#3DStartup: Addiguru and its real-time monitoring software for 3D printing
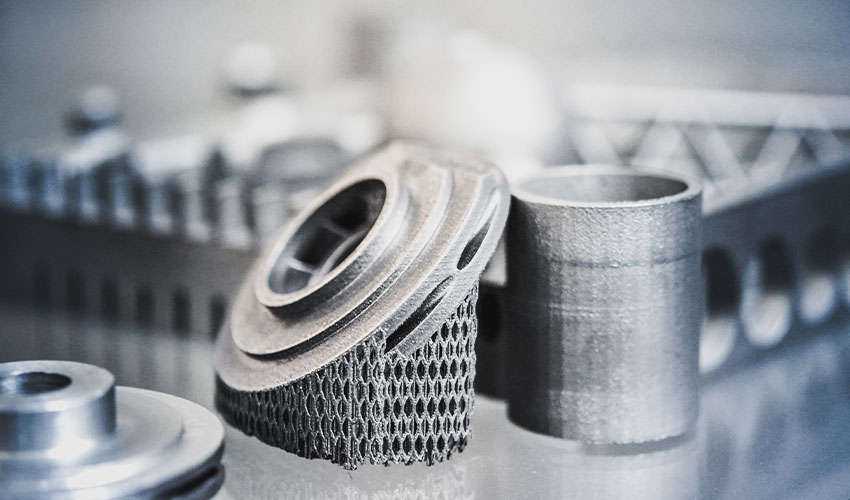
In the additive manufacturing market, the user is not immune to potential manufacturing defects, not only wasting time and money, but also sacrificing quality. In order to limit these defects as much as possible as well as automate the production process, the startup Addiguru has developed a software solution to monitor the manufacturing process in real time. For the moment reserved for Laser Powder Bed Fusion, this solution is expected to be extended to other 3D printing methods such as FDM or DED. We met with Shuchi Khurana, Addiguru’s CEO, to learn more about the software, its functionalities but also about the startup’s future projects.
3DN: Can you introduce yourself and tell us about your relationship to 3D printing?
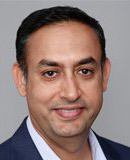
Shuchi Khurana
I have a Masters in Materials Engineering and my technical expertise in predictive analysis of welding and joining processes, which are the underlying processes for 3D-Printing. I have used 3D-Printing for prototype parts for the medical device that we created for my previous start-up company and it was very valuable for us to quickly create prototypes using 3D Printing. For last 12 years, I have developed and launched many products. Recently, one of them was a predictive maintenance software for a large global manufacturing company.
3DN: How did the idea to create ADDIGURU come up? Can you tell us how your monitoring technology works?
Additive Manufacturing is a layer by layer process and each layer provides us with an end point to observe and determine quality. I have a lot of experience with predictive analysis for manufacturing processes and I realized that most people are trying to detect the quality by continuous monitoring and the focus was on the melt pool. Melt pool is difficult to monitor due to the very fast movement of laser and the huge amount of data generated. Layer by layer monitoring is more practical and affordable for the industry. I saw the opportunity to help the industry with my past experience of predictive analysis and launching products. So I decided to start Addiguru in September 2019. As you can tell in the name – ‘Addi’ comes from Additive Manufacturing and ‘guru’ comes from the fact that we are creating an intelligent software that will guide 3D printing processes like a Guru does.
3DN: Which brands and AM technologies can implement ADDIGURU’s monitoring system?
Addiguru’s vision is to create a platform for monitoring all Additive Manufacturing technologies. We have started with Laser Powder Bed Fusion process and the software has been designed to easily add other processes to the mix. We are currently working towards adding FDM process. DED process will be added in the next few months as well. Addiguru’s software is machine brand agnostic as well as sensor brand agnostic.
