#3DStartup BIO INX on the Development of Innovative Bio Inks for 3D Printing
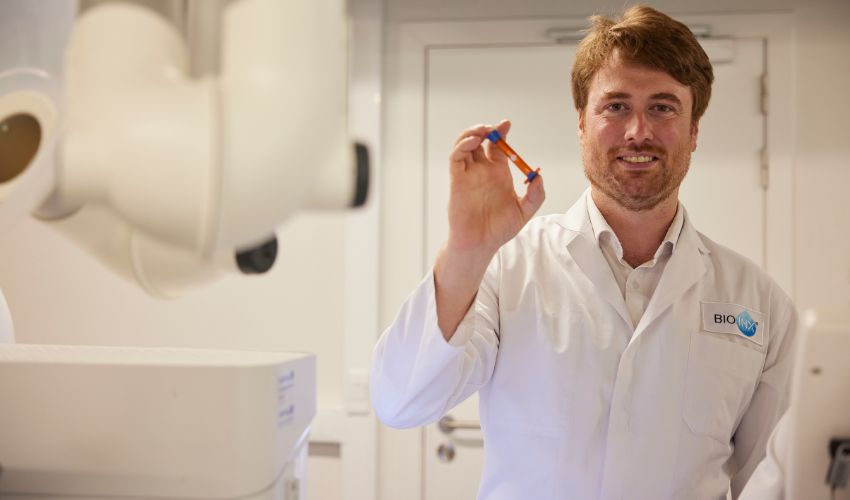
When will we be able to print usable organs? That is probably the question most often asked in connection with 3D bioprinting. And we have regularly reported on groundbreaking progress in this direction. For example, there are exciting projects to print neural networks, bioactive bone structures, wound-healing bio-inks and many more. Indeed, bioprinting is a major interest for the scientific community, but it’s also a business. According to a report by Markets and Markets, the 3D bioprinting market is expected to reach $3.3 billion by 2027, up from about 2 billion in 2022. This underscores the numerous researches on new processes and bio-inks to continue making profitable discoveries and driving revolutionary developments.
However, to print organs, muscles and tissues, the necessary cellular material is needed: bio-inks that can be used in additive manufacturing processes. One company that specializes in the production of such bio inks is BIO INX. The Belgian startup is engaged in the development of innovative and high-performance inks to push biofabrication and its applications. In the interview with CEO Jasper Van Hoorick, we learned more about the founding of the company and the exciting projects BIO INX is working on.
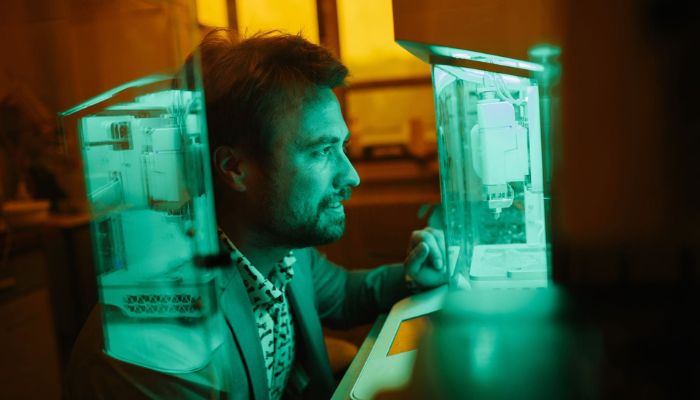
Jasper Van Hoorick, CEO at BIO INX
3DN: Could you introduce yourself and tell us how you got into 3D printing?
I am Jasper Van Hoorick, CEO and cofounder of BIO INX. I got into 3D (bio)printing during my PhD at Ghent University and Vrije Universiteit Brussel. During my masters and subsequent PhD (in chemistry and engineering) I was working on the development of new biocompatible materials (i.e. Gelatin and Polyesters) for 3D bioprinting technologies, more specifically two-photon polymerization, which is a high resolution laser based 3D printing technology. It was during my master’s that I got fascinated by the field of 3D bioprinting and decided to pursue a PhD in it as well.
3DN: How did the idea for BIO INX come about and what is the company currently working on?
During our (i.e. me and our CSO Aysu Arslan) PhDs, we developed new materials for 3D bioprinting, which we also managed to patent. BIO INX originated from this work and patented technologies/materials. As material chemists, we had a lot of collaborations with research groups focusing on applications of these materials for regenerative medicine applications. One of these collaborations was with the research group of Aleks Ovsianikov in Vienna, where Agnes Dobos (application specialist at BIO INX) was doing her PhD. This made us think, what happens with the research of these partners if the materials are no longer available? What’s more, if promising research is performed with materials produced in an academic research setting, you will have to start from scratch if you ever want to bring this closer to the patients due to reproducibility issues.
