#3DStartup: LEAM Improves the Layer Density of 3D Printed XXL Parts
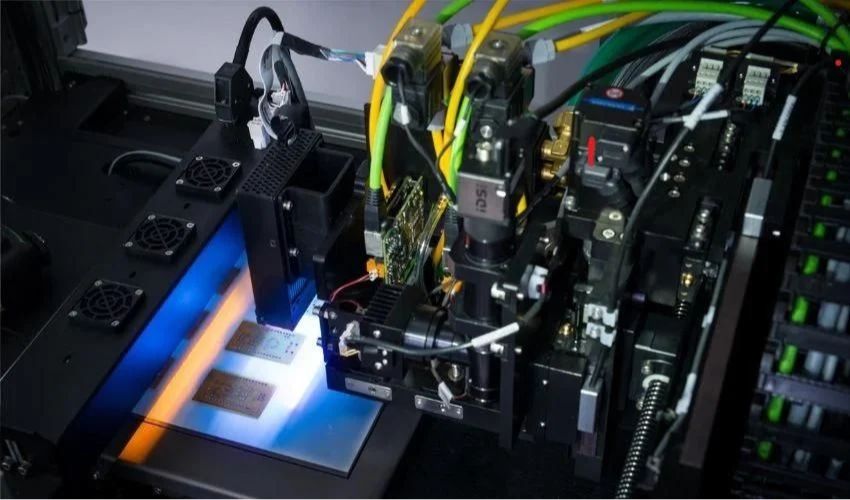
From science to 3D printing to business: this has been LEAM’s journey so far. The spin-off from the Technical University of Munich developed the foundation of the technology now marketed from within the university. With its DEMEX system, LEAM is breaking new ground in additive manufacturing. Instead of using a laser to melt material, they use a continuous light spectrum, heating the material just before the nozzle, ensuring better adhesion between layers. The DEMEX system developed by LEAM is available as an add-on module for large-format 3D printers. The young company has already attracted its first customers. We spoke to the LEAM team to learn more about the milestones they have reached, its technology and its plans for the future.
3DN: Could you introduce yourself and tell us how you discovered 3D printing?
The three of us founders (Patrick Consul, Ting Wang and Benno Böckl) have been interested in 3D printing ever since we studied mechanical engineering or started working as collaborating scientists at the Chair of Carbon Composites (LCC) at the Technical University of Munich, where we first met. Patrick had already tried his hand at 3D printing PEEK cores for aerospace structures during his Master’s thesis. But this was not possible at the time because the necessary strengths were not achievable. From 2017 onwards, however, he pursued this theme as a scientific collaborator at the Carbon Composites Chair. In the following years, he applied for and handled several research projects in which he continued to explore the subject.
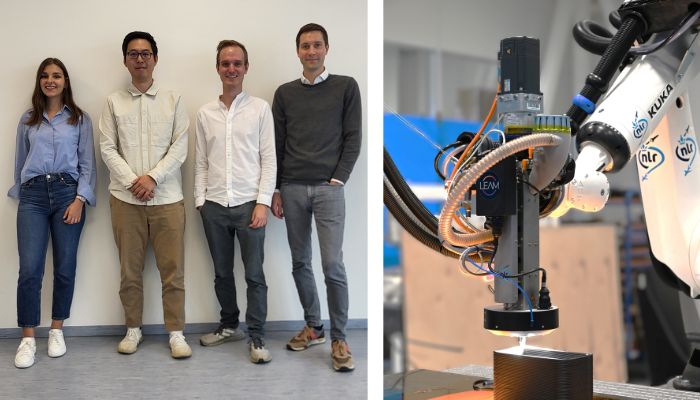
On the left, the LEAM team; on the right, the DEMEX system
Ting has been working on a research project to investigate the targeted heating of the substrate to achieve better bonding with the next layer. As a research associate, Ting carried out the first concrete preparatory work on which subsequent developments of the DEMEX system were based. Benno also worked for several years as a research associate at the Chair of Carbon Composites, where he became interested in the automated fiber placement process for carbon components manufacturing, a process with certain similarities to 3D printing. So, we came to 3D printing through science, which gave us a good understanding of its associated challenges. This has enabled us to develop solutions that open new possibilities for 3D printing in parts manufacturing.
