#3DStartup: Fluent Metal and its Powder- and Laser-Free Metal 3D Printing Technology
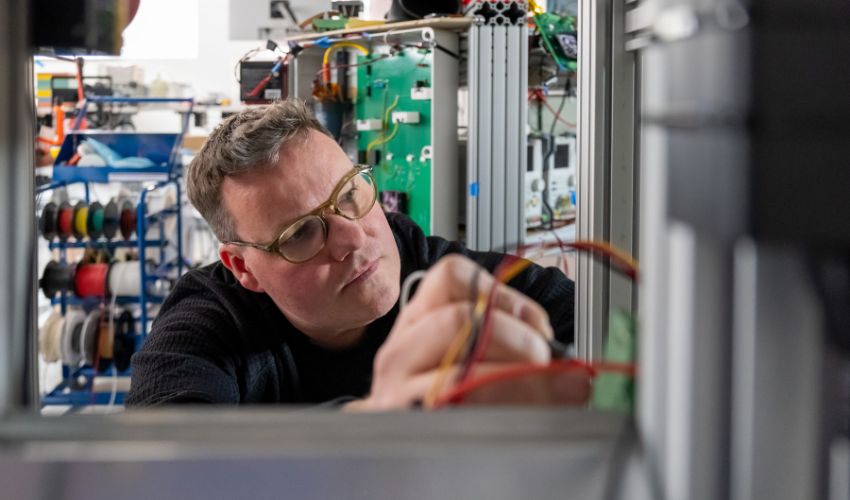
Metal additive manufacturing brings its share of benefits to the industry, with several processes, all of which are suited for different needs and constraints, falling under its umbrella. While powder-based processes are mainly favored by professionals, others are gaining ground. This month, we’d like to introduce you to a new metal 3D printing technique straight from the USA. Developed by Fluent Metal, this technology deposits metal droplets from an extremely fine wire. It is said to be compatible with a very wide variety of metals, therefore offering greater flexibility. To find out more, we spoke to Peter Schmitt, founder and CEO.
3DN: Could you introduce yourself and your connection with additive manufacturing? How did the idea for Fluent Metal come about?
Hello, my name is Peter Schmitt and I’m the founder and CEO of Fluent Metal. My link to additive manufacturing begins with an early interest in construction, building houses with my father and brother in Germany. Later, I took this drive to create physical structures and worked in sculpture, creating larger-than-life mechanical installations.
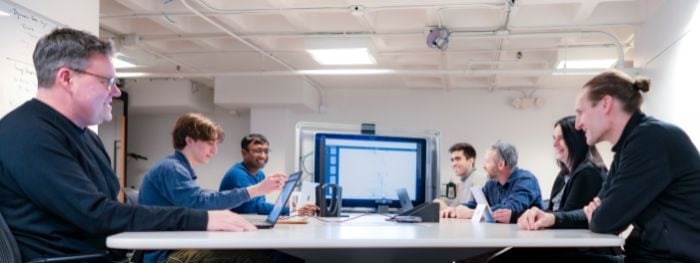
The Fluent Metal team
This path took me to the MIT Media Lab where I became more interested in the tools we were using, including additive manufacturing. After a number of different chief design officer roles, including at Desktop Metal, I saw an opportunity to approach the change of metal additive manufacturing in a novel manner, overcoming many of the challenges that limit the technology today. This is what we founded Fluent Metal to do.
3DN: Could you tell us more about Fluent Metal’s technology?
Our technology generates liquid metal droplets, directly from fine wire, about the width of a human hair. Those droplets are then deposited on-demand to build the designed part, similar to the inkjet approach. As mentioned, our feedstock is standard wire, which brings several advantages: it is easy to handle without the concern of health and safety issues and enables more efficient production without waste. On top of that, we have broad compatibility with various metals, from copper and silver to stainless steel and even tungsten. If the metal comes in wire, we can plug it into the equipment and start printing.
With our single-step process, we can build finished or near-finished parts without additional or major post-processing, of course depending on the requirements of the parts. Fluent Metal’s approach is designed to operate safely on a typical manufacturing floor or even in a prototyping shop, without the need for clean rooms or expensive safety measures. Additionally, material changeover is designed to be easy as plug&play, reducing setup efforts and allowing for higher machine uptimes, increasing overall production efficiency.
3DN: What are the main advantages of this process?
We’re taking a different approach than most of the current metal additive manufacturing companies– our approach is more sustainable, has a small footprint and can be operational in a regular workshop, and can use a much wider range of metals. Some of the advantages include:
Operational simplicity: With quick setup and material changeover, operating our technology requires low overhead and overall operative costs.
Broad material portfolio: Our process enables printing with most metals and alloys, including precious metals and refractories. If the metal comes in wire, we can plug it into the equipment and start printing.
Single-step process: We can build a finished part without additional or major post-processing.
Energy efficiency and no material waste: We enable highly sustainable end parts.
Highly scalable: Our system has the possibility to scale on demand, opening the door to high-volume production applications.
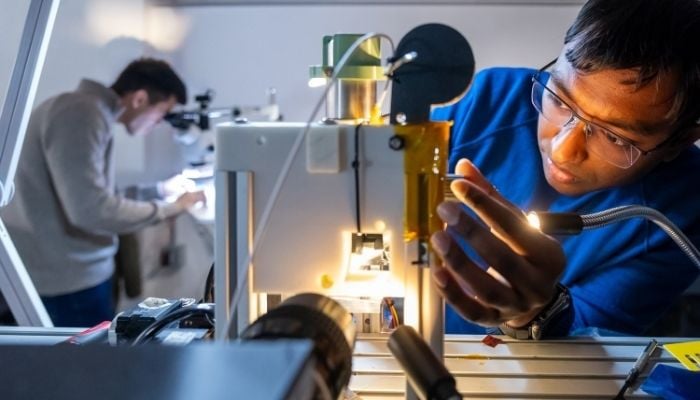
The Fluent Metal process has a number of benefits
3DN: Which sectors is Fluent Metal targeting?
In the near term, our intention is to spark the imagination of designers, engineers, and technologists to consider how rapid, on-demand production of custom metal parts could transform their capabilities. At scale, we think this approach has broad applicability across industrial manufacturing including defense, aerospace, mobility, and even consumer goods like jewelry.
3DN: Any last words for our readers?
There are already many existing metal manufacturing processes, but if you as an individual want metal parts, even if you just want to prototype something for a commercial application, you need to go to a specialist. It’s extremely difficult to get experimental or custom metal parts made.
Fluent empowers the creation of new tools and parts out of metal in a way that has never been available to individuals. At a grand scale, this changes the nature of metal manufacturing and could be a foundational technology that opens up unforeseen opportunities.You can find out more about the company HERE.
What do you think of Fluent Metal and its 3D printing technology? Let us know in a comment below or on our LinkedIn, Facebook, and Twitter pages! Don’t forget to sign up for our free weekly newsletter here for the latest 3D printing news straight to your inbox! You can also find all our videos on our YouTube channel.
*All Photo Credits: Fluent Metal
Fluent Metal’s technology represents a significant step forward in the field of metal 3D printing, especially in terms of safety, efficiency and flexibility.