Feeling the research of our PhDs had a lot of potential, we did not want it to die in academia or not make it further than something with ‘great potential’ in research papers. To take the research beyond academia and closer to the actual clinics, it requires someone to actively take this research to the next stage. This is the reason why we decided to apply for funding to explore spin-off creation and commercialization of our technology.
Therefore, we applied for some grants to explore spin off creation. Here, we were strongly supported by An Van Den Bulcke, business developer at UGent who also originally developed gel-ma, one of the most popular materials in the 3D bioprinting world. This somehow feels like the circle is round, as gel-ma forms the basis of a lot of biofabrication research in the last 20 years, making it very suitable that An supported with BIO INX creation where we also supply gelatin based materials. So after 2 years of university incubation, we launched BIO INX in April 2022. With BIO INX, we want to offer reliable and standardized bioinks, which enable printing of cells with unprecedented resolutions.
3DN: Why can’t one and the same bio ink be used for each technology? Could you explain what properties bio inks need to have for each technology?
Every technology relies on different characteristics for printing. Extrusion printing requires a very controlled flow of material, and especially a good shape fixation after printing. For this the crucial properties for a high performing bioink are related to viscosity and flow of the material. In other words, the rheological properties. For light-based printing, the photocuring properties are of predominant importance. Here fast curing reactions are preferred. However, these curing (i.e. photocrosslinking) reactions need to occur in a biocompatible way, not damaging the cells during crosslinking. For 2PP printing, there is a need for very specific two-photon photoinitiating systems, which are very active at the used wavelength (mostly near infrared or 780 nm), which can be very tricky. For DLP (digital light projection) printing, it is important that the penetration depth of the light within the material is limited to confine the photocuring reaction. Which again requires different photoactive systems than for 2PP printing.
In this respect, bioinks for these three technologies can rely on similar polymer materials but can still have completely different compositions to comply with the specific printing tech requirements. What’s more, bioinks do not only need to comply to these technical requirements, but also need to exhibit biocompatible behavior towards different celltypes. This tricky balance makes bioink development very interesting.
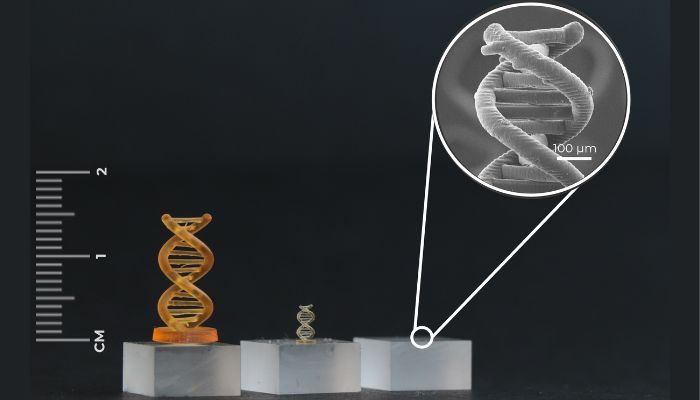
Multiscale hydrogel in the micrometer range.
3DN: What projects are you currently working on at BIO INX?
We are currently involved in 2 large projects. One is HU3DINKS where we are working on the generation of human placenta based bioinks as an alternative to animal derived materials such as gelatin. This is an international project with different project partners from Austria including THT biomaterials, Morphomed, Upnano and the Ludwig Boltzam institute for Traumatology and is supported financially by both VLAIO (Flanders) and FFG (Austria). With this project we aim not only to make inks which not only form a better mimic of the natural tissue, but also do so in an animal-free way, thereby assisting in the 3R principle of animal-based studies (Refine, reduce and replace).
Another big project we are working on is Astrocardia, where we are 3D printing cardiac tissue inside a microfluidic chip using 2PP printing. Next, this chip will be sent to space to study the effect of ageing on the cardiac cells, because it is known from literature that there is a factor 20 increase in ageing in space in comparison to earth. By sending 3D printed vascularized heart on chip models to space, we will be able to study the effect of ageing on the heart cells, as ageing is one of the reasons for heart issues occurring. This ageing effect is something which is difficult to manage. This project is a collaboration of multiple Flemish companies including SCK CEN, Space Application Services, Antleron and QBD and supported by VLAIO, Medvia and Flanders Space. The launch of the self-contained chip systems is planned for 2025.
