Additive Manufacturing vs. Injection Molding: Which Manufacturing Process to Choose?
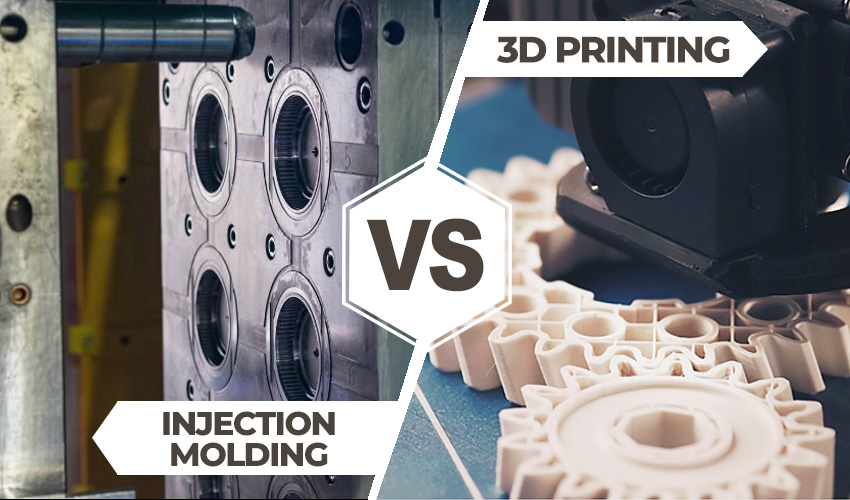
In modern manufacturing, a variety of production technologies cater to different requirements. And two of the most popular are undoubtedly injection molding and additive manufacturing. Both processes offer unique advantages and can complement each other. To gain a deeper understanding, we decided to take a closer look at the two different technologies to compare and contrast them, focusing on fundamental principles, distinguishing features, applications, manufacturers, and costs.
Before delving into each of these technologies, it is useful to trace their historical origins. Injection molding dates back to the 1860s when John Wesley Hyatt invented celluloid, an early plastic material. Hyatt and his brother Isaiah later patented the first injection molding system, which used a piston to force molten celluloid into a mold. Throughout the 20th century, the technology advanced significantly, notably with James Watson Hendry’s invention of the rotary screw injection molding machine in 1946, which remains the standard in injection molding today.
Additive manufacturing has its origins in the 1980s. The first 3D printing systems were based on the stereolithography technique, developed by Chuck Hull and commercially patented in 1986. In the decades that followed, additive manufacturing grew with the development of new processes that have allowed for expanded material options, thus offering solutions for different practices. Now, additive manufacturing has gained ground and has become extremely attractive for different industries.
Manufacturing Process
What Is Additive Manufacturing?
Additive manufacturing is a production process that creates objects by adding material layer by layer from a digital design. This method offers great flexibility and precision, allowing the creation of complex geometries that would be difficult or impossible to realize with traditional manufacturing methods, including injection molding. Additive manufacturing encompasses various families of technologies, each differing in the materials used, energy sources, and methods of material addition.
Broadly, these technologies can be classified into seven major families: extrusion, vat photopolymerization, binder jetting, material jetting, powder bed fusion (both metal and polymer), directed energy deposition and sheet lamination (although this is less widespread). Each family includes specific variants that require unique equipment, utilize different materials and yield distinct results. Despite these differences, all additive manufacturing technologies follow defined steps to produce the final part.
In additive manufacturing, the process starts with the creation of a 3D design using computer-aided design (CAD) software. Once the design is completed, it is converted into a digital file. The digital model is exported to a format compatible with the 3D printer, such as STL, OBJ or 3MF. Then, the file is loaded into slicing software, which converts the model into horizontal layers and generates the G-code. The actual fabrication will then depend on the printing technology used. Once the printing is complete, the object may or may not require post-treatment, which may be the removal of supports, sanding, or curing in the case of resins or heat treatments when working with metals or polymers.
What Is Injection Molding?
