#3DStartup: Inkbit, 3D printer powered by machine-vision and AI
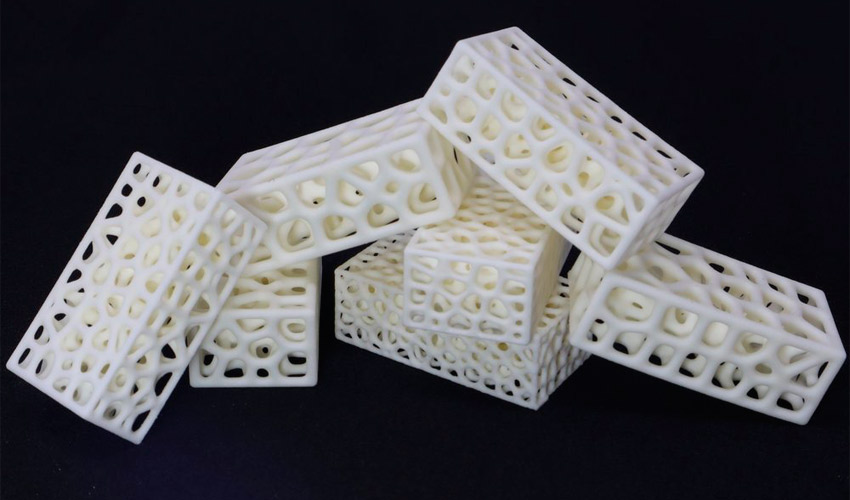
A startup straight out of MIT, Inkbit, is working towards overcoming traditional constraints to 3D printing by giving its machines ‘eyes’ and a ‘brain’. The industrial 3D printer developed by Inkbit is a multi-material machine capable of printing extremely flexible materials with great accuracy. It uses machine learning and artificial intelligence to address challenges in additive manufacturing, especially when using rubber-like materials such as silicone, or high-temperature materials such as epoxy. The system scans each layer that is being printed and corrects errors in real time, while at the same time it uses this information to predict the warping behavior of materials. We met with Davide Marini, co-founder and CEO of Inkbit to learn more about the startup’s technology and activities.
3DN: Can you introduce yourself and tell us how the startup Inkbit came about?
My name is Davide Marini and I am the co-founder and CEO of Inkbit. I am originally from Italy and came to the United States to pursue my PhD in mechanical engineering. I discovered my vocation for entrepreneurship after working for several years as a scientist at Children’s Hospital Boston, after which I cofounded a company called Firefly BioWorks in the area of life sciences. Interestingly, Firefly’s technology relied on shining UV light through a mask to polymerize monomers in a microfluidic channel in order to obtain individually encoded and bio-functional microparticles. It was essentially micro-scale 3D printing, even though at the time I didn’t think of it in this way.
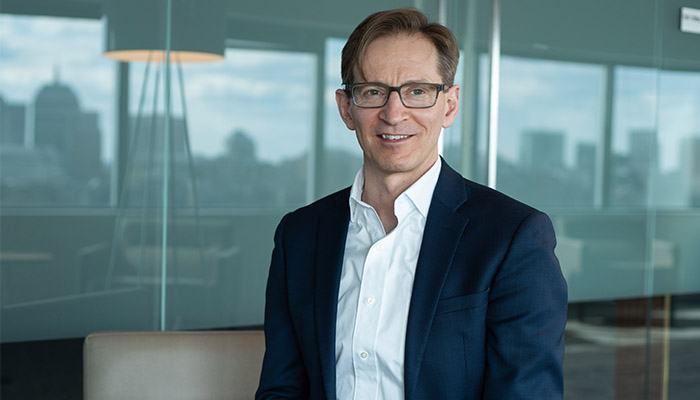
Davide Marini, co-founder and CEO of Inkbit
After Firefly was acquired, I was looking at a number of exciting technologies being developed in various academic labs, in search for my next adventure. I met the inventors of Inkbit’s technology at an event organized by the MIT Desphande Center for Technological Innovation, where they were exhibiting their prototype printer. The team was based at the MIT Computer Science and Artificial Intelligence Lab (CSAIL) and was led by Prof. Wojciech Matusik, a pioneer in the emerging field of computational fabrication. I knew very little about 3D printing then, but what struck me immediately in Javier Ramos’ description of the technology was the elegance of the idea. It seemed natural to me that a 3D printer should be able to react and self-correct in real-time while printing. The business card I handed to Javier carried a quote he recognized from a sixteenth century nun, which I took as a sign that I was looking in the right direction.
Over the following months the inventors and I got together often, and I gradually became more aware of the enormous potential of this simple idea. The inventors eventually invited me to lead the commercialization of their technology. We started operations in the Summer of 2017, and we named the company Inkbit to emphasize the vision of combining physical inks and digital bits.
