#3DStartup: AMFREE Overcomes the Constraints of XXL Metal 3D Printing
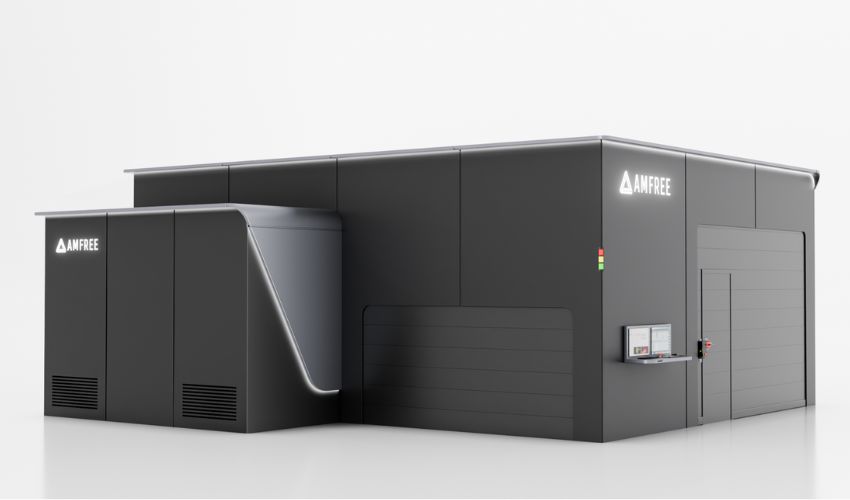
While metal additive manufacturing seems to be ever-expanding, the market still faces a number of challenges, particularly when it comes to producing and repairing large-format parts. The solutions available on the market are often unreliable, and the parts produced are either not compliant to regulations or too expensive. It is against this backdrop that French start-up AMFREE was born: it develops turnkey, pre-qualified XXL metal 3D printing hybrid solutions to facilitate the operator’s work and guarantee quality results. In particular, it relies on artificial intelligence to correct errors and learn from potential printing problems. We had the opportunity to meet Nicolas Villedary, the company’s Managing Director, to find out more about the technology used, the sectors targeted and the future plans of this ambitious start-up.
3DN: Could you introduce yourself and your connection to additive manufacturing?
Hello, my name is Nicolas Villedary and I’m the Managing Director of AMFREE, a company that markets metal 3D printers for the simple production and repair of large parts (up to 5 meters). These machines are distributed as turnkey, pre-qualified packages (machine, software, associated services), guaranteeing high quality production and ease of use.
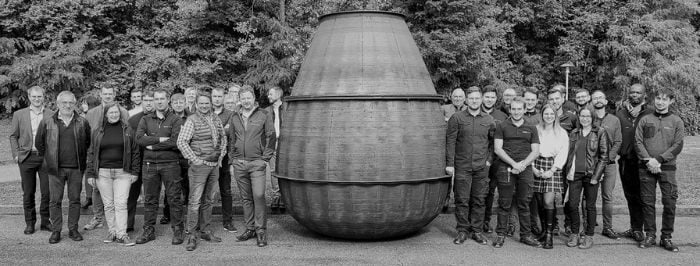
The AMFREE and IREPA LASER teams stand next to a 3D-printed XXL metal part
3DN: What is AMFREE? How did it come about?
Founded in August 2023 and based in Illkirch-Graffenstaden (Alsace, Bas-Rhin), AMFREE is a deep-tech startup that seeks to make metal additive manufacturing of large parts faster and more accessible. The technology was born in 2019 in the Alsatian CRT (Centre de Ressource Technologique) IREPA LASER. A pilot range has been set up and is already being used to qualify and produce industrial parts. At the same time, AMFREE has continued its R&D developments to develop new functionalities (3D scanning, machining, process control, intelligent sensors, etc.), the AI of its machines and its digital and service infrastructure.
We developed AMFREE based on the observation that the various additive manufacturing processes have their limits in terms of productivity and competitiveness. While some are gaining in precision, such as laser powder bed fusion (PBF) processes for complex parts, they are currently only suitable for designing parts a few tens of centimeters in length or diameter. These technologies are not suited to the manufacture of XXL parts that can reach several meters in length.
