#3DStartup: VENOX Systems Focuses on Durability With Its 5-axis 3D Printer
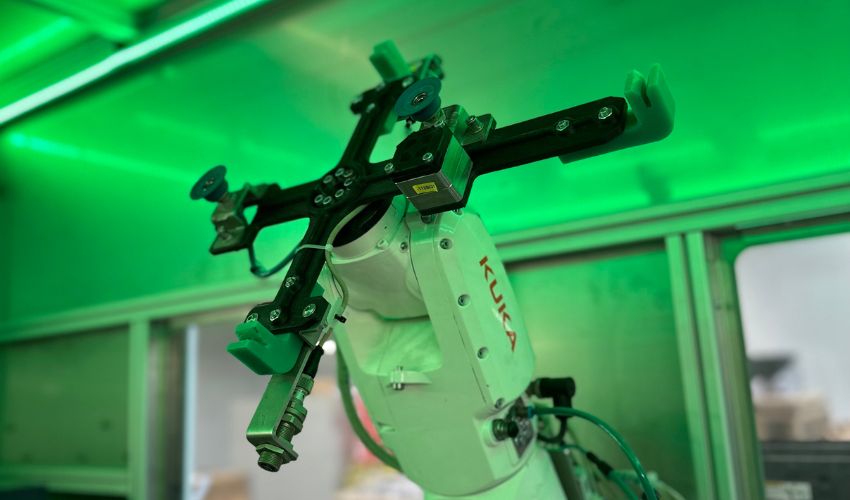
Based in Lingenau, western Austria, start-up VENOX Systems has come up with a 5-axis 3D printer capable of printing a wide range of thermoplastics, including continuous fibers. Its special feature is a head-changing system that gives access to several tools for different manufacturing options. In developing this machine, the startup aims to meet strength challenges in additive manufacturing. Indeed, it would be capable of depositing fibers – carbon, glass, aramid – along the part’s load path, thus offering a very interesting weight-to-strength ratio for many industries. We met the co-founder of this young Austrian company, Nicolai Wampl, to find out more about this printing process and its possible applications.
3DN: Could you introduce yourself and tell us about your connection to additive manufacturing?
My name is Nicolai Wampl and I’m co-founder of VENOX Systems. My journey with additive manufacturing began when I met the other co-founders of VENOX. They had developed a 3D printing system capable of printing with thermoplastic materials and continuous fibers. After overcoming the initial challenges, we sought financial support to bring our technology to an industrial level. Obtaining funding under an Austrian program marked a decisive turning point for our company.
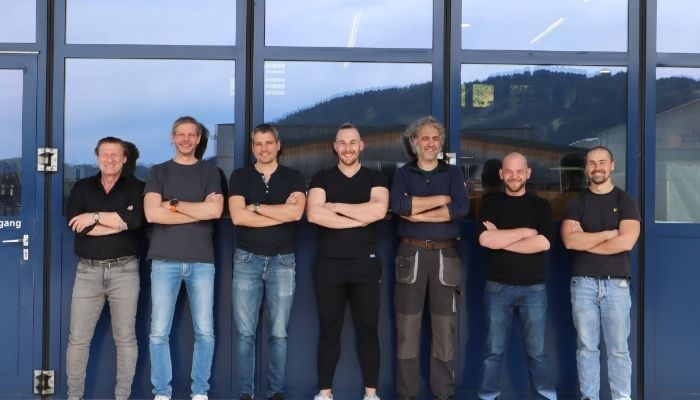
The VENOX Systems team
3DN: How did the idea for VENOX Systems come about?
A few years ago, when industrial 3D printing was starting to go mainstream, we took a look at the obstacles preventing 3D printing from competing with traditional manufacturing. We identified three major problems with FDM/FFF technology: part strength, manufacturing speed and surface quality. We set out to solve the first problem: strength.
3DN: Can you tell us more about your machine?
Our new machine, the V-REX (VENOX-Revolutionary Extrusion System), boasts several unique features. Drawing on our experience in mechanical engineering, we set out to create more than just an extrusion printer with a new gadget. Drawing inspiration from traditional manufacturing, we introduced a head-changing system that enables six different tools to be used in a single manufacturing process.
