#3DStartup: 3devo, recycling plastic to make 3D printing filament
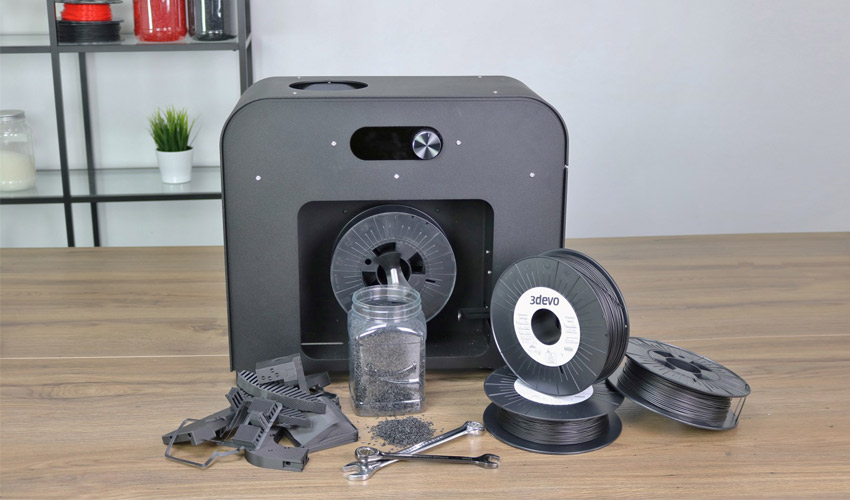
3devo is a Dutch startup created in 2016 that has developed three machines to recycle plastic and transform it into 3D printing filament. Therefore, it offers a real office solution based on the concept of a circular economy that enhances the value of waste and frees up the creativity of any user. 3devo offers a crusher that transforms plastic into granules; these granules can then feed the Filament Maker, a machine that creates customised filament reels; these filaments are then processed by Airid, a system that dries the filament to ensure optimal quality and flawless printing. We met Louis Rinaldo, startup materials specialist, to learn more about 3devo’s solutions and future projects.
3DN: Could you introduce yourself and 3devo?
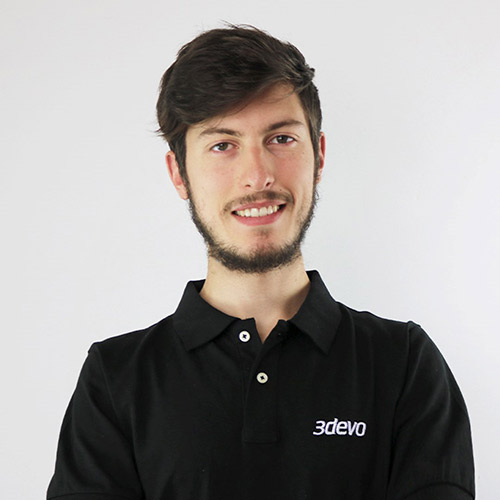
Louis Rinaldo
I am Louis Rinaldo, Material Specialist at 3devo. 3devo was founded in June 2016 by our CEO Tim Wesselink, with the help of young engineers. 3devo is a dynamic tech company which works closely with researchers and inventors, providing them with high quality equipment, expertise, with a friendly Dutch touch. We offer a complete desktop solution to manufacture all types of 3D printing filaments (even kinds that don’t exist yet).
3DN: Can you tell us more about the machines you manufacture?
We now manufacture 3 machines at 3devo. Our main product is the Filament Maker, which is a desktop sized complete filament production line. This machine gives anyone the ability to create spools of their own custom 3D-printing filament, starting from any thermoplastic pellets, powder or shredded material. Along with the fact that the machine is barely larger than a desktop 3D-printer, it is ideal for experimenting with new materials, fillers and additives. It was also designed to be as user-friendly as possible, while still achieving high quality filament production.
The second machine is the Shredder, called Shr3d It. While still being a desktop machine, it is extremely powerful and can shred any plastic into small flakes. The regrind can then directly be fed into the Filament Maker to make new recycled filament. The Shredder was created to close the loop, but of course the Filament Maker can also be used on its own to process virgin pellets.