Today, the manufacture of large parts is more akin to craftsmanship. Production facilities are often special or “in-house” machines, with varying results from operator to operator, plant to plant, machine to machine. XXL parts are often critical, high value-added parts, or expose their users to significant financial damage when they become dysfunctional. Because they are not easily replaceable, and because they are critical to the industry, it was necessary to develop simple, affordable and economical standard machines, capable of producing parts more quickly (to reduce lead time) or putting them back into service (circular economy, eco-responsibility, resource and energy conservation).
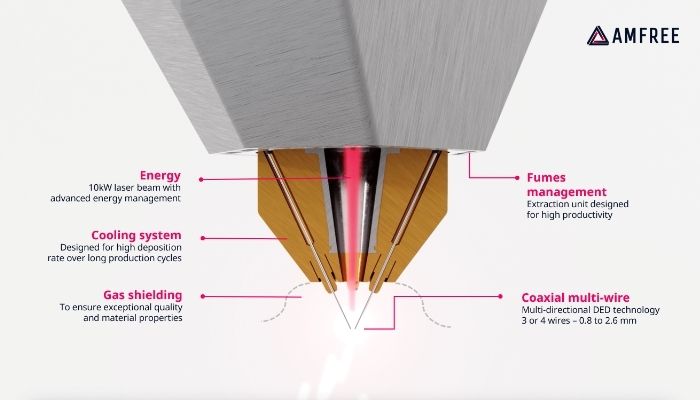
The machine uses multi-wire DED laser technology for dynamic energy management
3DN: What are the challenges involved in 3D printing large metal parts? How does AMFREE respond to these challenges?
For XXL parts, the challenge is to produce good parts on the first try. Parts are large, meaning non-conformities are often costly, and thus degrading the competitiveness of additive manufacturing.
To overcome this, AMFREE has chosen to provide a turnkey, pre-qualified solution. The result? Users are guaranteed to have all the equipment and software they need to manufacture XXL parts in conditions that have been adapted, validated and perfectly optimized. When purchasing a machine, AMFREE customers get everything they need, with no hidden costs, and 60 months’ expert support in materials and processes.
Furthermore, AMFREE machines are equipped with various specialized AIs that AMFREE improves day by day. As a result, all our machines benefit from new skills to help them master their craft and prevent poor quality. AMFREE is currently working on perfecting the process control of its machines, and is already interested in early anticipation of drifts to prevent them from occurring.
AMFREE’s service center works to qualify new materials and their associated AI, for industrial applications in many sectors (aeronautics, space, defense, industry, railways, tooling, O&G, nuclear, hydraulics, …), in partnership with various welding wire manufacturers. In this way, AMFREE’s technology can be used to guarantee the properties of fabrications/repairs. It also enables the development of innovative new materials and alloys for new applications (such as the O&G sector), through the simultaneous, controlled fusion of several wires of different types.
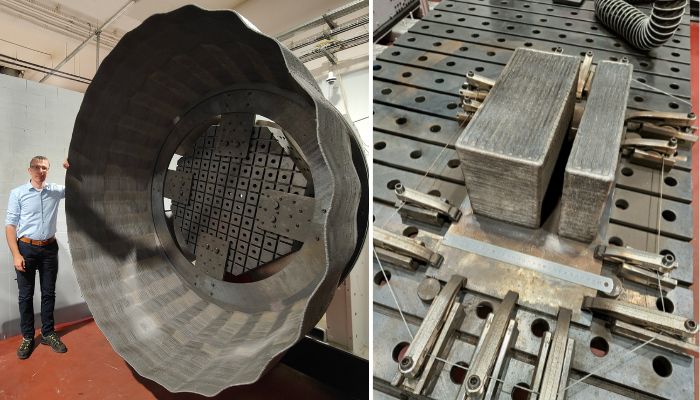
Examples of AMFREE 3D printed parts
3DN: Can you tell us more about your machine?
AMFREE has chosen laser-wire DED technology, because the use of a laser offers the possibility of precisely controlling the amount of energy applied, and of rapidly obtaining very high energy densities in a localized manner. To take this a step further, we have developed an innovative technology that enables us to achieve high wire deposition speeds, while controlling the geometric characteristics of the deposits and guaranteeing extreme metallurgical quality (often required for high value-added parts).
Our machines also use artificial intelligence to predict and correct unpredictable phenomena. Intelligent sensors developed by our teams are used for process monitoring. These data are processed by AI, which draws on all the data produced by the machine to correct any deviations before they lead to non-compliance, and ultimately to anticipate them so as to take preventive action and prevent them from occurring in the first place.
