3DM on Developing a Faster, More Optimized SLS 3D Printing In Order to Scale Up Production
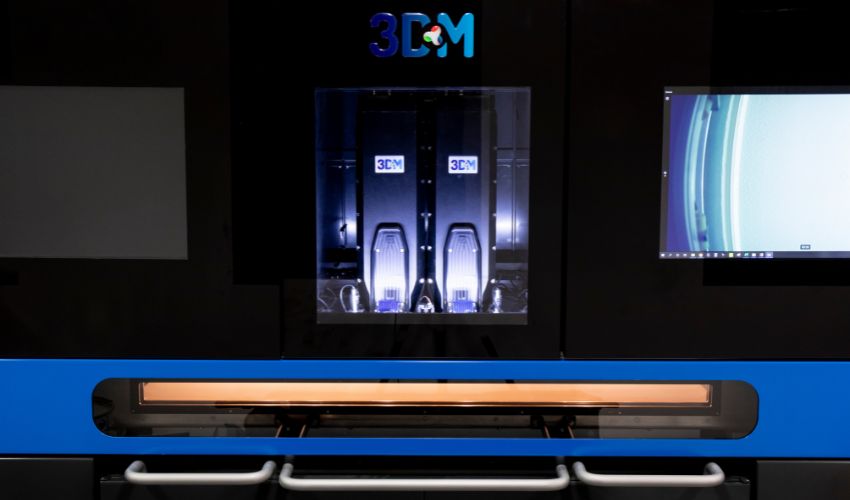
3D printing has come a long way since its origins in the 1980s. Though originally used almost exclusively for rapid prototyping, over the past few years we have seen additive manufacturing technologies rapidly industrialize and be used for end-use parts in a number of industries. But many questions remain on the scalability of the processes especially as it comes to production. Luckily, we are seeing increasing innovation to address these obstacles. One such company is 3DM which has developed its own printhead technology based on a parallel laser beam approach. With this solution, it is possible to accelerate printing speed and throughput while increasing printing resolution specifically with SLS 3D printing. We spoke to Ido Eylon, the CEO, to learn more.
3DN: Could you introduce yourself and 3DM?
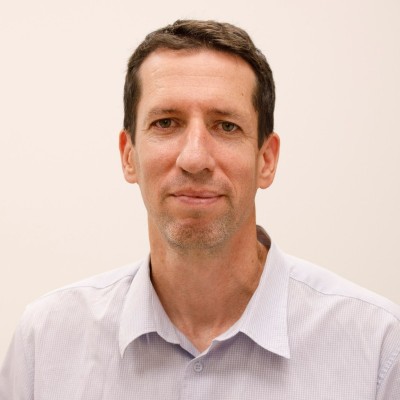
Ido Eylon, CEO of 3DM
My name is Ido, I am the CEO of 3DM and have been for the past year. Before that, I worked for companies in the AM industry. In my previous role I was the VP of sales and marketing of Massivit which I did for three years. And before that I worked almost a decade with Stratasys, moving over when the merger between Stratasys and Objet happened. I started with a more technical role and was a manager for the applications team in Israel when I started. It’s important to mention because this is how I developed my understanding of what makes sense to do with the technology, and also what not to do with it. After a couple of years, I moved to the US and was the applications and pre-sales manager for North America and was in a role where I could move closer to the customers and the use cases mentioned while gaining more exposure to the business side of the industry. I then went to Singapore to open up a business unit there and was the business manager for South Asia and my last significant role was the VP of Sales for Asia Pacific. In total three and half years in Singapore, where I got exposure in terms of the commercial, business, applications, use cases and different places.
Just before moving to 3DM, I was quite excited about the movement of the industry from “rapid prototyping” to industrial and I’ve identified in 3DM a way to get into this. SLS in general is one of the technologies that is key for high volume production usage, that means production that is in the up to 10,000s of parts. That is where 3DM comes in as a way to take SLS, which already has very high capabilities in the field, and push it even further.
3DM meanwhile was founded by Dr. Daniel Majer who holds a PhD in physics from the Weizmann Institute of Science in Israel. He is an expert in lasers and before founding 3DM he was already leading companies in the field. He built the first prototype for 3DM with his own two hands and raised some money from an incubator in Israel and the company started to grow and progress. Actually, we went public in Tel Aviv about 2 years ago raising some more capital and continuing the development process and now we are on the verge of commercialization. We expect in the next few months that we’ll have our first few beta units out in the field.
3DN: 3DM has a unique take on SLS 3D printing. Could you tell us about the technology?