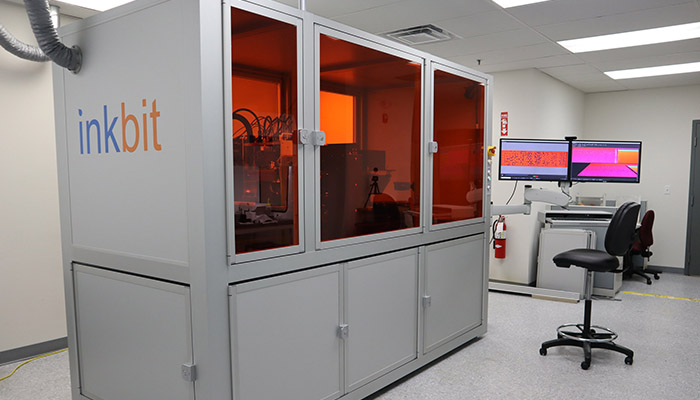
The Inkbit 3D printer
Today, engineers routinely use multi-material inkjet 3D printers to make prototypes, but they cannot manufacture final parts with the technology due to limited material choices. Many rubber-like materials such as silicone, and high-temperature materials such as epoxy, are difficult to 3D print due to uneven distribution, shrinkage, warping and printer failures like clogging. At Inkbit, we are endowing 3D printers with eyes and brains to address these challenges. Our machine is the first one that can learn the properties of a specific material and predict its behavior.
3DN: Can you tell us more about how Inkbit’s technology works? What are its benefits?
Our additive manufacturing system is the first to use machine vision and artificial intelligence (AI) to deliver a multi-material jetting platform with the speed, precision and materials required by the most demanding industrial applications. The key to our process is the elimination of mechanical flattening of each layer, as is done in today’s inkjet printers. Mechanical flattening poses some key drawbacks: it restricts the types of materials that can be printed, negatively impacts the process accuracy and precision, and wastes about 30% of all printed material.
Instead of physically flattening each layer, in our machine a sophisticated 3D scanning system generates a topographical map of each layer after deposition. Any discrepancy from the expected geometry is corrected by remapping subsequent layers. These data are also used to train a machine learning algorithm that enables our printer to learn the properties of each material and anticipate its behavior. This ensures parts are built quickly and accurately every time. Per-layer scanning also allows us to generate a full 3D reconstruction of each part as-printed, providing a complete digital record of every print, ensuring 100% quality control on every part.
We chose material jetting for our platform because it is multi-material, scalable, modular and already proven at industrial scale in the graphics, ceramics and textile sectors. Our adaptive, contactless printing also enables the use of new materials that can meet demanding performance requirements. For example, we can develop materials to meet a wide variety of customer needs, from elastomers stretching over 800% to strong resins capable of withstanding up to 170°C. Our multi-material 3D printer can reliably manufacture accurate, high-precision final parts in volume.
3DN: How can one incorporate Inkbit’s technology into a 3D printer? Could other systems benefit from what you have developed?
We worked for a long time to develop a state-of-the-art, proprietary optical coherence tomography (OCT) scanner as the main vision system of our technology. It uses light with a long wavelength to see through the surface of materials and scan each layer of a part at the voxel level, with real-time closed-loop feedback control. This system acts as the ‘eyes’ of our printer and enables corrections in real-time and is the basis for building an additional layer of artificial intelligence, ‘the brains’ of the printer, that enables the machine to anticipate the behavior of challenging materials.
In principle, it is possible to port our system onto other architectures. We have also received significant interest from metal 3D printing manufacturers in using our system in their machines. Yet, integrating our system into a printer requires access to, and significant rewriting of, the entire software stack that controls the machine. It is not a simple plug-and-play component.
3DN: Currently, who are your main clients and which industries are you focusing on?
Inkbit has begun working with leading global customers, such as Johnson & Johnson, through our early access program to develop an initial set of applications in the medical field. We are also very interested in life sciences, given my background, as well as in robotics and prosthetics applications.
3DN: In your opinion, what is the importance of AI and machine learning in additive manufacturing?
The use of machine vision is already well established in traditional manufacturing. I believe it will become an essential aspect of additive manufacturing as well. I am also especially excited by the use of AI in manufacturing, as some of the processes involved, such as multi-material 3D printing, can rapidly become intractable by simulation. Taken together, machine vision and AI will enable 3D printing to be widely adopted for production and not just prototyping.
3DN: Any future plans?
We will have some exciting news to share in the very near future. Keep watching Inkbit. You can find more information HERE
What do you think of Inkbit? Let us know what you think in a comment below or on our Facebook and Twitter pages! Don’t forget to sign up for our free weekly Newsletter, with all the latest news in 3D printing delivered straight to your inbox!