3DN: How was LEAM created, and what have been the main milestones to date?
In his research projects, Patrick investigated a wide range of approaches to increasing layer adhesion and thus component strength in extrusion 3D printing. It became increasingly clear that the only really promising approach was to heat and melt the underlying layer at the right time. Ting investigated this practical approach as part of a research project and developed the first prototype of our future DEMEX system, which, however, still used lasers as energy sources. This approach produced promising results, but its commercialization was questionable, as the costs and protective devices required would have made the product unprofitable. So, we came up with the idea of using broad-spectrum white LEDs instead of lasers. These are much safer and cheaper than lasers, and after the preliminary tests showed it could work, we decided to set up a company to offer the system as a product.
Obtaining a grant as part of the EXIST Transfer of Research was then an important step. This enabled us to finance the first 18 months and set up LEAM so that we could exist as a company. Last year, we also received a pledge from the ESA Business Incubation Centre Bavaria, which supports our project. Another milestone was the first proof-of-concept with a customer, which not only showed that our system works but also that there is great market potential. We were then able to sell and install the first systems to customers. In the middle of last year, we took on our first full-time employee, who works for us as a development engineer, so that we have now also become an employer. Finally, we were able to file a patent application for our technology, which is decisive for the company’s future.
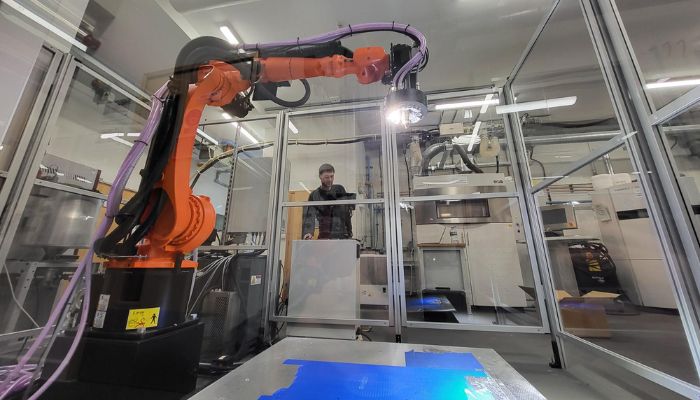
LEAM has registered a patent for its DEMEX system.
3DN: Could you describe your DEMEX system? What are its advantages over other processes?
The DEMEX system is a complementary component for large-format 3D printers. The system combines LED emitters and infrared cameras distributed around the extruder nozzle. Using the LED emitters, the DEMEX system can heat the substrate in a highly targeted and localized manner in front of the nozzle, guaranteeing perfect welding of the layers. A closed control circuit with infrared cameras ensures the desired target temperature is reached. Instead of the maximum z-resistance of 60% previously achievable, the workpiece can now reach 100% of the resistance specified in the material manufacturer’s data sheet – in all directions! What’s more, it’s now possible to use materials of much lower quality, such as injection-molded materials, which until now have been totally unsuitable for 3D printing, as it was impossible to achieve layer adhesion. The DEMEX system communicates with the printer controller, so it always knows in which direction the printer is moving and which area needs to be heated. This does not need to be taken into account when creating the G-code and does not disrupt the printer’s current operating processes.
Our technology solves common problems in 3D printing. One approach often chosen in 3D printing is that of heated print spaces. The disadvantage is that the temperature cannot be chosen at any height, otherwise, the part becomes unstable and collapses. This problem doesn’t exist with our DEMEX system, as we only heat a very thin layer on the surface in a very limited area in front of the nozzle. We can, therefore, go beyond the melting temperature of the material, enabling us to achieve much higher resistances. Another approach is to use infrared emitters distributed throughout the printing area or installed locally on the nozzle.
However, the latter have the disadvantage of very long reaction times, from one to three seconds, which makes infrared emitters very difficult to adjust. By contrast, the power of our LED-based system can be adjusted in milliseconds, and the power density achieved is also higher than that of infrared emitters. Our LEDs also offer a clear price advantage over lasers. On the one hand, the energy sources themselves are already 90% cheaper than a comparable laser system. On the other hand, the necessary protective devices, which can cost more for a large-format 3D printer than the entire DEMEX system we offer, are eliminated.
