#3Dstartup: 6K on creating advanced materials for additive manufacturing
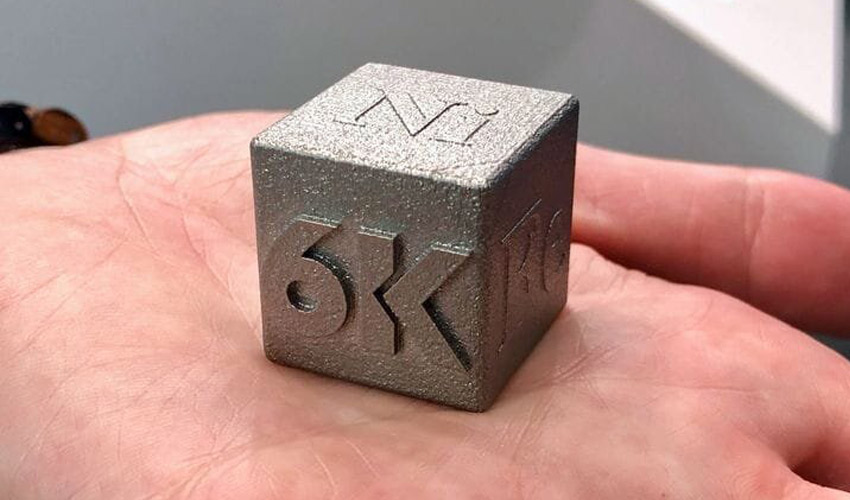
The U.S. company 6K is focused on creating premium materials to advance relatively new industries such as additive manufacturing, renewable energy, and more. If we focus on additive manufacturing, the company has identified the growing demand for metals that can be used in production for sectors like aerospace, medical, automotive and others. In order to meet this demand the company has developed a technology, which they call UniMelt, that enables them to create alloy powders that are truly spherical, void of porosity and satellites and that offer better flowability, or in other words high-performance powders. The UniMelt system uses spheroidization and densification processes to create these premium quality powders. In order to learn more about these processes and what type of materials 6K is working on exactly we had a chat with Dr. Aaron Bent, CEO of 6K since 2014.
3DN: Can you present yourself and your relationship with 3D printing?
My name is Dr. Aaron Bent and I am the CEO of 6K, having joined the company as CEO in 2014 as employee number 3 – we have just under 100 employees today. Over the last 25 years I have founded or run technology startups across markets as diverse as telecommunications, defense & aerospace, automotive, solar, and others, with a common thread that an advanced material has been the enabler for a class of new products. I look for companies that provide a fundamental ability to change the way things are done today, with the goal of having a profound impact on markets and products. 6K is such a company, and the one that has the most potential impact of any I have been involved with in my career.
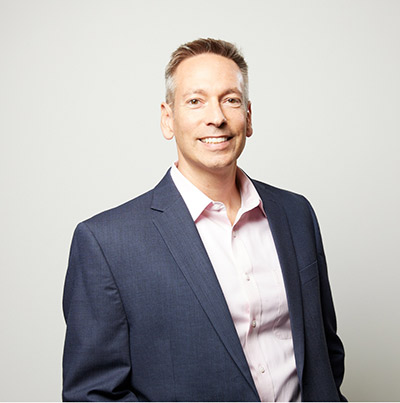
Dr. Aaron Bent, CEO of 6K
3DN: How did the idea of developing 6K come up?
6K (at its inception was called Amastan Technologies) started as a research project at MIT and later moved to the University of Connecticut focused on microwave plasma as a way to synthesize materials for various markets. We demonstrated the versatility of the platform to manufacture metal powder for AM, advanced materials for energy storage, phosphors for LED lighting, semiconductor materials, defense IR-transparent materials, and more. We quickly began an effort to focus and commercialize the technology, starting down the path of matching capabilities, materials and applications.
We commercialized the microwave plasma into a formal product called UniMelt® which is a manufacturing production system that creates the final material that is used for metal powder production today. Over the course of the last five years we’ve honed in on the additive manufacturing market and the energy storage market because of the advantages we can bring to those two markets with respect to sustainability, quality of materials and in the case of additive, being able to create not only the more common materials like In 718 and Ti 64, but custom materials that have never been available for AM.