As the name suggests, the injection molding process involves injecting molten material into a mold, where it cools and solidifies to create the final part. The process starts with selecting and preparing the material, which can be in the form of pellets, powder, or preforms. While plastics are the most common materials used, metals and glass can also be utilized in this process, which we will delve into further when discussing compatible materials later on. Once the material is prepared, it is loaded into a feed hopper similar to material extrusion systems in additive manufacturing and then conveyed to a barrel.
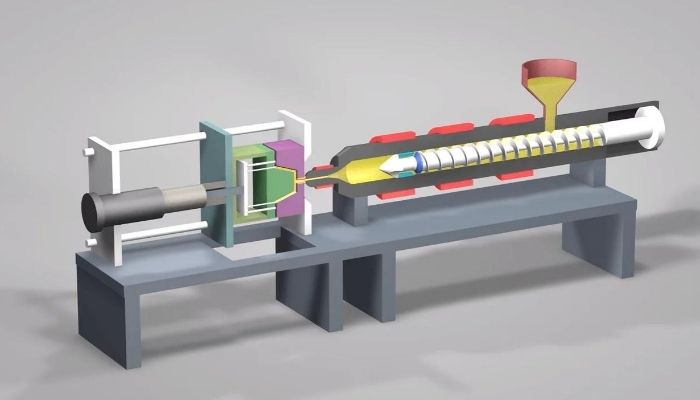
Anatomy of an Injection Molding Machine (Photo Credits: 3ERP)
Inside the barrel is a high-temperature screw that rotates and pushes the material while heating it. This heat melts the material, making it viscous and fluid. It should be noted that the temperature at this stage can reach up to 200ºC. Once the material has melted, the screw moves forward, injecting it at high pressure through a nozzle system, similar to an extruder, into the mold cavity. The injection time can be very short, usually between 0.1 and 2 seconds. Once the plastic is injected into the mold, it begins to cool and solidify almost immediately due to the lower mold temperature. In addition, the mold has breathers that help maintain a constant temperature and speed up the cooling process.
When the material has solidified, the clamping unit, which can be a hydraulic or electric press, releases the pressure, causing the mold to open and release the part. Finally, the mold closes, and the injection cycle is repeated to produce the next part. It is important to note that although there are different types of molds, such as multi-cavity, double-shot, or mixed-cast molds, they are made up of the same basic structure to comply with the described mechanics. Post-processing of molded parts consists of burr trimming, painting, surface treatment, or assembly. Printed parts themselves also undergo these post-treatment steps, although assembly, for example, is sometimes not necessary in 3D printing because end-use parts can be printed all-in-one.
Materials
Both additive manufacturing and injection molding employ a diverse range of materials suited to various applications and industries. In FDM 3D printing, for example, thermoplastics such as PETG, PLA, and ABS dominate due to their ease of melting and extrusion, making them ideal for recreational and industrial 3D printing. However, AM is not limited to these materials. It also utilizes thermosets, elastomers, and engineered resins such as nylon and polycarbonate, commonly used in SLS (Selective Laser Sintering).
Additionally, AM can handle metals (like titanium and aluminum) and ceramics, broadening its application spectrum (for metals – DMLS/SLM, EBM, binder jetting; for ceramics – binder jetting, material jetting, and PBF). Despite this broad material range, materials often must be certified to ensure quality and performance, especially in regulated industries like the aerospace and automotive sectors. Though this certification process can add to the time and cost, the use of pellets in AM can simplify this process since they are already used in more traditional technologies like injection molding.
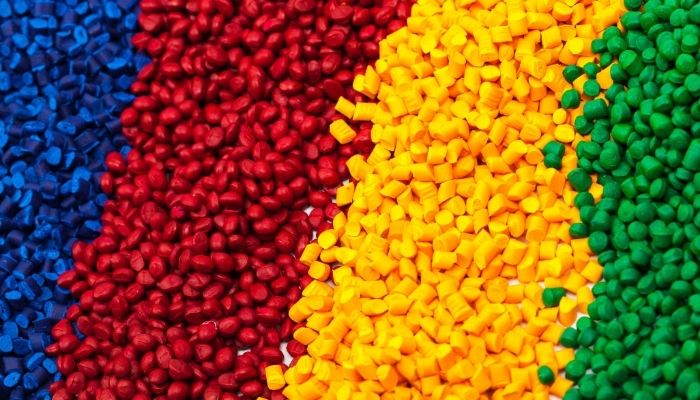
The material of choice in injection molding continues to be plastic.