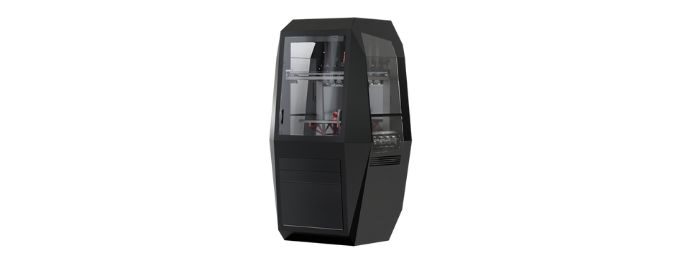
The V-REX 3D printer
These tools range from various FDM printheads to our exclusive CFFP (Collision-Free Fiber Placement) process, which enables the printing of continuous fibers such as carbon. While other machines can print continuous fiber-reinforced thermoplastics, our 5-axis gantry system is different. Carbon fibers and composites have anisotropic properties, meaning their strength varies with direction. Traditional 3-axis printers can only reinforce parts at the planar level, which translates into low Z-axis strength. Our 5-axis machine enables us to obtain stronger parts. It allows us to align the fibers along the part’s load path, resulting in lightweight, high-strength parts.
3DN: What materials are compatible with the VENOX Systems machine?
Our machine can print most thermoplastics with melting temperatures below 500°C, as well as composite materials such as carbon, aramid and fiberglass. In addition, it can print with wires instead of fibers to incorporate electrical features, although this capability is still under development. We have successfully produced the first demonstration parts.
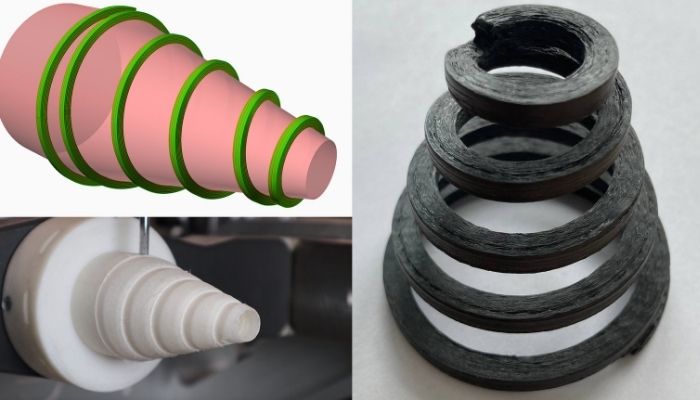
The machine is compatible with a wide range of thermoplastics
3DN: How does your machine respond to the challenges facing 3D printing users?
Our machine meets several major challenges. It is completely open, both in terms of material and software flexibility, enabling users to maximize the technology’s potential. The V-REX is designed for mass production of end-use parts, offering higher quality and functionality than simple prototyping.
3DN: Any last words for our readers?
By introducing this technology to the industry, we offer not only the machine, but also the printing as a service. If you have a project for which the weight/resistance ratio is essential, we’re the solution: don’t hesitate to visit our site HERE.
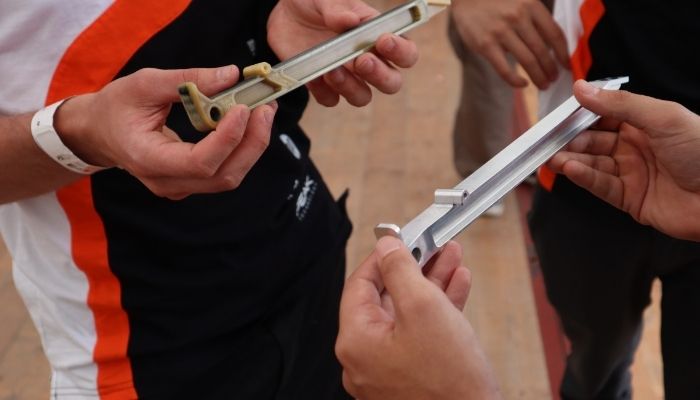
VENOX Systems also offers a 3D printing service
What do you think of the 3D printer developed by VENOX Systems? Let us know in a comment below or on our LinkedIn, Facebook, and Twitter pages! Don’t forget to sign up for our free weekly newsletter here for the latest 3D printing news straight to your inbox! You can also find all our videos on our YouTube channel.
*All Photo Credits: VENOX Systems