3Dnatives Lab: Testing the DF2+ 3D Printer from RAISE3D
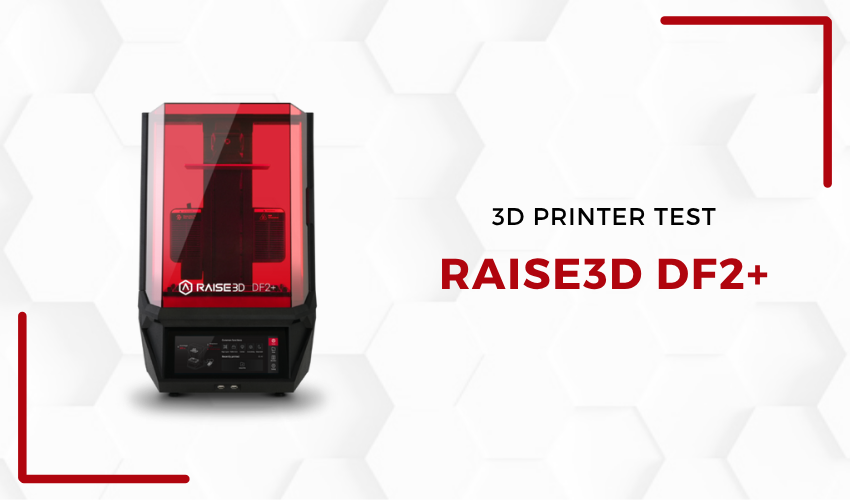
Previously known for its FDM 3D printers, Raise3D continues to diversify into new additive manufacturing technologies. In 2023, the manufacturer launched the DF2, its first resin 3D printer, unveiled at Formnext. Less than two years later, it is back with an updated version, the DF2+, which retains most of the design and user experience of the original model, but with one major improvement: a new, more powerful light source, compatible with a wider range of materials, including technical resins.
This test focuses on the DF2+, a machine designed for professionals looking for reliability, precision and a smooth workflow, from slicing to post-processing. This model is clearly part of a strategy to move upmarket and consolidate Raise3D’s professional offering, now extended to three major technologies: FDM, resin (DLP) and, most recently, SLS. A Raise3D SLS printer has indeed been announced, and we’ll have the opportunity to test it soon in the 3Dnatives Lab.
Unpacking
The DF2+ is neatly packaged, reflecting the machine’s professional positioning. The printer itself is voluminous, with a futuristic design that I’d even describe as almost Martian-inspired. It is ideally accompanied by two dedicated post-processing machines: a washing station and a curing station, sold separately, but which play an essential role in the ecosystem imagined by Raise3D.
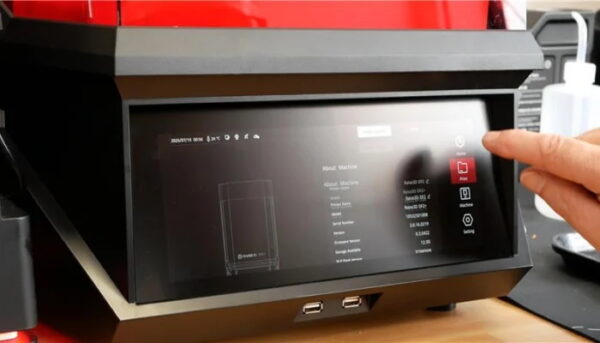
The large touchscreen on the front provides a good control experience.
One of the first eye-catching features is the imposing front panel touchscreen. Large, bright and well-defined, it immediately gives an impression of quality. This feeling is reinforced by the overall construction of the machine, which exudes solidity.
Installation and Start-Up
Getting the DF2+ up and running presents no major difficulties. Once the printer has been installed and connected, the touchscreen interface guides you through the first steps: automatic build platform calibration, component verification, network configuration, etc. Navigating the menus takes a little getting used to, and some functions are a little hidden, but you’ll soon get the hang of it.
In terms of ergonomics, we appreciate the screen’s responsiveness, even if the organization of parameters could sometimes be made clearer. It’s not always easy to find your way around at first, especially when adjusting certain print settings or accessing advanced parameters. That said, once you get the hang of it, the whole thing is generally well thought out.
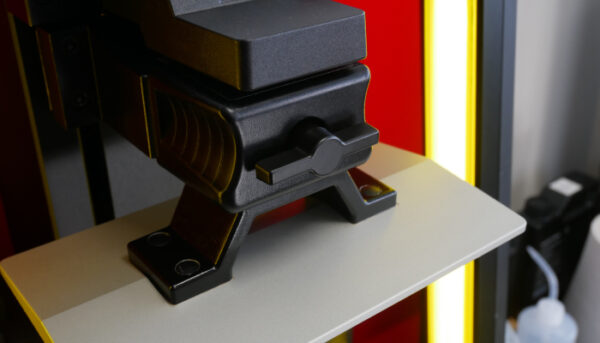
The DF2+’s print bed locks automatically, but a key included with the printer also allows manual control.
