#3DStartup: Balena and its Compostable, Biodegradable 3D Printing Materials for the Fashion Industry
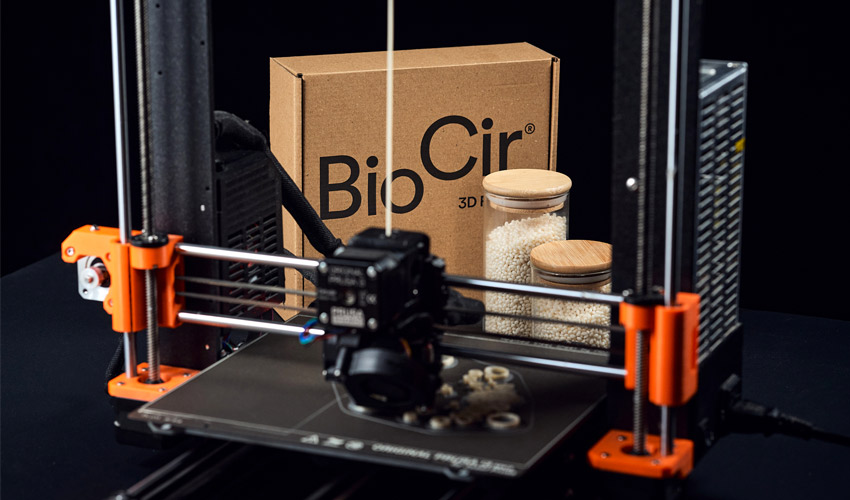
The fashion industry is one of the most polluting for our planet, consuming a lot of plastics which are unfortunately all too often thrown away too quickly and in the wrong way. Faced with this building ecological crisis, one young start-up has decided to develop a more sustainable solution to give a second life to our clothes and fashion accessories, Balena, an Israeli company founded in 2020. It develops compostable and recyclable thermoplastic materials, and has notably launched a solution for additive manufacturing. This is its BioCirFlex material, which can be found in filament or pellet form. We caught up with the company’s team to find out more about the characteristics of this polymer and how it could revolutionize the fashion industry.
3DN: Could you tell us more about Balena?
Balena is a materials science company dedicated to the development of compostable and biodegradable thermoplastic materials, founded by David Roubach. Balena’s mission is to create a circular model for consumer goods products and solve one of the fashion industry’s biggest challenges: the products’ end-of- life. David Roubach is a passionate advocate for sustainability and the circular economy, and he is committed to driving positive change in the industry by developing innovative and practical material solutions. Through his leadership of Balena, he is helping to transform the way we produce and consume fashion, and creating a better future for all of us.
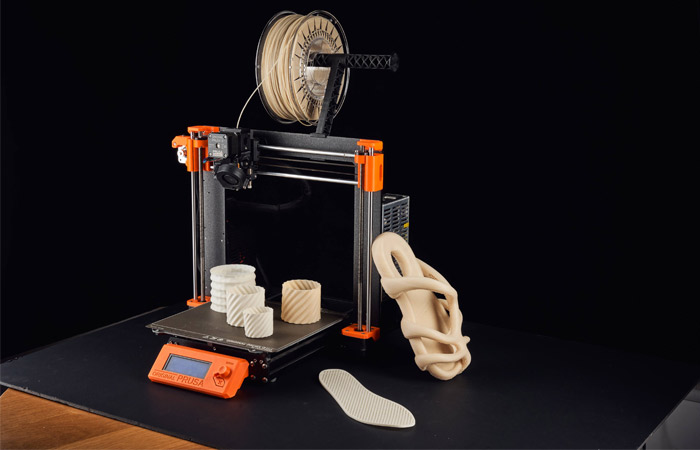
Balena develops compostable and biodegradable thermoplastic materials
3DN: How did the company get started?
Today, a whopping 60% of fashion garments are made out of plastic. In the US alone, over 21 billion pounds worth of garments reach their end of life and are sent to landfills or burnt every year. Out of which, only 1% is recycled. Currently, there isn’t a circular, end-of-life solution that can close the loop for these garments and solve the pollution caused to the earth and oceans. Additionally, while demand for bioplastics is ever-increasing, biodegradable polymers available in the market today are not advanced enough to include the features that conventional plastic materials include. Therefore, companies cannot fully replace hazardous, polluting plastics used in their products. Through the development of Balena’s flagship material, BioCir, we’ve created an opportunity to manufacture products that can be taken back at the end of their use and go through decomposition and biodegradation in a controlled compost environment without leaving any waste or contamination behind.
