3D Printing Steel: Everything You Need to Know!
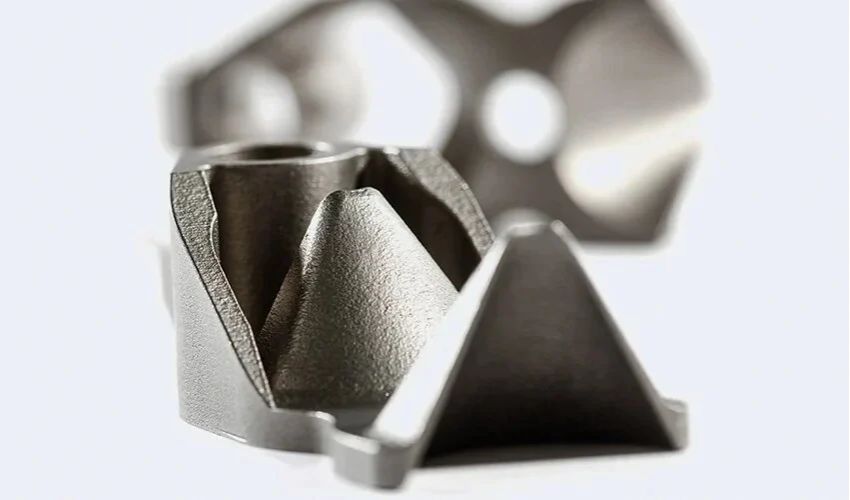
Steel is a well-known metal in the industrial production and 3D printing sectors. It is an alloy based on iron (Fe) and other elements, mainly carbon (C), but also materials such as zinc (Zn) or silicon (Si). These alloys modify the properties of iron according to the combination obtained, generating a more resistant or less oxidizable material. The metal is widely used as a resource in construction and as a raw material for various tools and mechanical parts. To better understand the properties of this metal, its applications and its compatibility with 3D printing, read this comprehensive guide.
Characteristics of the Material
Steel, like other types of powdered metal, can be obtained in different ways. The most common process is atomization, where the metal or alloy is melted and then dispersed in a fine spray. High-pressure jets of gas or water divide the molten metal into small droplets, which solidify into powder particles as they cool. Using inert gases (such as nitrogen or argon) minimizes powder oxidation during the process. Metal powders can then be mixed with alloying elements or other powders to obtain the desired chemical composition. The most common types of steel used in 3D printing are :
- 316L: It is the most widely used stainless steel in 3D printing. Composed of iron, chromium, nickel and molybdenum, this low-carbon metal offers high corrosion and pitting resistance, ductility and good thermal properties.
- Martensitic: This type of steel is highly alloyed with chromium and other elements. Its metallographic structure consists of martensite, and that’s where it gets its name. Martensitic steel can offer high-strength performance similar to aluminum for the same weight but is considerably more economical.
- 17-4PH: This material, which is also stainless, is characterized by high yield strength and good resistance to corrosion and wear. 17-4 PH is one of the leading hardenable steels and is compatible with additive manufacturing.
- 304: This is an austenitic stainless steel containing austenite-forming elements. It generally contains a minimum of 18% chromium and 8% nickel, combined with a maximum of 0.08% carbon. It offers good weldability, corrosion and oxidation resistance, and excellent toughness.
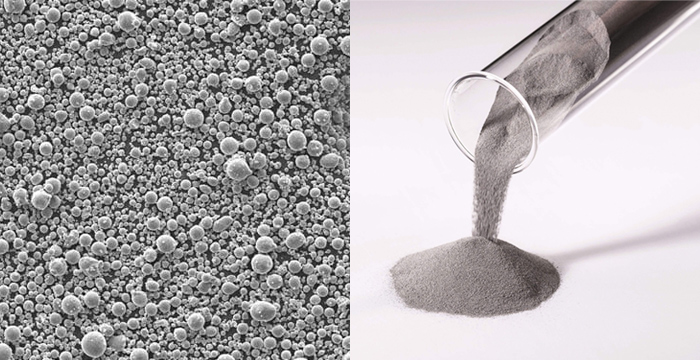
Within the large family of steels, a number of them are compatible with additive manufacturing
Processes for 3D Printing Steel
Steel is compatible with all metal 3D printing technologies. The most common is laser powder bed fusion (PBF), where a laser or electron beam melts metal powder into a solid layer. Powder binding, also known as binder jetting (BJ), is another 3D printing technique compatible with steel. In this case, metal powder is spread over the printing plate, then bonded with a binder deposited where the metal is to be fused. Finally, it is also possible to create steel parts using DED (Direct Energy Deposition) technology. In this case, the material can take the form of a powder or filament, which is deposited as it fuses, using a laser or electron beam as the energy source.
Whatever method is used, the steps are repeated layer by layer until the final part is finished. Then, when working with metal, appropriate post-processing is necessary. This includes removing unmelted powder for BJ and PBF technologies, but also using different surface finishing tools for DED.
Main Applications and Price
Steel 3D printing can be used in a wide variety of applications. Most are implemented in demanding sectors that require high-quality parts with advanced properties, like medicine. As a biocompatible material, steel is used to create all kinds of customized implants, medical devices and high-precision surgical instruments. In addition, its good mechanical properties, such as resistance to corrosion and high temperatures, make it attractive to the aerospace and automotive industries. Applications include exhaust systems, injection molds, tooling, end parts, brackets and fasteners.
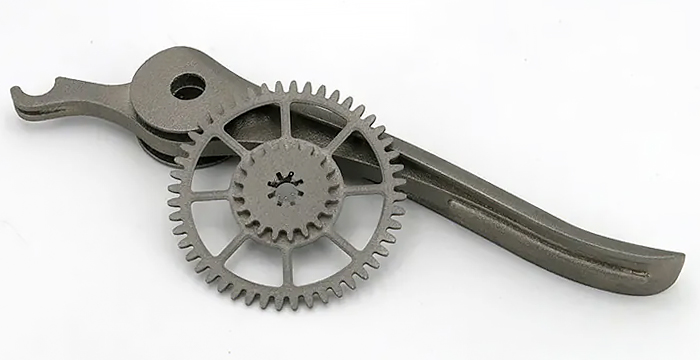
Photo credits: Sculpteo
Metal 3D printing technologies are more complex than additive manufacturing of plastics or resins. Although steel is not a precious metal, its powder can be expensive. In addition, materials heated to their melting point require a long cooling time, which reduces machine utilization compared to SLS technology. Consequently, the cost of the material and the machine, which often requires a high initial investment, are factors to be taken into account. Depending on each application and user, it will be necessary to assess whether it is cost-effective to adopt it despite the excellent results obtained on metal parts.
Have you 3D printed steel? Let us know in a comment below or on our LinkedIn, Facebook, and Twitter pages! Don’t forget to sign up for our free weekly Newsletter here, the latest 3D printing news straight to your inbox! You can also find all our videos on our YouTube channel.
*Cover Photo Credit: Materialise