3DN: What is the meaning of 6K anyway?
As for the name 6K, we recently rebranded the company to 6K from Amastan Technologies which reflects the UniMelt process in name and visually through our logo. 6K represents 6000 degrees, setting 6K technology apart from all others. It is the temperature of operation of UniMelt (5778K to be exact), the world’s only microwave production scale plasma, and is also the temperature of the surface of the sun.
3DN: Can you tell us more about your UniMelt system?
At the heart of the UniMelt® system is an atmospheric pressure microwave plasma generation unit that enables a large production zone with uniform temperature distribution, unmatched by arc-electrode or inductively-coupled plasmas. It is important to note that Unimelt is Not Gas Atomization (GA) or Plasma Atomization (PA). UniMelt is the world’s only microwave based plasma metal powder production system. At 6000 degrees, UniMelt is capable of processing ceramics, metals and alloys, both common AM metals like In 718 or Ti 64, but also custom alloys that haven’t previously been available for additive manufacturing.
Organizations can now design with an unprecedented range of materials because any metal or alloy that is machined can now become a feedstock for 6K’s premium powders. UniMelt does not use a wire of ingot as feedstock. Instead UniMelt utilizes certified machining scrap as feedstock opening up the possibilities for AM premium powder to include whatever material that has typically been produced using subtractive technologies such as CNC. In addition, we can rejuvenate used powder and even take AM supports and failed builds as a feedstock for the UniMelt process. This is important on two fronts. First, we can ensure certified chemistry because we start with certified chemistry in the form of scrap, used powder etc. Second, we are driving the circular economy and delivering the world’s first premium AM powder derived from sustainable sources.
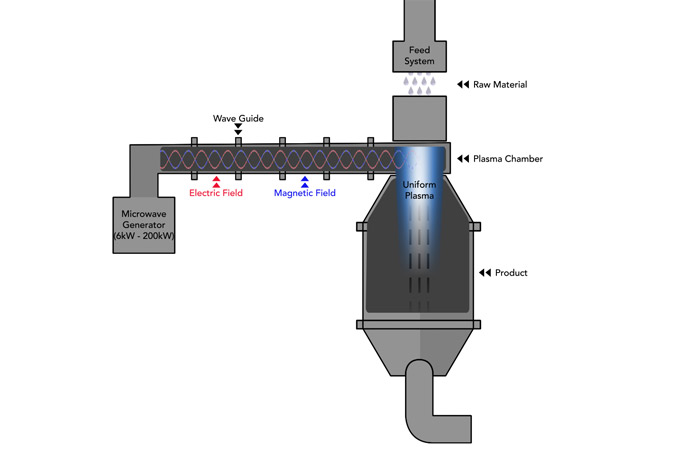
The UniMelt system is the world’s only microwave based plasma metal powder production system according to 6K.
In short UniMelt delivers:
- Highly-uniform plasma production zone
- Continuous, zero contamination process
- 99%+ efficiency (microwave to plasma)
- Inert, reducing, and oxidizing atmospheres
3DN: What kind of materials can you produce for the additive manufacturing market?
This is a great question and truly a key differentiator for 6K. As referenced above, UniMelt utilizes certified machined scrap, used powder etc., as a feedstock opening up a world of new possibilities to AM. Some key examples we demonstrated at Formnext included: INCONEL 718, INCONEL 625, Ti-6Al-4V, MOLYBDENUM, RHENIUM, STAINLESS STEEL 17-4, ALUMINUM AlSiMg, TANTALUM, TUNGSTEN, 8% YTTRIA STABILIZED ZIRCONIA. In addition, we demonstrated the world’s first High Entropy Alloy (HEA) at Formnext in Frankfurt last November. HEAs open limitless possibilities for having a ‘perfect blend’ of elements to tailor properties, such as high strength coupled with superior elongation, higher strength-to-weight ratios, or stable properties over a wider range of temperatures.
Our production team has 20 years of experience and knowledge in alloys, metals reclamation and powders productions. And we are excited for the expansion of production plant adding 40,000 sq ft additional production space to the facility located just outside Pittsburgh PA. Our production plant today sells over 1 million lbs of reclaimed titanium into the premium alloying for aerospace, medical and auto industries and is ISO9001 certified with AS9100 expected in Q3 of this year. The new 40,000 addition will be focused on additive manufacturing powders and will augment our already successful metals reclamation business.

