#3DStartup: Mechnano on Creating Additive Manufacturing Materials With Superior Properties
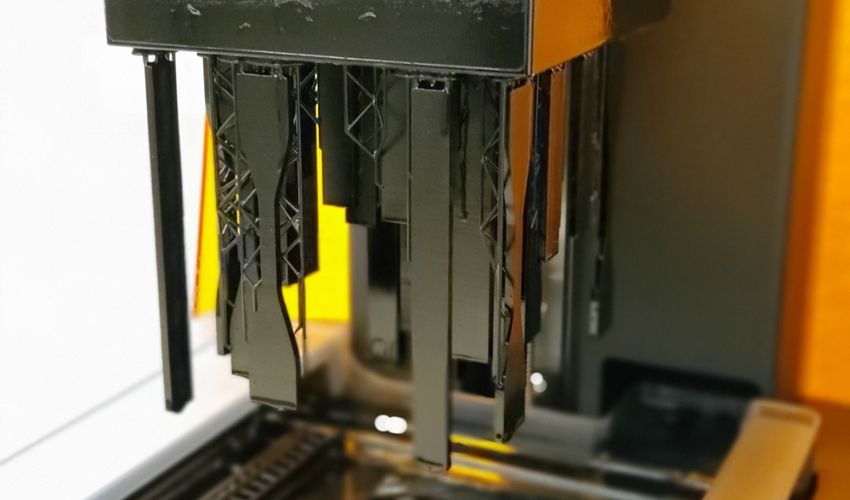
Though much focus in additive manufacturing is on the processes themselves, materials play a huge role in the final properties and characteristics of a part. It is for this reason that more and more we are seeing research and development focusing specifically on creating new materials for 3D printing, whether composites, metals or plastics. Out of the companies working on innovative solutions, we can count Arizona-based Mechnano, the first to put carbon nanotubes into resins to improve their properties, including strength or by enabling consistent ESD ratings. We spoke with Mechnano to learn more about its resins, the importance of anti-static materials and more.
3DN: Could you introduce yourself and your connection to 3D printing?
Absolutely. My name is Olga Ivanova, also referred to as Dr. O and I am the Director of Applications and Technology at Mechnano. I received my Ph.D. in Chemistry, specializing in nanomaterials. During my search for a post-doctoral opportunity, my goal was to explore a new technology or scientific domain while making a valuable contribution to a team. That is when I stumbled upon a job opening at Virginia Tech, related to nanocomposites for 3D printing.
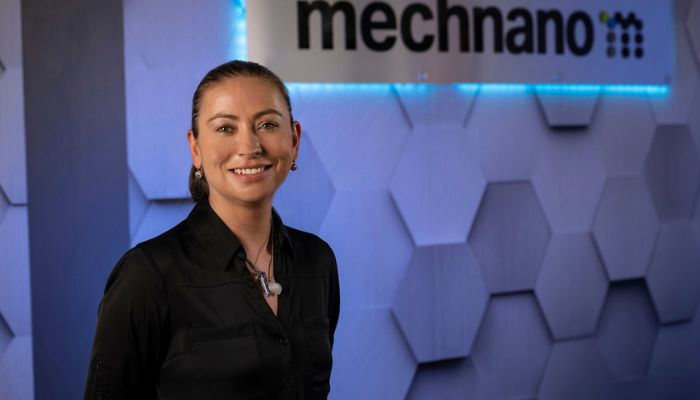
Olga “Dr. O” Ivanova
At that time, I had no knowledge about 3D printing, and I dedicated my time to understanding it through extensive research including reading articles, conducting web searches, and watching videos of the processes. It did not take long for me to develop a profound affection for this technology. I seized the opportunity and secured the job, marking the start of my journey in additive manufacturing.
3DN: How did Mechnano come about?
The initial vision of Mechnano’s founders, Steven Lowder and Scott Gillette, involved integrating discrete carbon nanotubes (CNTs) into AM materials to enhance their properties. Through their interaction with the AM community and extensive market research, these ideas evolved substantially. Mechnano gained strong support from key stakeholders, who confirmed that if discrete CNTs could offer the anticipated material property enhancements, this technology would enable AM to effectively rival traditional manufacturing methods.