Our latest addition to the cycle is the Dryer, called Airid. Most polymers need to be dried prior to being processed (extruded or printed). Unlike a conventional oven, 3devo’s Dryer removes all the moisture from plastics pellets, powders, or regrinds, very homogeneously, to make sure the batch can be safely fed into the Filament Maker.
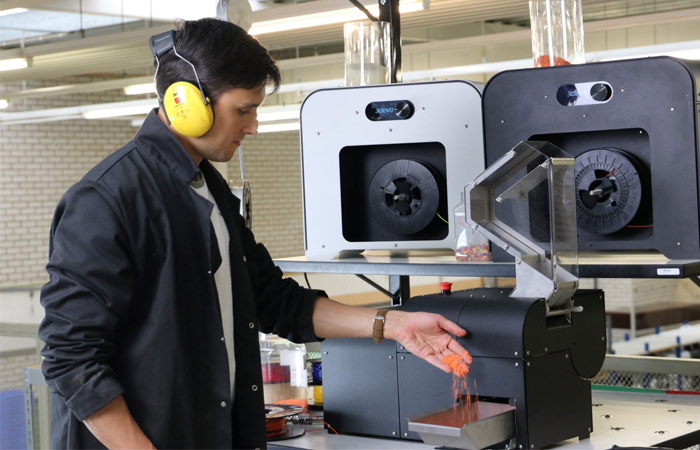
The shredder developed by the startup and the Filament Maker in the background | Credits: 3devo
3DN: Is it possible to recycle any plastic using your machines?
The answer is no, but the reason why, is interesting. Two main kinds of plastics exist: thermosets and thermoplastics. Thermosets can be given a solid shape once but cannot be remelted again afterwards. Think of a hard-boiled egg: the cooking process trapped it in its solid form, forever.
Thermoplastics however, are polymers which can be melted and solidified via heating and cooling. That is exactly what extrusion, injection molding, and 3D printing do: melting the polymer with heat and giving it a new shape (then cooling it down, of course). In theory, this can be repeated any number of times, which is why thermoplastics are recyclable, in addition to being printable.
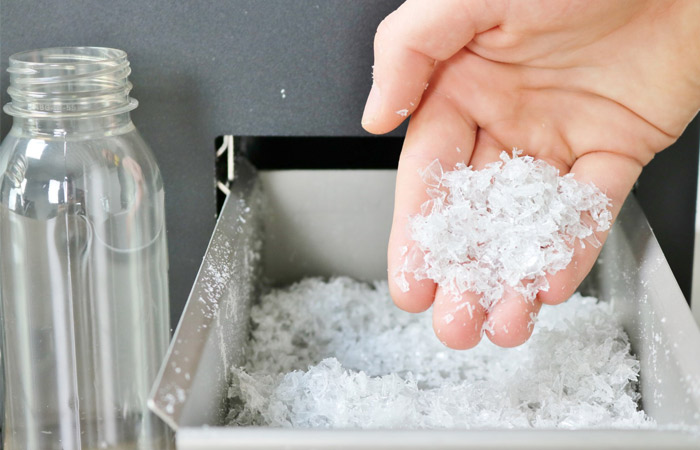
The machine transforms plastic waste into small flakes | Credits: 3devo
3DN: What challenges did you face to develop your products?
Extrusion is a well-known process in the plastic industry. The first challenge was to scale down the extrusion line to a compact, desktop solution. 3devo’s small Filament Maker can surprisingly process all kinds of plastic, from basic PLA to high end PEEK.
The second most important challenge was to guarantee the same filament quality (tolerance) as out of a big industrial extruder. Additive manufacturing relying on accuracy, bad quality filament has a very negative impact on the printed part’s properties and visual aspect. The solution was a smart quality sensor which can measure the thickness of the filament as it is spooled, and correct it where necessary to make sure it is kept tight within the tolerance.
The final challenge is an ongoing one: 3devo’s goal is to make filament making accessible to anyone, by spreading our knowledge and expertise. We thrive to become experts in the extrusion of all thermoplastics and recycling. We built up a large materials database using a hands-on experimental approach, and we now give extrusion trainings and share articles, sheets, reports, and more.
