8 Reasons Why Additive Manufacturing Complements Traditional Technologies
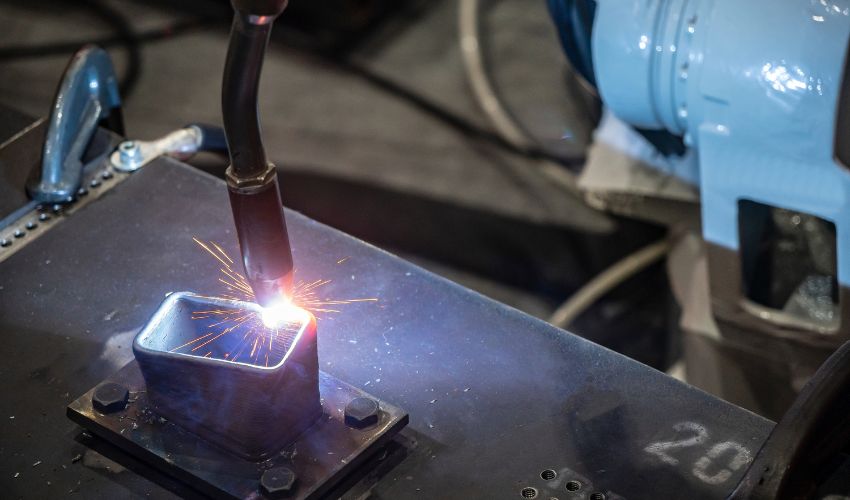
In the world of manufacturing, the integration of new technologies has been a pillar to maintain competitiveness in the increasingly demanding and dynamic global market. The adoption of new tools often seeks to improve efficiency, reduce time and costs, and improve manufactured parts. Additive manufacturing, for example, is being integrated as a transformative technology in industries with an entrenched use of traditional processes. Whether as a complementary tool or integrated into hybrid systems, additive manufacturing is compatible with conventional methods.
Traditional manufacturing remains the method of mass production, however, it faces challenges related to sustainability, flexibility in design and efficiency in the use of materials. Despite this, its ability to produce large volumes at low cost remains unsurpassed in many cases. The need to innovate and adapt to modern demands is driving the adoption of technologies that perfect processes, such as additive manufacturing. Recognizing the importance of getting the best of both worlds, here we explore 8 reasons why additive manufacturing complements other production methods.
1. Rapid Prototyping
Rapid prototyping benefits traditional manufacturing methods on several levels. For one, iterations serve to validate designs before mass-producing final parts. Rapid prototyping is especially useful in industries such as automotive and aerospace for aerodynamic and performance testing. 3D prototypes can be tested in wind tunnels or simulators to evaluate performance before the final part is manufactured using conventional materials and processes. Additionally, 3D prototypes can be used to validate traditional manufacturing tools such as molds for injection molding, patterns for casting, or critical components in machining.
Ultimately, rapid prototyping helps reduce the waste that typically comes from trial and error in traditional manufacturing. By taking advantage of the design flexibility that additive manufacturing offers, resources use can be optimized. This is not the case with subtractive techniques such as machining, for example, where much of the initial material is removed. This approach, combined with the ability to manufacture on demand, eliminates the need for large inventories and minimizes waste associated with overproduction.
2. More Efficient Molds
3D printing can also play a part in traditional manufacturing by creating molds for processes like injection molding. For instance, molds with intricate geometries like cooling channels can be printed, which improves thermal distribution and part cooling time. What’s more is that functional mold models can be created easily and quickly. By comparison, traditional mold-making can take weeks, even months, depending on the complexity of the mold.
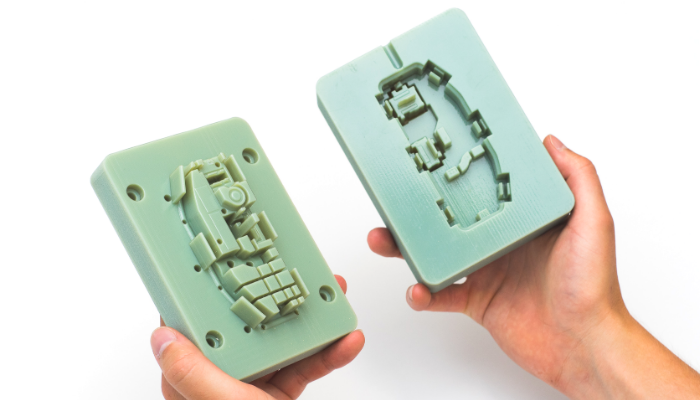
3D printing accelerates and optimizes mold manufacturing for injection molding (Photo Credits: Protolabs Network)
3. 3D Printed Patterns for Lost-Wax Casting
Lost-wax casting is a traditional process in the manufacture of high-precision metal parts. Using 3D printing, patterns can be produced in wax or castable resins with complex and detailed designs that would be difficult to manufacture using conventional methods. Ultimately, this not only reduces production times but also eliminates the need for expensive tooling. In addition, rapid iterations can be made in the pattern design, facilitating adjustments before advancing to the casting stage. This approach combines the flexibility of 3D digital design with the precision of traditional manufacturing.
