#3DStartup: Mantle on its Unique Paste-Based Metal Additive Manufacturing Process
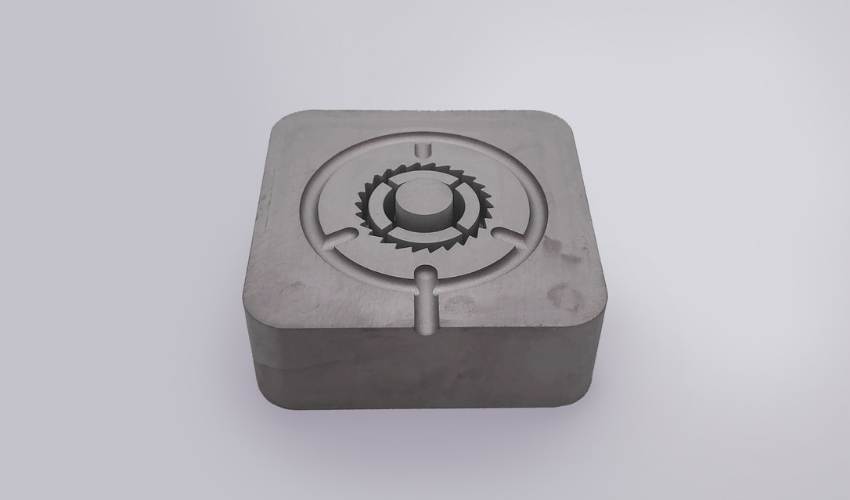
Mantle, a young, American startup, made headlines back in February 2021 with the launch of its TrueShape technology. The proprietary AM process distinguishes itself from other metal 3D printing processes on the market by using paste as the printing material as well as being the first to combine rough part creation and precision finishing. Thanks to the precision that their technology allows, the startup sees it as especially useful for applications like tooling. And with satisfied customers like L’Oréal and Westminister Tools, it’s clear that they are already starting to make their mark. We sat down with the CEO and co-founder of Mantle, Ted Sorom to learn more.
3DN: Can you introduce yourself and your connection to additive manufacturing?
Hi, I’m Ted Sorom, the CEO and co-founder of Mantle. I’m a mechanical design engineer by training and have spent most of my career developing and launching new products. My entire career, I’ve used polymer additive manufacturing for prototyping. I ventured into metal 3D printing when I saw the opportunity to redefine how mass-produced products are made by combining my tooling knowledge and Mantle’s new method of precision metal printing.
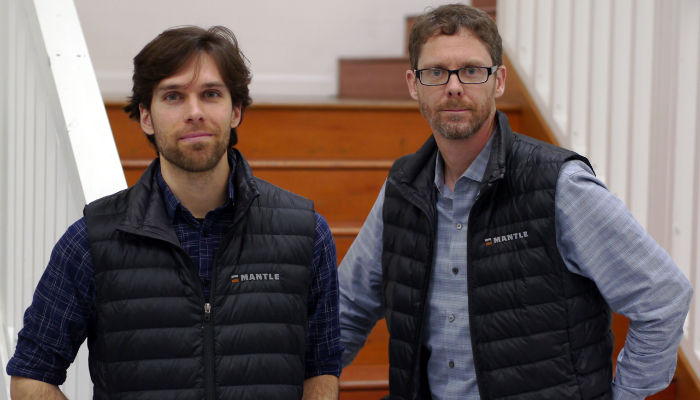
The co-founders of Mantle Steve Connor (left) and Ted Sorom (right)
When I was a new engineer right out of grad school, I joined a vertically integrated company that made high-end equipment using CNC machined metal and injection molded plastic parts which we made in-house. We were a small company, so I got to do a bit of everything: I designed the parts and molds upstairs and then went downstairs and made the molds before putting them into full production. I saw first-hand how time-consuming and expensive the toolmaking process was for even a simple plastic part. Our new product launch schedules were gated by tooling.
Unfortunately, my experience is not unique. Every day, we work with companies who struggle to bring their products to market because of the time-consuming and expensive toolmaking process.
