material print can be hard, heat-resistant, flexible and much more by combining the different materials that provide these properties. The surface can also be created specifically and have a positive effect on post-processing as well as the feel. By eliminating the need to piece together individual components in multi-material prints, a tedious post-processing step is even eliminated altogether.
The different, combined material properties also open up various application possibilities in a wide range of sectors. Multi-material 3D printing is used for microfluidic chips or for grippers in robotics and soft robotics, where flexible, soft and hard, durable parts are required. Multi-material 3D printing is also increasingly being used in medicine. Materials such as TPU (soft) and carbon fiber composites (hard) are often combined for 3D-printed prostheses. Success is not guaranteed with multi-material 3D printing, as caution is required to achieve the desired results.
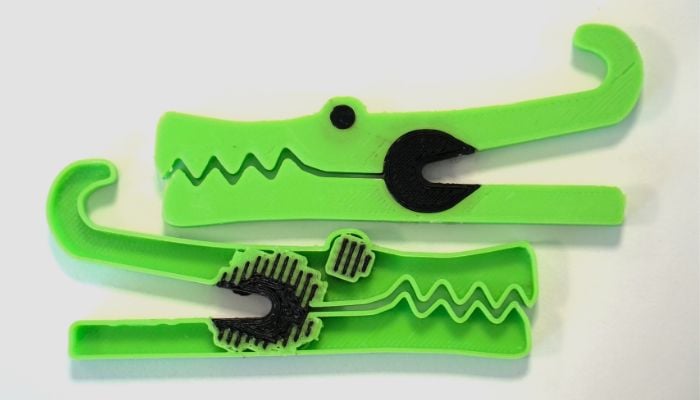
Multi-material prints are used in many areas when different properties are required in a workpiece, for example hard and soft (photo credits: UltiMaker)
When designing the print object, the question arises as to how the different materials should interlock, for example whether they should overlap or join together in a zipper system. It is important to create both a form-fit construction and a “fabric-fit” construction. Some filaments do not combine well due to their different properties. If the processing temperatures are too far apart, for example, it will be difficult to process them together. Even if the materials are similar, like adheres better to like. To artificially improve adhesion, interface layers can be used to better bond the layers together.
The material properties also determine the printing properties. Different materials require different settings in the printer in terms of nozzle temperature, print bed temperature, speed and retraction. All these parameters must be taken into account when combining two or more materials. These regulations also have the highest error rate and therefore, depending on the hardware used, there are a few things to keep in mind. For example, if you are using a single extruder with only one hotend from whose nozzle all the materials used are extruded, it is necessary to ensure that the materials do not mix there. Otherwise, a backlog can occur and, in the worst case, the nozzle may have to be replaced. This is particularly the case if unusual materials such as wood or metal are used for printing. If several extruders are used, dripping from the unused nozzle can become a problem; this phenomenon is also known as oozing.
Manufacturers of Printers for Multi-Material 3D Printing
There is now a wide range of printers for multi-material 3D printing, including desktop solutions, industrial systems and various add-ons and upgrades, as outlined above. One of the first multi-material printers was the Fab@Home, which was launched in 2006. At the maker level, Prusa, Bambu Lab and Flashforge stand out with their solutions, as well as Raise3D and UltiMaker. The Flashforge Creator 4, the Prusa XL with its up to five materials and the E2 from Raise3D are particularly noteworthy.
Industrial solutions are offered by Modix with the Modix Big-120Z, OMNI3D with the Factory 2.0 and Factory 2.0 NET and WASP with the Delta WASP 2040 Industrial X, among others. AIM3D also focuses on multi-material 3D printing at industrial level and even combines pellets and filaments in its printing systems. Whichever solution you choose to implement successful multi-material 3D printing, it is essential to consider the material properties and printer settings in advance.
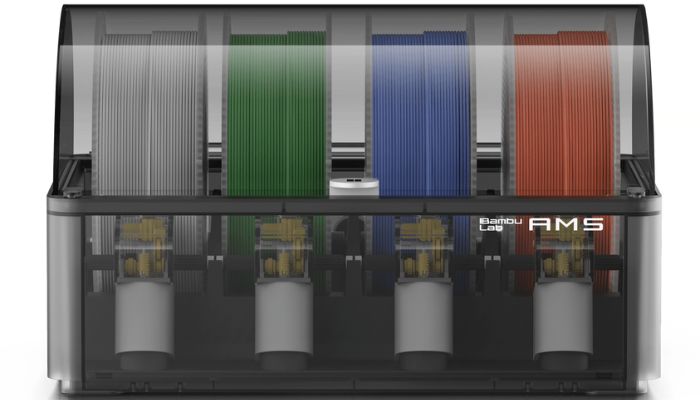
Bambu Lab’s AMS allows different filaments to be processed for multi-color or multi-material printing (photo credits: Bambu Lab)
Do you use multi-material 3D printing?Let us know in a comment below or on our LinkedIn, Facebook, and Twitter pages! Don’t forget to sign up for our free weekly newsletter here, the latest 3D printing news straight to your inbox! You can also find all our videos on our YouTube channel.
*Cover Photo Credits: Harvard University