A Complete Guide to Zero Gravity 3D Printing
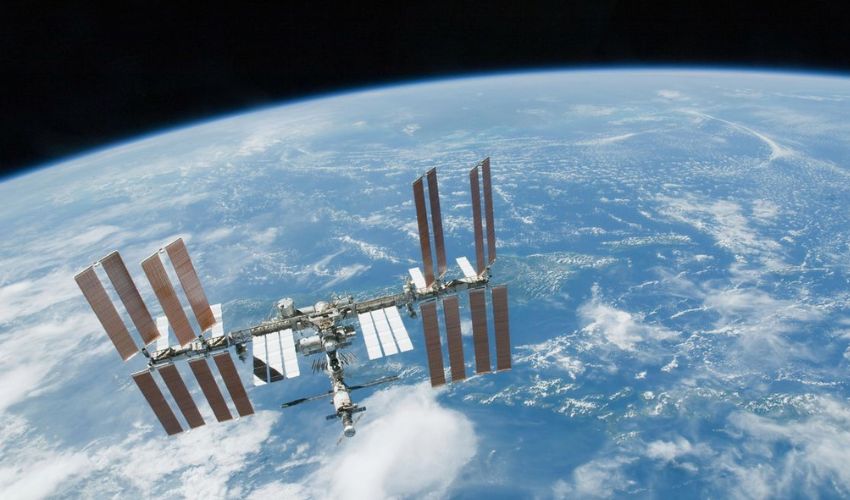
Since the early days of space exploration, curiosity about the universe has been a driving force behind innovation and technological progress. Institutions like NASA and private enterprises such as SpaceX and Relativity Space have advanced missions that push the boundaries of our understanding of space. At the forefront of this pursuit lies zero gravity 3D printing, a technology that has the potential to significantly improve terrestrial manufacturing and is expected to redefine operations in the realm of space.
Zero gravity, or microgravity, 3D printing refers to the process of additive manufacturing in the unique environment of space where the effects of gravity are minimal. This approach, which was only theoretical before the first 3D printer was sent to space in 2014, allows for the production of tools, parts, and even entire structures directly in orbit, reducing the need for costly and logistically complex resupply missions from Earth. Unlike traditional 3D printing, which relies on gravity to hold materials in place, zero gravity 3D printing must adapt to the unique challenges of a weightless environment.
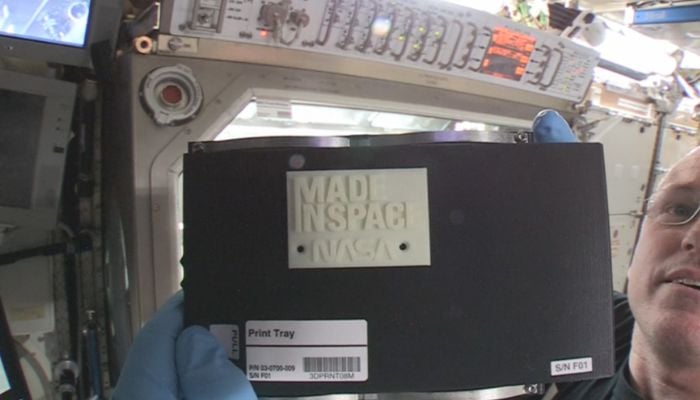
The first-ever part 3D printed in space (photo credits: NASA)
As 3D printing in space continues to advance, this method is increasingly being seen as a compelling solution for long-duration space missions where carrying spare parts and tools for every potential need is impractical. But how does it work? What challenges are we still facing when it comes to zero-gravity 3D printing? We took a closer look.
The Start of Zero-Gravity 3D Printing
To understand zero-gravity 3D printing, first we need to understand its history. And the journey of zero gravity 3D printing began with early experiments conducted by NASA and its commercial partners as they worked to explore the role of 3D printing in space. One of the first significant milestones was achieved in 2014 when Made In Space successfully installed and operated the first 3D printer aboard the International Space Station. This printer used fused filament fabrication (FFF) technology to produce various tools and parts.
Since then, numerous advancements have been made, including the development of metal 3D printing capabilities by the European Space Agency (ESA) and other organizations as well as research into bioprinting in zero gravity. Several significant milestones achieved this year alone include UC Berkeley’s SpaceCAL 3D printer successfully printing plastic parts in orbit and the European Space Agency (ESA) successfully completing metal 3D printing aboard the International Space Station, among many others.
What Are the Continuing Challenges?
But just because it has come a long way, does not mean that there are not significant obstacles. In fact, zero gravity affects 3D printing processes in several ways. On Earth, gravity assists in the layering process by keeping the material in place. In space, the absence of gravity means materials must be carefully controlled to prevent them from floating away or deforming. This requires careful consideration of material properties and printer mechanics to ensure that each layer adheres correctly without the assistance of gravity.
Additionally, managing heat dissipation, facilitating extrusion from the printer nozzle, and dealing with more unpredictable behavior of liquids and molten materials in the microgravity environment present challenges. This involves specialized hardware, software adaptations, and unique material formulations to accommodate the conditions of space, which presents an obstacle of its own in terms of costs.
