ORNL develops AI software to assess 3D printing quality in real-time
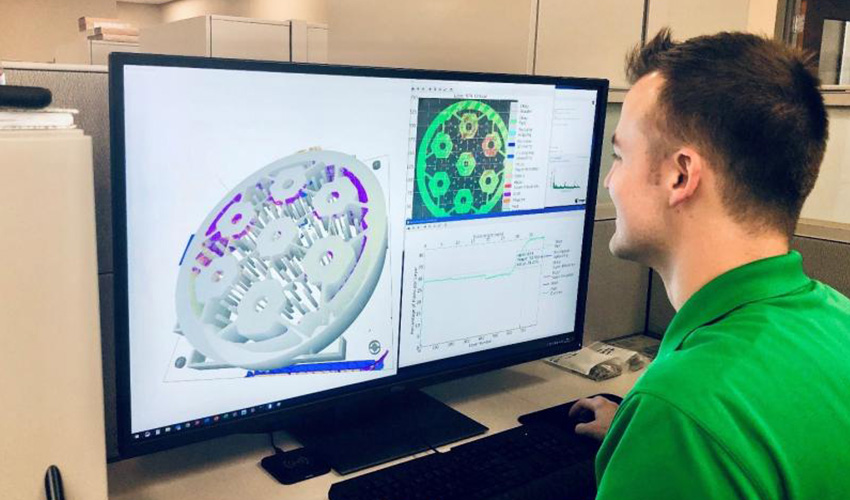
The automation of various stages of the 3D printing workflow will accelerate industrial 3D printing. When parts are made at scale, repeatability becomes essential, however 3D printing systems cannot always provide this. Therefore, part of this automation concerns assessing the quality of parts being 3D printed in real time. At the Oak Ridge National Laboratory, researchers have developed an artificial intelligence program to do this. The software collects and analyses data through every step of the manufacturing process, from design, feedstock selection, print build to material testing.
By capturing the information as a part is being 3D printed, the artificial intelligence is able to create a digital clone of each part. This clone provides a trove of data, from the raw material to the operational component. One of the researchers at ORNL, Vincent Paquit, explains: “We then use that data to qualify the part and to inform future builds across multiple part geometries and with multiple materials, achieving new levels of automation and manufacturing quality assurance.” In the future, the aim is to have this data enable the 3D printer to be self-correcting in real-time.
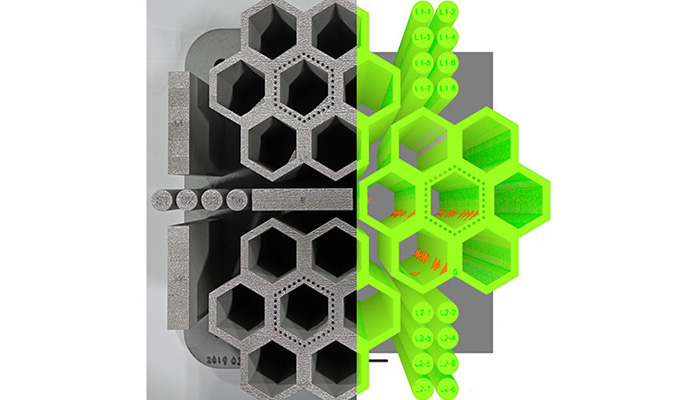
Defect detection | Credits: Luke Scime/ORNL
This concept requires a control method at the end to determine if the parts are ready to be installed in essential applications like cars, airplanes and energy facilities. By developing a computer vision technique that quickly analyzing images captured from cameras installed on the printers, ORNL’s software can control for surface-visible defects. When the software detects any anomalies, it automatically alerts operators so adjustments can be made.
First developed for powder bed fusion systems, the researchers explain that anything can cause a defect in the part. Such as problems with uneven distribution of the powder or binding agent, spatters, insufficient heat, and some porosities. “One of the fundamental challenges for additive manufacturing is that you’re caring about things that occur on length-scales of tens of microns and happening in microseconds, and caring about that for days or even weeks of build time,” said ORNL’s Luke Scime, principal investigator for Peregrine. “Because a flaw can form at any one of those points at any one of those times, it becomes a challenge to understand the process and to qualify a part.”
Scientists are developing an AI software that can be installed on any powder bed fusion system. It produces a common image database that can be transferred to each new machine to train new neural networks quickly, and it runs on a single high-powered laptop or desktop. Standard cameras were used in the research, ranging in most cases from 4 to 20 megapixels and installed so they produce images of the print bed at each layer. The software has been tested successfully on seven powder bed printers at ORNL so far, including electron beam melting, laser powder bed, and binder jetting. You can find more information as detailed in the journal Additive Manufacturing HERE.
What do you think of this AI software to assess 3D printing quality in real-time? Let us know in a comment below or on our Facebook and Twitter pages! Sign up for our free weekly Newsletter, all the latest news in 3D printing straight to your inbox!