How to adopt metal additive manufacturing: Experts give their advice!
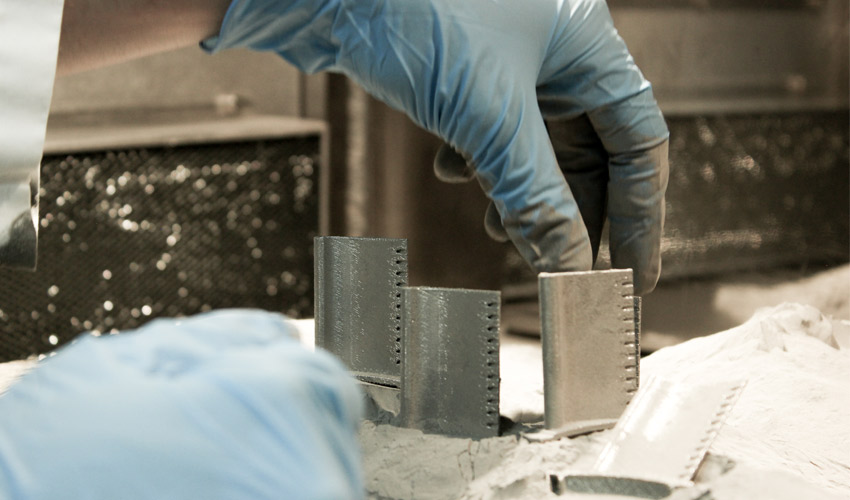
While metal additive manufacturing technology has been maturing over the years, experiencing greater growth in comparison to plastic printing processes, one question seems to persist in the market: how can you successfully integrate metal additive manufacturing into your business? Metal 3D printing remains a heavy investment with higher machine and material costs than other technologies on the market. Moreover, for mass production it struggles to compete with other more traditional manufacturing techniques such as machining. Today, metal additive manufacturing is predominantly used to make functional prototypes, tooling components, spare parts or even to repair defective parts, nevertheless some sectors are starting to design end-use parts for series production. How can you be sure of the solution you choose and how can you integrate it efficiently into your production processes? We interviewed three experts to give you practical advice!
Bernd Martiné has been Expert for Advanced Manufacturing Technologies at GF Machining Solutions since 2013, and responsible for sales and applications of additive manufacturing in Germany. Today, he manages various industrial sectors that have invested in metal solutions, be it for tooling or the production of end-use parts. Our second expert is Benny Buller, CEO and founder of VELO3D, the pioneer of the support-less process for metal AM. Last but not least, Dr. Johannes Gumpinger is Advanced Manufacturing Process Engineer at the European Space Agency (ESA). He develops solutions to apply additive manufacturing as a standard design process for space missions.
- Bernd Martiné
- Benny Buller
- Johannes Gumpinger
Why consider investing in metal additive manufacturing?
Metal 3D printing technologies offer more complexity and geometrical freedom than traditional machining methods while also optimizing the total weight of the part thanks to adapted software, which allows using the necessary material only. ESA, which has been using metal additive manufacturing for more than 10 years, developed an interest in R&D, seeking to understand how to further develop the characterization of materials and the resistance of parts. Today, Dr. Johannes Gumpinger explains: “The high geometrical freedom can effectively be used for developing parts with increased performance, reduced mass, but also lower costs.”
This is an opinion shared by Bernd Martiné of GF Machining Solutions. He explains that companies will consider metal additive manufacturing when they cannot produce their parts using conventional processes, especially when it comes to reducing the complexity/weight ratio. “In some companies, I have seen the management investing in such AM machines without having any dedicated parts, just to force their people to think about new designs and to not miss a trend.”
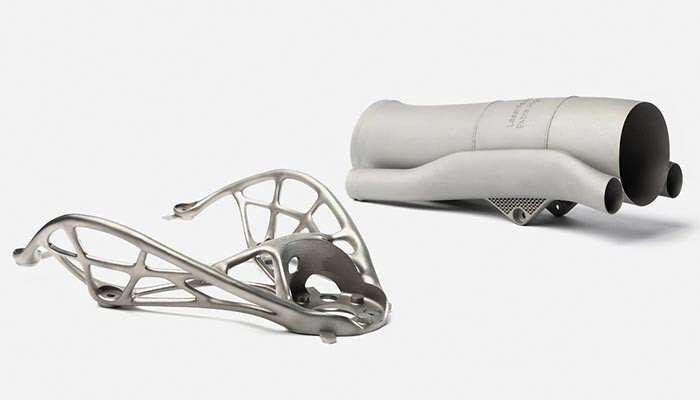
3D printed pieces by GF Machining Solutions
Benny Buller adds that a company needs to consider 3D technologies when looking to improve product performance and/or when faced with an uncertain supply chain. Additive manufacturing can then help reduce inventory by designing parts on demand. He adds: “Companies that have medium/low volume circulation of spare parts that suffer from supply chain uncertainty, quality and price challenges are the most ideal candidates for AM adoption.”
How to choose the right metal additive manufacturing solution
There are many metal 3D printing processes out there: Laser Powder Bed Fusion, Directed Energy Deposition, process inspired by MIM (for Metal Injection Molding), cold spray, etc., which does not make the choice of a machine easy. Benny Buller advises to start with a service provider and test the different metal additive manufacturing techniques available: “Use contract manufacturers or service bureaus to make the first few steps, consider internal deployment only after successfully implemented first few wins.”