3DN: Could you tell us about Mantle?
My co-founder, Steve Connor, and I founded Mantle to dramatically speed new production introduction via 3D printing. Early on, we were able to print parts with an entirely new level of surface finish and precision that for the first time were applicable for tooling. We then spent several years improving our process and developing the high hardness steels appropriate for the tooling industry. We are more focused than most companies in the 3D printing world because we know the problem we are solving.
Steve is a brilliant chemist who spent the early part of his career specializing in nanoparticles and metal pastes. He successfully developed a lower-cost replacement for the expensive silver metal pastes used in the solar industry. He then shifted gears to see if similar technology could be used for additive manufacturing. We started developing these pastes and our 3D printing process and had great results. We’ve refined our technology over the last five years and have proven that our approach works. As I describe below, these metal pastes are the foundation for our technology.
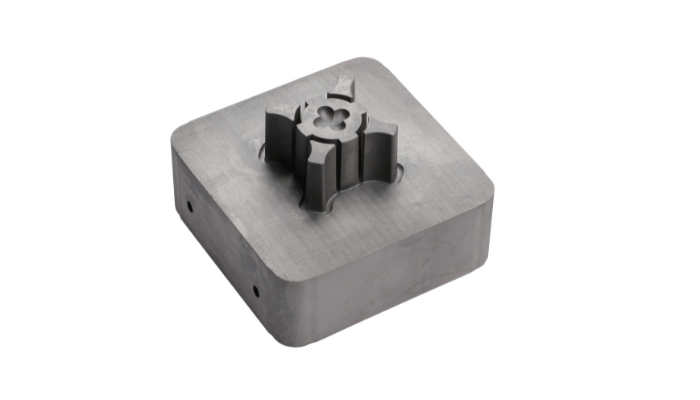
A part made by Mantle before removal and post-processing
3DN: How would you describe your unique technology, TrueShape?
TrueShape is a hybrid additive/subtractive process that 3D prints metal pastes before refining the part surface via traditional subtractive machining. It is different from other metal 3D printing processes because the parts from our process are highly precise and do not require extensive post-processing. They are accurate, have an outstanding surface finish, and have the mechanical properties of standard tool steels.
Our process starts with our metal paste material. The paste consists of metal particles and liquid carriers, which we extrude to build up the parts layer-by-layer. Then we heat and dry the paste inside the printer, which removes the liquid carrier and leaves a “green body” that is relatively soft and can be machined quickly and easily. The machining creates the accuracy, surface finish, and fine features needed for precision parts like molds. The final step is a sintering step, which is important because it allows for the final densification of the metal particles and establishes the final material properties. We sinter in a high-temperature furnace that brings the part’s temperature to just below the material’s melting point, then cools it off. When the parts come out of the furnace, they are high-hardness tool steels with extraordinarily smooth surfaces that can go directly into injection mold tooling applications with no post-processing of the mold surfaces
3DN: What advantages does TrueShape have that other 3D processes might not? For example for applications like tooling and molds?
For any 3D printing technology to be effective for an application, it needs to meet its specific requirements. Precision tools and molds have several critical requirements, including: high-hardness steel materials; outstanding surface finish so molded surfaces are smooth; high accuracy – a mold that is too large or too small by half the width of a human hair won’t work.
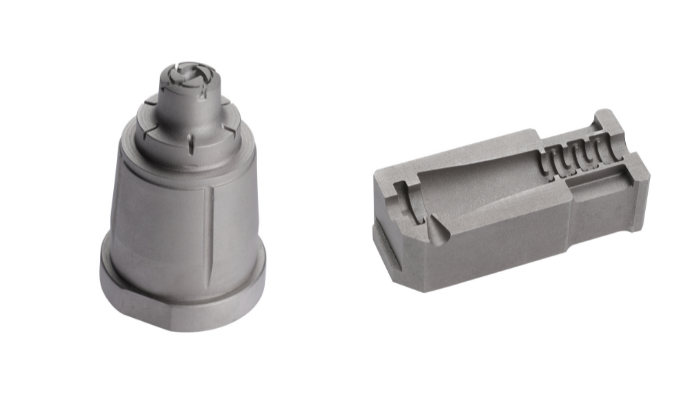
Thanks to Mantle’s TrueShape process, parts can be intricately detailed and precise. Here two different examples show different ways the technology can be used.