Like AM, injection molding also accommodates a wide array of materials, sharing much of the same material usability (thermoplastics, thermosets, elastomers, metals, and engineered resins like nylon and polycarbonate). This versatility enables the production of durable automotive components, medical-grade silicone implants, and other high-performance parts. Injection molding’s capability to process dense materials makes it highly beneficial for producing parts requiring high structural integrity and dimensional accuracy.
Post-Processing for Additive Manufacturing and Injection Molding
Finishing and post-processing are essential to enhance the functional and aesthetic properties of parts manufactured through AM and Injection Molding. In AM, achieving a smooth surface finish often necessitates post-processing techniques such as sanding, polishing, or chemical treatments due to the rough textures and visible layer lines that result from the printing process. For many 3D printing technologies, particularly FDM, SLA, DLP, and material jetting, support removal is another critical step in AM post-processing, especially for designs with complex geometries or overhangs.
Overall, these techniques are crucial for refining surface texture, improving part durability, and ensuring dimensional accuracy, which is crucial for applications that demand high-quality aesthetics or functional surfaces. Though, each post-processing technique is highly dependent on the 3D printing technology initially used.
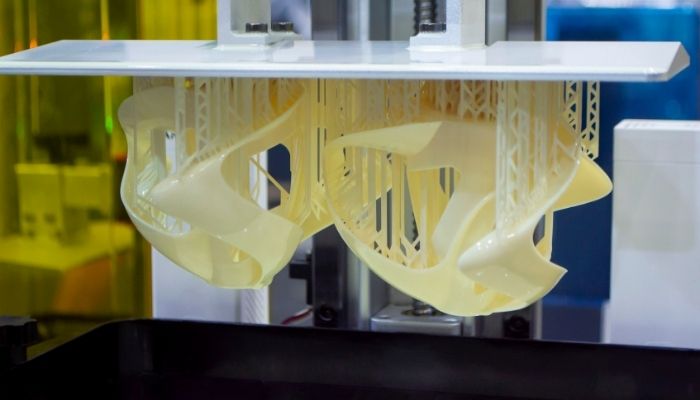
Resin 3D printed parts require some post-processing to remove supports and excess resin.
In injection molding, post-processing is generally much less extensive compared to AM due to the high-quality finish that molds can transfer to the parts. However, several steps are sometimes necessary to ensure the final product meets the desired specifications. One of the most common post-processing steps is the removal of flash, which is the excess material that can seep out of the mold cavity during the injection process. Like the removal of support structures in 3D printing, flash removal is typically done using trimming or cutting tools, although, in high-volume production, automated systems are often used to speed up this process.
Applications for Additive Manufacturing and Injection Molding
Both processes are used extensively across a wide range of industries, each leveraging unique strengths to meet specific manufacturing challenges, needs, and opportunities. AM excels in industries requiring customization and complex geometries, such as medical, aerospace, automotive, and consumer goods. AM’s agility in prototyping and customization can be seen easily within the medical field, where personalized implants and prosthetics are tailored to individual patient anatomy, enhancing treatment outcomes and patient comfort.
Similarly, the use of AM is significant in aerospace, with specific applications emerging in hypersonic missiles, rocket engines, and stand-alone 3D printers for increased self-autonomy throughout space missions. Aerospace engineers leverage AM’s ability to produce lightweight yet durable parts with intricate designs, as these components contribute significantly to improved performance, whether by reducing overall weight or optimizing complex geometries that traditional manufacturing methods struggle to achieve. Additionally, automotive manufacturers also leverage AM, using the different technologies for rapid prototyping and design iteration, tooling, and manufacturing of lightweight parts. This allows for quick, affordable part alterations and enhanced customization.