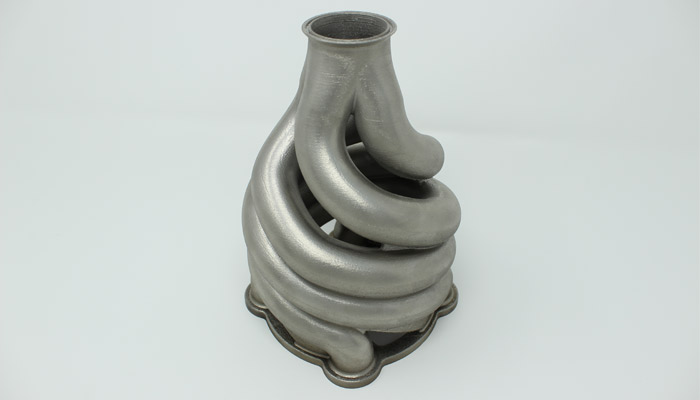
Velo3D’s technology enables to print complex parts without supports | Credits: Velo3D
The choice of solution will of course depend on what you want to produce and the material you want to use. At ESA, Johannes Gumpinger explains that they quickly turned to “machines which can repeatedly and economically produce parts with high mechanical and physical properties.” Space applications typically require light alloys, nickel-based superalloys, copper alloys and steels. On the materials side, the number of metals for additive manufacturing continues to grow and some processes will be better suited to handle all of them, such as powder bed technology. Bernd Martiné adds: “There is still room for new developments in terms of materials and the machine, but for most industries, our company is already able to offer an alternative to their standard materials.”
Successfully integrating metal additive manufacturing
The first thing to consider when you want to integrate a 3D printer into your production line is to identify the type of parts you want to design and what you want to do with them: do you want to create prototypes to speed up product development? Tooling to reduce costs? Or end-use parts to be more innovative and efficient? One thing to always keep in mind is that metal additive manufacturing is not necessarily the right solution, which is why it is essential to know in which direction you want to go. Bernd Martiné adds: “We suggest that companies should not try to produce parts using AM that can already be made using conventional, existing technologies, as AM is more expensive in most cases. Instead, think about the limits of the existing technologies. Where could we add functions, and how can we reduce complexity.”
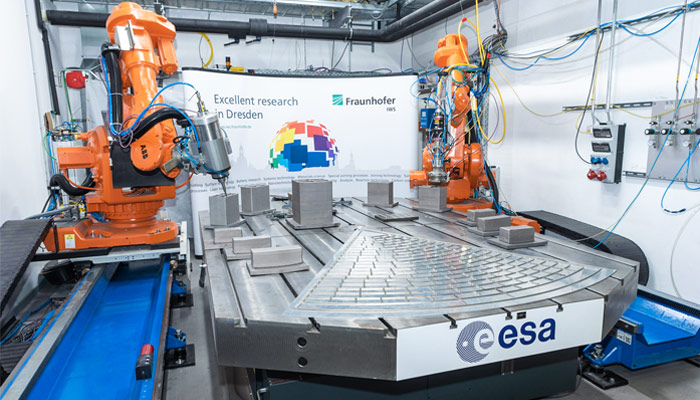
As part of the Athena mission, ESA worked with the Fraunhofer Institute to 3D print a titanium optical bench | Credits: Fraunhofer IWS
Training is also a key component for successful integration. Employees must be trained in the use of the machine, the software, but also in post-processing techniques and reminded of safety rules. You don’t handle an industrial machine in the same way as a desktop 3D printer, or metal powders like plastic filament spools. There are certain risks to be taken into consideration and it is crucial to make them known to all users of the machine. Typically, GF Machining Solutions has set up “Centers of Competence” in Europe, Asia and the United States to provide the right training for equipment. Bernd Martiné explains that they have developed workshops for “customers who are still planning an investment. We are able to offer workshops to give them a detailed overview of this technology.” Even as a user, it is important to keep up with the latest market developments and emerging technologies. Johannes Gumpinger explains that at ESA, employees “attend conferences and training courses, conduct and publish research, but also organize conferences and workshops ourselves.”
Finally, good integration starts at the design stage and not at the manufacturing stage: you have to “Think Additive,” as Bernd explains. Successful integration involves various learning phases, so it is necessary to start gradually, to test several things before going into production. Benny Buller concludes: “Start with 3D printing of existing parts without redesign to understand if the technology process is dependable. Spare parts that are already in serial production is an ideal place to start with AM.”
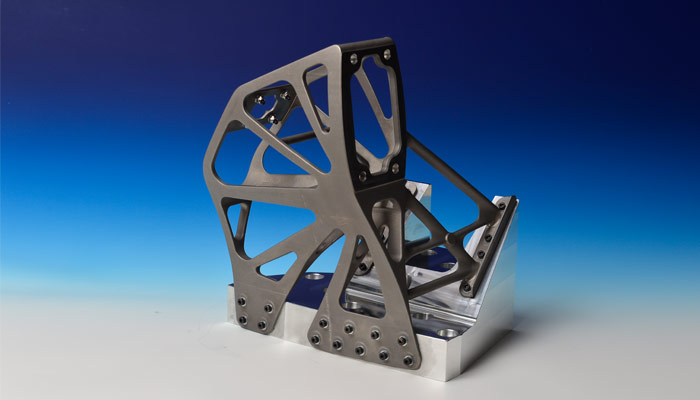
3D printed Ariane launcher support Credits: ESA
You can find more information on the metal additive manufacturing solutions offered by GF Machining Solutions HERE and Velo3D HERE.
*Cover Image Credits: Velo3D
Was this expert advice useful? Let us know in a comment below or on our Facebook and Twitter pages! Sign up for our free weekly Newsletter, all the latest news in 3D printing straight to your inbox!