While working on functionalizing CNTs for AM and thoroughly validating our initial material formulations utilizing this nanotechnology, we successfully tackled the challenges associated with introducing new technology to the market as a startup. It was during this process that we began to grasp the magnitude of the market gap that could be filled by offering nano-uniform ESD resins, which refers to resins capable of producing parts with a consistent ESD rating compared to the variable ESD found in competing products, causing difficulties in electronics manufacturing. Consequently, we refined our business plan and go-to-market strategy to align with our discoveries.
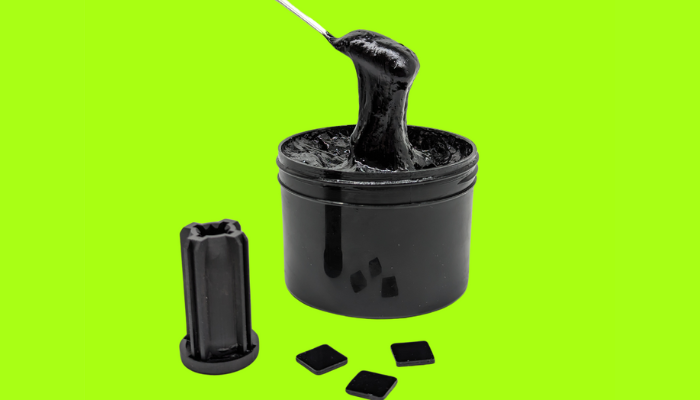
Mechnano is known for its distinctive resins that have been enhanced thanks to the use of CNTs
As a result, our primary focus revolves around ESD products. We offer Masterbatches to our formulator partners as a solid base for creating innovative materials. This unique “Collaborator via Masterbatch” approach has enabled us to introduce a range of ESD products to the market. These include a tough ESD resin, three rigid ESD resins tailored to meet the temperature requirements of room, bake, and interconnect processes in electronics manufacturing – all with nano-uniform ESD performance, which are of increasing importance in the Semiconductor, Packaging, and Microelectronics industries.
3DN: Could you explain how Mechnano’s ESD materials work and their benefits for additive manufacturing?
First, let me provide a brief introduction to Electrostatic Discharge (ESD). ESD is the sudden flow of electricity that occurs when two objects with opposite electrical charges come into contact. It can range from a mild shock to a potentially deadly Arc Flash. Even a low ESD voltage of 20 volts can damage micro-electronic parts, which is often caused by personnel during manufacturing and assembly. This can result in flawed performance, permanent damage, equipment downtime, and expensive repairs or part replacements. Furthermore, ESD is especially dangerous in environments with flammable substances.
There are three categories of materials used for preventing and managing electrostatic discharge. Conductive materials have low resistance and allow electrons to travel easily, transferring electricity to the ground or other conductive objects. Dissipative materials have a slower and more controlled flow of charges towards the ground. Finally, anti-static materials prevent the buildup of static electricity and reduce static charges.
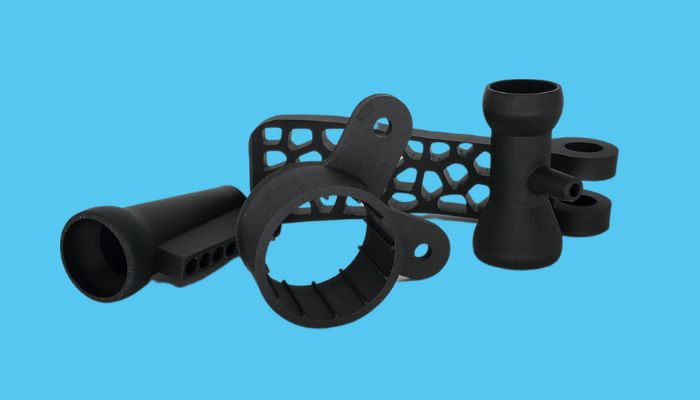
There are a number of applications for Mechnano’s resins
Mechnano uses our proprietary technology, D’Func (Discrete, Dispersed, and Functionalized Carbon Nanotubes) to deliver static dissipative properties to AM parts without compromising mechanical performance of the base material. The main goal is to overcome the natural tendency of CNTs to agglomerate into large bundles by achieving a discrete state and subsequently functionalize sidewalls to prevent re-agglomeration. We precisely control the CNT loading levels to achieve desired surface resistance. When incorporating D’Func into fabricated components, it guarantees nano-uniform ESD, facilitating safe and gradual movement of electrical charges to ground, which is crucial for protecting sensitive electronics, particularly systems with high monetary value.