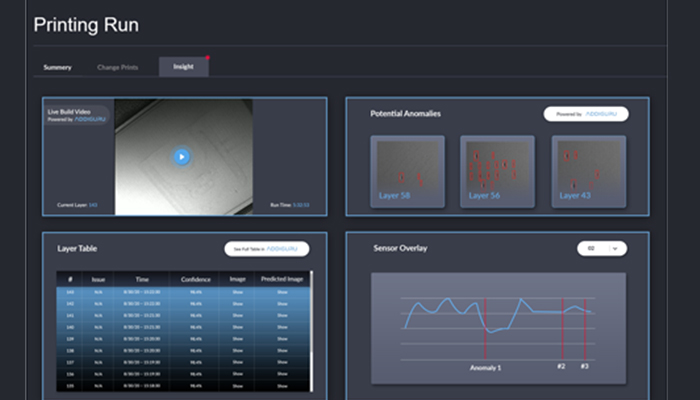
Addiguru’s platform
3DN: In your opinion, why is it important nowadays to implement an AM monitoring system? How can it help to improve productivity?
AM process is dependent on many factors and sometimes even slight variation in a process parameter may result in a defective part. It is very easy for an operator to miss a slight variation that could lead to an internal defect. A real-time monitoring system will provide a lot of confidence in the quality of the parts produced. This will help reduce the reliance on Non-destructive Testing at the end of the part build process which will help accelerate adoption of AM. In metal AM processes, especially DMLS processes, the defect rate is very high and each part can be very expensive to produce. By our calculations, on average, a real-time monitoring solution for a DMLS process that can provide notifications when an anomaly occurs, then it can help save about $160,000 per year per machine. Most people will argue that this number is on the lower side and they can get even higher value. For polymer part production, the savings will be lower but still significant savings will be possible with a real-time monitoring system.
3DN: Can you tell us what sectors you’re targeting? Can you share some of your current clients with us?
Currently, we have a beta version of our software for LPBF process and it is deployed in four locations, including service bureaus and a research institution. The part makers are focused on Aerospace industry and tool making industry. We are currently in talks with adding more installs including an install at a company with focus on medical implants. We are adding FDM process to our software and it is expected to be in beta launch by end of 2020. DED process will be added in Q1 2021.
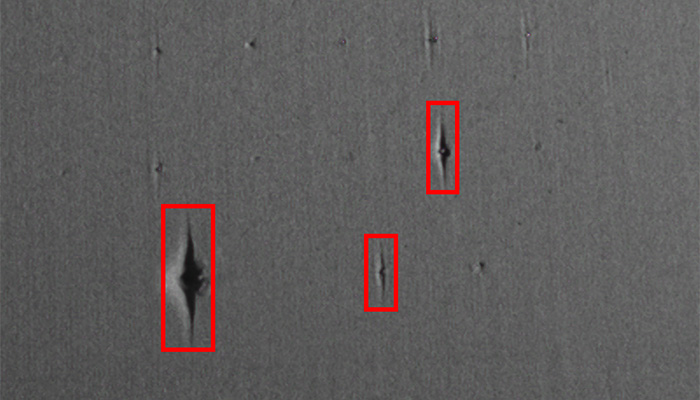
Anomalies detected in the laser fusion process by Addiguru’s artificial intelligence algorithms are indicated by red boxes.
3DN: Where do you see ADDIGURU in 5 years?
As mentioned earlier, Addiguru’s vision is to create a platform technology which is machine, sensor and process agnostic. We envision that in a few years we will have a robust software that is widely used and beneficial. The data will be such that the digital twin of the final part produced will be available from Addiguru’s software. The software will be embedded in the machines and sold as add-on with the OEM’s machines. Addiguru’s data and user interface will be available directly from Addiguru as well as integrated with the MES softwares available in this space.
3DN: Do you have any last words for our readers?
AM is an exciting technology and growing rapidly. Real-time monitoring can save a lot of time, money and headaches for the part makers. I will encourage people in the industry to evaluate the benefits they can get from real-time monitoring and look for an appropriate tool. Also, researchers and engineers working on real-time monitoring technology need to hear from the users about their needs to provide solutions that are helpful. So please be vocal about your pain points.
Another thought is that all AM industry experts agree that a monitoring system will greatly benefit the users and the industry. However, no good quantitative studies are done on advantages of a real-time monitoring system for AM processes. I encourage engineering and business school communities to come together for such research. If you want to learn more about Addiguru, you can check out the website HERE.
What do you think about Addiguru’s solution? Let us know in a comment below or on our Linkedin, Facebook and Twitter pages! Sign up for our free weekly Newsletter here, the latest 3D printing news straight to your inbox!