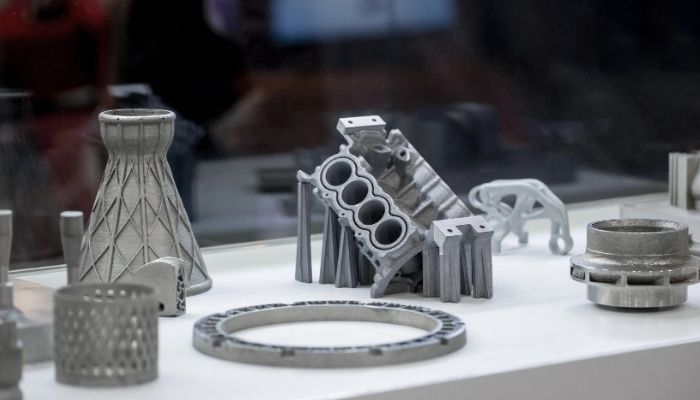
3D printing to produce parts with intricate designs.
Though there is considerable overlap in the sectors that use this technology, injection molding, on the other hand, serves a distinct role in industries requiring high-volume production and precise, consistent part quality. Like AM, it is highly prevalent in automotive, consumer goods, and medical device manufacturing, but for fundamentally different reasons.
Injection molding is favored for its ability to efficiently produce standardized parts with excellent surface finish and dimensional accuracy. Specifically, automotive applications rely on injection molding to produce large volumes of components like bumpers, handles, dashboards, and exterior body panels, ensuring uniformity and meeting stringent industry standards. In consumer goods, injection molding is instrumental in manufacturing plastic containers, packaging, electronic enclosures, and toys at scale, maintaining product consistency while allowing for mass production.
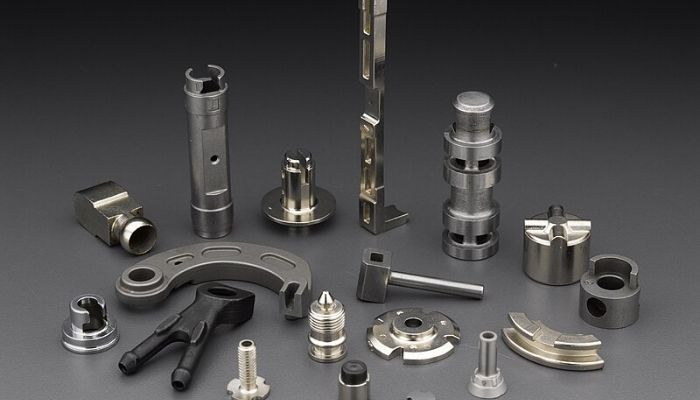
Parts manufactured by Metal Injection Molding (MIM)
Similarly to AM, the medical sector also benefits significantly from injection molding, but particularly in producing medical devices such as syringes, catheters, and surgical instruments. Injection molding is particularly advantageous here, as it allows healthcare professionals to use devices that meet strict regulatory requirements for biocompatibility and dimensional precision.
Benefits and Limitations
Injection molding is hailed for its efficiency and cost-effectiveness in high-volume production, making it a cornerstone of high-output manufacturing across various industries. The primary advantage of injection molding is its ability to produce large volumes of identical parts with minimal material wastage. Once molds are created, the production process is rapid, with each cycle producing a fully formed part, making it ideal for mass production in consumer goods and electronics sectors. This efficiency translates into significant cost savings per unit as production scales up, making the initial setup expense worthwhile for many companies. Injection molding becomes incredibly profitable for large series production, often more than additive manufacturing.
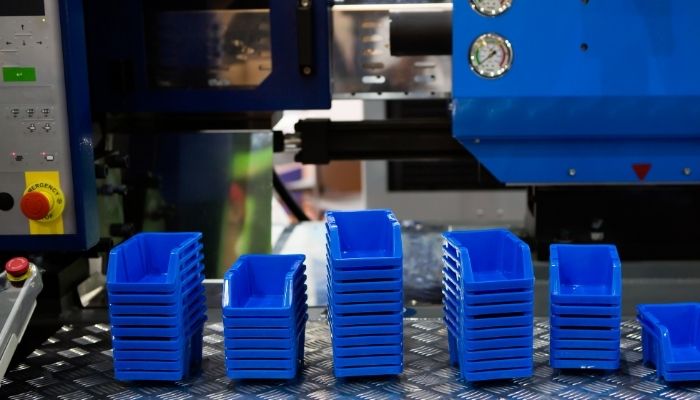
The main advantage of injection molding compared to additive manufacturing is the production of large volumes of identical parts.