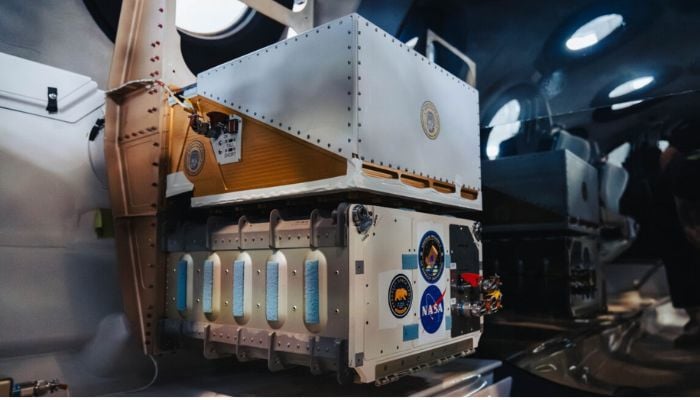
The SpaceCAL Microgravity 3D printer. (Photo Credits: Virgin Galactic)
Additional hurdles include quality control and consistency, as ensuring the structural integrity of printed parts in space is challenging when these parts must meet strict safety and functionality standards for spacecraft use. Resource management is also critical, given the limited supplies of raw materials and energy on space missions. Moreover, the 3D printers themselves must be designed to withstand the harsh conditions of space, including radiation, temperature extremes, and the vacuum environment, while operating reliably over long periods without maintenance or repairs. This requires heavy consideration of transport logistics since every kilogram launched into space significantly adds to the mission’s cost.
It is for that reason that we have seen significant research and development in this field in recent years. There are 3D printers on the ISS and the recently-launched Ariane 6 will also be bringing up additive manufacturing solutions to test results in microgravity. Extensive testing and adaptation in a microgravity environment is expected to help rapidly advance the technology.
Applications and Benefits
Despite these hurdles, zero gravity 3D printing offers transformative potential for space exploration and habitation, which is why its being so heavily researched. One of the most significant applications is the ability to manufacture tools, spare parts, and complex structures directly in orbit. This capability addresses the challenge of transporting every needed item from Earth, which is both costly and time-consuming. For instance, if an essential tool breaks aboard the ISS, astronauts can print a replacement on-demand, ensuring mission continuity without waiting for the next resupply mission. This benefit extends to critical spacecraft components, allowing for immediate repairs and maintenance, resulting in enhanced safety and efficiency of space missions.
Moreover, the use of 3D printing in space opens various new avenues for medical applications in space. Astronauts on long-duration missions face unique health challenges, and having the ability to print medical devices and supplies tailored to their needs can be life-saving. For example, custom splints, casts, and even surgical instruments can be produced on-site. Additionally, there is ongoing research into the feasibility of food 3D printing in space.
Beyond the immediate needs of astronauts, this technology might also pave the way for the future construction of space habitats. Using locally sourced materials, such as regolith on the moon or Mars, 3D printing could enable the construction of various structures, reducing the dependency on Earth for construction materials. Thus enabling more sustainable and longer-term human presence in space.
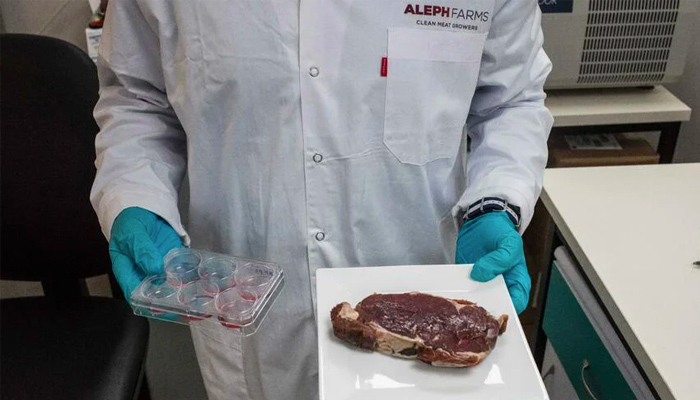
Aleph Farms, which announced in 2019 its project to 3D print meat on board the International Space Station. (Photo Credits: Aleph Farms)
But the benefits of zero gravity 3D printing extend to Earth as well. Research and development conducted in space often lead to technological advancements that can be applied on our planet. The innovations in manufacturing techniques developed for space applications can translate to and enhance industrial processes on Earth, leading to more efficient and cost-effective production methods. Additionally, the experience gained from manufacturing in extreme environments can translate into improved resilience and adaptability in various sectors, such as the automotive, aerospace, and medical industries. Because of this, zero gravity 3D printing not only supports the future of space exploration but drives progress and innovation on Earth as well.
The Future of 3D Printing in Space
Future advancements are likely to focus on expanding the range of materials that can be printed in space, including high-performance metals and composites, enabling the creation of more complex and durable structures and equipment. As technology evolves, we can anticipate the development of larger-scale printers capable of fabricating entire spacecraft components directly in space, significantly reducing the need for Earth-based launches while expanding mission duration. Though some might argue that zero gravity 3D printing may still be too much in its infancy to make these predictions, the potential for zero gravity 3D printing is undoubtedly vast and transformative.
What do you think about zero gravity 3D printing? Let us know in a comment below or on our LinkedIn, Facebook, and Twitter pages! Don’t forget to sign up for our free weekly newsletter here for the latest 3D printing news straight to your inbox! You can also find all our videos on our YouTube channel.