3DN: Could you tell us more about the materials Balena is developing for 3D printing?
BioCirFlex material is an advanced, bio-based, flexible and fully compostable thermoplastic material. With it, we hope to reduce the toxic, fossil fuel-based materials used in the fashion industry. BioCir™ can be used for mass production injection molding and for 3D printing using filaments or pellets. The unique combination of compostability and flexibility is what sets our BioCir apart from others in the 3D printing industry.
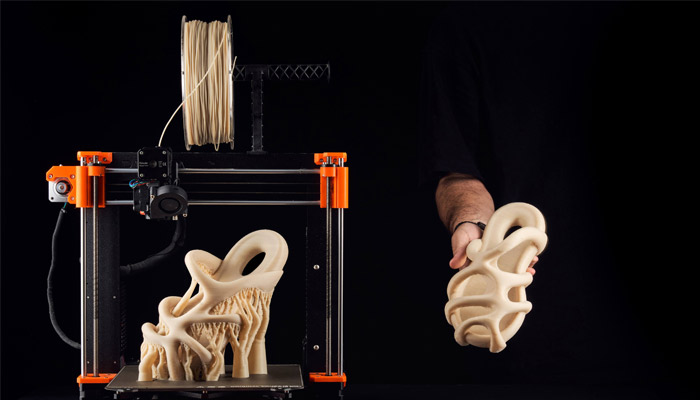
BioCir™ material is used in both injection molding and additive manufacturing, and is available in filament or pellet form.
3DN: How does BioCir meet the needs of the fashion industry?
The fashion industry is one of the most polluting industries in the world, with plastic such as PU, EVA and PVC being incorporated into clothing and becoming a core environmental issue that will affect our planet in the near and far future. This is the reason we have started off with targeting the fashion industry, as there isn’t a circular, end-of-life solution that can close the loop for these garments and solve the pollution and damage caused to the earth and oceans
3DN: Can you tell us more about the recently developed ROOTS concept?
We partnered with renowned stylist Kitty Shukman to create a unique 3D-printed sandal concept. As her name suggests, Kitty was inspired by tree roots and sought to reproduce their shapes and coils. The result is a tangle between upper and sole that mimics that of the roots beneath our feet. The ROOTS sandals were 3D printed with our filament, the aim being to create a circular, more sustainable product for the fashion industry.
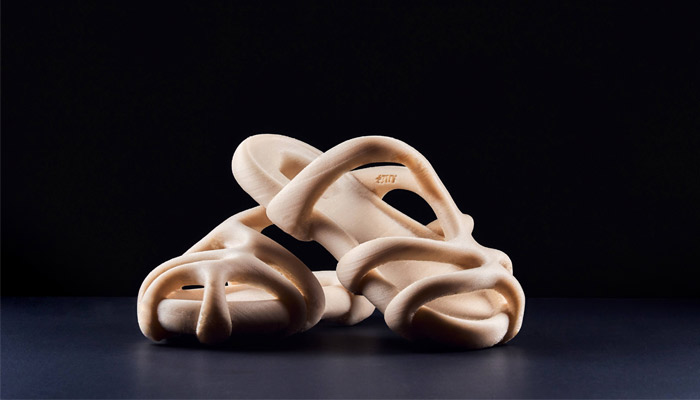
ROOTS sandals 3D printed with BioCir™ material.
3DN: What do you see as the link between additive manufacturing and the circular economy?
3D printing is transforming the fashion industry and paving the way for a more sustainable and circular economy. With its potential to reduce waste, optimize resource utilization, extend product life, and enable local production, 3D printing is opening up new possibilities for closed-loop manufacturing processes. However, the lack of suitable production-grade materials has limited the success of 3D printing in footwear production until recently.
The available materials were not able to meet the high-performance standards required for footwear production. However, a new generation of 3D printable materials that are friendly to footwear has emerged, including our BioCir material. It has been designed to meet the durability and flexibility standards required for footwear production, opening up new possibilities in the 3D-printed footwear production industry. Please visit our website HERE to learn more about us!
What do you think about Balena, our 3D startup of the month? Do you think it will revolutionize the fashion industry? Let us know in a comment below or on our LinkedIn, Facebook, and Twitter pages! Don’t forget to sign up for our free weekly Newsletter here, the latest 3D printing news straight to your inbox! You can also find all our videos on our YouTube channel.
*All Photo Credits: Balena