4. Cutting Tool Optimization
Additive manufacturing can improve final parts, but it can also optimize traditional tools themselves. Milling tools, commonly manufactured with carbide inserts, can wear out quickly due to the heat generated during cutting. In addition, they are difficult to manufacture by machining. Thanks to 3D printing, it is possible to create tools with customized geometries and internal cooling channels that remove heat in the cutting zone, significantly extending tool life and performance.
5. Manufacturing Guides and Accessories
In manufacturing, jigs and fixtures are key tools designed to improve process accuracy, efficiency and repeatability. Thanks to additive manufacturing, it is possible to produce jigs and fixtures faster and customize them to suit specific needs. Examples of such tools are drilling jigs, fixtures for workpiece clamping, welding jigs and dies, etc. It is therefore possible to print a welding jig that ensures accurate positioning of parts in a complex assembly, minimizing human error and maximizing repeatability. This is especially valuable in industries such as automotive or aerospace, where accuracy is critical to product functionality and safety.
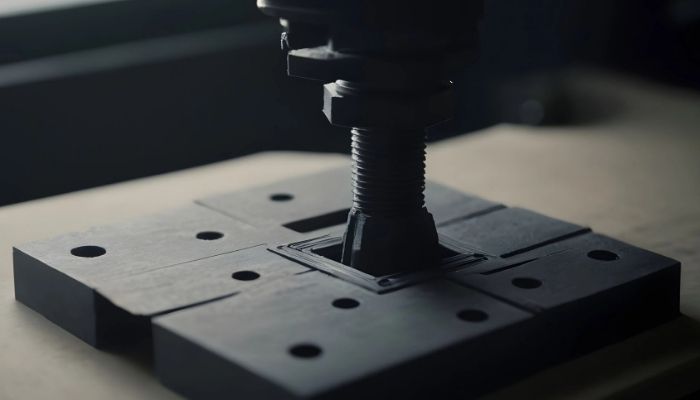
Jigs and fixtures ensure precision in traditional manufacturing (Photo Credits: Parts to go)
6. Combination of Materials
Another reason to integrate additive manufacturing into conventional processes is the ability to use multiple materials in a single part during manufacturing. 3D printing can use advanced materials such as alloys, ceramics or reinforced polymers to create complex internal structures or customized components that would be difficult to realize with traditional methods. On the other hand, traditional manufacturing can work with more resistant materials or materials with specific properties, such as hardened metals, which require subtractive processes for high-quality final finishes.
With hybrid manufacturing, materials can be combined during fabrication, for example, when a product needs heat or tensile strength in one area and not the entire part. By following this procedure, producers can use specific materials for the part that requires it and use more cost-effective materials for the rest without altering the final quality.
7. Repairs and Maintenance
3D printing helps with maintenance and repairs in traditional manufacturing by offering fast and efficient solutions to extend the life of tools and components. With the help of reverse engineering, for example, it is possible to 3D scan parts and then create a CAD model. This model can be modified or replicated to restore discontinued or hard-to-find parts, avoiding long lead times and high costs associated with replacement.
In addition, advanced 3D printing technologies such as direct energy deposition (DED) allow metal components to be repaired by adding material only to the damaged areas, preserving the rest of the structure. This is especially useful in applications where parts are expensive or have long manufacturing times. Over time, this reduces costs and minimizes waste by avoiding premature discarding of tooling or equipment that can be restored to functional condition.
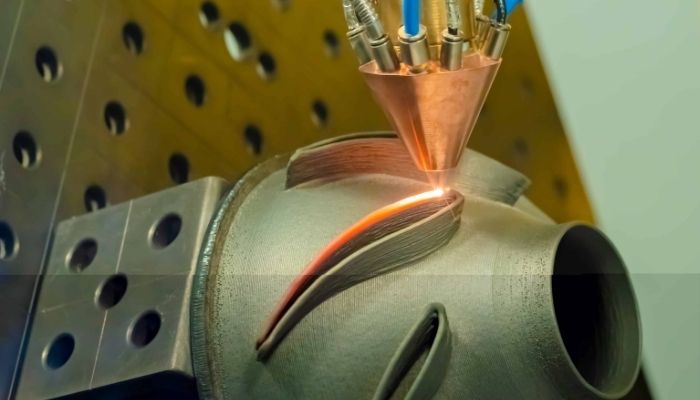
DED technology can apply metal powder or wire only on the parts that need it.
8. Faster Time to Market
Thanks to additive manufacturing’s ability to create rapid prototypes, the technology can bring products to market at a faster rate. 3D printed prototypes allow companies to validate and test designs much more quickly and cost-effectively than traditional methods, significantly reducing product development times. This is achieved because 3D printing supports bridge production, which is an intermediate phase between prototyping and mass production using traditional methods. With this technique, companies can produce small series of products cost-effectively while waiting, for example, for large-scale production facilities to be ready to go into operation.
What do you think of integrating additive manufacturing into traditional production? Let us know in a comment below or on our Linkedin, Facebook, and Twitter pages! Don’t forget to sign up for our free weekly Newsletter here, the latest 3D printing news straight to your inbox! You can also find all our videos on our YouTube channel.