A small detail to note, but one that may be important in everyday use: the printer, as well as the post-processing stations, emit numerous beeps when navigating the menus. It is possible to deactivate the beeps, but on post-processing machines, they persist at start-up. What’s more, the printer’s LED ribbons blink when printing is complete, until the operator intervenes – an annoying little detail when launching a print job for the weekend, for example.
Software and Applications
Raise3D accompanies its printers with its own slicer, IdeaMaker, well known to the brand’s users for FDM machines. Here, it has been adapted for resin printing, with a slightly reworked interface and specific profiles. The overall experience is positive: options are numerous, automatic supports are well generated, and print parameters are advanced enough for experienced users.
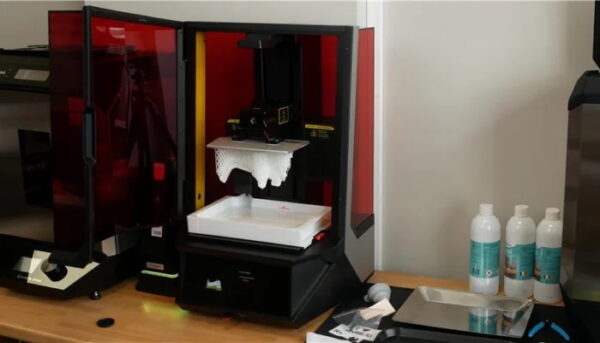
The Raise3D DF2+ can be connected remotely using the Raise3D Cloud, accessible via the web or ideaMaker.
In parallel, Raise3D also offers its RaiseCloud cloud platform for remote print management and fleet supervision. However, at the time of testing, the DF2+ was not yet fully integrated with this platform, which limits the cloud’s interest in this machine for the time being. We imagine that a software update will fill this gap in the near future.
Finally, a mobile application is also available for managing the printer, but it is still very much focused on the use of FDM machines and leaves much to be desired when it comes to use with a resin printer.
First Impressions
During this test, I used several types of resin offered by Raise3D: a standard resin, a High Detail resin, and a more technical Tough 2K resin. In all cases, the quality of the results was highly satisfactory. Prints show excellent definition, with very few visible layers, and crisp detail, especially with the High Detail resin, which enables very fine geometries to be captured with precision.
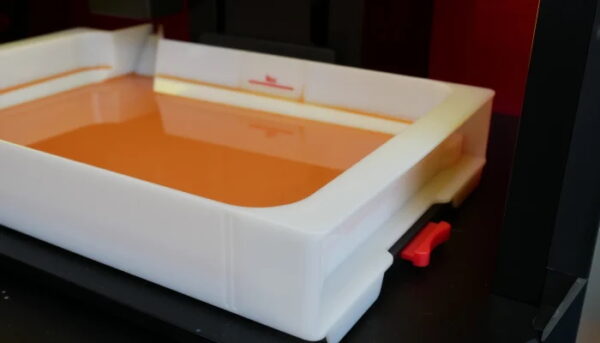
The resin tank (vat) can be removed and reinstalled in just a few moments using fixing clips.
The stability of the print is also impressive: no failures were observed during my tests, and the machine proved to be consistent across all the prints I made. This lends credence to the idea of a product designed to meet professional requirements.
That said, not everything is perfect. I’ve noticed that parts tend to adhere strongly to the build platform, sometimes even a little too much. Removing parts can be tricky, especially for thin bases or delicate substrates, which can break during lift-off. This phenomenon seems to be mainly due to overexposure of the first layers, which is not uncommon on resin printers. Raise3D could improve this aspect by offering better optimized base profiles or more detailed recommendations for adjusting exposure according to resin types.
Another area for improvement is the resin feeding system. While auto-feeding works well once in place, the installation procedure is a little restrictive. First, you have to manually pour a small amount of resin into the tank, then place the cartridge on the external dispensing station. If the resin is changed, the hose and pump must be replaced to avoid cross-contamination. This adds to day-to-day management, all the more so as a system integrated directly into the printer, as seen with other manufacturers, could have simplified this operation.
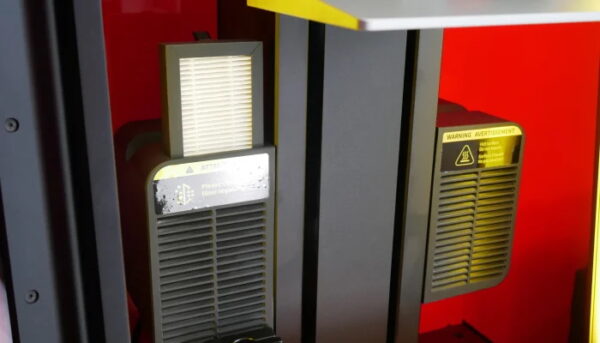
The DF2+’s internal filter helps reduce resin odors and fumes, although it is still important to use the printer in a well-ventilated area.
