3ntr and the Importance of Continual Innovation in 3D Printing
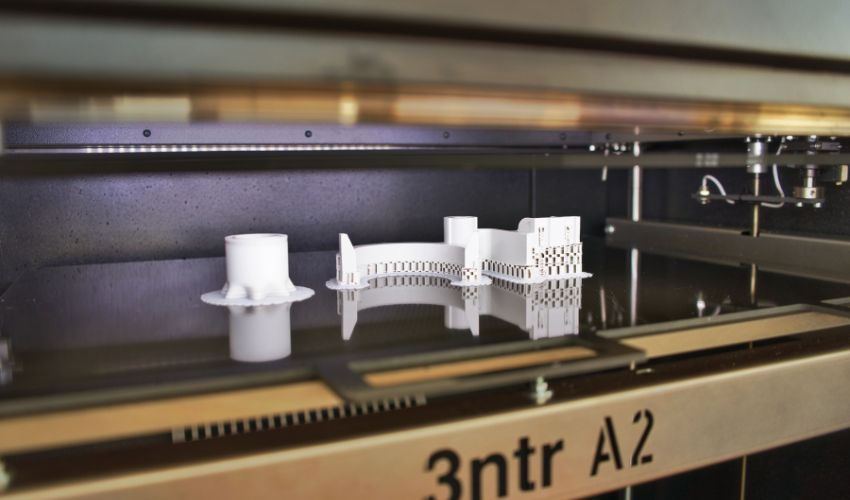
When it comes to Italian-made excellence in 3D printing, there is one name in particular which often stands out. 3ntr is a family-owned company that was founded over 60 years ago as Jdeal-Form. However, under the name 3ntr, it has been involved in additive manufacturing since 2010, building multi-material, extrusion solutions for a variety of different sectors including automotive, aviation, and medical, among others. One of the ways the company has made its mark on the industry is through its commitment to research and analysis, always seeking to improve its solutions as well as offering everything that the customer could need, from material to software. We spoke to Davide Ardizzoia, the CTO of 3ntr, to learn about why they got started in 3D printing, their solutions and applications and more.
3DN: Could you introduce yourself and 3ntr?
It’s quite interesting actually. Before 12 years ago I never had any exposure to 3D printing. Of course, I had been exposed to automotive, design, construction and so on. But the company had no point of contact with additive manufacturing until 2010 when we started using it for some parts for power machinery.
Back then the technology was still quite exotic. And we were drawn to it for a simple reason. Our supplier was constantly late and we had always had issues because the parts we were sourcing were functional parts. At this point we decided to do it on our own. We told ourselves, look we are already making machinery, why don’t we make our own 3D printer to make some of these parts. And after six months we put together a functional 3D printer.
Funnily enough, visitors, suppliers etc. started hearing about the machine so they started asking why don’t you make a copy for me. And we really started to see the benefits of the technology in when we were able to make several iterations of a mold for a French company in August of that year. This was actually unbelievable at the time because in Italy, no one works in August, but we were able to make 6 or 7 iterations in that month despite that. The final result was that we were able to win the customer because we were extremely reactive. This was around 2012.
In 2013, we started making our own printers and we were featured in September in Wired Italy. Starting that month, I went to my first 3D printing trade fair, the Maker Faire in Rome. That helped us to understand what to do next. I saw a lot of people who were clueless about 3D printing and that made it easy to decide to become a professional 3D printer supplier and to keep away from consumer 3D printing. The reason behind that decision is that if you really want to do something with 3D printing you need to know how to design and do that in 3D. And not everyone can do 3D modeling, so we wanted to focus on professional solutions.
3DN: What about your solutions today?
Currently we offer a number of FDM 3D printing solutions: the SPECTRAL 30 3D printer which is capable of addressing even the most complex markets and most extreme manufacturing challenges; the A2v4 for high precision large format 3D printing; the A4v4, a powerful and compact 3D printer that is suited for research and production; and last but not least our latest printer SEQUOIA, a hot chamber large format 3D printer. All our 3D printers are capable of true multi-material 3D printing and are robust and reliable. Beyond our software and material offerings, we also have our own drying units, VENTO and STORM as well as the F1 filtering unit.
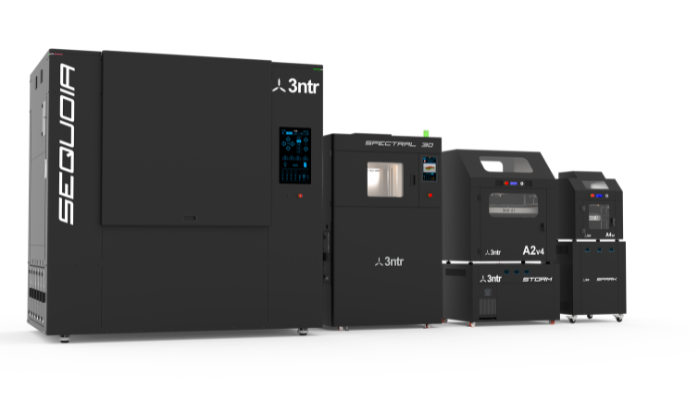
The current line-up of 3ntr’s FFF industrial solutions
Above all, we want to give our customers’ a choice. Our machines are open, our material choice is open, yet we are giving the user a tested solution with our materials and software if they don’t want to do any R&D. Most people would prefer to have a solution that is click and print. But for the remaining 30-40%, these are customers that if needed they are able to dig deeper and move the parameters to achieve that special result. We promise quality and we promise that flexibility.