In its standard configuration, an AMFREE machine consists of a robot on a linear axis, carrying an AMFREE multi-wire laser nozzle. Adaptable on request, its initial manufacturing envelope is 5 x 2.5 x 2.5 m.
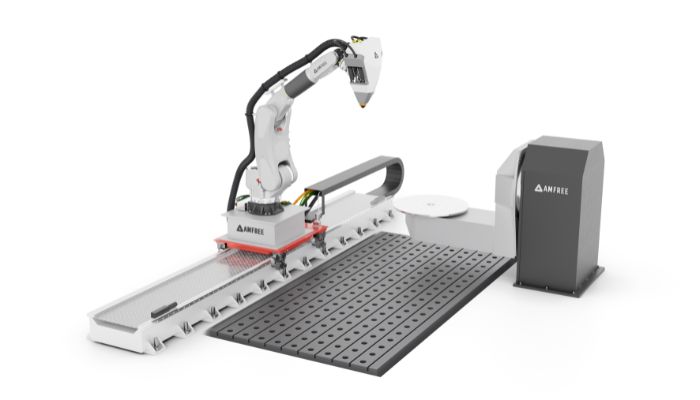
The standard AMFREE machine consists of a robot on a linear axis.
As an option, a positioner (for continuous multi-axis manufacturing), a sliding headstock (for cylindrical parts) or an additional robot can be added to incorporate 3D scanning or machining options for multi-process use. The idea is to place the part inside the machine enclosure and work around it (dimensional control, surface preparation, additive manufacturing, machining of inaccessible areas after manufacture, non-destructive testing). Furthermore, these machines make it possible to remanufacture parts close to final dimensions from simple spools (or drums) of wire, but they also enable the manufacturers who operate them to extend their market share to the world of repairs, and thus adopt a circular, virtuous and lucrative approach to manufacturing.
These machines are equipped with the latest Siemens Sinumerik ONE numerical controls. They inherit all the functionalities of the machining world. Fully instrumented, they are also adapted to new uses (communicating, 4.0, scalable, AI-enhanced machines, etc.).
3DN: Which sectors are you targeting? Do you have any projects in the works?
In Europe, we are targeting principals (the bridgeheads of industrial sectors), users of forging and casting parts, and maintenance companies.
Supported by the French government (BPI) and the Grand Est region, we are accelerating digital developments around the process (intelligent sensors, dynamic energy management) and the digital and service infrastructure behind the machines, designed to support future enhancements developed by the AMFREE service center. Work is also underway to qualify the performance of options available on AMFREE machines (3D scanning, machining), and to simplify the use of XXL additive manufacturing in all its forms.
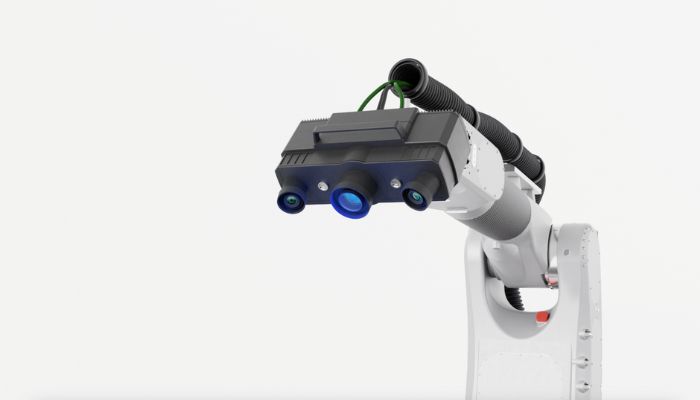
The machine can be optionally equipped with a 3D scanner or a machining spindle
We will soon be raising 2.5 million euros to strengthen our workforce, continue simplifying the architecture of our machines and their uses, and intensively promote this new, highly productive technology in Europe, with its potential that is still little-known by industry, and hitherto unexpected for large dimensions.
Finally, we plan to sell our first machine in 2024, with the aim of selling a dozen units by 2026, targeting sectors such as aerospace, energy, industry, O&G and defense.
3DN: Any last words for our readers?
We’re looking to forge strategic partnerships with various European manufacturers and technical centers, to popularize the technology and promote its still largely unknown assets. Please visit our website HERE to find out more!
*All Photo Credits: AMFREE