AL3D-Power Trio: ALPHA LASER Combines Safety, Resource- and Cost-Efficiency in One Metal 3D Printing System
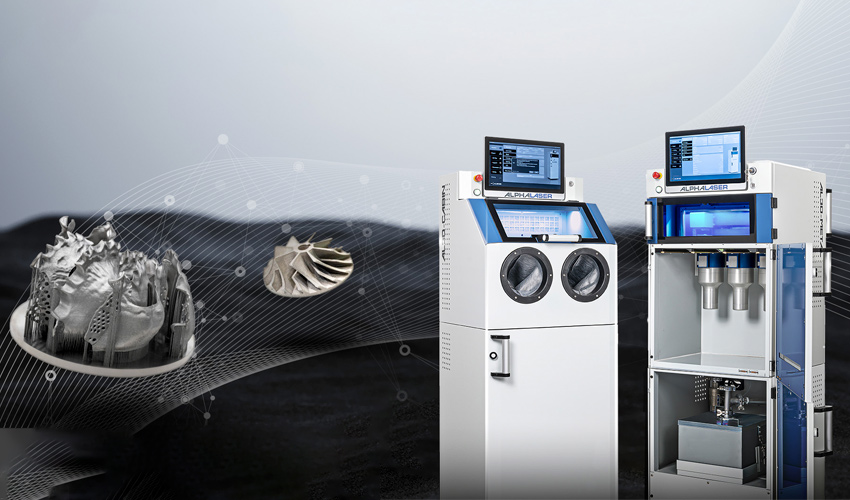
“How can we provide our customers with the best possible support for their tasks with a new machine?” – This question is at the beginning of all product development at ALPHA LASER GmbH. The company has set itself forth as one whose employees breathe life into the machines and thus help users to perform their work at the highest level. The Puchheim, Germany-based family business was founded back in 1994 and has been a pioneer in the development and manufacture of laser systems for welding, powder cladding and metal hardening ever since. Thanks to its flexibility, durability and the enormous range of laser power classes, ALPHA LASER GmbH systems can be found in a wide variety of sectors in trade and industry. Examples include classic sectors such as tool and mold making, the automotive industry and sheet metal processing, as well as the dental, medical technology and jewelry industries.
ALPHA LASER combines engineering expertise with state-of-the-art manufacturing techniques and is constantly adapting to changing market situations. With the rise of additive manufacturing combined with the company’s profound knowledge of laser material processing, it was therefore only a logical step to add a 3D printer developed in-house to the product portfolio. In 2020, the AL3D printer system was finally presented – a complete solution for metal additive manufacturing using metal powder bed laser beam melting (laser powder bed fusion – LPBF).
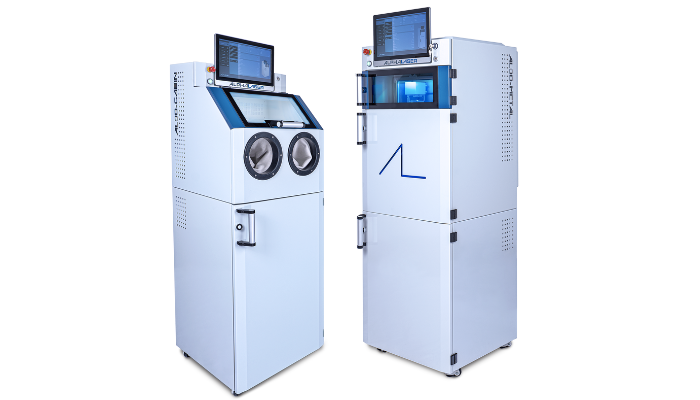
ALPHA LASER has been a specialist in laser treatment options for 30 years. The AL3D is the company’s first 3D metal printer
Metal 3D printing offers some significant advantages over conventional manufacturing processes using injection molding or machining. These include increased sustainability, almost unlimited design freedom for the components to be manufactured and reduced production time and costs. Machining production results in a material loss of up to 70%, whereby the chips have to be further processed in a complex and energy-intensive recycling process.
In additive manufacturing, such as selective laser melting, this figure is reduced to less than 5%, as the unused powder can be processed by a simple sieving process and fed directly back into the subsequent printing process. This results in significant resource savings. In addition, with LPBF, components are produced directly from a powdered base material using a digital file. The upstream production of injection molds and the associated restrictions with regard to component geometries are completely eliminated.
In addition to the purely functional advantages of laser-based production technology, regardless of whether it is laser welding, hardening or selective laser melting, the safety of the user is always at the forefront of ALPHA LASER products. With the AL3D metal printer complete system, the company has therefore developed a concept that minimizes the user’s contact with the metal powder during handling. As a result, the printer offers excellent application possibilities in the dental, medical, small industry and jewelry sectors and is suitable for use in educational institutions and laboratories.
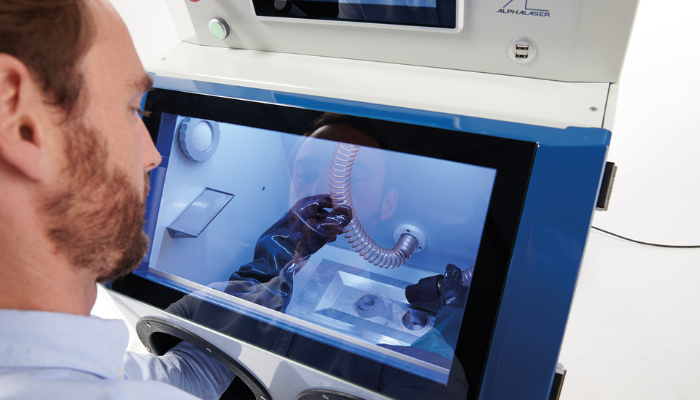
With the AL3D, the unused powder can be removed and recycled completely safely
Ensures Reliable Metal 3D Printing With the AL3D System
The AL3D system, also known as the AL3D-Power Trio, is made up of three individual systems: the AL3D-CABIN – a powder handling station, the AL3D-CARTRIDGES – the exchangeable cartridges, which also function as powder reservoir, build and overflow cartridges, and the heart of the trio, the AL3D-METAL 200 – the actual metal 3D printer. These three systems interlock seamlessly and enable an intuitive and user-friendly printing process that can be broken down into the following steps: insert an empty cartridge into the AL3D-CABIN and fill it with the desired material, insert this filled cartridge (powder reservoir cartridge) together with two empty cartridges (build cartridge and overflow cartridge) into the AL3D-METAL, select the print file, prepare the powder bed, start the printing process, done.