And our path has always been quite clear, that is why we kept working on improving our solutions along with software and material improvements. We understood that when you start working with more industrial materials like ABS, ASA, polyamides, you need a working support polymer. This means that a single nozzle is far from being acceptable for an industrial solution. As a result, most are looking for something that is the final shape, with minimal support removal needed. So, across all those years, we have seen a good evolution of the chemistry and support generation itself.
On the other side, we have been evolving our mechanical approach covering everything from extrusion to heated chambers. Something to note as well is that we have never relied on 3rd party extruder suppliers. We always made them ourselves because the extruder is the heart of the machine, that is where you find all the value of the machinery. And right now, we are probably at the 24th version of our extruders and we are very excited about it. Because beyond the performances and the finishes we are achieving, which will come to fruition in the V5 series with Sequoia being the first, the quality is amazing. And the speed as well. Through the years, we have been improving and bringing to the market new capabilities that many companies are just now starting to embrace. At the moment, we are at 3 or 4 nozzle printing and with this set up we are able to make real multi-material parts that can be used in many situations.
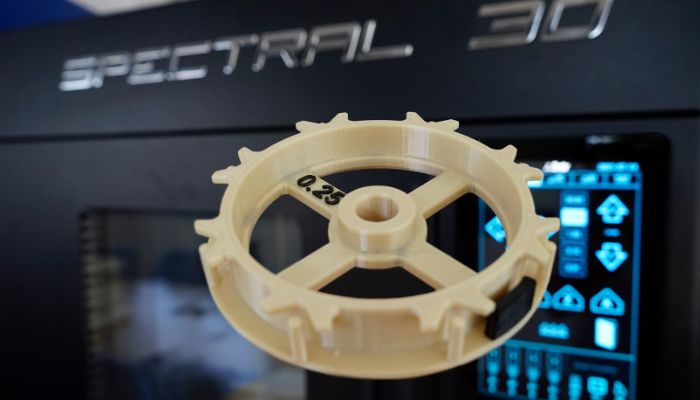
3ntr’s technology allows for high-quality parts including those made with high-performance polymers
A good example for this is a part that the DENSO Corporation, a spin-off of Toyota Motor Corporation, made using the A2V4 3ntr system. For those who do not know, DENSO is a supplier that develops advanced technology for nearly all vehicles on the road. They are particularly well-known for their air-conditioning systems. And their story is a good example of what you can do with true multi-material printing. Thanks to A2V4, they were able to combine a hard material which a soft one for a two-part prototype, namely an ASA polymer and a rubbery filament Elasto 85. The resulting part is a regulating part for the AC market, and it is a really functional part, it is working exactly like an end-use final part. Thanks to this approach, the customer was able to cut the development from weeks to a few days and saw a cost-saving of over 80%.
3DN: With which industries does 3ntr work?
It is perhaps faster to say which ones we are not working with: jewelry and dental. Both industries are much better served with resin 3D printers, and most of them are available with vertical packages for jewelry design, wax casting, it is a market we are not able to compete in. But on the other side we are doing very well in other sectors and every day we have a new customer, a new application, or a new market.
Through the years we have gone from nuclear, healthcare, wind farms, search engines, the fashion world, countless universities, polymer companies using our machinery to developing new polymer alloys for 3D printing. Companies involved in racing, automation, robotics, packing, special machinery are an easy fit because those are looking for reliability as well as a solution that is capable of dealing with functional polymers.
Right now, we are supplying the best Italian companies in a number of sectors. And the latest development for us is in oil & gas. It’s seeing a growing importance in our everyday work. And unfortunately, the reason is quite evident, it is because of the worldwide disruption of the sector and the search for new alternative energy sources.
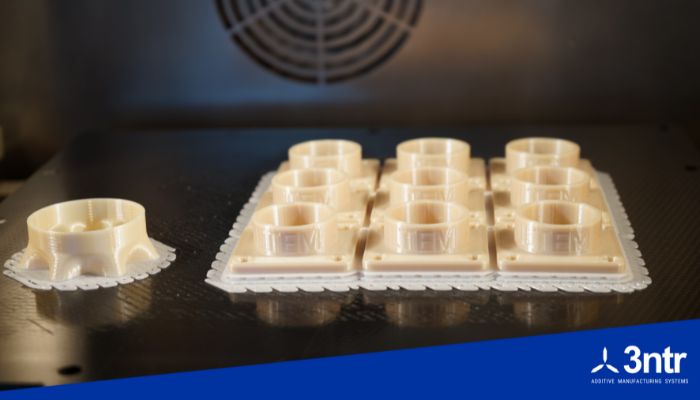
3ntr’s solutions can be used in many different industries
3DN: Any last words for our readers?
We have always been concerned with energy efficiency. All our machines have always been developed with a good eye for energy efficiency. And good return on investment. So, when we heard about machinery that took hours to prepare to start printing, we knew that was something we needed to change. And at this moment, we have no machine that takes more than 1 hour to start printing.
And still, we are always analyzing energy consumption and these data are available to our customers. This means, our customers can know precisely what is the carbon energy footprint of our machines. Even better, we are registering new patents about this because our new generation of machinery will be exploiting those findings to use the least amount of energy possible without any limitations. So, without giving up the possibility of working with any thermoplastic, we are offering energy efficiency and safety. You can find out more about us at our website HERE.
What do you think of 3ntr? Do you already use their solutions? Let us know in a comment below or on our LinkedIn, Facebook, and Twitter pages! Don’t forget to sign up for our free weekly Newsletter here, the latest 3D printing news straight to your inbox! You can also find all our videos on our YouTube channel.
*All Photo Credits: 3ntr