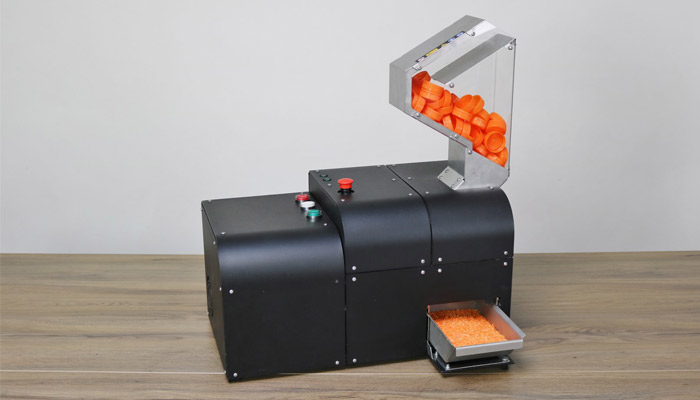
Credits: 3devo
3DN: Who are your customers today?
Most of our customers are innovators, creators, researchers: people and companies who want to manufacture custom filaments not found on the market and/or to recycle plastics.
FDM printing is shifting away from being just a prototyping method: high performance parts can now be printed out of an ever growing variety of polymers and composites, even for structural applications. The advantages of FDM over other printing techniques are its accessibility, and the fact that it can process all thermoplastics. The challenge is that plastics were originally designed to be injected. In order to research into new 3D printing applications, the plastic formulations must be optimised for filament extrusion and 3D printing. That is exactly what some of our customers are doing, at a lab scale first before bringing the process up the industrial notch.
It is easier to conduct an experiment with a small machine and 1kg of material, than on a production plant wasting half a ton every single trial.
3DN: Do you think 3D printing will play a part in environmental preservation?
Let me answer this question by giving the following example.
The ISS (International Space Station) is a limited space which offers a limited amount of resources to its users. This also applies to Earth. It is impossible for the astronauts to order parts from outside the system, and they have to rely on the materials already present in their environment. The only way to avoid running out of materials is to close the loop. It is possible to recycle all thermoplastics multiple times with little energy compared to metals.
Because 3D printing creates less waste than conventional manufacturing techniques, and because plastics are recyclable, this cycle could become the most sustainable way of making modern items. On the ISS, an astronaut would be able to print a hammer on Monday, and then convert it into a box on Tuesday. Also, 3D-printing gives the ability to manufacture only what you need, instead of mass-manufacturing the same parts where only half of them will ever be used.
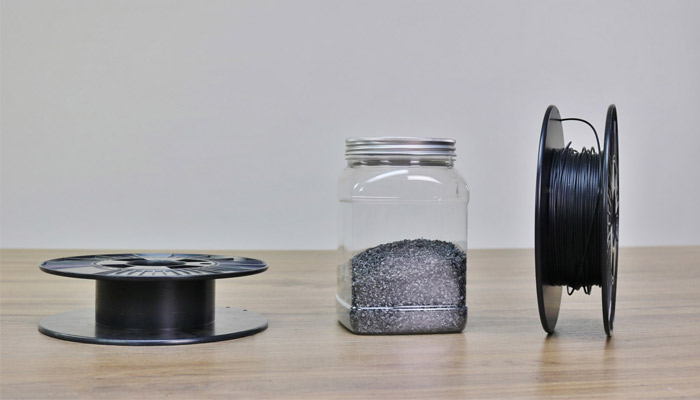
Credits: 3devo
3DN: A last word for our readers?
Do you want to manufacture a special part to answer a specific need? 3D printing has the shape covered. Extrusion is the key to the second half: the material. Filament extrusion will bring 3D printing up the final notch.
You can find more information HERE.
What do you think of our startup of the month, 3devo? Let us know in a comment below or on our Facebook and Twitter pages! Sign up for our free weekly Newsletter, all the latest news in 3D printing straight to your inbox!
I live in South Africa where recycling processes is not as developed as in Europe. How much would a set of yr machines cost?
Hello
we are a small NGO , that helps refugees camps in north of Mozambique.
we are looking to manufacture squatting pan toilets with recycled plastic.
is this possible, can you provides a machine 3d printer to do this ?
best regards
00258848966504