3D printed turbine blade using 6K premium materials
3DN: Who are your main targets? What applications do they create?
Our initial material that will go into production will be In 718 so the markets that utilize this material are aerospace, oil and gas, land-based turbines and other industrial markets that require the characteristics In 718 delivers i.e. heat and corrosion resistance. Later this year we will introduce Ti 64 which will address the markets listed above but will also open up the medical device and implant space. As mentioned earlier, we are also working on HEA and discussing partnerships with organizations in the aerospace/defense markets and oil and gas. Certainly, given the tremendous application possibilities, HEAs could address many other markets, based on their element make-up and advantages.
Its also important to note that the UniMelt has a tunable particle sized distribution (PSD) with 100% yield which allows 6K to produce metal powder very efficiently for many technologies including powder bed, EBM, and Binder Jet, direct energy deposition and cold spray, plus PM processes like MIM and HIP.
3DN: What are the main advantages of your plasma technology?
UniMelt® is a highly robust production platform that delivers the highest premium powder for additive manufacturing. Powders that are highly spherical, void of porosity with the fewest satellites of any powder manufacturing technology. What’s more, UniMelt leverages sustainable sources as feedstock. Whether it’s certified millings from CNC, grindings, used additive powder or even the support material used. There is no excess waste or other cut sizes that head off to the landfill or sit in some warehouse being written off the books. UniMelt can tailor the PSD to the requirements of a particular additive process and even enable organizations to alter PSD to advance a material or zero in on a PSD that will deliver higher performance.
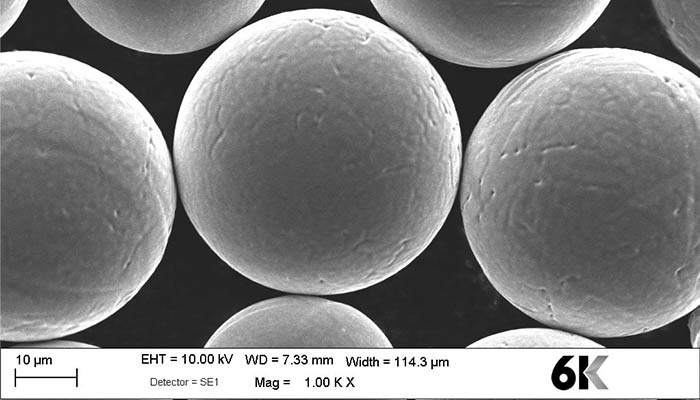
According to 6K, powders that are highly spherical, void of porosity with the fewest satellites of any powder manufacturing technology | Credits: 6K
UniMelt is the world’s most capable plasma production system engineered for:
- Highly sustainable process
- Up to 100 tons per year
- Continuous feed process not limited by wire or ingot feedstock
- Capable of processing ceramics, metals, alloys, and thermoplastics
- Highly-uniform plasma zone
- High uptime systems, recipe-driven, remote operation
- Nano through 100s microns
3DN: Any last words for our readers?
As on organization we are excited to make an impact on the additive manufacturing market and to help customers advance their production with powders from 6K. Our overall goal, is to enable a better business case for AM designers through:
Infinite Materials Choices: Enable customer to build with infinite material option and not be limited by today’s material choices. Our goal is to help them develop new products that meet and exceed market expectations with a wide choice of material options from 6K.
Highest performance parts: We want to ensure our customers build the highest performance parts. This means leveraging the strength on UniMelt to produce powder with zero porosity, high sphericity with no satellites with high flowability all while meeting or surpassing ASTM specifications.
Building for a circular economy: Lastly, we want to encourage our customers to build sustainability and contribute to a circular economy. This means not only utilizing 6K powder, but contributing back by partnering with 6K on their certified machine scrap, used powder and other sources of potential feedstock that can be rejuvenated back into premium powder.
What do you think of 6K’s system to develop advanced materials for additive manufacturing? Let us know in a comment below or on our Facebook and Twitter pages! Sign up for our free weekly Newsletter, all the latest news in 3D printing straight to your inbox!