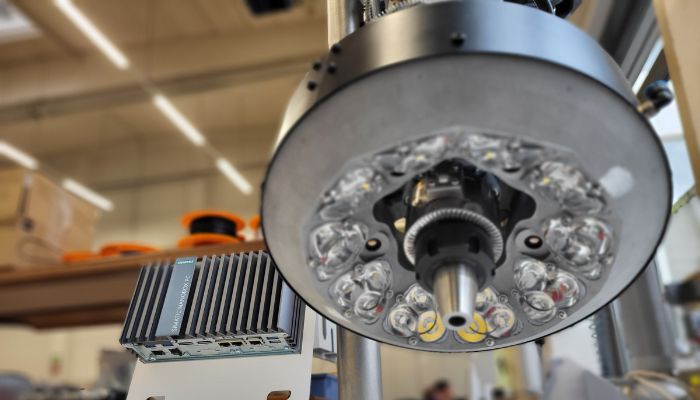
With DEMEX, LEAM uses LEDs rather than lasers. LEDs can be adapted quickly and are also less expensive than lasers.
3DN: Who is the DEMEX system designed for, and which applications benefit most from it?
The advantages of the DEMEX system are particularly evident in applications involving high-performance plastics or very large components, like in the aerospace or oil industries. This is where the problems we solve have the greatest impact. If we consider, for example, a large component that breaks down during printing, the part would have been considered scrap, with costs that can run into the thousands. With the help of DEMEX, printing can easily be continued after the interruption, as the connection with the lower layer is assured. The system is also suitable for other industries using engineering plastics or fiber-reinforced plastics. In principle, anyone wishing to print parts subject to mechanical stresses for which the strengths achieved to date with 3D printing are not sufficient will benefit. Examples include shipbuilding, rail vehicle construction and the automotive industry.
3DN: What have been LEAM’s most exciting projects so far?
The installation of our first two systems was certainly exciting. We installed the first DEMEX at NLR, the Dutch equivalent of the German Center for Aeronautics and Aerospace (DLR). Shortly afterwards, we were able to commission the second system at the University of Exeter in England. But current projects are also very interesting. There are always new requests in sectors we’d never have thought of. For instance, we’re currently talking to customers in the construction sector, but there are even people interested in fish farming, so there are no limits.
3DN: Any last words for our readers?
The next step we want to take with our system is to adapt it to smaller printers. At present, we can only use large-format 3D printers as we still need a certain amount of printing space. But we’re already working on reducing the size of the various components, and we want to be ready to equip filament printers with the DEMEX system later this year. We’ve received numerous requests to this effect, so the demand is high. What’s more, we’ll be rolling out the switchover to Siemens Industrial Edge in the coming weeks. This involves new hardware and software components in our system, which introduce entirely new possibilities in terms of system maintenance and upgrades, as well as reliability.
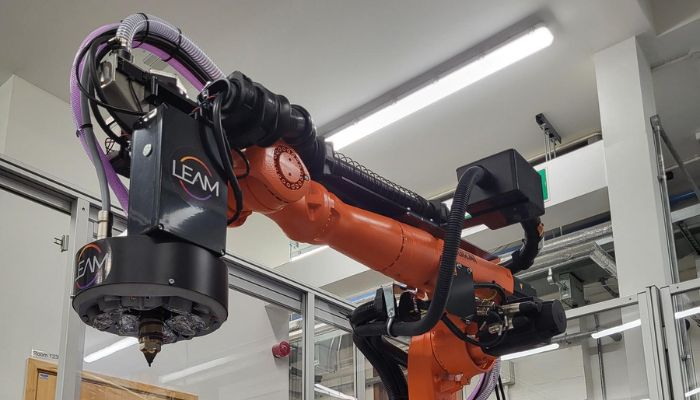
The DEMEX system is currently only available for large-format 3D printers.
What do you think of the LEAM startup and its DEMEX system? Let us know in a comment below or on our LinkedIn, Facebook, and Twitter pages! Don’t forget to sign up for our free weekly Newsletter here, the latest 3D printing news straight to your inbox! You can also find all our videos on our YouTube channel.
*All Image Credits: LEAM