Apart from these projects, we are also involved in some custom research projects for customers and we are developing our Curasol technology. The Curasol technology is one of our patented technologies which enables curing of some of our materials in the solid state with high efficiency, in the absence of any solvent. This enables extrusion printing of thermoplast materials from the melt, followed by photocuring turning them into thermostets with unique properties including unprecedented elasticity and shape memory behavior.
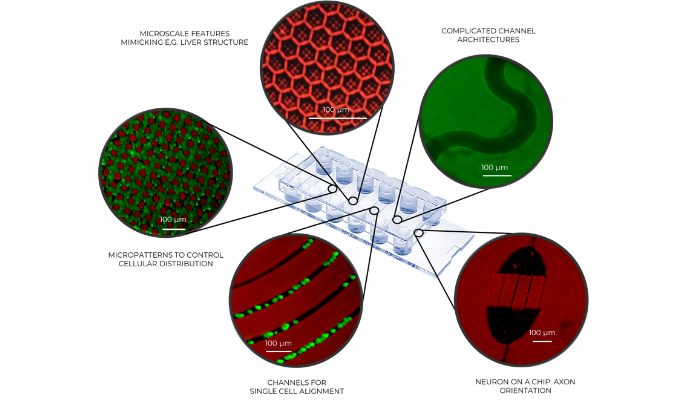
2PP can be used to produce microfluidic chips.
3DN: You had already mentioned Two Photon Polymerization and its application in bioprinting. What are the opportunities and limits of 2PP technology?
The main benefit of 2PP printing technology is that it is the only technology which allows printing at subcellular dimensions, thereby making it possible to recapitulate the complex architecture of living tissues which is of crucial importance for tissue function. Additionally, it is the only technology which enables straightforward printing of structures within microfluidic chips to create organ on chips for drug and cosmetics screening applications. The technology has made huge leaps in the last 10 years in terms of printing speed and maximally obtainable object size. However despite the fast writing speeds (i.e. meters/second) printing of large structures still takes a considerable amount of time due to the extreme high resolution of the technology in combination with the scanning principle of the laser.
3DN: Where do you see 3D bioprinting in the next 5 to 10 years? What steps are necessary to push 3D bioprinting to the next level?
We believe that the technology is close to its tipping point from research to application. However, the main bottleneck in my opinion is the unclear regulatory pathway, especially when also living cells are involved during printing. But what is crucial in this respect is to have a guaranteed quality and reproducibility of all aspects including materials, printing processes, cell culture etc. Standardization and reproducibility are the way to clinical applications. Albeit, we believe that the first tissues will not be fully functioning human organs but start with “simple” straightforward tissues including cartilage, bone ore cornea tissues (i.e. Avascular tissues). etc. Especially tissues not requiring vasculature.
However, in order to get there, standardization of every step along the way is crucial, including standardized bioinks. And this is exactly the motivation that pushed us towards the incorporation of BIO INX. Biofabrication is a very exciting field to be working in. There are a lot of exciting things happening in the market currently, and the science is advancing rapidly. Therefore, we are very happy to contribute our small piece to the dream of 3D printed tissues and organs.
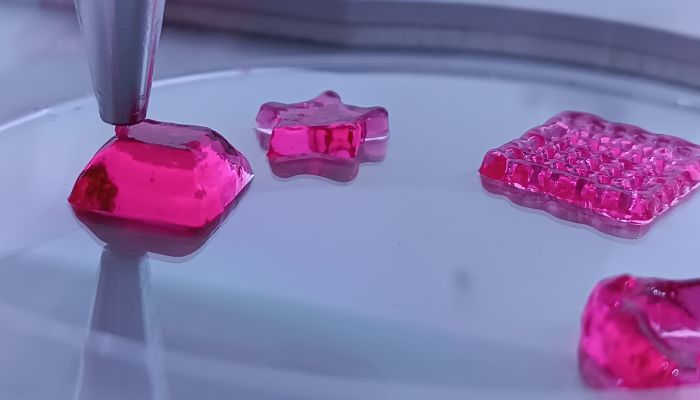
Standardization is needed to drive biofabrication forward.
What do you think about BIO INX, our 3D startup of the month? Do you think it will revolutionize the fashion industry? Let us know in a comment below or on our LinkedIn, Facebook, and Twitter pages! Don’t forget to sign up for our free weekly Newsletter here, the latest 3D printing news straight to your inbox! You can also find all our videos on our YouTube channel.
*All Photo Credits: BIO INX