Our TrueShape process is unique because of our ability to meet these requirements without requiring costly and time-consuming post-processing. We produce highly accurate parts with an outstanding surface finish (1-3 um Ra) comparable to the surface finish of molds made conventionally. Furthermore, we have developed our materials to behave just like the tool steels that toolmakers use today, enabling long mold lifetimes and mold adjustments via texturing, polishing, machining, and welding.
TrueShape can also be used to produce mold designs that cannot be made conventionally, such as conformal cooling lines, which improve the performance of the molds. Other metal 3D printing processes have been used for tooling and molds in the past, but they all require extensive post-processing. This post-processing increases the time and cost of the mold; therefore, adoption has not been widespread. TrueShape’s process is faster and less expensive than both other 3D printing processes and traditional methods for making molds.
3DN: In terms of materials, instead of powders or filled filaments, Mantle has created a proprietary Flowable Metal Paste. How does it work and are the benefits to working with it over other ways to use metals in AM?
We chose to use pastes for several reasons, including that pastes are the most effective format for making precision components like molds. We formulate our pastes so they are optimized for our printing process and so they yield the required material properties of high-hardness tool steels.
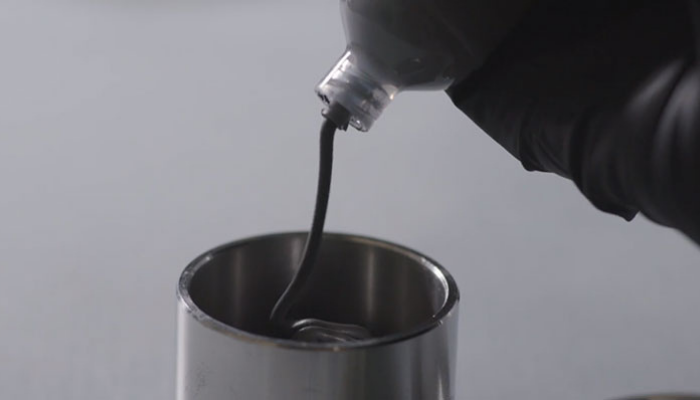
Mantle uses proprietary pastes for its precision metal AM technology, in contrast to others in the market.
Pastes offer several advantages: pastes can be extruded like other inexpensive 3D printing processes and do not require expensive lasers to melt metal powders together; pastes do not require a separate debinding step like most sintering-based extrusion metal printing processes; pastes do not require the same kind of special handling and safety protocols that loose powders require; and pastes shrink much less than other sintering-based technologies that use metal powders, which improves the accuracy of the printed part. But ultimately, we found that pastes are the most effective format for producing a wide range of materials with high accuracy and outstanding surface finish.
3DN: Any last words for our readers?
We are excited to bring this technology to market. We spent our first five years quietly developing the technology and working with a few companies to provide us feedback and validate our technology. These companies – including toolmakers, molders, and OEMs across industries – have helped create proof points that we can now share publicly. For example, a leading dishwasher manufacturer uses a tool insert from Mantle in production and already has over 200,000 shots from it. Our tool reduced lead time by 70% and cost by over 65%. A leading medical device company used Mantle to reduce the time to make a prototype mold from 7 weeks to 8 days – and reduced costs by over 50%. We are excited to now work with others and help them improve their toolmaking and product development processes. You can find out more about Mantle at their website HERE.
What do you think of Mantle and their unique metal 3D printing process? Let us know in a comment below or on our Facebook and Twitter pages. Don’t forget to sign up for our free weekly newsletter, with all the latest news in 3D printing delivered straight to your inbox!
*All Image Credits: Mantle