Advanced b-FDM Breakthrough Enhances Material Blending in 3D Printing
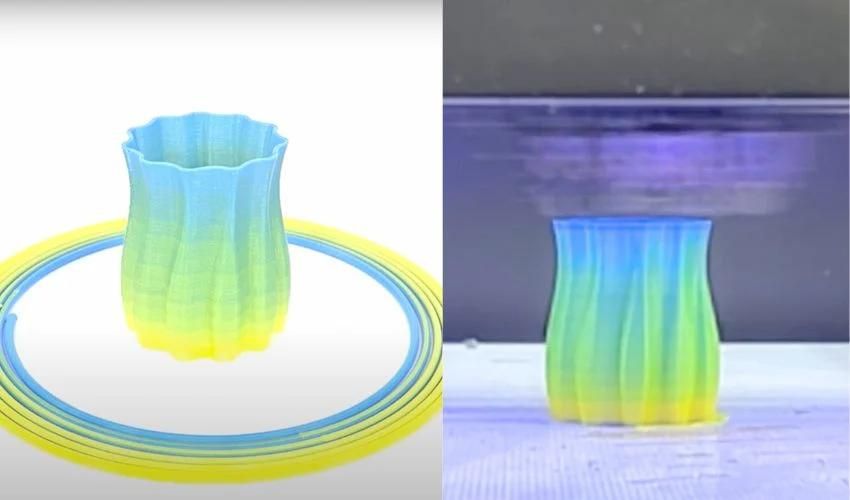
Fused Deposition Modeling (FDM) offers many advantages, particularly its accessibility and office-friendliness, making the technology appealing. However, the extrusion nozzle can only print and process one type of filament at a time, limiting precise, spatial control of material blending. To address this limitation, researchers Sang-Joon Ahn, Howon Lee, and Kyu-Jin Cho from Seoul National University have developed a unique two-step process for FDM 3D printing, allowing different properties to be combined in a single base material. Using this Blended-FDM (b-FDM) method, they successfully printed a single FDM filament with 36 different colors by utilizing four primary color filaments.
The b-FDM process consists of two steps. First, the team printed digital material (DM) by layering different base materials and manually switching between them. The resulting filament is then used as the base material for the final object in the second step. As the filament is extruded through the nozzle, the materials are mixed, creating the desired properties in the final product. This technology enables the printing of diverse material properties by combining several base materials into a single DM filament, ensuring precise control over the material composition.
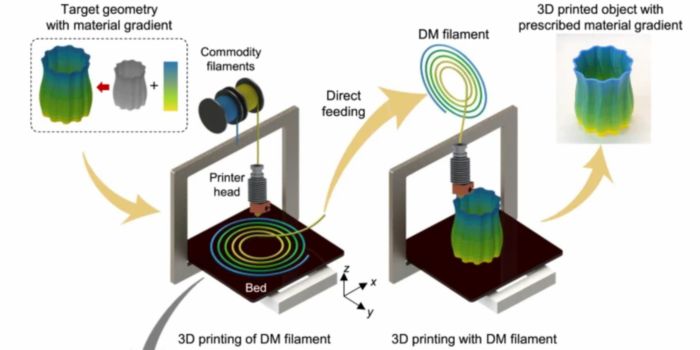
The b-FDM printing process.
The filament was printed with a layer thickness of 125 μm and consists of 14 layers of extruded material. Each layer includes two to four 3D printing lines, each 440 μm wide. During the printing process, the raw material was changed manually, allowing different properties such as color, strength, conductivity, and stretchability to be combined. The filaments were printed into several test parts using the original Prusa i3 MK3S from Prusa Research, with good adhesion achieved by heating the 3D printing bed to 70°C. The researchers combined conductive, brittle PLA (CPLA) with soft, flexible polyurethane (TPU), resulting in conductive parts with potential applications in wearable electronics and sensors. The filament is also designed to have a standard diameter of 1.75 mm, making it compatible with any FDM printer.
To demonstrate the technology, the researchers printed a multifunctional origami gripper with rigid facets, flexible hinges, electrical circuits, and sensors using a simple FDM printer and a single filament. This illustrates that their innovative approach can be easily applied to standard printers.
The technology is cost-effective and accessible, as it can be implemented with conventional FDM printers and requires only a few common filaments. It also unlocks the full potential of FDM printing for various technical applications. The researchers view these results as a significant enhancement to existing FDM 3D printers and an opportunity to push the boundaries of current 3D printing capabilities. To learn more about this project, click here.
What do you think of b-FDM printing? Let us know in a comment below or on our LinkedIn, Facebook, and Twitter pages! Don’t forget to sign up for our free weekly newsletter here for the latest 3D printing news straight to your inbox! You can also find all our videos on our YouTube channel.
*All Photo Credits: Nature Communications and Seoul National University