Another shortcoming, more annoying depending on the context of use, is the absence of a function to resume printing in the event of a power cut or machine shutdown. If the printer shuts down during a job, whether intentionally or not, it will detect that printing has been interrupted when it restarts. However, instead of proposing a restart, it simply asks you to remove the part and clean the build platform, thus ending the process. In certain professional environments, where electrical interruptions can occur, this can represent a real limitation.
Finally, it’s worth noting that the printer emits several beeps when navigating through the menus. While some sounds can be deactivated, others, such as those at start-up, remain present. This is not inhibitive, but it can be a little intrusive, especially in quiet environments or when the printer is running outside office hours.
Workflow and Post-Processing
The workflow offered by Raise3D with the DF2+ is clearly one of its strong points. The logic of the ecosystem is fluid, coherent and well thought-out for professional environments. Once a print job is finished, simply transfer the tray to the dedicated DF-Wash wash station. Thanks to an RFID reading system, the station automatically identifies the parameters linked to the resin used and triggers an appropriate cleaning cycle, without the need for manual adjustments.
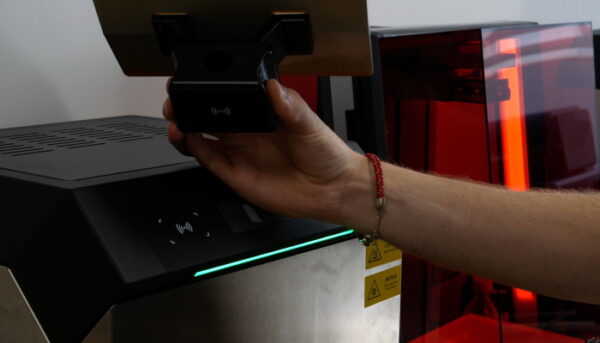
The workflow is greatly simplified by the use of RFID chips for material identification and semi-automation of post-processing.
DF-Wash also incorporates an automatic isopropyl alcohol drainage system via a secondary tank designed for this purpose. This feature relies on a resistance sensor to prevent overflow. If the liquid level in the tank is too high, the system automatically switches off the drainage. This little addition facilitates maintenance while enhancing user safety.
After washing, the tray can be transferred to the DF-Cure polymerization station, which also automatically detects the necessary parameters thanks to RFID technology. The post-polymerization cycle is then started automatically, guaranteeing curing adapted to the resin used, without the need for operator intervention.
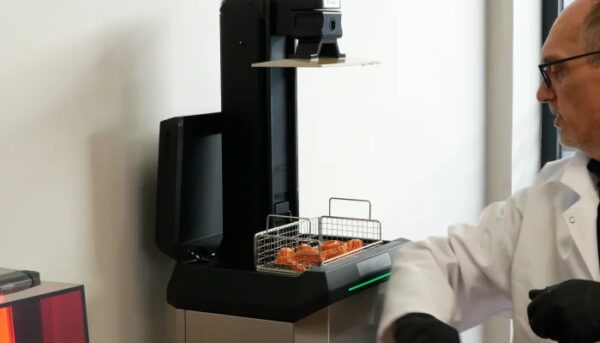
The post-treatment stations have sensors allowing automatic opening and closing by simply pressing the elbow.
In addition to this appreciable automation, both post-processing stations feature a touch-free opening system that can be activated by hand or elbow, which is particularly practical when wearing resin-covered gloves. This attention to ergonomics and hygiene contributes to a good user experience, particularly in professional environments where handling must be reduced to a strict minimum.
Finally, when a print is complete, the printer signals the end of the process by the continuous flashing of its LED ribbons. While this makes it easy to spot a finished part, it becomes a little annoying when printing is started at the end of the day or on weekends, as the LEDs continue to flash until the user intervenes manually.
The machine plus post-processing package forms a coherent solution that simplifies the daily workflow while maintaining high quality standards, which is exactly what professionals expect.
Conclusion
- 3D Printer Contents 8.5/10
- Software 9.5/10
- Print Quality 9.5/10
- Getting Started 9.5/10
Pros:
- Complete ecosystem with automated post-processing stations / RFID on the tray to simplify steps
- Large, comfortable touch screen.
Cons:
- Resin supply system not integrated;
- Documentation still too basic.
With the DF2+, Raise3D confirms its determination to make its mark on the resin 3D printing market. More than just an updated model, the DF2+ represents a strategic evolution in the brand’s ecosystem, which now seeks to cover all major additive manufacturing technologies.
The DF2+ stands out for its print quality, its compatibility with technical materials thanks to its new light source, and above all for its automated, intelligent workflow, which makes everyday life easier for professional users. Software ergonomics, though still improvable, is convincing overall, and the machine + post-processing package forms a coherent solution.
A few points remain to be addressed: the sometimes excessive adhesion of parts to the platen, the perfectible resin feed system, and the current lack of full compatibility with RaiseCloud. But all in all, this DF2+ stands out as a serious, robust, well-thought-out resin solution for demanding workshops.
To learn more about the Raise3D DF2+, visit their website HERE.