Before getting into our specific solution, it is important to answer the question, why SLS? Even non-optimized SLS is the technology that is showing the most promise in terms of true industrial production with 3D printing. This is thanks to its very nature where you can create many quality parts at once as well as customize. However, it still has its own challenges which we are aiming to address with our solution.
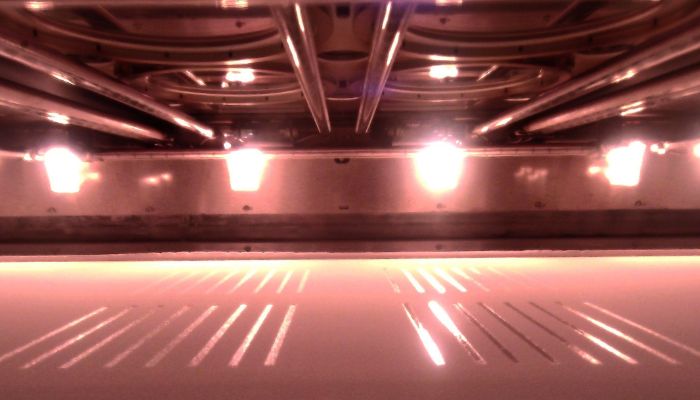
The 3DM printing process
This starts notably at the lasers. We have our own QCL lasers which we have developed and the most important unique point of these lasers is that they are designed, planned and manufactured for optimized plastic melting. We don’t just take a CO2 or fiber laser off the shelf nor are we just making adjustments while limiting the range of materials that are possible. Instead, our lasers work with us analyzing the desired material and then tuning the lasers to melt the material at the required wavelength.
To understand how it works, I ask you first to consider a FTIR (Fourier Transform Infrared Spectroscopy) analysis. These are often used in a number of different scientific domains, for example to check the quality of food products or to find prohibited materials or explosives. And essentially, it shows what wavelengths will interact well together with the intended material. This is where our founder started in order to create our own technology.
Every material has a specific wavelength or a few wavelengths that are most efficient for melting. Looking at an FTIR you can see it directly because there are peaks and the goal is to be close to this peak as possible for the material to react in the desired way. But if you are using a CO2 laser, they will always be at 10.6 microns and if the material absorbs enough, it will melt or not, but it is not optimal. Alternatively, you can go with a higher power laser but then you need to pay for it in other ways. So, there’s never really a point where the laser itself has been optimized for each material. And that is where we come in, seeing how the different materials react to different wavelengths.
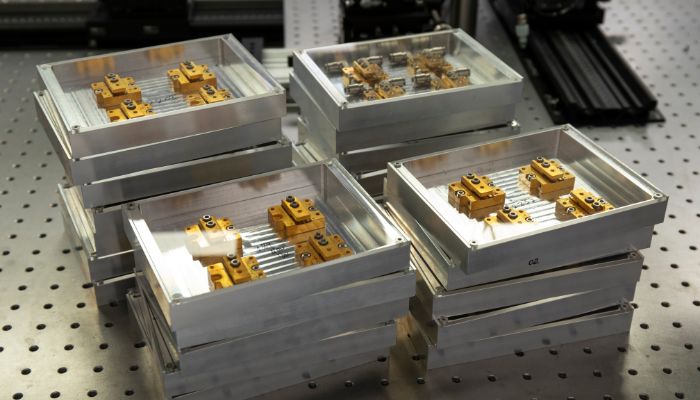
The four lasers are paired in couples
Once we have understanding, we start fabricating the chip, which is very small, only half a millimeter wide & ~5mm long, and that will emit light between 2–3 watts, very strong for the laser of this size. Then, you put this chip on the cooling device to make the first optics element and then build up to create the laser module. Ultimately, we take four of those, potentially more, and they are combined to increase power and capabilities. In this beam head, all the lasers are combined and focused to one beam and this will create the spot on the powder.
Moreover, with the beam heads, the technology is truly scalable. In one solution, it is possible to have four beam heads, each with four of these lasers that are arranged in couples, with each one set to its own wavelength. This is the ideal set-up for industry and the machine itself is large as well. Then with these lasers, theoretically we can melt any thermoplastic. Right now, we mostly use all the materials available for 3D printing but we are confident that as we ourselves grow, we will be able to print in the future also with materials that no others can.
3DN: What are the benefits of this unique technology from 3DM?
It has quite a few benefits beyond the vast applications available as well as the wide range of materials that are possible. I’ll mention notably higher printing speed, lower costs and an open platform. Additionally, even with all that, we can still guarantee the mechanical properties of the printed part since we can see how the wavelengths will react and ensure that the final part has the desired properties. And the final part is isotropic so we are also ensuring the properties along the z-axis which is not the case for many other technologies.