3DN: Could you expand on a specific application example of your ESD materials?
There is a multitude of components that require static dissipation performance. Until recently, fabrication of ESD-safe components using AM techniques was limited to large geometries without fine features. Machining and mold tooling were the sole options to address parts requiring a smooth surface finish or intricate features. Mechnano has changed this situation with the ability to produce stable ESD-safe vat photopolymerization resins. These resins allow substitution of machined or molded parts with AM. This not only facilitates VAT printing for new product development (NPD) or low-volume surface mount technology (SMT) nozzles, JEDEC trays, grippers, circular connectors, dispensing tips, and various other components, but also paves the way for handling high-heat processes, which brings even more excitement to the table.
One specific example of high-temperature application involves a quick-turn fabrication of a carrier responsible for taking a circuit board through a reflow process at a temperature of 245°C. To execute this task, our customer utilized CAD to design the carrier, then sent it to a machine shop, where an aluminum carrier was machined and delivered back within a two-week timeframe. Subsequently, a verification process was conducted to assess the carrier’s fit to the circuit board. In the event of a mismatch, a replacement would require an additional two weeks to be obtained. Regrettably, such a delay often resulted in the loss of the project. To mitigate this risk, an intentional “fudge factor” was introduced during the carrier’s design phase, enlarging the pocket size slightly to ensure successful functioning during the first attempt. However, this approach also resulted in poor performance due to suboptimal fit.
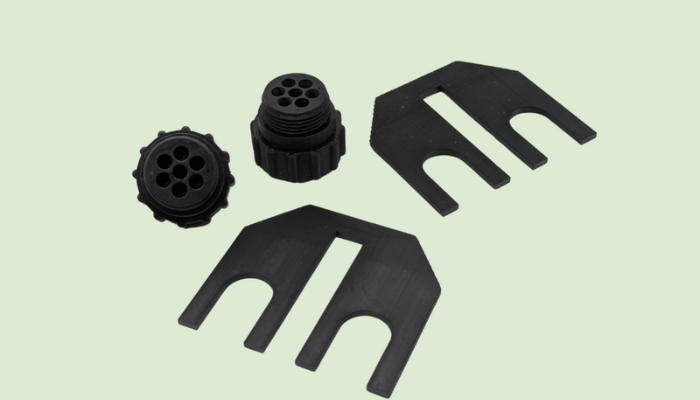
Most recently, Mechnano has unveiled a high-temperature resistant ESD material
Using our high-temperature ESD resin, our customer can build and cure the carrier to the precise dimensions before the board is delivered. In case the circuit board does not fit, any necessary design modifications can be quickly made. The updated version can then be printed, allowing for the immediate use of a precisely fitting, heat-resistant carrier on the floor going forward.
3DN: What are Mechnano’s future projects?
Our formulator partners have expressed interest in functionalizing CNTs to incorporate conductivity, EMI Shielding, and Rad Hardening into AM resins. While these developments are undoubtedly exciting, the largest projects by volume will focus on our laser sintering powders and pellets. We have successfully coated Polyketone, Polyamide, and PEEK with D’Func, thereby transforming these originally insulative powders into static dissipative with minimal impact on their mechanical properties. In addition, Mechnano has successfully integrated D’Func into Polycarbonate pellets to attain electrostatic discharge capabilities. Notably, our team is actively developing two additional products, and we look forward to sharing these exciting innovations with you. Stay tuned for more updates.
3DN: Any last words for our readers?
If you currently rely on machined aluminum or composite parts or use injection molding to fulfill your ESD requirements, it is highly recommended to consider AM for applications that require quick turnaround, necessitate exceptionally precise ESD ranges, or must endure extremely high temperatures. It is highly likely that you can fabricate nano-uniform ESD components through AM, that not only meet but surpass your performance expectations. You can find out more about Mechnano on our website HERE.
What do you think of Mechnano? Let us know in a comment below or on our LinkedIn, Facebook, and Twitter pages! Don’t forget to sign up for our free weekly newsletter here, the latest 3D printing news straight to your inbox! You can also find all our videos on our YouTube channel.
*All Photo Credits: Mechnano
Wow, this is really exciting to hear about Mechnano and their work on incorporating carbon nanotubes into 3D printing resins. As someone who is deeply passionate about the potential of additive manufacturing, I’m always eager to learn about the latest innovations in materials science that can unlock new capabilities.