AFRL Uses Additive Manufacturing to Make Single-Block Rocket-Engine Thrust Chamber
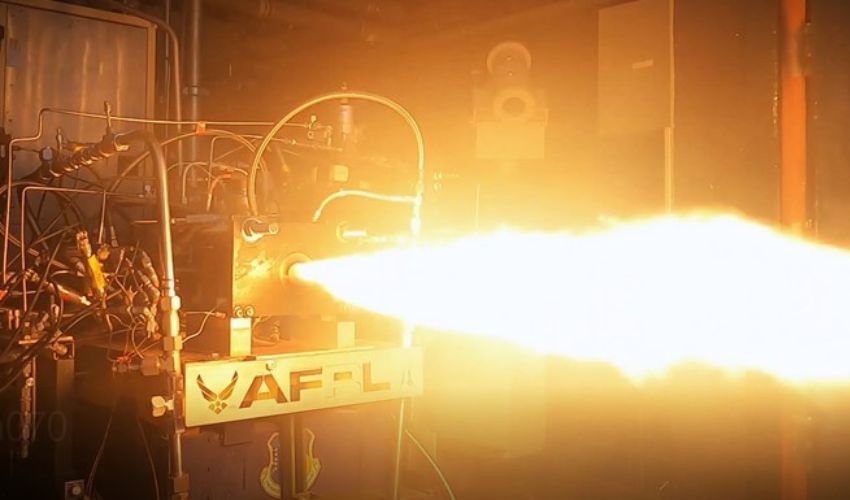
The American military has been one of the most fervent adopters of additive manufacturing in recent years. From submarine parts for the Navy to the Army’s 3D printed barracks and hulls for vehicles, there are no shortage of examples of how the United States Armed Forces have turned to 3D printing for its speed and flexibility. Now yet another branch has once again showed its commitment to the technologies. The Air Force Research Lab (AFRL), the primary scientific research and development center for the Air Force, recently announced that it has designed, printed and hot fired a first-ever, single-block rocket-engine thrust chamber using laser powder directed energy deposition (DED).
Rocket engines are an area where we have seen rapid adoption of additive manufacturing technologies in recent years. NASA especially has been leading the charge, unveiling, for example, a 3D printed rocket engine nozzle made in one-piece from aluminum at the end of 2023. Private companies like Ursa Major and Relativity Space have also made great strides, notably with Relativity’s successful lift-off last year. 3D technologies have become valued in the space for their ability to quickly create multiple iterations and even end-use parts. This has also been the case with this latest example, the 3D printed rocket-engine thrust chamber from the AFRL.
AFRL Uses DED to Make a 3D Printed Rocket Engine
To create this 3D printed rocket engine, the AFRL Rocket Propulsion Division, which is a part of the Aerospace Systems Directorate, has been working with other actors in the U.S. space industry. The idea has been to embed advanced AM processes into robust digital engineering environments, according to a press release from AFRL. Showing not just the maturity of 3D technologies, but their increased importance when it comes to rocket manufacturing.
The use of DED was no accident either. Dr. Javier Urzay, chief of the Combustion Devices Branch at AFRL, expanded, “It provides the largest build box volume for thruster hardware to date, capable of printing seven-foot-tall parts. This build box volume is much larger than that obtainable with techniques like the laser powder bed fusion, or LPBF, process. In addition, DED enables an order of magnitude less investment in powder and less material waste. Engineers can also realize alloy blending and transitions in real time for multi-alloy builds to exploit the strength, weight and performance gains of next-generation superalloys.”
He continued, “These unique capabilities allow us to tackle complex engine designs requiring fewer iterations and leveraging shape optimization, lightweight materials, advanced metal alloys and composites, and rapid manufacturing.”
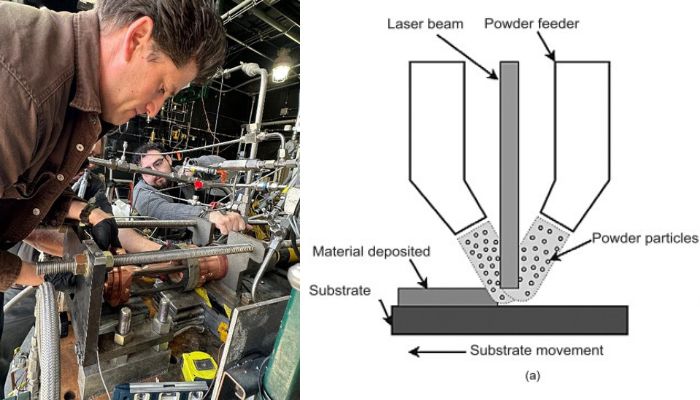
Left: Edgar Felix, Lead Investigator, front and Isaiah Jaramillo, Mechanical Specialist, work on the single-block rocket-engine thrust chamber (photo credits: U.S. Air Force); Right: Though they did not share the exact solution used, the AFRL notes that they turned to laser powder directed energy deposition (photo credits: Wae Zin Tan et al.)
DED was in turn combined with other technologies often found in Industry 4.0 including artificial intelligence, machine learning, digital twins, 3D volumetric scanners and CAD design. The hope is that the integration of these various technologies will help with the transition from traditional manufacturing methods for rocket engine hardware to automated manufacturing processes. Furthermore, this should help to overcome some of the challenges still hindering AM adoption.
Indeed, the AFRL confirms that the nature of the digital environment is necessary to manage printers producing parts. This includes lightweight thrust chambers, manifolds, injectors, pressure vessels, valves and turbomachinery blades which are being made with AM a way to achieve 3D shapes and internal features not easily achievable with traditional processes. You can find out more in the press release from the AFRL HERE.
What do you think of AFRL’s 3D printed rocket thrust engine? Let us know in a comment below or on our LinkedIn, Facebook, and Twitter pages! Don’t forget to sign up for our free weekly newsletter here, the latest 3D printing news straight to your inbox! You can also find all our videos on our YouTube channel.
*Cover Photo Credits: U.S. Air Force