Precision is also a key benefit as the print resolution is directly affected by laser absorption efficiency. With CO2 lasers, all you can do is change the intensity of the laser which affects the selectiveness, but it will not be as reactive. We can adapt directly to the ideal wavelength for optimized melting, resulting in much finer details and a better surface finish.
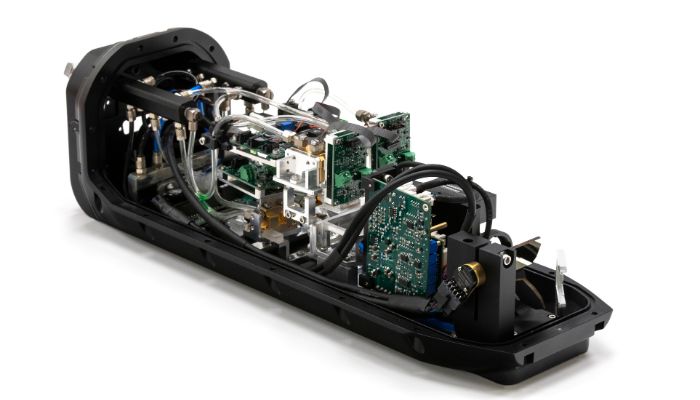
A look inside of a beam head
And last but not least, as previously mentioned the scalable nature of this technology is also a clear advantage over many other methods. Again, with our lasers, the more you add, the higher the speed and resolution. Our beam heads are made specifically to be used with more lasers thanks to the parallel laser approach and have a better result because it is clear that in SLS 3D printing the laser is what is going to have the biggest impact on the result, especially in terms of making many parts at once. The second most important thing is the management of the heat and again with the beam head, we are able to add heating devices in between the lasers and heat the powder even in the middle of the build.
3DN: How can users scale up additive manufacturing for production? What is preventing further spread as it is now? How do you address this?
I mentioned it earlier but SLS in general is one of the few AM technologies that can be scaled up for production. And our solution even more so thanks not only to its unique properties. But one thing I did not talk about enough is material cost and we understand that concern on the manufacturer’s side. Indeed, to address this we have a policy of being an open platform and we work very closely with material manufacturers to ensure that openness. The exact business model with materials is very flexible and we are committed to doing what is best for the customer in terms of high-volume production and application which of course is one of the key ways we are working towards higher volume production for users. Moreover, this is also the benefit of the new companies coming in rather than the older ones, ones that might already be more prototyping than mass production
Thanks to this, we are targeting all the markets where it would make sense to have high volume production using 3D printing and SLS specifically. To name a few, electronics and consumer goods are especially good fits but really our solution is ideal for any industry where either customization or supply chain issues might be a concern. This is especially true for sectors where customization has a lot of value,
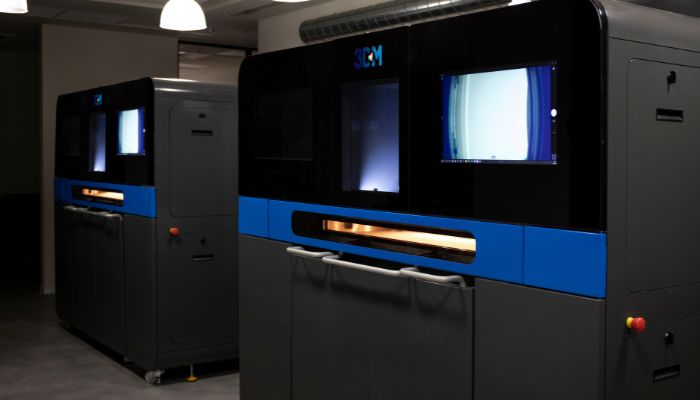
3DM’s full solution
3DN: Any last words for our readers?
We have two major messages right now. One, we are on the verge of commercialization and productization of the technology, you can expect to see more soon. Two, though we are already engaged with different industry players who will be beta or early bird users of the technology, we would love to interact with even more and are always happy to hear from others to learn about their high volume production goals and to learn more about what they need. You can get in contact with us to learn more HERE.
What do you think of 3DM? Let us know in a comment below or on our LinkedIn, Facebook, and Twitter pages! Don’t forget to sign up for our free weekly Newsletter here, the latest 3D printing news straight to your inbox! You can also find all our videos on our YouTube channel.
*All Photo Credits: 3DM