However, injection molding faces significant challenges, notably in setup time and initial investment. Designing and fabricating molds can be time-consuming, typically ranging from several weeks to months, depending on the part’s complexity. This long lead time makes injection molding less flexible for quick design alterations than 3D printing. The high upfront costs associated with mold creation, machine acquisition, and material procurement can restrict entry into the market for many smaller enterprises and startups.
Design constraints also play a crucial role, as intricate geometries and internal features can be challenging to mold without compromising part integrity or significantly increasing costs or production time to design a new mold. Additionally, sprues, the point at which molten material enters the mold, must be designed and precisely calibrated to ensure the material flows evenly into the mold, preventing warping and premature cooling. Despite these hurdles, once the initial investment in mold creation is overcome, the price per part drops considerably as production ramps up.
On the other hand, AM requires minimal setup time compared to injection molding, making it incredibly useful for rapid prototyping and on-demand production. This quick setup is particularly advantageous for companies in fast-paced industries like aerospace and automotive, which benefit from fast iterations and reduced lead times, allowing for significant cost savings.
When design modifications are necessary, such as in rapid prototyping, AM enables quick and cost-effective adjustments, whereas injection molding demands costly replacements or changes to the mold. Furthermore, AM holds a distinctive advantage over injection molding in terms of sustainability, as it drastically reduces material waste in most cases. The additive nature of the process means material is deposited only where needed, minimizing scrap. While injection molding is relatively sustainable compared to traditional methods, AM excels by producing no waste from misaligned sprues or overflow material.
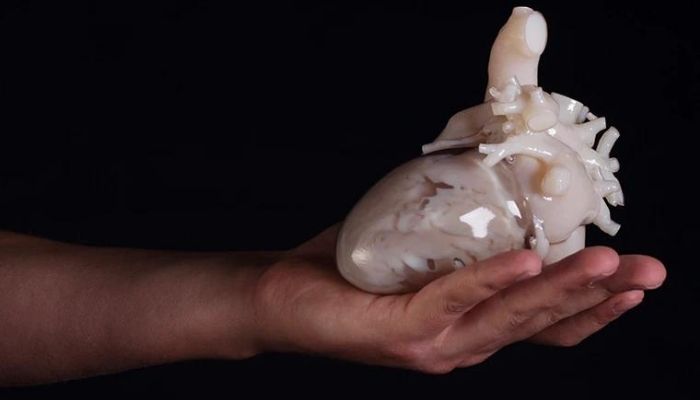
Photo Credits: Materialise
However, this is not to say that AM doesn’t present its fair share of challenges. While the initial setup is quick, the actual production speed of 3D printing is typically much slower than that of injection molding for high-volume output. Additionally, despite continuous advancements within the industry, the surface finish of 3D printed parts often requires extensive post-processing to achieve the desired smoothness or aesthetic quality, a limitation typically not experienced by injection molding (though some technologies like material jetting, for instance, are not bound by this limitation). This adds time and cost to the production process, particularly for parts requiring a high-quality finish.
Furthermore, the entry price for AM can vary significantly depending on the sector it is used in, determining whether it is a low or high-cost option. While AM presents a reliable and generally affordable manufacturing option with unmatched design flexibility, it is typically not suited to be the economical choice for mass-producing simple, uniform components.
Production Time of Additive Manufacturing vs. Injection Molding
Although the exact timing of each step cannot be given, there are determining factors. For example, in the case of injection molding, mold preparation can be time-consuming, as it involves the design, fabrication, and machining of the mold. This is because the mold design not only considers the structure of the part but also the whole mechanism surrounding the mold, the cooling system, the breathers, the injection channel, etc. In the case of parts for printing, the design time is focused exclusively on the part and, of course, on the supports. In both cases the design time varies according to the complexity of the parts and the modifications to achieve the desired result.