Thanks to the intelligent AL3D-CARTRIDGES, safe and economical powder handling is possible. The cartridges are currently available in two diameters, 50 mm and 100 mm, and in three different heights: 50 mm, 85 mm and 120 mm. They each have their own locking mechanism that automatically locks the cartridge as soon as it is removed from the AL3D-CABIN or AL3D-METAL. The user’s contact with the powder is thus reduced to a minimum, which limits the need for special protective equipment.
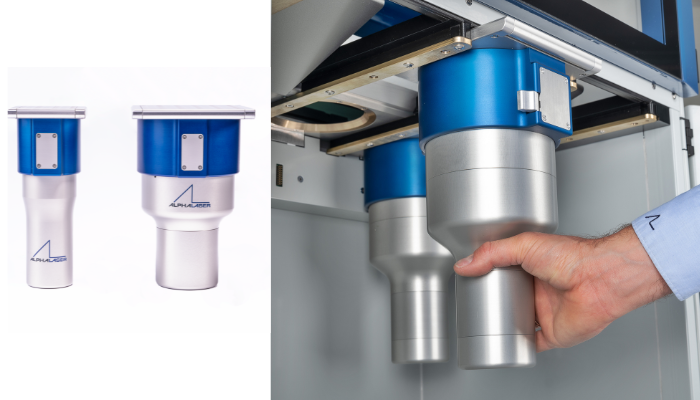
In the AL3D-CARTRIDGES, the powder is transported back and forth between the printer and the powder handling station in complete safety
During print preparation, as already mentioned, an empty cartridge is filled with the desired material in the AL3D-CABIN and then inserted into the AL3D-METAL together with two empty cartridges. The filled cartridge serves as a powder reservoir during the printing process and provides the printing process with fresh metal powder. The two empty cartridges, on the other hand, act as the build cartridge – the cartridge below the scanner optics, in which the component is produced via laser melting – and as the overflow cartridge – the cartridge in which the excess powder is collected.
The AL3D-METAL has a powerful laser and a closed gas circuit for reduced gas consumption. With a footprint of just 600 x 617 mm, it is one of the most compact metal 3D printers on the market. For this reason, the system is particularly suitable for use in laboratories, studios, offices and educational institutions.
The AL3D-OS all-in-one software solution, also developed by ALPHA LASER, which is integrated into every AL3D-METAL and is also available as a desktop version, enables intuitive and rapid print project creation, including support structures, process parameters and slicers. Thanks to remote access to the printer and the integrated camera, the printing process can be conveniently monitored and controlled from the office or even from home. Moreover, with the help of laser powder bed fusion, the printer is able to achieve material densities of > 99.9% for the printed parts.
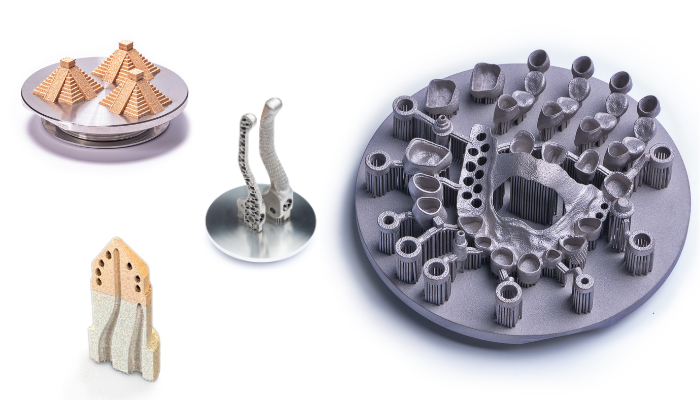
The AL3D-METAL can be used to process various materials for a wide range of applications
ALPHA LASER Power Trio Allows for Process Reliability Thanks to Minimal Powder Contact
After printing, the build cartridge is removed from the AL3D-METAL and reinserted into the AL3D-CABIN. Here, the printed objects are separated from the remaining metal powder and optionally prepared for subsequent post-processing. The residual powder can be conveniently collected and/or sieved for recycling. Thanks to the closed process chamber, this machine also offers a high level of safety for the user.
The entire printing process is characterized by reliability, precision and, above all, safety. Particularly noteworthy is the aspect of process reliability with significantly reduced powder contact, which sets ALPHA LASER apart from other metal printers on the market with the AL3D-METAL. The wide range of possible applications already mentioned above and the optimum material utilization for reducing costs and increasing sustainability round off the promising, high-quality overall package. You can find out more about ALPHA LASER HERE.
What do you think of the AL3D Power Trio from ALPHA LASER?Let us know in a comment below or on our Linkedin, Facebook, and Twitter pages! Don’t forget to sign up for our free weekly Newsletter here, the latest 3D printing news straight to your inbox! You can also find all our videos on our YouTube channel.
*All Photo Credits: ALPHA LASER