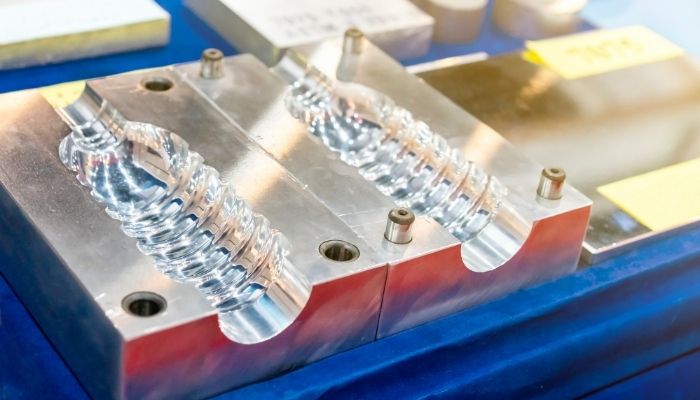
Example of a mold for the production of plastic bottles.
When it comes to production times, additive manufacturing durations vary based on factors such as part geometry, print resolution, chosen materials, and the specific technology employed. Small, straightforward parts can be printed in a matter of minutes, whereas larger and more complex components may necessitate hours or even days. In contrast, injection molding excels in manufacturing speed due to its precision and repetitive material injection process. Machines are calibrated to inject material with high accuracy, enabling the production of large volumes of parts in seconds.
Price Comparing Additive Manufacturing and Injection Molding
Another key point is the cost of production. The initial investment for industrial injection molding equipment can range from $50,000 to over $200,000, depending on the size, capacity, and technical features of the machine. With the rise of desktop 3D printers, the injection molding industry also started to propose solutions for smaller-scale production following this technology. Although industrial 3D printers can also approach the prices of injection molding machinery, one of the main differences between the two processes is that in additive manufacturing, there is no investment in molds. Indeed, molds are one of the most expensive components, especially when they are very complex. Molds can cost up to $100,000, but in the long run, the price of the parts is low.
Another investment is software. Both processes require software for both design and process monitoring. Since the investment for both processes is unique, there are online calculators that serve as a benchmark for manufacturing calculations, in addition to professional estimating services. Some examples of calculators for injection molding are Hubs, ICOMold, or CustomPart; for additive manufacturing, we will find solutions such as AMOTool or ShatterBox. In both cases, it is important to keep in mind that there are also installation costs and time to market involving investments, maintenance, labor, and materials.
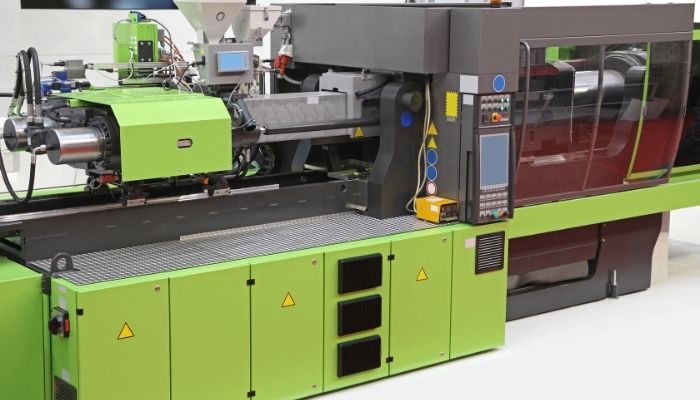
Injection molding is ideal for large quantities of identical parts.
While additive manufacturing has traditionally been favored for low-volume projects, custom parts, and rapid prototyping, its role is rapidly evolving. Evidence of this shift can be found in a recent report by Protolabs on market trends, which underscores a growing trend: professionals increasingly turning to additive manufacturing for producing high-volume parts that were traditionally made using technologies like injection molding. This indicates a significant potential for additive manufacturing to expand its application into broader industrial and manufacturing sectors previously dominated by conventional manufacturing methods.
What do you think of this comparison of additive manufacturing vs. injection molding? Let us know in a comment below or on our LinkedIn, Facebook, and Twitter pages! Don’t forget to sign up for our free weekly newsletter here for the latest 3D printing news straight to your inbox! You can also find all our videos on our YouTube channel.
This was a very informative article. It helped me understand the differences between additive manufacturing and injection molding, As a consumer, I’m excited about the potential for customized products made through additive manufacturing